The ICF walls can be taken directly off your traditional strip foundation, raft foundation, or best in class, off your insulated raft foundation.
In this article we cover:
- How ICF projects are costed
- How to minimise thermal bridging at the wall/floor junction
- ICF with traditional strip foundations
- ICF with standard raft foundations
- ICF with insulated raft foundations
Traditional strip foundations for ICF
The one downside I have found in bringing ICF off a standard strip foundation is that a contractor will have to carry out two concrete pours to get to first floor level on a two storey house, and to wall plate level on a single storey house.
That’s because you first need to pour up to the finished floor level where you need to add a horizontal damp proof course. The second pour can then take place to the wall plate or first floor level.
The small issue (additional cost) of the two concrete pours can be eradicated with a standard or insulated raft.
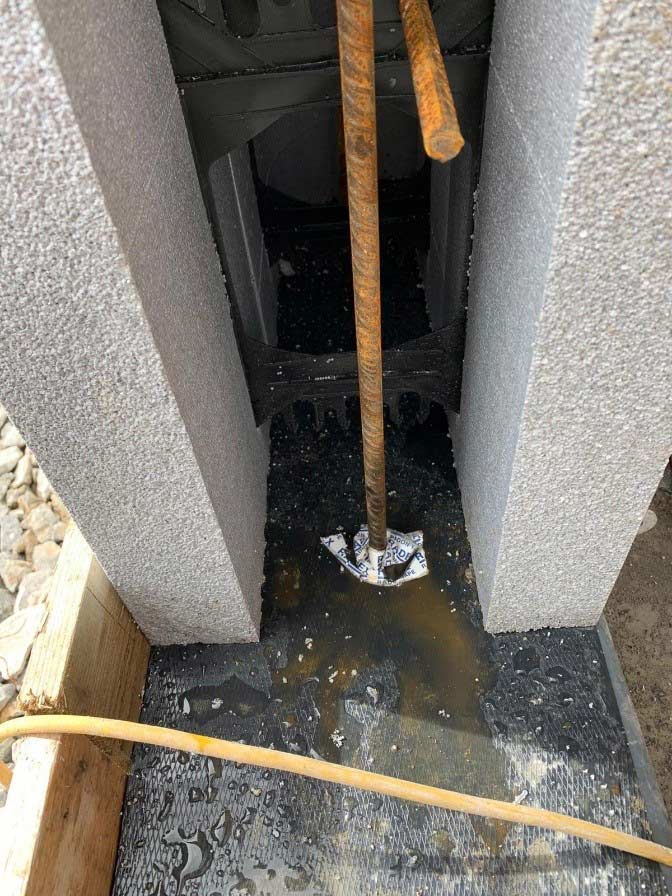
Standard raft foundations for ICF
There is currently an ongoing debate among industry professionals as to the necessity of vertical reinforcing bars at the edge of foundations. Thickening the raft or the strip foundation punctures the horizontal damp proof course at finished floor level every 1200mm centres.
This leads to a very costly and labour intensive detail where each protrusion is required to be sealed with radon and moisture resistant tape.
But is the rebar required at all? I have inspected some sites where the contractor has poured them as per the structural engineer’s detail and then when laying the first row of ICF forms, they cut away the rebar.
If you take a standard blockwork house, where the walls are built directly off the foundation without any rebar, what’s the fundamental difference? Two other alternatives for the horizontal damp proof course (DPC) allowed for in the certified ICF systems are as follows:
A plastic applied DPC across the wall at 150mm above external ground level.
The use of waterproof concrete up to a minimum of 150mm above external ground level, which in practice requires two concrete pours and once again is a costly option compared to the more traditional horizontal DPC shown in Figure 6.
Recently I have seen the introduction of a hydrophilic strip placed on the raft slab in the centre or slightly off centre depending on the cover required by the strip. This can negate the need for the horizontal DPC. However, my advice here would be to have it installed by a competent installer.
