In this article we cover:
- What is timber frame
- Stick build construction
- Open versus closed panel construction
- How timber frame kit suppliers work, with a breakdown of each stage
- Who does what on site with the different timber frame options
- How timber frame is assembled
- Log homes and green oak frame
- Eco builds that use timber frame
There are many ways of forming a frame with timber. The type that is built from scratch, on site, using wood from a builder’s merchant, is rare in Ireland but relatively common in the USA. A mixture of bureaucracy, the current lack of sufficiently well-trained carpenters and unfamiliarity with the techniques involved amongst other building trades make this more difficult here.

In fact in the USA and Canada, there is a long tradition of building in timber frame from abundant locally available raw material. There are even a number of North American manufacturers who fabricate timber frames (post and beam construction, often using long length of timber) including windows, doors and cladding and export them as a kit for assembly in Europe as a watertight shell.
Cedar cladding is often used, as well as structural softwood such as spruce or fir, with glazing often up to ridge height. These houses have a distinctive open plan style that shows off the high quality native timber to good effect.
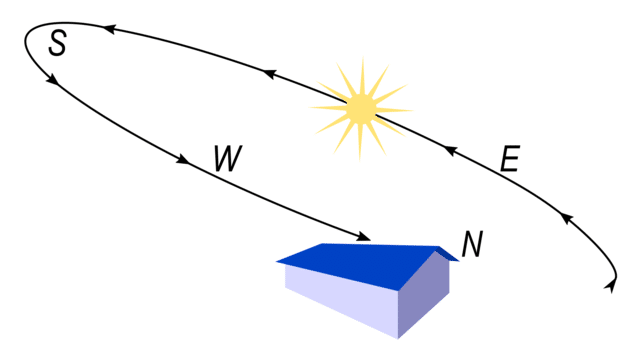
Most of the countries in continental Europe are also ahead of Ireland in terms of the use and diversity of timber frame houses and in general terms are also more adventurous with design and technology.
In a modernist tradition, German manufacturers often place a high priority on expressing the construction
of a house in the design and making it an integral feature of the appearance. German post and beam construction tends to be prefabricated and exported to the UK to a very high standard of design and construction, making them relatively expensive.
But for the purpose of this article, we look at the Irish timber frame systems most commonly available on the market. These are kits that depend on factory prefabrication. This means the frames are certified and pre assembled to be as cost effective as possible.
It also means these structures are built to be fire resistant, rot and pest resistant and are very good at keeping noise out of the building. Timber is a natural material that is vapour permeable, which when sustainably sourced, provides the benefit of being renewable.
The insulation, airtightness and ventilation strategy is essential to get right, as timber can decay, and you will have to follow through with the design you agree to as alterations on site will prove difficult.
Open vs closed panel
Open panel timber frames
The most widely available type of kit is the open panel. It is popular because it is easy to put together both when the prefabricated parts are made and when it is assembled on site. In the factory, softwood studs form the main structure, and a rigid board such as plywood provides bracing.
These are simply nailed together to form a strong, rigid panel, designed for easy delivery and assembly. The studs and the panels fixed to them are both crucial elements of the structure and if either is damaged or missing, the strength of the panel is reduced. The name ‘open panel’ derives from the fact that when the panels arrive on the site one side is open and un-boarded.
It is usually left open until the building is weathertight at which point services and insulation are put into position. It is closed over with a sheet of plasterboard or a gypsum-fibre board along with a vapour control layer to prevent condensation within the panel.
