This article covers:
- Reasons for going DIY with pros and cons
- What is an eco build?
- Eco build options in Ireland
- Costs of eco building
- The Irish cob house project with full costings
- The Irish recycled house project with full costings
- Top tips if you are planning a budget and eco friendly build
A common wish among self-builders is to reduce costs. Unfortunately, building to ecological standards usually adds to the budget rather than take away from it. But that doesn’t necessarily have to be the case.
In fact, over the past ten years eco building has moved from being a marginalised idea to a mainstream concept, in part pushed along by building regulations. However, progress has tended to focus on energy efficiency and renewable energy only, largely driven by a narrow policy agenda concentrating on energy and associated CO2 emissions.
Other equally important environmental issues associated with housing, including water, waste, and indoor air quality, appear to be less of a priority when it comes to the regulations. On your project it’s a good idea to take a holistic approach, that is, one that takes into account all of these elements, starting at the design stage.
But remember, what’s important is that your efforts bear fruit during the entire lifetime of the building.
It’s easy to get bogged down trying to decide how to do the right thing, a difficulty not helped by the fact that there are a multitude of eco build creeds, each with its own bible and preachers. There isn’t one simple build style, nor is there one HomeBond-style Ecological House Building Manual.
Instead, there’s a patchwork of solutions that have been experimented with, responding to the particular needs, means and abilities of their promoters, as well as constraints and opportunities of their particular locations in terms of climate and site characteristics.
The availability of local materials is another key consideration and influence on which method to choose. Also, compliance with planning law and building regulations may not be straight-forward so these will have to be considered carefully early on.
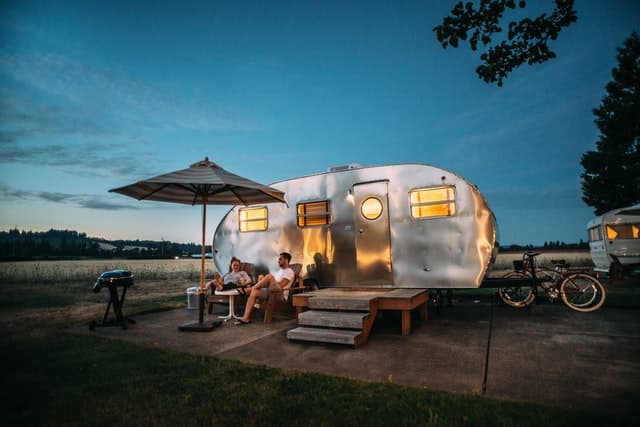
Designs for DIY eco builds
The most obvious way to save money is to cut down on labour costs, which can account for half of your final bill. That of course can be done by doing most of the work yourself, but paying for someone else to do it could end up being cheaper than a DIY approach, depending on your circumstances, skills and frame of mind. Remember, time is money. Even if you have the time to spare, weigh the fact that a skilled builder will get the job done much more quickly than you.
OK, so now that you’ve decided to do as much as you can yourself, where do you start? The Walter Segal method is perhaps the most famous, as it provides a very basic blueprint to build a timber frame structure. Advice from an architect, engineer or other design professional familiar with such a method should be sought if that’s the path you choose.
What you’ll end up with are simple plans to follow, but depending on your ambitions, this may be a more or less realistic endeavour. Bear in mind that a small project will be easier to achieve: in general, the more you upscale the more complex it becomes to build.
An Irish-made small-scale example is Peter Cowman‘s EconoSpace (Economical Space) which are quick build designs that come in a range of sizes, between 10sqm and 25sqm. You can not only build it yourself, but easily and quickly.
The logic behind these building methods is that mortgage debt is unsustainable. With the EconoSpace, you’re given the possibility of building a 25sqm structure for €10,000. That certainly puts the dream of living mortgage free within the reach of many people.