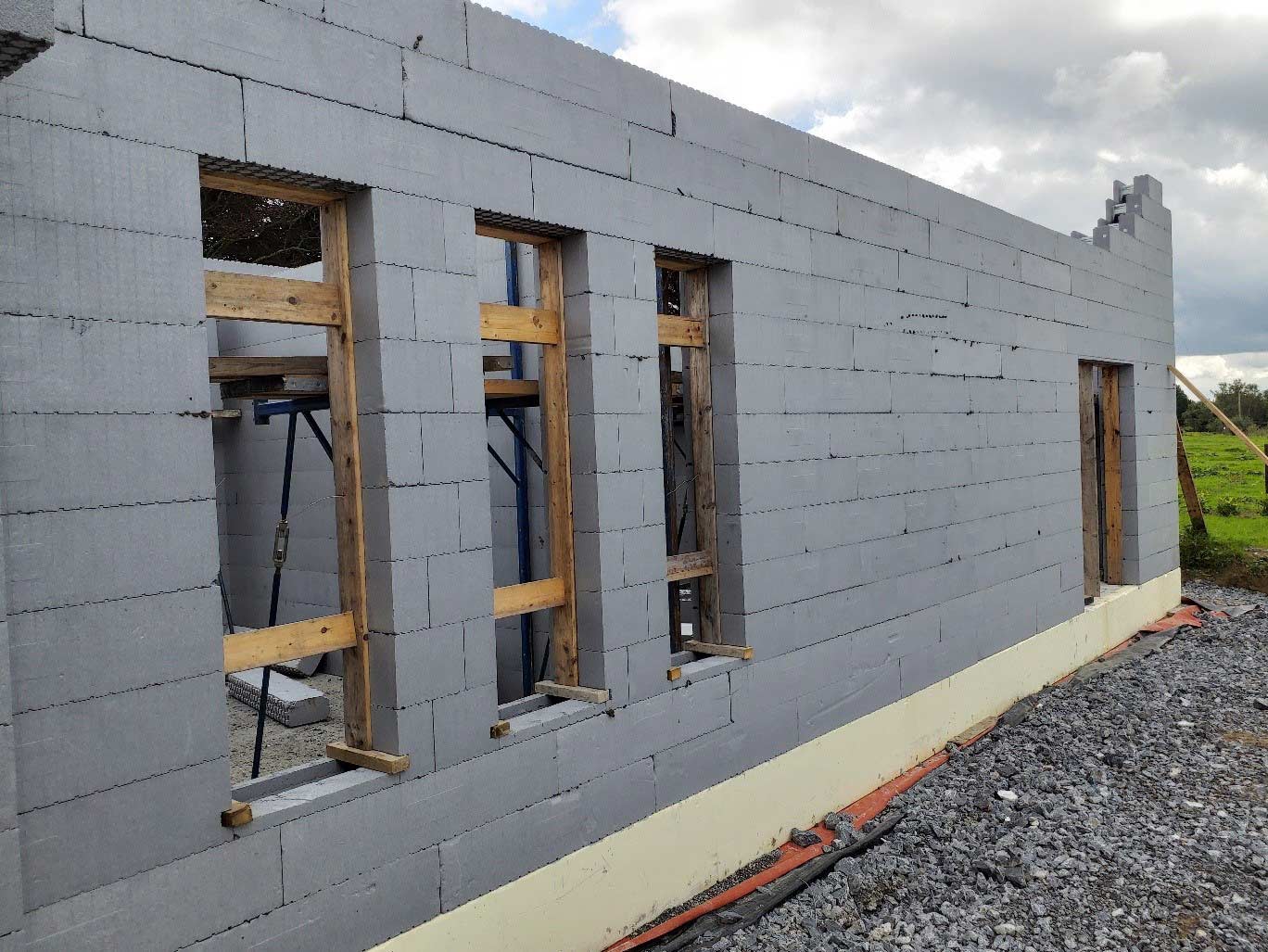
Insulated raft foundation
From experience, an insulated raft foundation is the best thermal and damp proof detail out there. In Figure 2, the white EPS is the insulated raft and the grey EPS is the ICF system. There is continuous insulation wrapped around your building, with no breaks or gaps for a thermal bridge.
On this particular project, we placed the radon barrier beneath the insulated raft which provides considerable protection to the radon barrier, preventing it from tearing due to the installation of rebar and subsequent pouring of the floor slab. We also used the hydrophilic strip for the horizontal DPC.
However, the insulated raft is now your finished floor. Should you wish to have a polished concrete floor then ICF may not be the way to go. If a standard cavity wall had been built, then there would be no issues with a polished concrete floor because there is no need for propping a block wall. Props for the ICF have to be fixed to the floor for stability when pouring the concrete.
See Figure 3 of the prop fixed to a finished floor slab that was eventually polished. In this particular project the clients were happy to see the prop marks from the fixings on their finished floor however, we have had clients who want them polished out which can be difficult and costly.