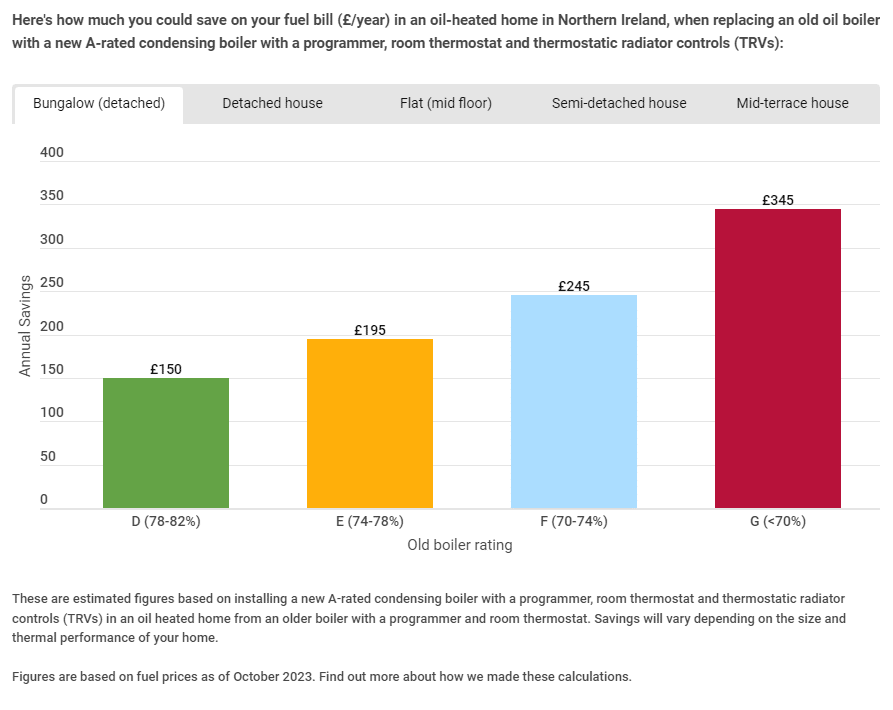
The platform frame method of assembly is generally used for the open panel system, because the short sections of timber needed lend themselves to prefabrication and transport to site – longer timber would require a special lorry.
Internal walls that are not carrying any load are usually supplied along with the rest of the frame, but can be improvised on site if necessary. If the internal
wall is part of the structural design of the frame, it must be manufactured as part of the kit.
The panels support the roof and are in an identical location within the structure to that of the block work inner leaf of a masonry cavity wall construction. The voids between the studs are filled with insulation.
Because warm air from the house carries moisture, the internal lining of an outside wall usually has a vapour control layer, such as a foil backing to the plasterboard, to stop air leaking into the inside of the panel. To disperse any vapour that does find its way in, the outer sheathing of the external wall is covered with a breather membrane, that keeps out water (such as rain) but also allows vapour-laden air to pass through to the outside of the frame.
The timber structure of an open frame is never exposed and would not look very attractive even if this were possible. The outside cladding can be almost any building material, including bricks, softwood boarding, tiles and render. When brick cladding is used, only an expert eye will be able to spot that there is a timber frame concealed behind it.
Main features:
- Fast construction on site
- Can be clad in any material
- Easy to transport – robust and damage easily repaired
- Cost effective use of the materials
- Suitable for hands on self-builders
- High level of insulation possible
- Limited alterations on site are possible
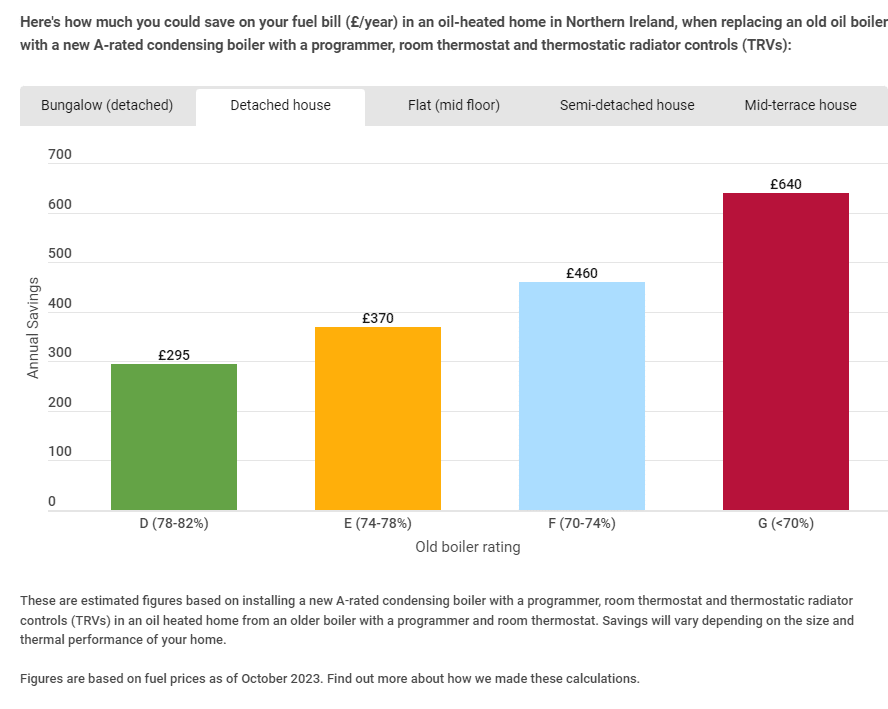
Closed Panel Timber Frames
If the framework of studs is enclosed on both sides it is called a closed panel system. The panels are factory-made in their entirety, including the insulation, electrical wiring and window and door linings. The main job required on site is to assemble them, after which the inside is ready for fitting out and decoration.
