In this article we cover:
- How luck and perseverance got them their dream site
- House style influences
- How the build was managed
- Top tips for going direct labour
- Troubleshooting on site: issues with windows and doors and roofing materials
- Why he chose timber frame
- Choice of heat pump and why
- Interior design tips
- Landscaping tips
- Tips for those looking to build a similar looking house
- Biggest splurge
- Floor plans and specification
- Suppliers and professional photographs
Tell us about the site.
Pure chance and timing. That doesnât mean it wasnât a highly competitive process â over 40 people turned up at an open day so I knew it would be a difficult acquisition. My wife Janice and I went in high to ensure we got it.
It did feel expensive at the time, but it doesnât now when we look at the vision that we have achieved and winning the RTÃ Home of The Year (HOTY) Award 2023.
We had been on the lookout for a number of years as we were stuck on one particular area where sites rarely come up. We were not looking at sites anywhere else. Little were we to know that a dream site would come on the market. We just had to have it.
House size: 3,000 sqft
Plot size: 4.5 acres
Number of bedrooms: 4
Build method: timber frame
Heating and hot water: air source heat pump
Ventilation: centralised mechanical with heat recovery
EPC (SAP): A (98)
What influenced your style?
We were mostly influenced by our experiences. You have to live in a number of homes to really understand how you live and therefore what the design and functionality should be to match your behaviours. That dictated the flow and layout.
We also drew on our extensive international travel experiences. Seeing things along the way that we incorporated, from the open plan space inspired by Cairns, Australia to the shower seat inspired by a visit to a resort in the Ozarks, Missouri.
The HOTY judges were particularly interested in consistency of style and continuity being a key aspect of this design. Whether youâre in a bedroom, the hall or the main living space, the house has a similar look and feel.
We have also tried to pull the outside in with our choice of materials, textures and colours. Being in a wooded site means we have used lots of wood on the house and in the styling.
How did you tackle the statutory requirements?
We had our architect manage the planning and building control processes for us as part of a package. I would say that this took the pressure off us.