Plus, at such a small size, you shouldn’t require planning permission either (check your local planning department) but this option might not be realistic if you have a family. I have heard though, many stories locally of households two to three times the current average size of 2.8 people/ household living in 600sqft (55sqm) houses, only 50 years ago. Of course, larger sizes are possible, but obviously come at an extra cost and more building complexity.
The EconoSpace structure is made of a timber frame (floor, roof, walls) and has been designed to be easy to build and compatible with a wide range of walling, roofing and flooring materials. The building fabric serves multiple purposes including weatherproofing, insulation, thermal mass, providing access and light to the internal space, as well as allowing air transfer for ventilation.
The infill of the walls, roof and floor structure can be done with manufactured products, however these can be expensive, particularly if they are ‘natural’. After many years of trying different materials, the masterminds behind this concept have reached the conclusion that clay-straw infill meets the requirements of insulation, thermal mass and strength while the raw materials can be sourced cheaply and locally. It’s also easy and straightforward to work with.
Metal roofing and sand/clay plastering (protected by generous overhangs) can be used for low-cost weatherproofing, with slates for the roof and timber cladding for the walls as more complex and expensive alternatives. The careful configuration and furnishing of the internal space should meet the purpose of its occupants (habitation, art studio, garden office, shed) while preserving compactness (think about the type of built-in units you’d find on a boat or caravan) and adaptability for future uses.
Additional features of the EconoSpace include relative ease of disassembly, with the ability to recycle materials or rebuild at another location without difficulty. Modularity is also helped by the grid-like structure and Econospace units can be extended or joined up to create bigger living and/or working spaces.
The cob house example
Self-builders Féile Butler and Colin Ritchie built their house in County Sligo out of cob, a mixture of mud and straw, and their experience has been a gratifying one. “Initially, we wanted our house to be environmentally-friendly,” says Féile.
“As we researched natural building techniques, in particular cob, we found there were many other positives associated with it. We love the fact that we could make our own building material from the soil beneath our feet, something even gardeners don’t want!”
“We love that men and women, children and the elderly can all find a pace and a scale that they are comfortable building with. There are few construction materials that are so democratic. And there is nothing daunting about working with mud. It is a very forgiving material, so it suits all skill levels. Because we made it ourselves, from the soil on our site, it has possibly the lowest embodied energy of any building material we are aware of.”
In addition, 80 per cent of the other building materials were salvaged, reclaimed from dumps, in skips, at demolition sites, in fields and even beside a football pitch. All their wall framing timbers came for free from local recycling yards.
Salvaging also extended to internal fixtures such as a bath, sinks, radiators, and floor boards. But it has to be said that their efforts were supported by a community of well-wishers that kept an eye out for useful junk.
This approach required a careful strategy, and time! In their case, it took them three years to accumulate and store everything before building started. Construction then took another two years, and the project was completed in 2011.
Where they could, Féile and Colin used straw bales for insulation or salvaged insulation. However, it was necessary to supplement these free/cheap insulation materials with top-grade natural insulation products in some places. They used lightweight expanded clay aggregate (LECA) for the earthen ground floor and wood fibre insulation for difficult details demanding higher performance.
Another low cost component that Féile and Colin banked on from the very beginning was to build a home that was about half the size of the average Irish self-build. “We wanted to build a proper, functioning family home, hence building it 130sqm.
The best advice if you want to save on money is to build small,” she says. Compared to the average floor area of ROI one-off rural houses at 253sqm, the cob house is quite modest in size and can still comfortably meet the needs of Féile, Colin and their two kids (and two dogs).
Féile’s estimate on the cost of the house is €114,000 or €877 per sqm (€81/sqft) as compared to her estimate of around €1,660 per sqm or €153/sqft for a build with similar high specs in a rural area.
Savings on construction materials and labour allowed them to splash out on the wood and solar heating system (€20,000), high-spec external doors, double and triple glazed windows and roof lights (€22,000 in total), as well as a rainwater harvesting system (about €4,500).