The idea is that once it is in place, the wall will not have to be drilled or cut. If this happens, the panel is damaged and careful repair is needed. As a result a very high degree of pre-planning is necessary. The position of anything that is to be fixed onto the walls, or supported by them in any way has to be built in when the panel is made.
Assembly once the panels have been delivered to site is quick, although relatively large lorries will be needed for transportation with cranes to lift the panels. Apart from the speed of erection and higher quality control, another benefit is that the building is easy to make air tight. Once in position, the frame is then clad in whatever material is required, in a similar way to the open panel frame.
Main features:
- Very high quality of construction
- Most of the building is assembled in the factory
- Very quick erection on site
- Careful handling during transport
- Very little work needed on site after groundworks and floor slab
- Low level of labour required on site
- Little room for improvisation on site
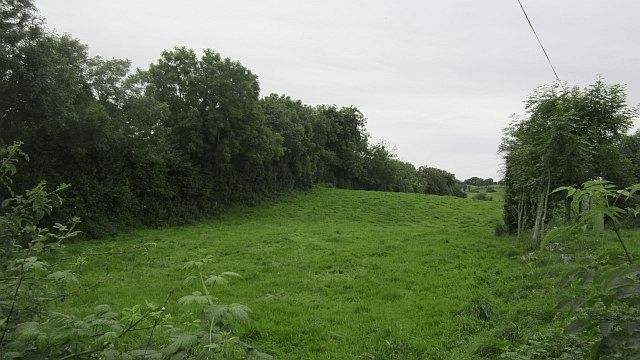
Assembling the timber frame
There are two main approaches to assembling the structure of a timber frame building, and most systems that use studs, joists and rafters are a variation of one of these:
Platform Frame
With this method, the ground floor walls and first floor structure is erected and the resulting platform is used as a base upon which to construct the next floor. This means that the whole frame can be built on site from relatively short timber lengths.
Balloon Frame
The balloon frame method is similar in principle to the platform, but the walls are built
as a continuous structure, from ground floor level up to the eaves. A benefit is that once made, the frame can be erected to a watertight stage faster. The balloon frame cannot usually go higher than two storeys because there is no timber sufficiently long enough to reach further in one go.
“Most of the countries in continental Europe are ahead of Ireland in terms of the use and diversity of timber frame houses…
Julian Owen
Green Oak Frame
There is a very strong element of nostalgia that attaches to traditional timber buildings and those genuine examples that have survived are greatly prized. However, there are many companies that have studied traditional methods of construction and do their best to replicate them.
One advantage the new buildings have over the real thing is that they comply with modern standards. A much higher level of insulation is possible and they also allow modern layouts and room sizes.
These buildings are not the cheapest in comparison to the other types of frame and require a relatively generous budget. The modern oak framed house takes the practices and principles of carpenters from the middle ages and re-interprets them using twenty first century factory prefabrication methods. Chunky beams, columns and rafters are assembled with slotted and dowelled joints just like the traditional frames.
The building is clad either by filling the gaps between the posts with insulated panels, or covering the whole structure with a cladding such as tiles, timber boards, render or brick.