For an area known for Ulster Scots style of homes, there were no objections at all to the plans that we submitted. I think a big reason the process was so smooth was our architectsâ expertise.
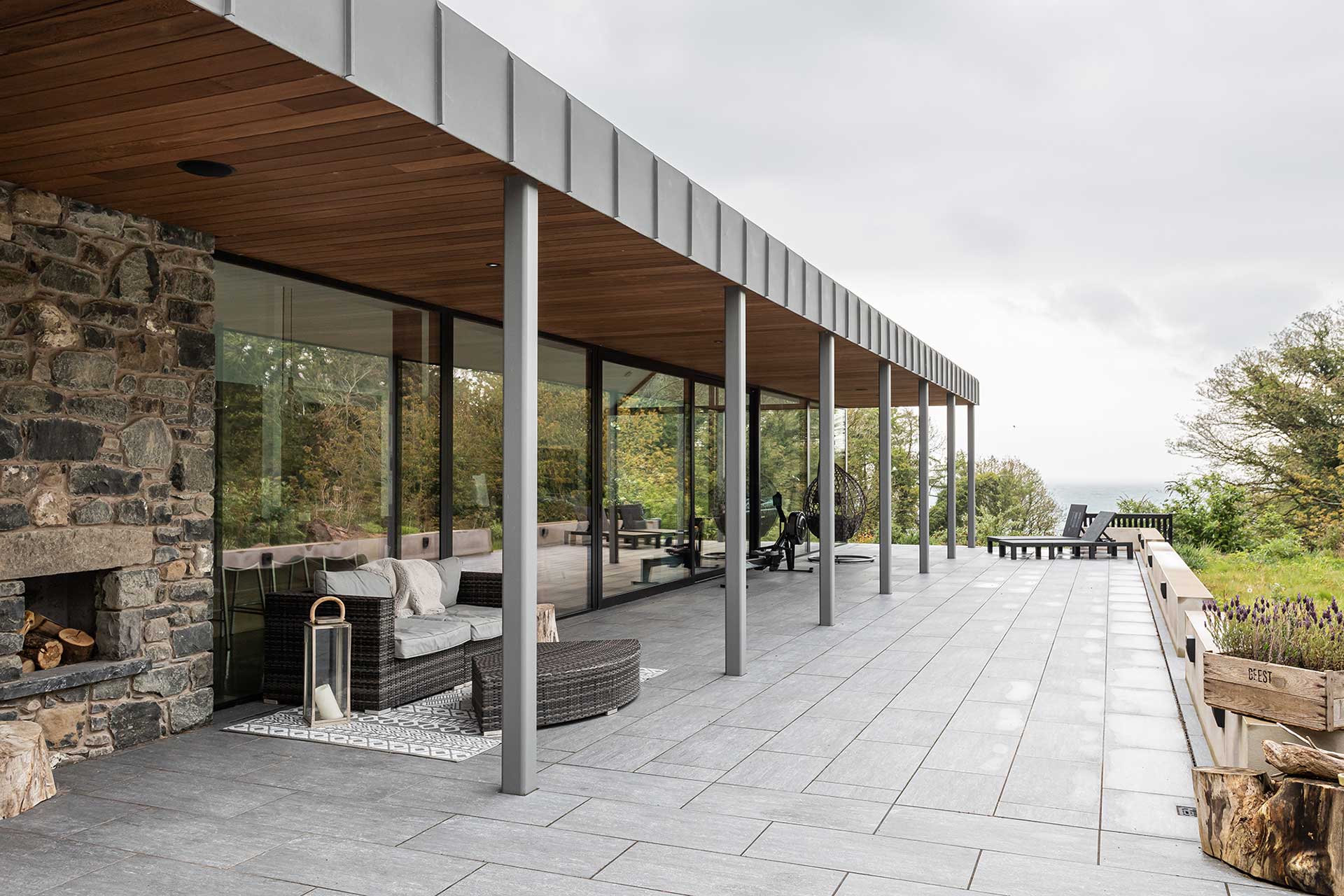
As I managed the build myself, health and safety was paramount and down to us to ensure risks were not being taken, i.e. regularly checking scaffolding, tidying each night to ensure a clean site, removing any trip hazards, etc.
We insured the build with a self-build policy through a local broker throughout the process which gave us peace of mind. We had to extend the policy as the build went beyond 12 months.
Top tips for going direct labour?
I project managed the build and we had a site manager who would be there each day and was also able to turn his hand to jobs that needed done around the site and take deliveries.
Day to day, there was always troubleshooting to do. We had to set expectations on what we wanted done and there were always questions, decisions to take that came thick and fast from the trades people.
I used a whiteboard in our adjacent barn, a building that was part of the 18th Century old mill complex. I created lists and instructions daily to be followed. I also had all drawings and details printed on large A5 printouts, so trades had all the information they needed to support their part of the process.
The nature of the build, using very modern construction methods, a vast array of materials and an unusual design, meant that often those working on the project were dealing with something new or different. They had to ask a lot more questions than they would on a standard block build.
As a novice, looking back I could have done with more knowledge to keep things right. Also at times I had to go head to head with trades to drive the approach, and quality, when I did not have all the knowledge of experience. I knew enough to stand my ground but things moved so fast, without the previous experience there was only so many hours in the day to do homework and understand how things should be done.
Also quality of workmanship varied greatly. With it being Covid times, companies such as window and kitchen suppliers were using trades they may not have worked with before in these areas. There were serious issues and challenges to deal with, when it came to installation. This was very taxing and stressful and has been a long running process to get resolved.
