
Achieving these two aims means building houses now that meet strict criteria on energy, emissions and sustainability. If we are to take these seriously, we will need to change the way we build to one where we use materials and systems that not only save us costs in the future, but that we can afford to pay for now. I believe this will have to be a more dramatic change than many people are prepared for at present. The systems introduced over the last decade have largely been engineering solutions using combinations of existing materials in new ways, or new or improved energy technologies. The question is: is it possible to build zero carbon houses? I believe it is, and the answer is to use hemp.
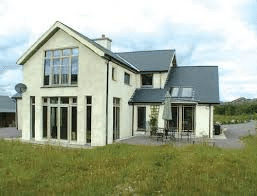
Hempcrete hemp-lime bio-composite
Since the mid 80’s there has been a growing market for hemp products, especially in the food and clothing sectors. hemp has very good ecological credentials as it not only helps the land it grows upon, it also provides products with many health related qualities such as high levels of nutrition from the seed or improved comfort/durability from insulation made from its fibres. The processing of the plant involves separating the seeds and fibres from the main stems, leaving behind the woody core of the stem in chipped form. These particles, called hurds or shivs, were formerly thought of as waste, but in France in the mid 1980’s a man named Charles Rassetti came up with the idea of using them as an aggregate with a lime based binder to provide infill to the medieval oak framed house he was repairing. It soon became apparent the material had more possibilities than just Heritage repair and so was developed as a new build option when cast around a timber frame.This technology spread in the 90’s to Switzerland, the UK and to Ireland where it has been used on a great variety of projects, these have proved its flexibility of application and signalled a promising potential.
Unlike other materials there is no particular ‘look’ to a hemp building, it can be built up with perfectly straight and level walls or manually applied to give a hobbit house like appearance. Hempcrete thus has an advantage over materials such as straw bales or cob houses when it comes to the future marketability of the houses as they can have a very conventional style.
The use of hemp in construction raises issues over the direction we take to achieve sustainability goals. Are we to rely on depleting resources such as oil or steel or are we going to take the direction offered by bio based materials for absorbing CO2 (annually for hemp, every 20 years for timber), rather than releasing the CO2 stored by coal, gas and oil which took thousands of millions of years to accumulate?
Hempcrete has become the generic name for a mixture of hemp shiv and a binder (usually lime based), to produce a hygroscopic ‘breathing’ bio- composite material. It is generally not considered to be load-bearing and as a result is used to create a high performing envelope around a timber frame. However, load-bearing variations based on clay mixes which can be tamped or purchased in the form of pre-cast blocks, have been developed in Spain.
Although the insulating properties (k-value) of the various Hempcrete mixes produced are not quite as good as those for mineral fibre or foam, the thermal mass effect and exemplar thermal inertia (the ability to delay and smooth changes), helps to maintain a comfortable indoor environment and regulates humidity. Experiment is an essential process in developing all technologies and to make the concept regionally applicable, there will need to be variants suited to local materials to help reduce transport emissions. The basic properties of any binder used for Hempcrete are hygroscopicity (breathing and humidity buffering), sets fast enough to be practical on a building site and is strong enough when finally dry and set. The lime gives it porosity and is formulated to improve speed of setting. Materials with these characteristics are available around the world and can be combined to produce a suitable binder using variations of ingredients, most of which include hydrated or hydraulic lime but also other local or imported additives to improve performance. Calculations for a Hempcrete mix show a negative carbon figure for a cubic metre of the material of around -100kg making it possible to lock up carbon in a hemp structure instead of emitting it. This figure can be improved with the use of more local or less CO2 emitting materials, creating carbon sequestering possibilities to the construction industry world wide.
In Ireland there are at least 16 examples of complete houses built using this technology, each of them slightly different in the materials, design and methods used. This is quite a unique collection which provides a wide range of systems developed in the challenging conditions of the Irish climate.
