In this article we cover:
- Cost comparisons of bungalow vs two storey house built out of blockwork
- Timber frame cost comparison for bungalow vs two storey
- How the cavity dimensions impact on costs
- Floor to ceiling height cost differences
- Wall finishes cost differences
- Explainer of how the walls are built up
- U-value requirements and insulation variations
For cost purposes, external walls refer to the structure of the main external envelope of the property. In most cases it’s the main structural element and also the area that’s most visible and, along with the roof, lends character to the build.
The external wall will start at the internal ground floor level of the property (the DPC level at which the substructure element stopped) and extend to the wall plate level of the roof construction.
The cost of external walls is down to three main factors: height, makeup, and finish. The height of the walls will depend on factors such as the number of floors and floor to ceiling height, with the cost increasing with the height.
Cost of blockwork and timber frame walls
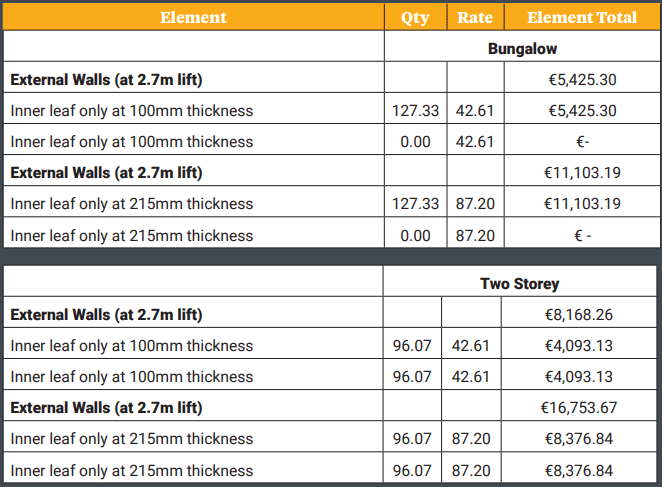
The makeup of the walls is an important aspect of the calculation of the U-Value of a property, which must meet the new building regulations requiring a U-Value greater than0.7 W/sqmK. The better the U-value the more insulation there is.
The most common method of external wall construction remains traditional cavity wall construction, while timber frame has also seen a revival, especially in large scale housing developments. Insulating Concrete Formwork is picking up speed in ROI too.
Cost notes: rates have been left the same for the same works and it is assumed specifications are the same; costs exclude accessories or scaffold.