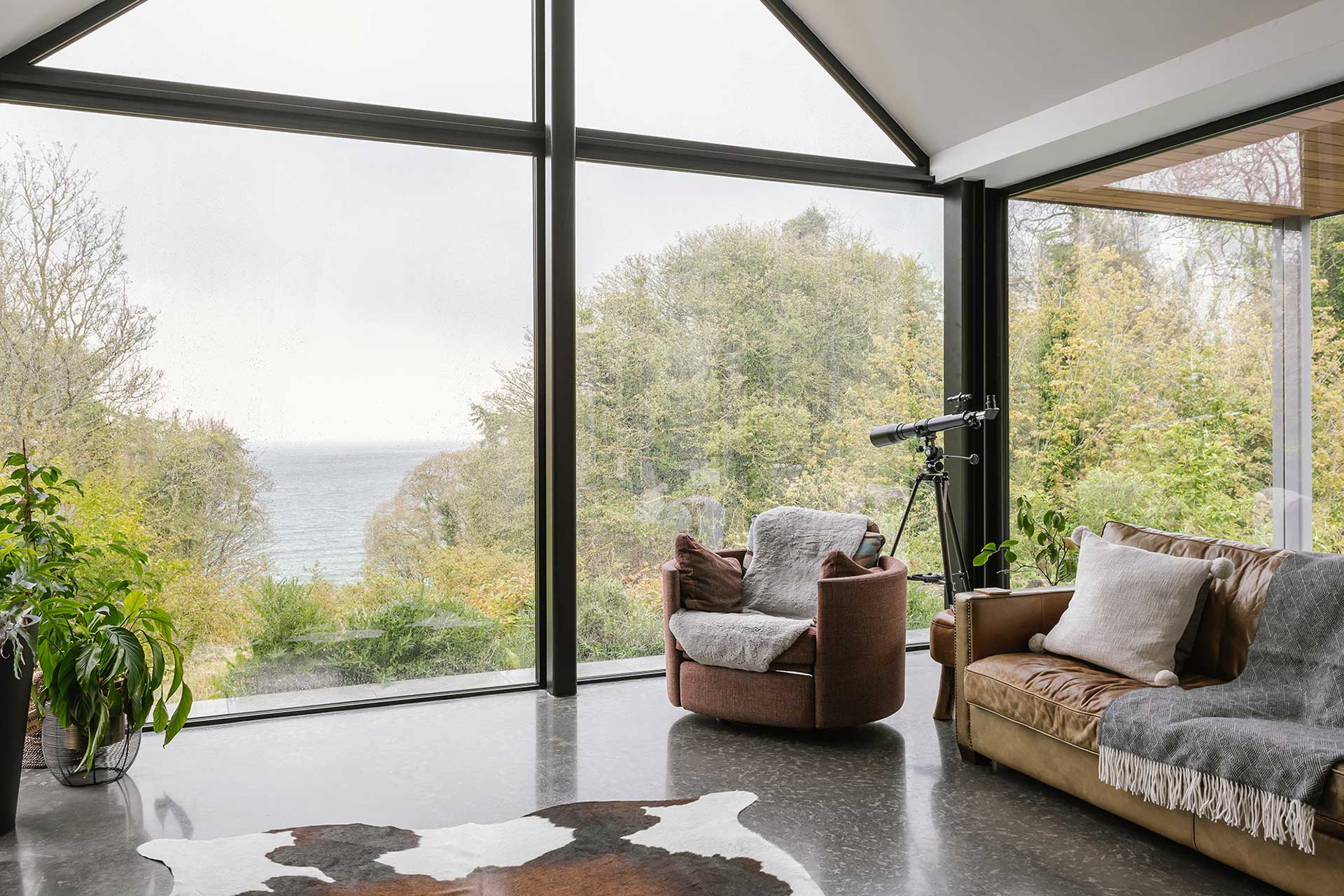
Give us some examples of troubleshooting.
The windows and doors were a big pain point on the build. Three years on and we are still waiting for the window company to resolve our issues. The aluminium was damaged when it was fitted, which may have been down to inexperienced staff. In hindsight, I would have preferred something thatâs less easy to damage.
The reason we chose aluminium was the views, to make the frame as slim as possible. We knew from the start that it was a trade off between low profile, double glazed aluminium windows frames and energy retention. I would have preferred triple glazed however we wanted low profile and less glazing columns and couldnât do that with triple glazing.
We also had issues with the roof; we chose two materials, Spanish slate and fibre cement corrugate. We sourced slate from a local supplier and the corrugate from a company in Dublin that was appalling to deal with.
The product arrived faulty and cut incorrectly, and the aftersales service was dreadful. This was a common feature on the build and important to call out. Several suppliers made many mistakes and how they handled solving them was hugely frustrating and disappointing.
Of course some put their mistake right but others to this day have not, leaving us to sort ourselves and be out of pocket.