I discovered Hempcrete in the late 90’s when half way through building my own home and though too late to use it to build the walls, I learnt it could be mixed with increased binder to make a plaster. I experimented with it and the cottage type appearance I achieved was not only exactly what I wanted for my home, but was admired by friends and neighbours and I was soon supplying, and in some cases installing it, throughout Ireland.
Retrofitting
It is though in the areas of retro fit and renovation that hemp has been most widely used in Ireland. The uptake of Hempcrete materials here coincided with a wider understanding of natural materials in Heritage buildings and other ‘green’ concepts such as lime mortars and renders, the use of natural fibres such as sheep’s wool or hemp and flax for insulation, and straw bale or cob techniques, some of which were often included in the projects. The overwhelming majority of these 200 plus builds in ROI and NI were self-builds. In many cases, owners were spending their weekends applying an insulating plaster to the stone walls (or cob, straw bale or clay block) of their homes and achieving a finish they were very happy with, having previously thought it beyond their capability.
With around 30% of our total energy consumption used to heat our homes, there is a huge retro fit sector where many houses are still in need of improved insulation. The health gains would also be considerable. In the UK, Bristol Neighbourhood Construction2 have taken a community approach to this, demonstrating on their own homes how Hempcrete can solve insulation and condensation problems. These projects are used to train other neighbours in the hope that the knowledge will spread virally throughout the local community and further afield.
New Build
Building complete houses with Hempcrete involves codes and regulations being applied to Hempcrete materials, all of which have undergone extensive testing for the qualities determined by certification. The most commonly used mixtures will have similar characteristics as all commercially produced hemp is now of a suitable quality. Most binders will fall into an acceptable range of strength, density and porosity if made with appropriate ratios of ingredients. Specification for these performances and qualities is at present being devised by the International Hemp Building Association3. With a basic understanding of the material and application details it is not complicated for architects to adjust plans to use this material. Similarly, builders can achieve airtight walls as the monolithic structure is cast or sprayed into position leaving only the sealing around windows or door apertures.
By adopting a ‘fabric first’ approach, with Hempcrete it is possible to create a high performance building envelope which helps achieve passive house standards. This reduces the need for technology with limited lifespans such as solar panels or heat pumps. It also provides the possibility of opening windows without all the heat escaping, as most of it is stored in the fabric of the building and not just the in the air. Examples of hemp houses built to passive house standards or approach in the UK and France have proved that heating is not needed for more than a few days of the winter. However, for an accurate BER/EPC the unique qualities of Hempcrete will need to be included in the measurements to take account of the properties of thermal inertia and the added effect of latent heat produced by the evaporation and condensation of water vapour as it moves through the wall (phase-change phenomena), to give a true result4. Software packages with algorithms for these properties are already available allowing calculations of how the property will behave as a whole, taking into5 account aspects of humidity and passive gain not included in standard ‘U’ value calculations.
Hempcrete is also suitable for multiple unit or modular building projects. The Triangle project in Swindon6 is a fine example of this energy saving in practice where the rows of terraced houses built around the central triangular green have, not chimneys, but ventilation towers. Kevin McCloud, whose company developed the project, was delighted by the low level of noise during construction and the resulting site safety for workers due to the simple installation process.
For a hemp building to achieve the equivalent of CSH (Code for Sustainable Homes) Code 6 status the production of hemp will need to be established in as many locations as possible. With no reliable supply of Irish hemp as yet we are currently reliant on producers in Yorkshire and France. Of course the importation of this to Ireland is just as unsustainable as bringing the fuel to make cement or steel and many other products, however the projects built in Ireland using imported materials do prove the concept and show what could be done. Producing hemp suitable for construction in Ireland is certainly a possibility as research for a number of years has shown, it only needs the investment to make it a reality. We also have locally sourced products that can be used to make a purely Irish Hempcrete binder, so a material that has real sustainability potential is possible in the near future.
Steve Allin
Environmental Design Consultancy, Kenmare
Tel. 064 664 1747 www.hempbuilding.com
Additional information
Ian MacCarthy, Lime Technology Limited,
Oxford OX14 4SA tel. 0845 603 1143
www.limetechnology.co.uk