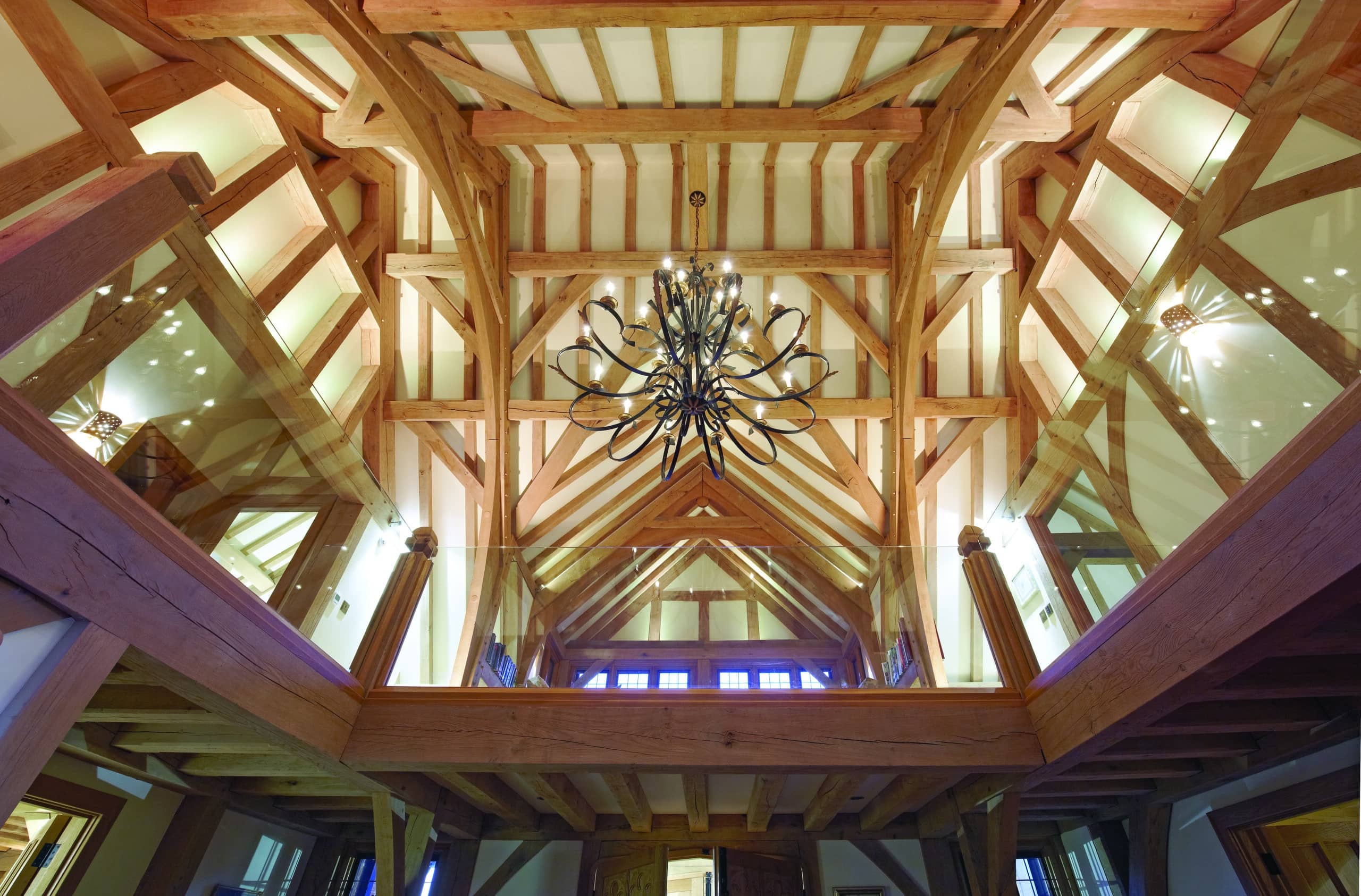
Often referred to as ‘green’ oak, because when relatively freshly cut it is fairly easy to saw and shape. Once felled, the timber gradually begins to harden and become impervious to water. After about 18 months to two years, it has become so hard it is resistant to insects and difficult to cut or sink a nail into.
As the green oak matures, it dries out and begins to shrink, twist slightly and even develops small splits. In an ordinary building this may be considered a disadvantage and no one should choose a green oak house unless they accept that this is part of the character of the material and key to its charm.
Main features:
- Authentic traditional appearance
- High quality construction
- Structure is expressed as part of the design
- Weathers naturally – no need for finishes
- Very durable – no preservatives needed in most cases
- Suited to open plan design
Log construction
Colloquially known as ‘log cabins’ this system has its origins in what was probably the earliest form of timber construction. Most kits originate mainly from Scandinavia, particularly Norway and occasionally North America.
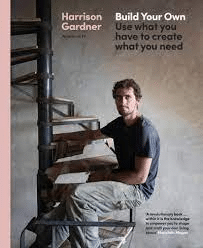
The basic concept of logs piled up on top of each other to form walls with dovetailed joints chopped out at the corners to interlock has been developed into a more sophisticated version. Chunky sections of timber are shaped by machine so that tongue and groove joints along their length interlock as they are stacked up to form the inner leaf of the wall.