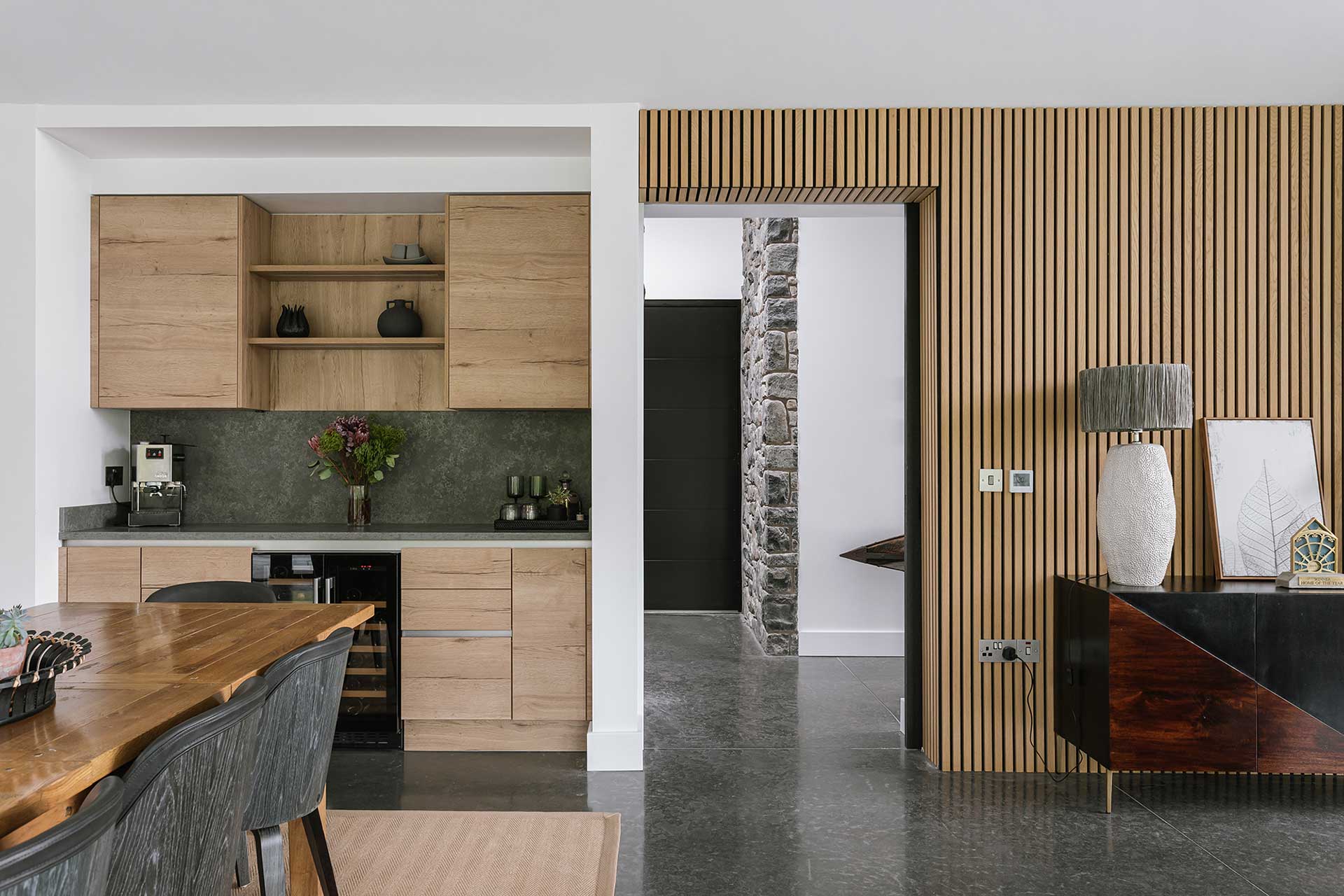
What building method did you choose?
We went for a timber frame, which was built and assembled on site by a specialist company, as I see it as the way forward for house building. Itâs also a faster means of construction and one of the most thermally efficient options. This is true only if you have good quality control at the design and construction stages, and everything is done correctly on site.
When it came down to building the other elements, we were lucky in that this was very much a family supported build. Parents and brothers and sisters were on hand to help with some very tough tasks such as laying the radon barrier and installing the insulation, which we did ourselves according to building control regulations.
How did you choose your heat pump?
We wanted a renewables system to avoid gas or oil. An air source heat pump was the obvious solution, and we chose to go with underfloor heating throughout the house. We chose an Irish company as we wanted one supplier for the heat pump and the heat emitter. Also because we live by the sea and the company we chose had won awards for the efficiency of its heat pump and could provide an anti-corrosion coating.
How did you style the interiors?
We had a good idea of the style we wanted, and as soon as the plans got planning permission we were on the lookout for what we would buy. We then sourced bathroom fittings and furniture well in advance and bagged ourselves great bargains on high end brands. We ended up getting all of our bathroom fittings and furniture from the one place over a period of three years or so and stored it in our barn until the day they needed fitting.