Cavity wall construction costs have increased 19 to 41 per cent since our analysis four years ago, on average 36 per cent. In order to comply with building regulations the current cavity wall makeup will generally include an outer leaf, a cavity with at least 125mm of insulation, an inner leaf and a drylining or insulated plasterboard finish.
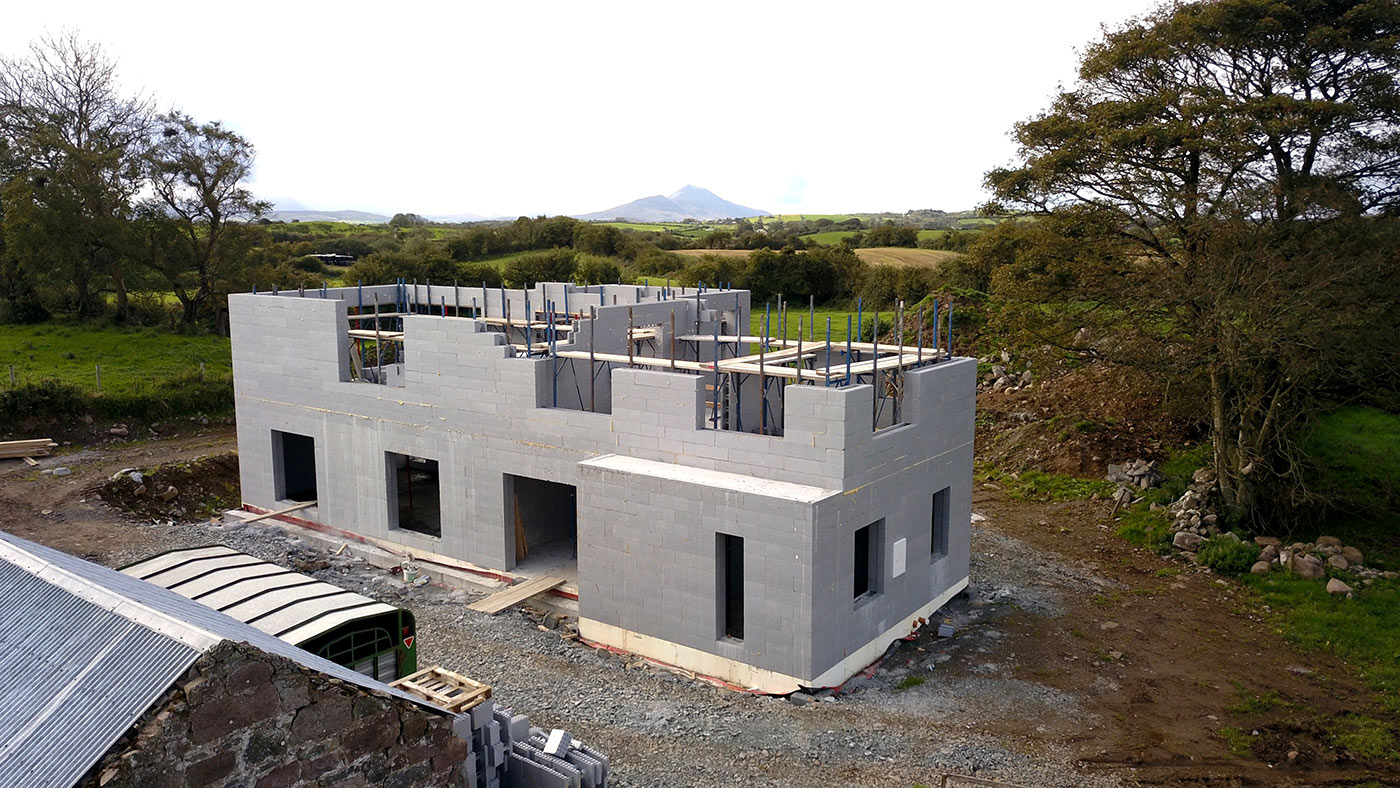
The thickness of the internal insulated plasterboard will be dependent on the overall U-value requirement of the wall. The final cost of this item will depend on that selected thickness but on average the material cost of the plasterboard will increase by 10 to 12 per cent for every 10mm of insulation thickness.
The inner leaf of blockwork will generally be either 100mm or 215mm in width. Where the inner leaf is not carrying the load of a precast floor slab construction it will generally be 100mm wide but 215mm will be required where precast or similar floor construction is required to be carried by the wall.
This change alone will double the quantity of blocks in the inner leaf of a cavity wall as outlined below. A 100mm wide blockwork wall has 9.88 blocks per sqm but a 215mm blockwork wall has 20.22 blocks per sqm.
The cavity is then generally either a fully filled or partially filled with 100-150mm thick insulation (either board or pumped-in beads). The brand and thickness of insulation will vary in cost but on average costs will increase with every 10mm of insulation thickness by circa 10 per cent.
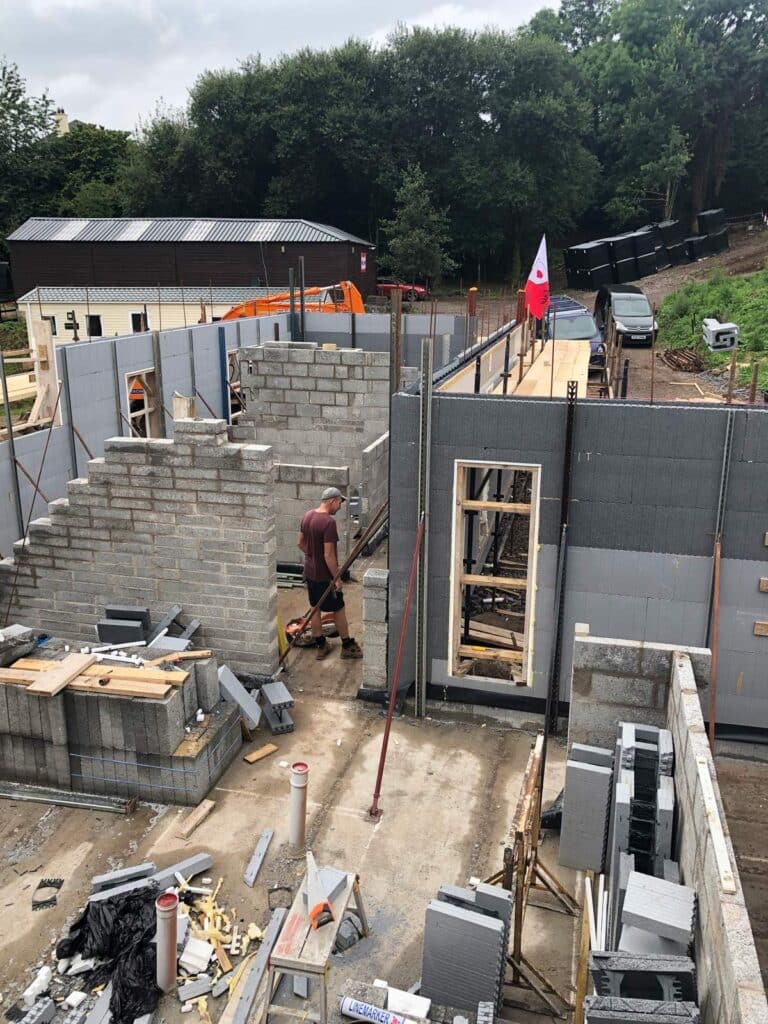
The blocks themselves can be standard concrete, insulative concrete up to insulative clay and costs will vary according to this.
