In this article we cover:
- What is insulating concrete formwork (ICF)
- Typical timeline for an ICF build from start to finish
- How it compares in cost with traditional masonry construction
- The layers in ICF
- How does ICF comply with regulations
- How does ICF impact on your design and where it can save you money
- Mortgage and insurance considerations
Formwork
In construction, formwork refers to a temporary shutter/mould into which concrete is poured and formed. You can also mould lime or hemp lime mixes in this way.
If you want to build an in-situ concrete wall, you will need to cast it in shuttering or formwork made of plywood or other board material. The shuttering is tied and propped the required distance apart to form your mould which is then filled with concrete.
When the concrete is set you can remove the temporary timber shutters, leaving you with a cast in situ concrete wall. A very labour intensive and costly exercise.
Now imagine you didn’t have to strike (remove) the shutter but instead, it’s part of your wall.
Expanded Polystyrene (EPS)
With Insulating Concrete Formwork (ICF) there is no timber formwork. The shuttering is made of expanded polystyrene (EPS) which is lightweight and interlocks together. It can be built like a traditional block wall, one on top of the other. Instead of mortar, you have a sealant you apply with a silicone gun. And when you are at the required height, you pour your concrete into the mould.
You now have a solid concrete wall with an inner and outer shutter of EPS. What’s important to remember is that you now have a solid concrete wall, not an EPS wall. The EPS is the shuttering that you leave on to provide insulation. The wall is made of concrete.
Remember that you as the owner will be the person filing the documents with building control: the building notice in NI (you need to file one for the drawings and another before you start), or the commencement notice in ROI. In those documents, you can file that you are building a solid concrete house. Not a house made of EPS. I have had some queries from ROI Building Control about the description of the ICF materials used to build the house. Structurally, it’s mass concrete.
Building regulations
There is no one standard for EPS blocks. There are in fact several ICF suppliers on the market who supply different certified EPS blocks. Common wall thickness we have used in one-off dwellings over the past 12 months consisted of:
– 100m EPS external leaf
– 150mm reinforced concrete core
– 100mm EPS internal leaf.
The height of the blocks is typically around 400mm. This build up achieves a U-value of approximately 0.14W/sqmK. This is based on a 12.5mm skimmed plasterboard finish internally and a 7mm acrylic render externally. Considering the minimum elemental U-value required for walls in both NI and ROI is now 0.18 W/sqmK, this build-up is building regulations compliant. It also contributes greatly to a high energy rating.
Acceptable or Accredited Construction Details (ACDs) are the go-to when it comes to checking if the work on site is done correctly. In ROI, Acceptable Construction Details were initially published in 2011 and in NI Building Control Northern Ireland published Accredited Construction Details in 2015.
The ACDs are to be read in conjunction with TGD Part L 2021 Dwellings (ROI) and Technical Booklet F1 2022 (NI). There have been several iterations over the past 11 years, mostly focusing on thermal bridging and airtightness.
The ACDs make for a good read if you’re technically minded as they are presented in two parts. Part 1 discusses the general theory of insulation continuity and airtightness in construction. Part 2 provides indicative detailed drawings of thermal insulation and airtightness details for specific construction interfaces.
However, ICF systems are not covered under the ACDs. This is why it is important to work closely with ICF suppliers, certified installers, and architects with experience in the use of ICF.
In both ROI and NI, some ICF suppliers have all critical details thermally modelled by a National Standards Authority of Ireland (NSAI) registered thermal modeler or Building Research Establishment (BRE) registered modeller in NI.
Psi values measure how thermally efficient the house is and you will get a better energy rating if you don’t use the default Psi value. With an ICF house it’s better to have the energy assessor calculate it with the Psi value calculator, as detailed in the technical guidance documents.
ICF construction comes into its own with thermal bridging; because you are dealing with a continuous solid wall construction, you are reducing the likelihood of heat escaping.