The logs can be flat, oval or round to imitate true logs. Timber alone is usually not a good enough insulator to satisfy current regulations, so there is then a layer of insulation, usually faced with timber
boards on the outside.
Alternatively, the structural wall can be insulated internally and dry lined. Either way, log construction is more energy efficient than ordinary timber frame, because the bulky timbers absorb and store more heat than the relatively lightweight timber studs and posts.
Timber frame kit suppliers
The content of a kit varies significantly between different suppliers. Some provide the frame for the walls, floors and roof and no more. Others offer everything that is part of the construction that is made of timber, including windows, doors, staircases and skirting boards.
These extra items included in a kit package should be carefully scrutinised. Sometimes, in exchange for the convenience of not having to choose or source the items, there may be a significant mark up compared to the cost of supply by a builder’s merchant.
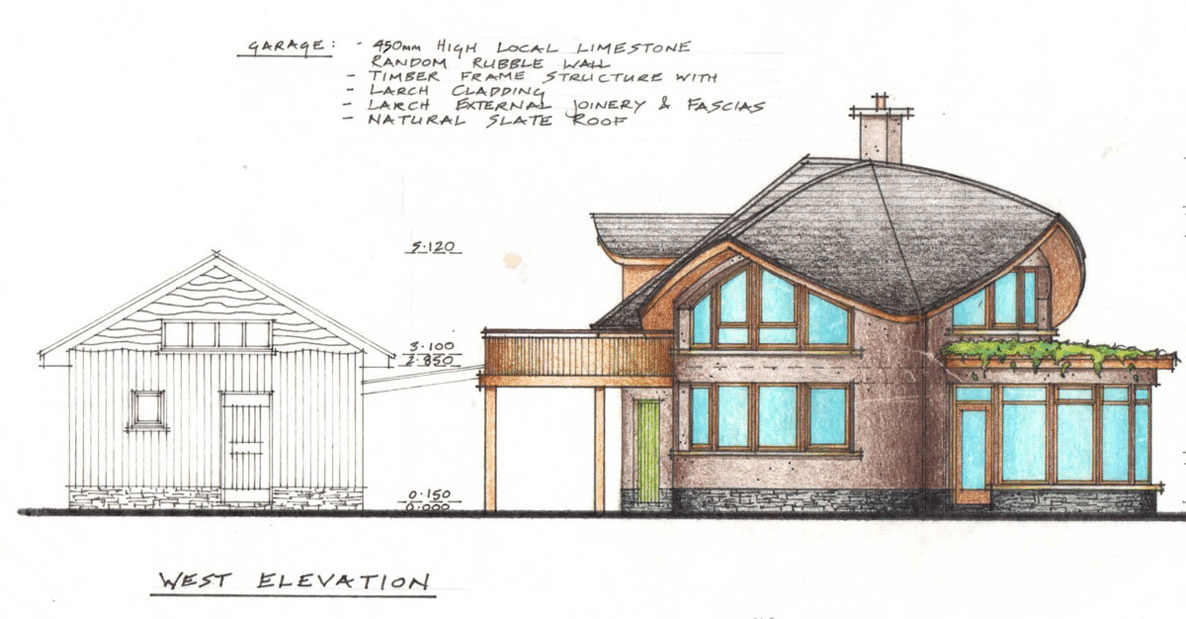
Some firms do not actually make the timber frame themselves. They ‘add value’ to the basic product, which consists of timber and boarding, by offering design and management services or the convenience and relative predictability of building a pre- designed house that has been refined and perfected over the many times that it has been made and built.
On first enquiry most kit suppliers will confirm that they will readily customise their designs
to suit a client’s requirements. However for some of them, this may mean that they will move a few internal walls around but be reluctant to make any significant changes in the overall dimensions or appearance. Others, particularly at the higher end of the market, will happily design a unique house for an individual family.
Programming the project
The majority of the work constructing a timber frame is by specialist tradesmen with much of it being carried out in factory controlled conditions. In some cases such as with a green oak frame, the entire structure will have been already assembled in the factory as a ‘dummy run’ to eliminate any problems that may otherwise occur unexpectedly on site.

Erection of a kit for a small very straightforward house may only take three days, a larger frame may take a couple of weeks. Generally a house built with a timber kit will be finished more quickly on site than an equivalent sized traditionally built masonry cavity wall structure, although there is usually a long lead-in time between ordering the kit and delivery onto site, typically three months or more.