Given the cut roof across much of the building, we went for LED spots. We also then made use of mood lamps and lighting, all sourced locally (although Hugh from HOTY thought we were lacking in this area!). Truth be told, our large open living, dinning and kitchen area has glass on three slides, so lighting was never going to be a real issue.
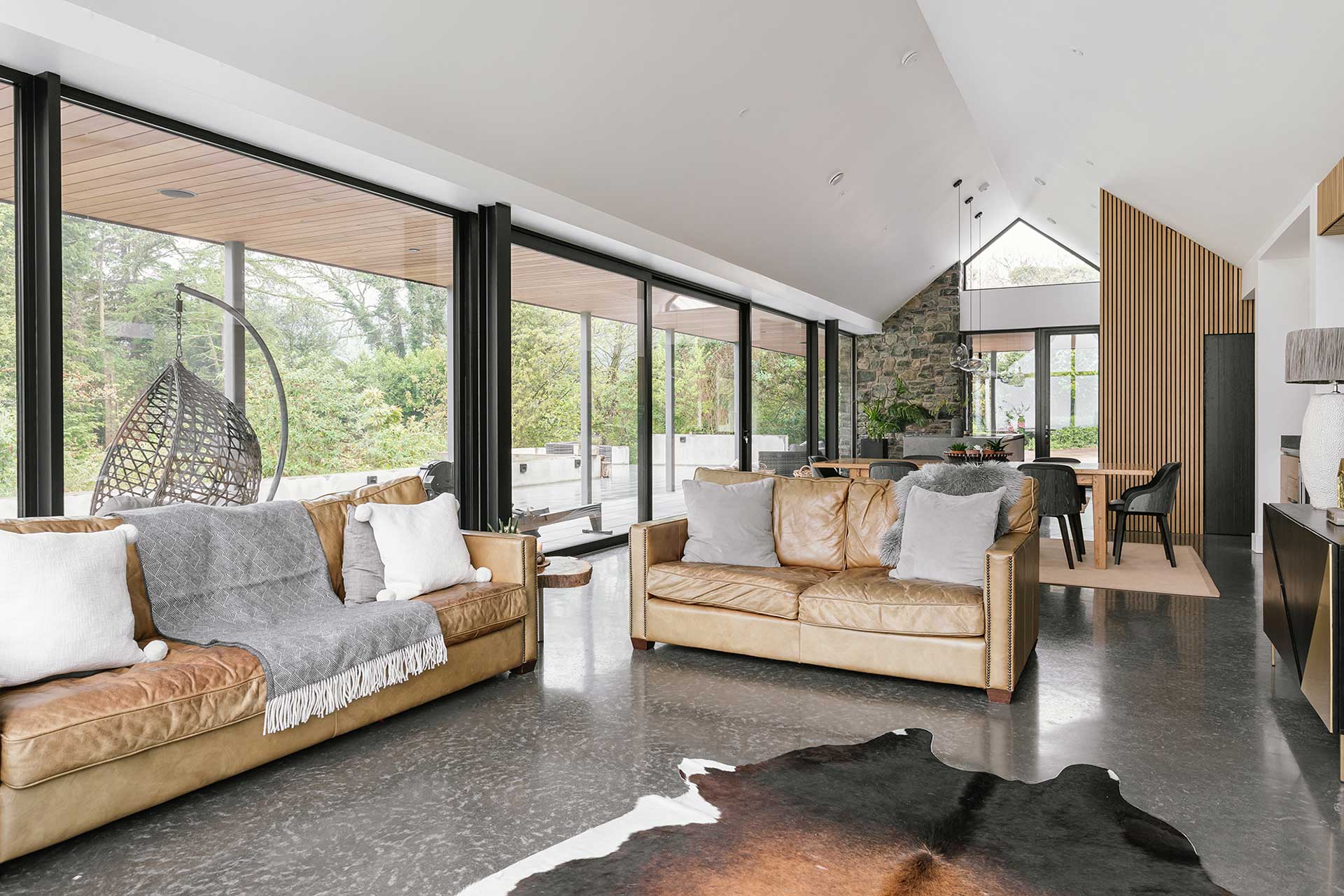
How did you tackle landscaping?
There were already beautiful and mature gardens surrounding the property, so we have not had to do any landscaping. If anything we had to cut back and invest time into keeping the place under control. Thatâs the beauty of dropping a new build into a forest.
