In this article we cover:
- What is cavity wall board insulation with pros and cons
- What is EPS bead insulation with pros and cons
- Typical build up of cavity board insulation on site
- Typical installation for EPS bead insulation
- Where to use board or bead insulation
- How much does board insulation cost
- How much does bead insulation cost
A popular method of insulating new build cavity walls is to fill the gap in between the two leaves, either by pumping them with EPS beads or by adding rigid board insulation. So which is better, beads or board insulation?
In NI and ROI partial fill cavity wall insulation is widely considered to be the most traditional wall construction build up. The cavity is there to reduce the risk of moisture soaking through the external wall. In a bid to reduce heat loss, nowadays cavities are built wider than in the past to allow for insulation to be installed within them. By insulating inside the cavity you reduce the need to insulate on the inside of the house or externally.
HOW MUCH DOES IT COST?
Contractors typically charge €10-€12/£10 per sqm to pump the walls with 150mm of platinum EPS bonded beads. It typically costs €9-€10/£8 per sqm to achieve the same value with PIR insulation boards so there is not much in the cost difference.
Further reading: Lecompte, J. (1990). ‘The Influence of natural convection on the thermal quality of insulated cavity construction’. Building Research and Practice, No. 6, pp. 349-354.
Board insulation
For current standard construction detailing, a typical wall build up would consist of a brick or block outer leaf, 40mm clear cavity, 80mm insulation, 100mm block inner leaf and internal plaster. The insulation is protected in the cavity and is installed by the block layer as he builds the walls. Housing standards have improved over the past two decades and so have insulation products. PIR insulation boards have replaced polystyrene because PIR has a lower conductivity which means you can achieve the same insulation value with less thickness. Phenolic foam is better again.
‘To achieve the calculated U-value, which measures heat loss, the insulation must be tight against the inside leaf. ’
A 150mm cavity with 110mm PIR can easily meet the current building regulations and achieve a U-value as low as 0.18 W/sqmK as outlined in the new ROI Part L building regulations coming into force this year.
This means an insulated slab on the inner leaf of the wall is not required to boost the U-Value. This in turn has the benefit of maximising the thermal mass, (masonry’s ability to store and slowly release heat), in the building. While partial fill insulation makes a lot of sense and can be very cost effective, it is difficult to get it 100 per cent right. To achieve the calculated U-value, which measures heat loss, the insulation must be tight against the inside leaf.
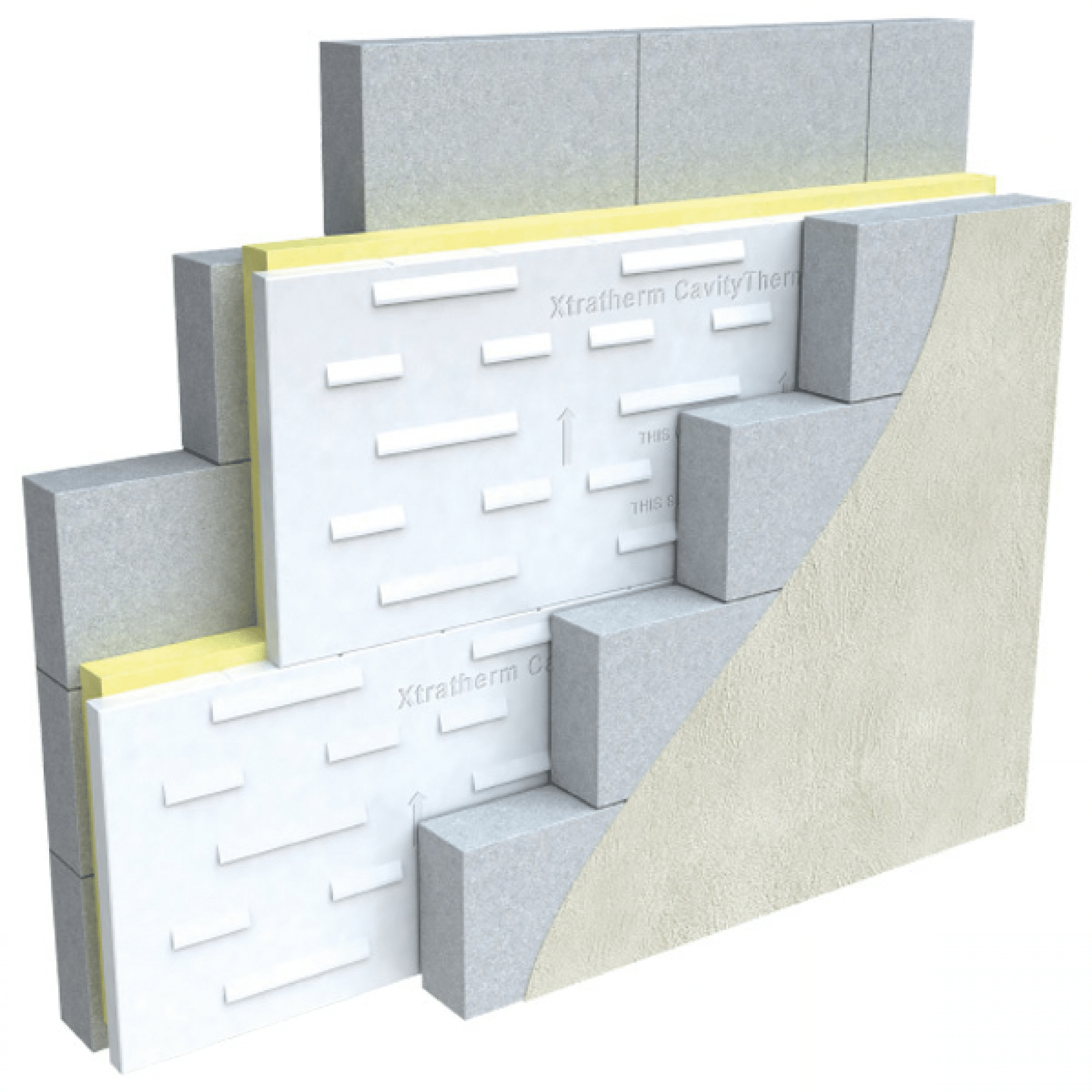
Any air gap between the insulation and the wall on the warm side of the cavity causes thermal looping. Thermal looping happens when there’s an air gap between the insulation boards and the inner leaf of blockwork – this leads to heat getting drawn from the inside of the house into the cavity. This considerably reduces the effectiveness of the insulation. A study (see Further reading page opposite) carried out in the early 1990s shows that a 5mm air gap causes a 35 per cent reduction in insulation effectiveness, 10mm a 93 per cent reduction and 15mm a 180 per cent reduction.