The crucial point in the programme is the arrival on site and erection of the kit. The necessary preliminary works must have been completed and the base must meet the tolerances and standard of construction specified by the suppliers – level, square and of the correct dimensions.
This is crucial. If the base is not ready the erecting crew will return to the factory and extra costs will be incurred to cover the abortive visit and for the storage of the components.
Site set up materials and delivery
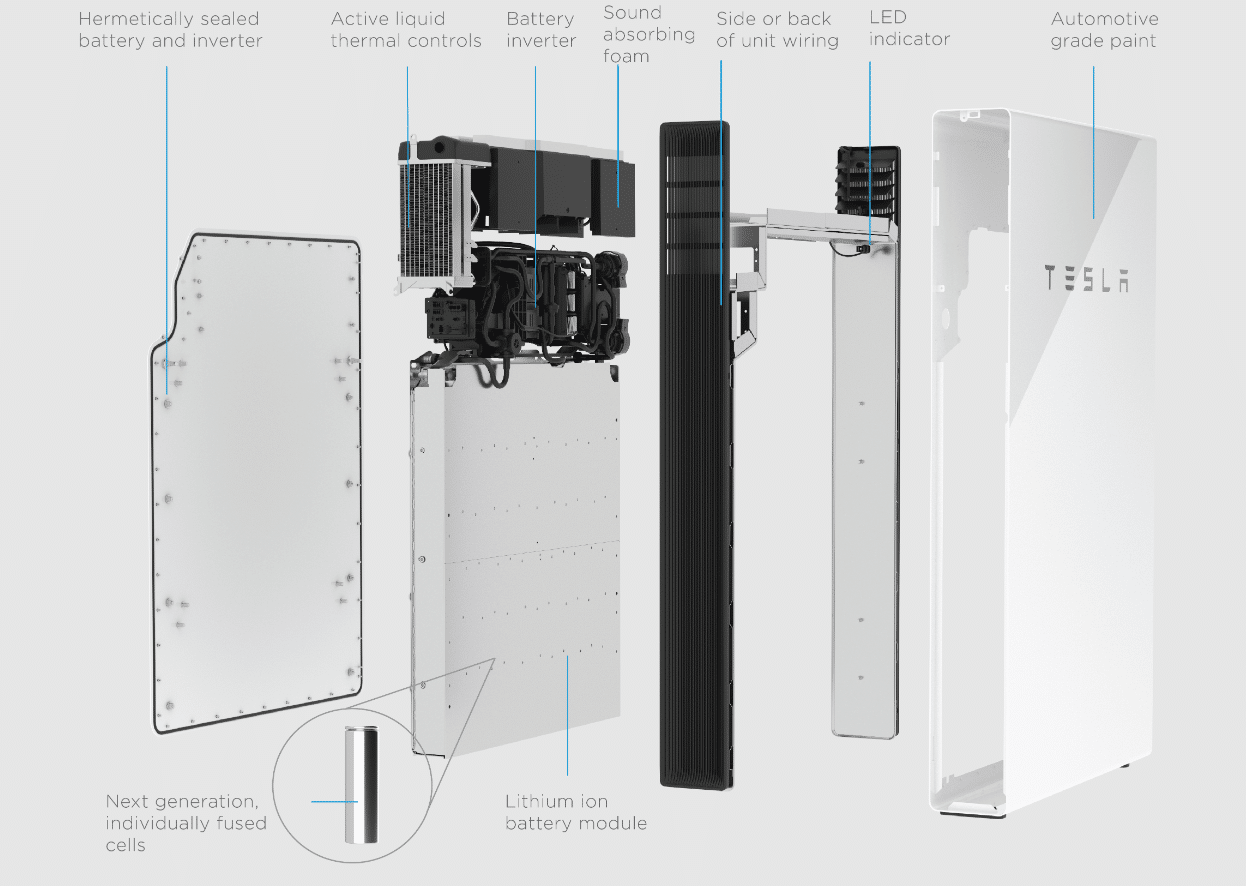
Once a delivery date has been agreed with the frame supplier, the onus is on the main contractor and client to get the substructure ready on site to receive the frame. For a larger project or if there is very limited space on the site for storage, delivery may be in two or three stages, but usually most of the kit will arrive on one day, with some other items such as roof trusses or chipboard following later.
It is possible that some of the peripheral items bought from the kit supplier, such as plasterboard or insulation will come directly from the manufacturer and it may be necessary to arrange delivery separately with these companies.