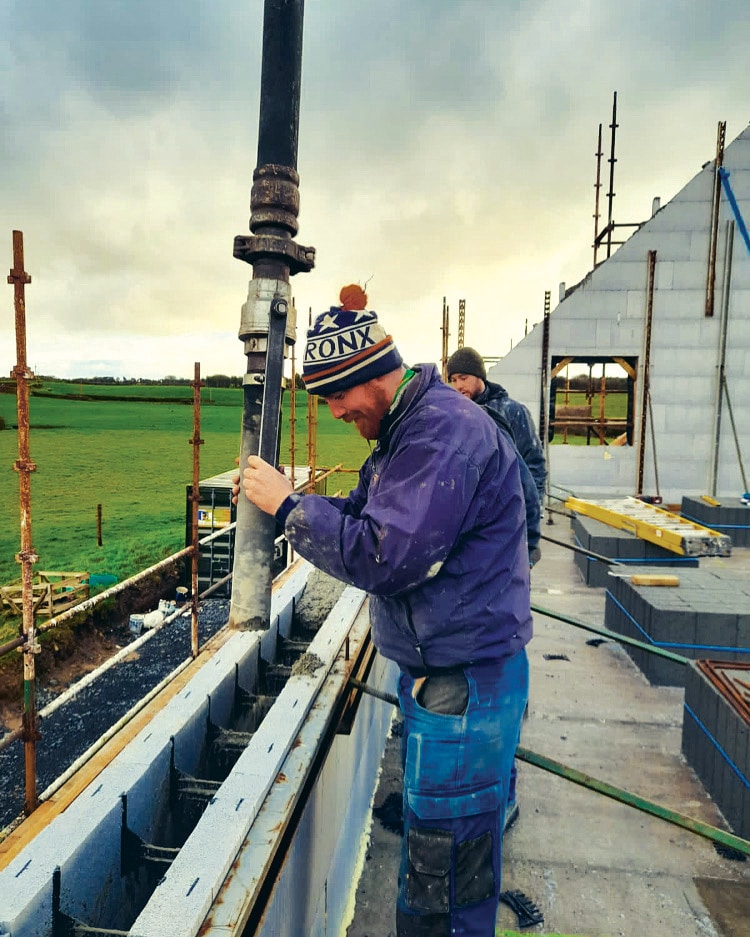
Mortgage and insurance
To date, our practice has had no issue with the banks approving mortgages for ICF dwellings. Similarly, I have had no issues reported back by clients on insuring their dwellings, during or after construction.
All certified ICF systems, built as specified on the certificate, meet the requirements of fire safety concerning means of escape, the internal spread of flame and the external spread of flame.
Design Process
In my experience, the design process does not differ significantly when designing for ICF. If possible, it would be good practice to keep window and door openings and floor levels to ICF block dimensions.
Your typical ICF block is 1200mm long by 400mm high by 350mm. Trying to achieve this in the design may reduce the amount of waste and also labour in constructing the formwork prior to the concrete pour. This does not mean that you are limited to just square boxes – quite the contrary.
ICF is ideal if you plan to have curved walls – when building with other methods, curved walls usually add to the cost but not with ICF.
You will need to take into account how the external finish may impact on the cost and complexity of the build. For instance, the use of some external cladding systems such as stone, timber, and metal cladding may lead to constructability issues at roof junctions or overhang details, for example, or weathering.
Cost of ICF versus traditional masonry build
This is a very difficult topic to address given the current market volatility around the cost of insulation and other relevant construction materials. I can only speak from my current experience and at this point in time, to build to current energy standards, ICF is slightly cheaper to build than your traditional masonry build. But not by much.
ICF roofs
Still in its infancy I have only detailed one in all my years’ experience which never made it to site due to the pandemic.
Much like the walls it’s very fast to erect and also very safe as you are not dealing with heavy loads at height. However, the roof system still requires a primary steel structure to carry large spans.
Typical Timeline
For an average 2,000sqft single storey house with a simple design. Lead times on materials such as reinforcing bar, structural steel etc. not accounted for in any of the
time estimates below.
Insulated raft foundation installation
two weeks including radon barrier
First concrete pour
one day
Curing time
two days for the concrete raft to cure (technically you could walk across the slab after 10 hours) before starting the ICF build – as opposed to seven days for a traditional block house built on a raft foundation
ICF block lift to first
floor level
two weeks
Second concrete pour
one day
Hollow core placement (assuming all structural steel elements are in place) one day
Second lift of ICF walls to wall plate
two weeks
Third concrete pour
one day
Roof (standard cut timber A roof counter battened with a natural slate finish) approximately three weeks.
Rendering (weather permitting)
two weeks