These are alarming results. If a wall is designed to meet a U-Value of 0.21 W/sqmK, the actual U-Value with 10mm gaps would be 0.4 W/sqmK. This does not even come close to complying
with the building regulations. 80mm PIR will achieve 0.21 W/sqmK but with a 10mm gap it is the equivalent of 40mm PIR. A 5mm gap would be well within a block layer’s tolerance for accuracy but considering mortar droppings and small pieces of aggregate falling into the cavity, less that 10mm is hard to maintain.
This is a widely recognised problem and manufacturers have tried to address it with tongued and grooved insulation boards and full fill solutions (straight edge sheets installed on top of each other). This means that a 150mm board is added to the 150mm cavity as the block layer builds the wall.
This leaves no tolerance for the block layer and the cavities must be kept spotlessly clean. When there is an obstruction in the cavity it is easier to cut out a piece of insulation than to take down the wall to remove the obstruction, which can lead to more thermal looping.
Cavity closers (images Xtratherm)
Beads
Many people are now opting for pumping the cavity walls with bonded EPS beads after the wall is built rather than relying on the block layer to put the insulation in as he goes. This also requires that cavities are kept clean but with a 150mm wide clear cavity there is much more space to maintain a clean cavity.
The walls are drilled and pumped before the final coat of external render is applied. The bead is pumped at high pressure and mixed with a binding agent so the beads bond together in the cavity. The binding agent is very important as it allows the beads to become a solid mass. This helps to prevent moisture migration across the cavity, it also prevents the beads flowing out if the walls are opened for alterations or drilled for services. This system is fast and cost effective.
External wall pumped with EPS beads – all images KORE Insulation
However some would say that the air gap in the cavity is there for a reason, so there is no bridge for the moisture to pass from outside to inside. This is a fair point and not all houses are suitable to be pumped.
All bonded bead systems in ROI should have an NSAI Agrément Certificate (IAB)/ in NI a BBA Agrément Certificate with details of how the system should be used and where it should not be used. The NSAI certs state that the beads do not promote the migration of moisture across the cavity if the bead is applied as per the NSAI Certificate. Also ensure the system is installed by an NSAI Registered Contractor. Caution needs be taken where houses are in highly exposed areas to make sure the external render has no weakness or defects that may allow driving rain to penetrate the wall. It is not acceptable to pump brick walls in areas identified on the certificate – coastal areas are off limits.
Any wall that’s not plastered or consists of fair faced blockwork should not be filled with beads either. In addition to cavities and wall ties being kept clean and free of mortar, know that bonded beads should not be in contact with cables and ensure all cavities are closed prior to pumping, especially at the wallplate (top of wall).
As with any system, if you do not follow the instructions there is a chance of failure. 150mm of bonded bead can meet the current maximum U-Value requirement of 0.21 W/sqmK. Better U-values can be achieved by increasing the width of the cavity but this has structural and cost implications on foundations and wall ties. Alternatively, an insulated slab can be added internally to achieve a lower U-value. This adds more cost to the build but also helps eliminate thermal bridging.
Beads or board insulation?
PIR INSULATION
Advantages
Can be installed as the walls are being built to ensure all sections are insulated
Lower U-values can be achieved without the need for wider cavities
Can meet the nearly zero energy building standard without an insulated slab internally
Some suppliers provide thermal bridge free details
Disadvantages
Difficult to install correctly and poor installation reduces the effectiveness of the insulation
10mm gaps in between the insulation and the internal leaf can reduce the U-value by up to 97 per cent (thermal looping)
EPS BONDED BEAD INSULATION
Advantages
Walls can be built faster
Easier to keep the cavity clean
No risk of thermal looping
Fully fills the cavity to ensure insulation continuity
Disadvantages
Must be installed correctly to avoid the risk of moisture problems
Some limitations regarding where it can be used
A wider cavity is required to achieve lower (better) U-values
May need an insulated slab on the internal wall to achieve low U-values
Words: Jeff O Toole