Timber frame and Structural Insulated Panels (SIPS) construction The inner leaf will be the timber frame structure which will be specifically designed by a selected manufacturer. The cost will vary depending on the design, member sizes and required U-value and differs greatly from company to company.
Timber frame companies will cost their proprietary systems as a whole; the insulation is integrated in the wall construction makeup and this cost is included in the designed system. In standard timber frame you will get an option of different types of insulation, SIPS generally consists of OSB bonded with board insulation. External wall insulation systems the inner leaf of blockwork is generally the only leaf and as such it is usually 215mm wide as it will form the loadbearing structure on which any floors and roof will rest. The wall is then externally insulated.
Floor to ceiling height
To identify the impact of floor to ceiling height on costs we analyse both property shapes for three different floor to ceiling heights. The costs are based on a standard cavity wall construction with a 100mm outer leaf and a 100mm inner leaf of blockwork.
The comparison below is based solely on the cost of the blockwork and takes no account of any openings, which in general block layers will measure through when calculating their costs.

How the wall is finished
The outer leaf of a cavity wall is the main rainscreen element of the structure. It will generally not form part of any loadbearing aspects of the design and it can be finished in a number of ways. The outer leaf is most commonly a 100mm thick concrete block or a selected brick finish. Where a stone finish is required this will generally be installed to the front of a blockwork outer leaf.
The difference between the cost of an outer leaf of blockwork and brickwork will be substantial. Although a finished product (an outer skin of blockwork will require an additional finish, most commonly plaster) in itself, the cost of brickwork is expensive simply due to the quantity of bricks generally required.

In a timber frame system the outer leaf will be installed in exactly the same manner as that of a cavity wall system but the blockwork will need to be tied in to the timber frame for structural stability.
Following completion of the timber frame kit erection, scaffold will be installed to the perimeter of the building and a selected outer skin of blockwork or brickwork will then be installed as outlined above. It is also possible to install a rainscreen on a timber frame kit using a cement board fixed directly to the timber frame finished in a plastered finish but at present this is not a vastly commonly used approach unless you want to finish the house with cladding.
In an external wall insulation system the outer leaf will in effect be the external insulation system. Costs on these systems vary greatly from manufacturer to manufacturer and it is advisable to shop around.
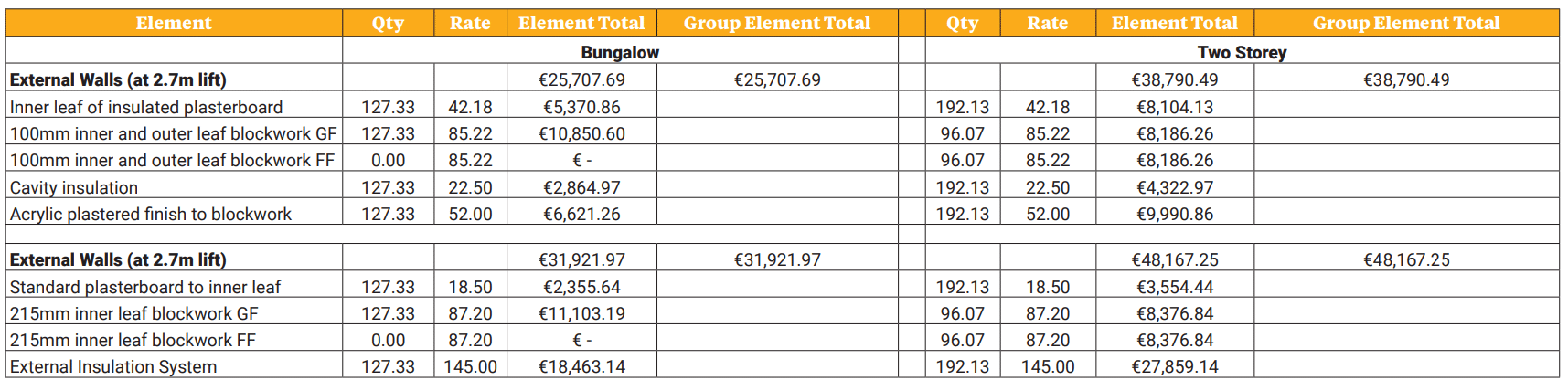
Other cost components
External walls have openings for windows, doors and the like. It is common for block layers to charge for their works “through openings”. In calculating the quantity of blocks to charge for on a project, block layers generally measure a building as if no openings exist.
The selection of the materials will have a direct impact on costs for a project. Traditionally concrete was used for sills but over time imported granite and stone alternatives have become commonplace. These generally come at a higher cost.
Due to concerns in relating to airtightness and thermal bridging, insulated products are becoming increasingly popular and have the advantage of being more lightweight and easier to deal with in terms of health and safety.