A critical point to note: if using a tanking membrane below ground, say on a basement wall, ensure no primer is used on the EPS as it will erode the EPS. And this will make the tanking membrane useless. Speak with a tanking specialist to ensure the correct membrane is used for ICF walls.
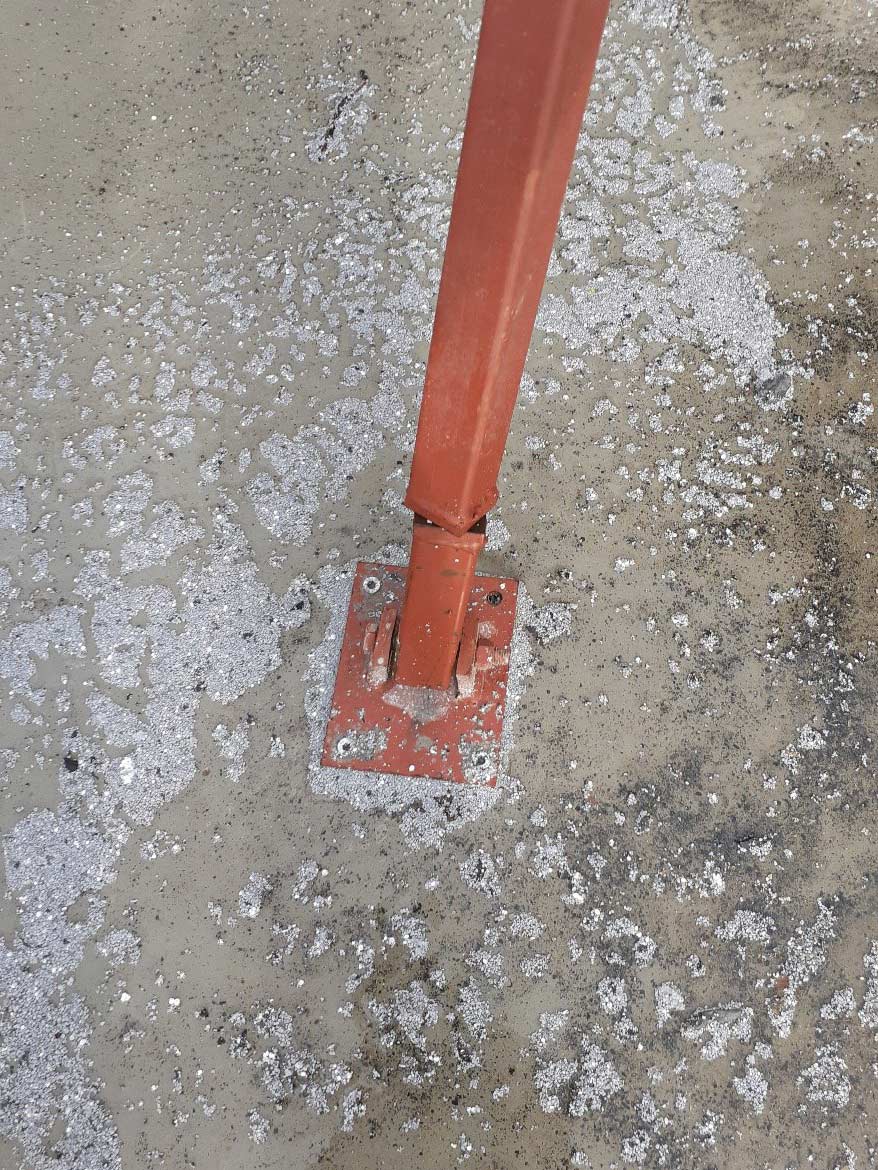
How are ICF projects costed?
ICF manufacturers will each have different cost points depending on how they make their blocks. The price of these will be partly determined by the cost of EPS and other components such as the webbing but will mostly be related to their manufacturing processes and efficiencies.
Manufacturers have a network of approved installers who will be the self-builder’s contact point for pricing an ICF job. They will include the cost of the blocks, their own labour/margin, and also the cost of concrete, steel reinforcements, propping and other materials required, including scaffolding and other standard building materials and equipment.
Pricing will also hinge on factors such as geographical location and the type of project – due to economies of scale, a one-off house is likely to have a higher cost per sqm than a development or a commercial unit for example.
Concrete is one variable within ICF construction projects which self-builders can organise themselves, as agreed with the ICF contractor. For poured concrete, the price increase has been of 5 to 7 per cent over the last 18 months.
Jamie Smyth, Stax ICF staxicf.ie