In this article we cover:
- What is an energy efficient home
- How to devise an insulation and airtightness strategy for your home
- How homes built today are different
- How to take into account lifecycle costings
- Embodied energy: what it is and how to minimise it
- Example of an eco home and choices made
Your airtightness and insulation strategy will depend on how you build your house, what your overall aim is for energy efficiency, and how you plan to ventilate it. You will then have to make choices based on cost versus performance versus eco credentials.
The adage “Build Tight, Ventilate Right”, coined by Earle Perera of the Building Research Establishment in the 1990s, is as true today as it ever has been.
This means that in energy efficient buildings, the insulation and airtightness strategy must factor in ventilation to protect your own health and to prevent sick building syndrome. But there’s even more to it than that.
How different and more energy efficient buildings are today
Victorian buildings were very robust, adaptable and abundant in architectural features. They had large areas of glazing and plentiful ventilation due to their lack of airtightness and fireplaces in most rooms. This meant ample fresh air and light, but also poor energy/resource efficiency.
The challenge today is to retain the positive features, including an efficient ventilation strategy (which was in many cases sacrificed in the late 20th Century to make way for insulation), while addressing the downsides. Here are some of the variables to consider:
Lifecycle costing: While the precise definition can vary, it tends to take into account the upfront cost (and, in the case of insulation for example, payback period in terms of energy saved against purchase price), what you need to pay to maintain and replace the product as you use it, plus the cost of disposal of materials at end of life, all of which is adjusted for inflation.
Embodied energy: This analysis not only looks at the energy a building will use during its lifetime, but at the energy consumed in the extraction/processing/manufacture of components and, potentially, the recyclability of materials at end of life. Databases are available for the embodied energy of materials, which are generally independent of geographical location. An extension of this approach is embodied carbon assessment, a trickier and less researched subject as it depends on the energy types used for extraction, manufacture and shipping of materials/components and will thus vary depending on where the products are produced and where they are used.
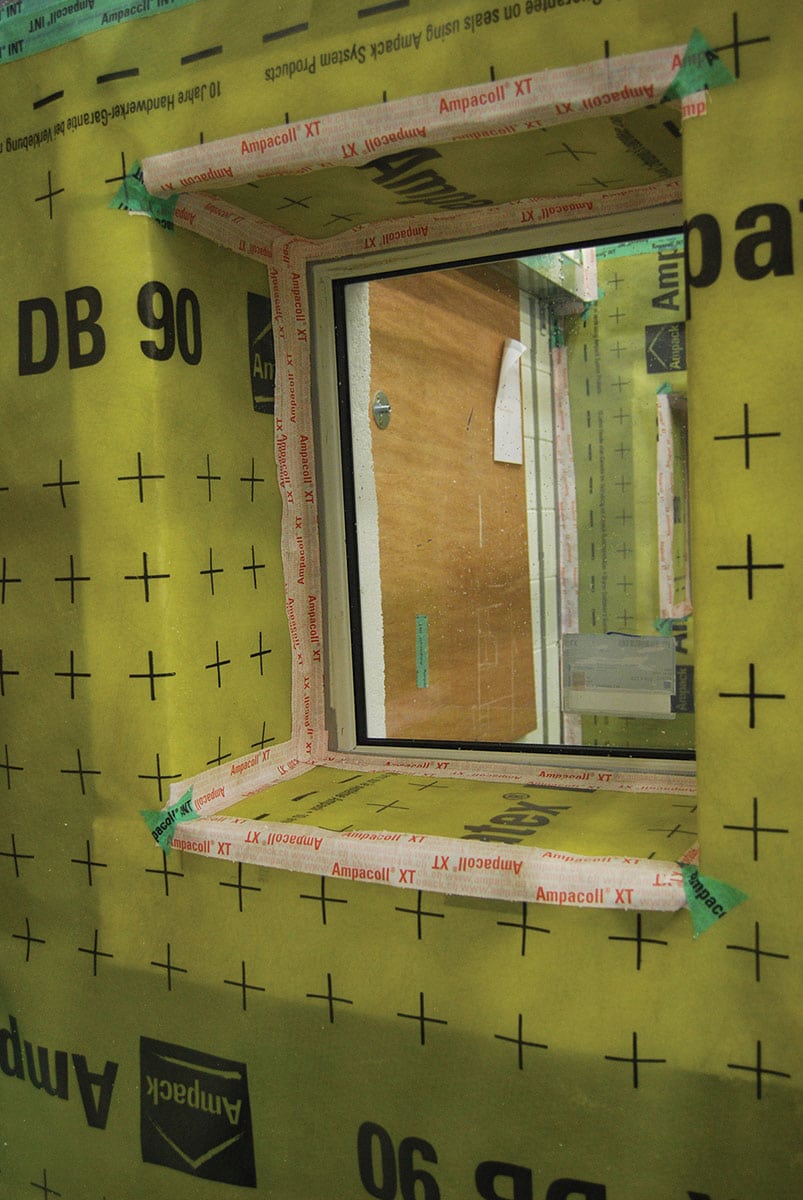
Eco credentials: It is possibly simpler to only look at the inherent eco credentials of a material: Does it need much processing and what impact does its extraction have on the environment? Can it be readily recycled or reused at end of its life? As far as I am aware, there are no specific eco options for airtightness and vapour control membranes – these are engineered products with particular properties regarding air and moisture transfer in specific directions (into or out of the fabric). So the eco analysis tends to apply to insulation products, and herein lies the dilemma: the best energy performing insulation materials are usually the most engineered.
Overall, an insulation and airtightness strategy will need to take into account these but other performance related issues. Moisture management comes to mind; for example a material that can help regulate moisture transfer will be suitable next to a breathable membrane. There are dangers too in using impermeable materials in old solid walled houses as moisture movement needs to occur in the fabric.
When considering my own self-build nearly 15 years ago, I was often torn between using higher performing, oil based (plastic) insulation products and more natural materials with higher thermal conductance (poorer performance).
The rule of thumb is that lower performing insulation materials require greater thicknesses to achieve a given insulating effect. And while happy to embrace a wider-than-normal wall element, I had to draw the line somewhere.
To give you some context, the driving force for my build was to design out the central heating system. I had calculated that I should be able to do that if I could reach an average U-value for the entire building fabric (including windows) of about 0.2 W/sqmK.
Anywhere there was a breathable membrane I used hemp batts for their good moisture regulation properties. Then for the roof, the 200mm rafters were filled with 150mm PIR boards.
The floor had 200mm PIR insulation partly because it had to play a role in supporting the screed.
The 150mm timber stud walls contained mineral fibre, as per the standard make up for timber frame. The walls were then internally drylined with insulated plasterboard (phenolic or PIR). The windows were almost all triple glazed including rooflights.
And, as you would expect, the house has a mechanical ventilation heat recovery (MVHR) system. The q50 air permeability was 1.3 m3/(h.sqm) which, though some way off the Passivhaus minimum requirement, I was happy with.
The whole house is heated by a wood burning stove with its own dedicated combustion air, assisted by the MVHR in distributing the heat around the house. The wood burner has a back boiler which feeds the hot water tank via a gravity loop.
Between the back boiler and solar thermal tubes (both feed the hot water tank), which complement each other well seasonally, the electric immersion has hardly ever been used (but there is an electric shower in the upstairs bathroom).
Today the house, which achieved an A2 energy rating at the time, performs as well as ever. I have replaced the wood burner once (very recently) and the MVHR thermal wheel motor once (some time ago; I have also been changing the filters regularly of course). Otherwise we have used only logs for heating, at a cost of about €300/yr, and electricity for everything else, using approximately 2,500 kWh/yr.