Store-bought natural, breathable materials for finishes such as lime render and eco-paints are more expensive than standard materials, but were also used.
Féile and Colin super insulated the timber frame walls, roofs, floors and windows (with average U-values compatible with the Passive House standard) to compensate for the poor insulation value of cob walls (U-value = 0.65W/sqmK, about eight times worse than what’s required by the building regulations for a fully insulated wall), and the house performs very well in energy terms. They burn off-cuts from Colin’s carpentry work in their stove and spend about €115 a year on fuel bills.
While the U-value of cob is poor, it regulates moisture very well and its thermal mass provides a strong buffer against outdoor temperature changes. It also takes full advantage of passive solar gains and overall, in Féile’s experience, it delivers as good thermal comfort as the super insulated walls.
The recycled eco build example
Amy lives in a remote rural location on the west coast of Ireland where she built her house in 2011. She was on a tight budget and worked closely with a local low-energy builder to find the best way possible to enable her dream of rural living in a cost-effective and environmentally friendly manner.
After careful consideration, they opted for a second-hand Dutch cabin recycled from a building site in Germany. These cabins were originally made of a timber structure into which sandwiched timber panels (tongue and groove/insulation/ tongue and groove) are slotted in for the walls, timber boards for the floor and roof cover. Windows come in standard sizes and are also slotted in the rebated posts.
The structure follows a simple grid and is very modular. Assembly and disassembly are easy and fast, and can be done with simple tools and minimal carpentry skills. These Dutch cabins are quite popular in the region, and served many families in need of a cheap extension or a temporary dwelling while building their house. Some of them have been lived in for over 25 years and are still in great shape.
Amy’s cabin is 60sqm and was re-built in Ireland for long-term use and comfort. She therefore carried out considerable upgrades on the basic fabric, chiefly to achieve good insulation and airtightness levels. All of the existing single glazing that came with the cabin windows was also replaced with high efficiency double glazed units.
The suspended floor sits on three reinforced concrete bearers and has been insulated with 100mm thick rigid PIR board between the joists. An airtight/vapour check membrane has been applied internally and taped carefully to minimise air leakage through the floors, with new varnished high density, low formaldehyde OSB boards on top to provide a warm floor surface.
The original exterior walls were sheeted with a 50mm layer of compressed, flexi-edge mineral wool insulation between 50mm battens, over which a wind-proof, breathable membrane was applied, taped and sealed at the junctions with windows, roof and floor.
The roof’s A-frame, purlins and timber panels came with the original kit. They were then weather-proofed with a breathable membrane (sealed and taped for wind tightness) and covered with corrugated steel sheets.
Amy also added an ingenious, low maintenance in-built composting toilet, and a well was drilled on site to provide potable water. Most of the kitchen furniture and bathroom fittings were salvaged and reconditioned.
The overall cost for the cabin, ready to move in, was approximately €40,000 (€667/sqm or €62/sqft). This includes a lean-to at the front, simple electrical wiring (€900) as well as the ground work (estimated at €5,000) and the well installation (€3,000).
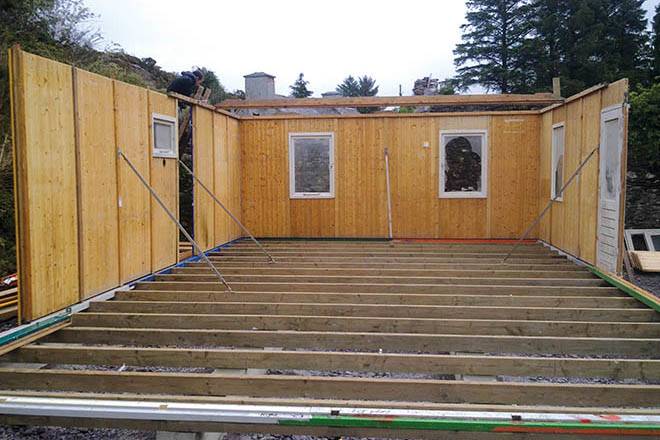
Top tips for your eco build
Time: Above all, you must be highly motivated, and that often comes in the form of a strong wish to have a certain lifestyle and reconnect with the tradition of building your home. In order to commit to your build, compromises will have to be made. If you work nine-to-five you’re unlikely to be able to dedicate much of your attention to the project. If you had other activities before taking up the build, you’ll have to push them to one side. Low cost ecobuilds are just like ‘true’ self-builds, they take a lot of time due to the need to do a lot of the work yourself, not only building but planning and preparation. And as they say, time is money.