Everyone on the main contractor team must be aware of all the delivery dates and their importance, so that the necessary work is complete and ready when the erectors arrive on site.
Always check early on that vehicle access to the site is adequate for the delivery lorries. To be ready for the frame to be delivered and erected:
- Date, timing and content of deliveries agreed and confirmed in writing.
- Substructure, walls and ground floor (if concrete) ready and built within the tolerances specified by the kit supplier.
- Space within the site for temporary storage of the larger components.
- Tarpaulins available to protect loose timber items.
- Secure, dry storage, available e.g. portacabin or container
- Locations of any cranes on the site worked out and agreed.
- A clear, unobstructed route wide enough for the delivery lorry prepared.
- Someone to be present on site responsible for co-ordinating with the kit supplier.
- A full set of drawings, specifications and fixing schedules available on site.
- Scaffolding must be ordered and coordinated with the kit supplier’s build programme.
Erection of the frame
Unless the general builder has extensive experience with the particular kit system being used and has the agreement of the supplier, a specialist team from the supplier should be used to erect the frame.
The skills required are over and above those of a typical carpenter on a building site, because the frame has been made to very fine tolerances and each system has its own idiosyncrasies that must be respected. If the frame is erected by the supplier, it also provides a single point of responsibility should any problems develop.
Accurate setting out of the position where the foundations are to be placed is essential as the kits are precision made with tight tolerances. ‘Setting out’, that is creating a precise template for the general builders to work to, usually indicated by pegs in the ground with string run between them, is a crucial job.
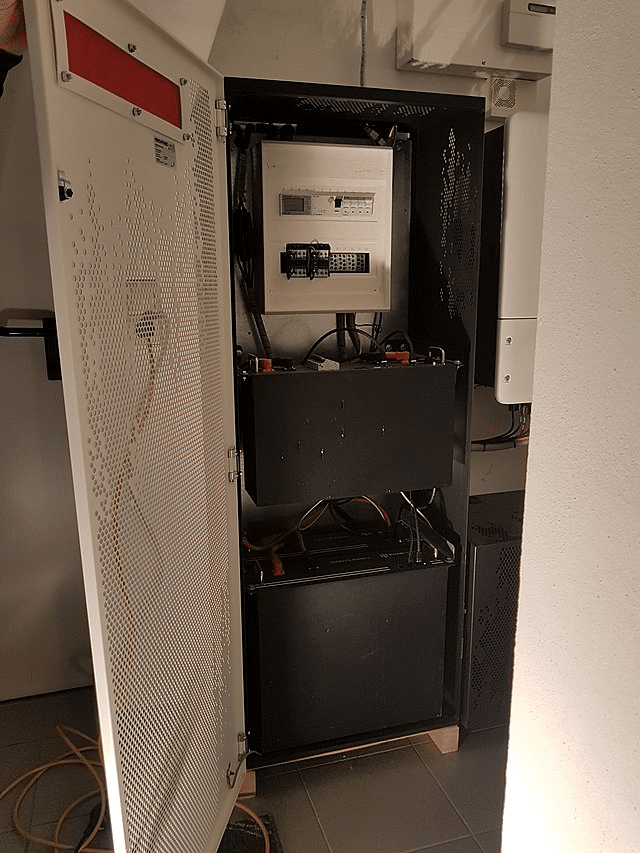
The joints need to be very tight and secure for their structural integrity – the result is a very rigid box, to an exact size. The slab must be very level and absolutely square in plan, if not, the frame will settle once it is in place and not fit together properly.
Sometimes the plasterboard lining is designed as part of the bracing or racking to the walls, and if this is the case, the temporary support should remain in place until the lining of the internal face of the walls is complete.
After the frame has been erected, the scaffolding has to be moved out slightly all around the outside of the house to allow space to either fix cladding or construct a skin of masonry. The breather membrane and roofing felt are fitted as soon as possible after the frame is up to help the frame to start drying out and provide a sheltered interior for other trades to start work inside.
Completion of the general builder’s work
Once the frame is in place and the erection team have left the site the general building tradesmen move in to complete the house. There is less room for the builder to improvise when working on a timber frame. Moving an internal wall or drilling
a large hole in a floor joist for a drainpipe are to be avoided, and all the manufacturer’s specifications with respect to fixings such as ties and straps should be followed exactly. Any departures from the specification and drawings for the kit must be approved by the supplier or a structural engineer.