Given the location, for the build we stripped back just enough for the construction and to establish access. We used a great local contractor for all groundworks.
We put in a lot of drainage and finished roadways with Scottish pebbles all round. We also bought porcelain tiles from a local supplier and fitted it ourselves using a local tradesman. The supplier had quoted us an exceptionally high cost to do the job; going with a local tradesman we saved ourselves around 75 per cent of what heâd quoted. So the lesson is, shop around.
Q&A with Rob
Favourite features?
The overhangs and outdoor living space. We also love the character of the charred timber and stonework combination. And the fact that it’s single storey with no stairs, we’ve futureproofed our home. The views in the open plan living space are exceptional too.
What would you do differently?
I would only make one change to the entire design and that is to add a skylight to my sonâs bedroom who sits beneath a flat roof. I put one in for the adjacent utility room and it was an oversight. Other than that, the design in terms of functionality for our family is first class. This is a credit to our architects.
On floor insulation, now that I have a better understanding of the options, if I were to do it again I would have done bead insulation. Given the volume of pipes for utilities and cabling in certain places, beaded insulation would have been a better job.
Another thing is painting, which was done by hand as we had a site foreman that was a great painter. But for speed and cost, doing it again I would possibly use spray painting.
Biggest splurge?
The stonework and burnt cladding. We really had to have it, and think it makes the build.
Tips
Seek plenty of references for big spend areas before you pay any deposits or commit. It will hopefully save you in the long run. Where you get recommendations from family or friends, donât take this as gospel â do your homework as it may save you from a world of pain.
Manage your expectations. Building can be very challenging and stressful, especially when you are doing it up and above a day job. You need to dig deep and find the resilience; you have to fight through the frustrations and also be aware that not everyone cares the way you do. Some trades want to be in and out quick. Others really do their work as if it were their own home. Itâs a mixed bag.
Accept imperfection otherwise you risk making yourself sick. The building trade does not do perfection.
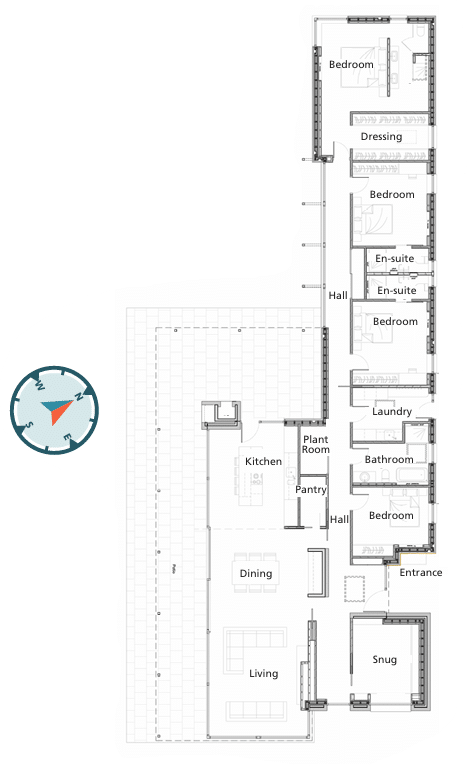
Spec
Walls: timber frame with 140mm glass mineral wool plus 50mm PUR insulation, U-value 0.17W/sqmK ~
Roofs: vaulted roof 180mm mineral wool plus 50mm PIR insulation, flat roof 120mm PIR, U-value 0.14W/sqmK
Floor: standard build up with 120mm PIR, U-value 0.14W/sqmK
Windows and doors: average U-value 1.1W/sqmK
Airtightness: 2.7m3/sqmh at 50Pa
PV panels: 4.03kWp on 45deg elevation
Suppliers
Architect
2020 Architects
Timber frame
Leadon Timberframe
Roof coverings
Zinc from Edgeline Roofing; slates from MacBlair
Stonework
Scullion Stone Masonry
Kitchens
Creative Kitchens
Charred timber
Toasted Wood
Electrician
M.R. Electrical
CCTV
Berek Burnside Electrical
Concrete
RTU Concrete and RPC Concrete Polishing for polishing floors
Groundwork/landscaping
Lyttle & Son, Gibson Paving for the tiles
Heat pump
Grant Engineering
Insulation
Walls Knauf Frametherm 35; Vaulted roof Kingspan TR27; Flat roof Kingspan Thermaroof; Floor Kingspan TF70
Photography
Elyse Kennedy, elysekennedy.com