Approach: As with each self-build, each eco-build project is unique, but it follows on from the work carried out by pioneers in experimenting with different ideas and techniques. In many cases, it involves re-appropriating that shelter-making spirit and skills that were prevalent only a few generations ago, at least in rural communities. Many of the eco-building approaches are well documented in manuals, blogs, etc. but there is nothing like learning by doing. There’s a number of courses you can attend to get an idea of what you’re getting into and whether it works for you.
Building regulations: Being guided by core sustainability principles throughout the life-cycle of the project is essential to achieve the ecological building objectives, but a very purist approach may be impractical and counterproductive. Demonstrating compliance with insulation requirements, fire-safety, etc., when using construction materials and techniques that are out of the ‘established norms’ might prove difficult. For instance, if you plan to build a cob house in ROI today, know that the recently introduced energy requirements will make it very difficult for you to comply with the building regulations. Fire safety is another requirement that you will have to consider, especially if you’re dealing with structural materials that haven’t been certified, e.g. salvaged components.
Planning permission: With any type of construction, obtaining planning permission to build a house in a rural location can prove very difficult. This reality has unfortunately shattered the country living dreams of many eco-builders. While the planners are keen to push green technologies, some areas are just very difficult to gain permission to build in, regardless of what type of house you intend to put there. One alternative would be to do up a house with eco-building techniques, as county development plans make exceptions for those who will prevent buildings from going into disuse.
How to cut costs with an eco build
As we have seen, eco-building on a shoe-string can involve different cost-cutting strategies. Using recycled and/or salvaged fittings and furnishing improves the project’s environmental and financial bottom-line. Also, opting for locally available and cheap natural raw materials such as subsoil, straw, or timber, instead of manufactured, often imported solutions, provides similar benefits.
Getting involved in the actual construction of the house, using suitable low-skill techniques such as cob and often with the help of volunteers, is another feature of many low-cost ecological building projects. However, one shouldn’t underestimate the time commitment required, including for planning and preparation.
Last but not least, remember that small is beautiful… and cheap! Plus, building an excessively large house is not only likely to mean you won’t be using a lot of the rooms, it will add to your maintenance requirements (vacuuming, window cleaning, the list goes on). Also remember that square shapes are the cheapest, and easiest, to build.
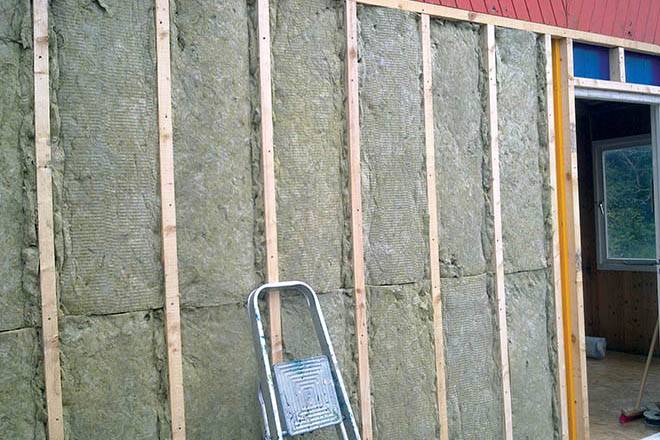