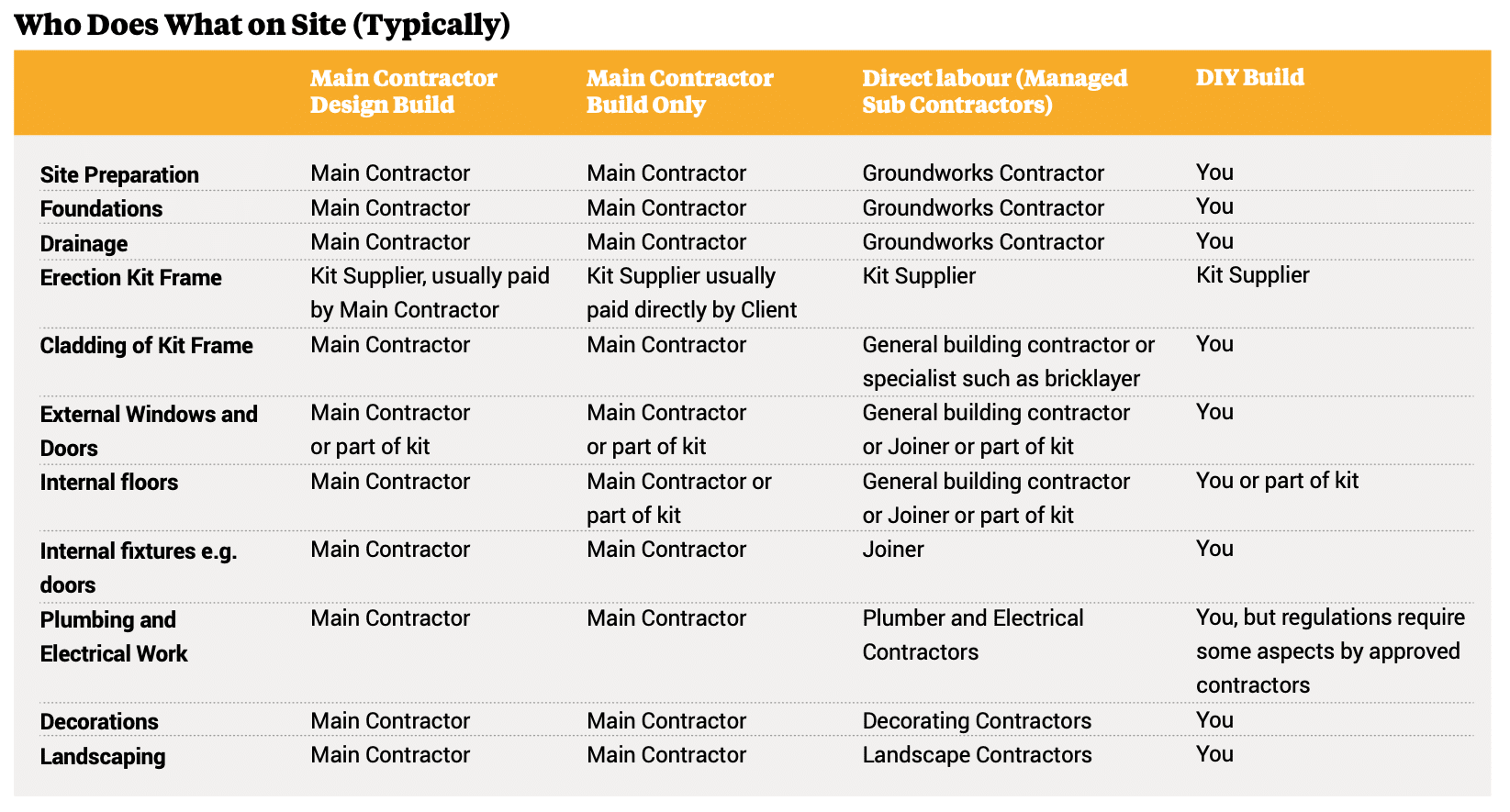
Eco builds
Timber frame kit suppliers will often use breathable insulation materials but may also use modern insulation methods such as PIR or phenolic boards. There are in fact many insulation products to choose from, all of which will form part of your specification and which needs careful consideration in tandem with your airtightness strategy.
Eco builds, or structures that mostly use natural or renewable materials, will often use htimber frame as the supporting structure. Straw or hemp builds that are DIY driven will typically use timber as the basis to work from to fill a frame built on site (not a kit).
Breathable plasters such as clay or lime have to be used with natural insulation products.