In this article we cover:
- Managing cash flow
- Design process and who was involved
- Mark’s experience with the SEAI deep retrofit scheme
- How he kept on top of the budget
- Top tips for novice renovators
- Project management route and reasons for it
- How he went about the fit out
- What he would do differently
- Timeline, specification and suppliers list
Tell us about the project
Elis and I renovated and extended a 1905 house in the heart of Greystones, completed with the help of the Sustainable Energy Authority of Ireland (SEAI) Deep Retrofit pilot scheme.
We entirely gutted the house and kept two walls standing. It was a blank canvas, which in many ways turned out to be a curse as there were so many ways to configure the house. It was also a very busy time as we had a young child at the time we went for planning permission.
House size before: 118sqm
House size after: 280sqm
Extension build method: blockwork full fill insulation in cavity wall
Heating: air to water heat pump
Ventilation: centralised mechanical with heat recovery
BER after: A1
Build cost: €550,000 plus purchase of original house
Tell us about the design process
On the design team was myself, a quantity surveyor (QS) Russell Lincoln, and a friend and architectural designer, Garry Cohn. Elis and I both wanted to keep period features and stay true to the house’s original design. The question was more about what to do with the modern extension at the back, and how to reconfigure the layout.
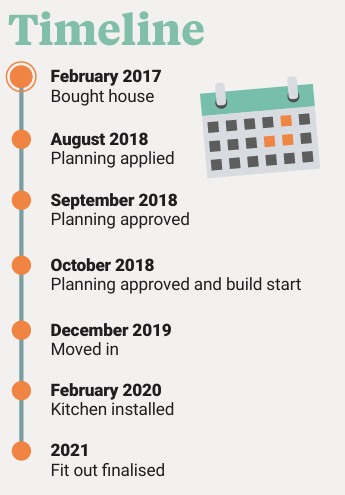
My previous house build was more straightforward than this one, in that there weren’t that many options in terms of design; it was a mews house on a small plot. I learned from the mistakes I’d made on that project, namely that the kitchen should have been bigger.
And in terms of finishes, we’d left a brick wall exposed but we should have plastered it for ease of maintenance. I have to say I was very conscious of getting everything absolutely right on this house and I got myself caught up in it.
At this point I relied heavily on Garry’s advice. I brought him on board because I quickly realised that for our forever home, I couldn’t be both client and designer. Garry brought clarity to the many different design variations running around in my mind, at a time when I was second guessing everything.
I was afraid to make a mistake I’d regret and I wasn’t enjoying the process so he helped a lot at that point, and thanks to his advice we were able to attain the design character I was after, on a budget.
At the start I worked very closely with the QS, before lodging the planning permission application. He did a full bill of quantities and the original costing he brought back was way too high. So we did a redesign based on his costing advice. It took two or three goes to get the design within a budget range I was happy with.
To get there we reduced the house size, removed a lot of the cantilevers I had originally included and reduced the amount of glazing in the extension, especially the corner glass units which are very dear.
The initial costings were just for the shell and core, meaning there were only basic finishes inside (we moved in without a kitchen), no landscaping done, no joinery items. We wanted a certain level of finish on the house and knew we couldn’t afford to do it all in the one go so we did it all over a period of a few years, and now it’s done.
In many ways it’s a more difficult way to go about it but it’s also more fulfilling. Also as this is my home, it’s a great business card for my architectural business to future clients, so they can see what kind of design and finish they can attain.
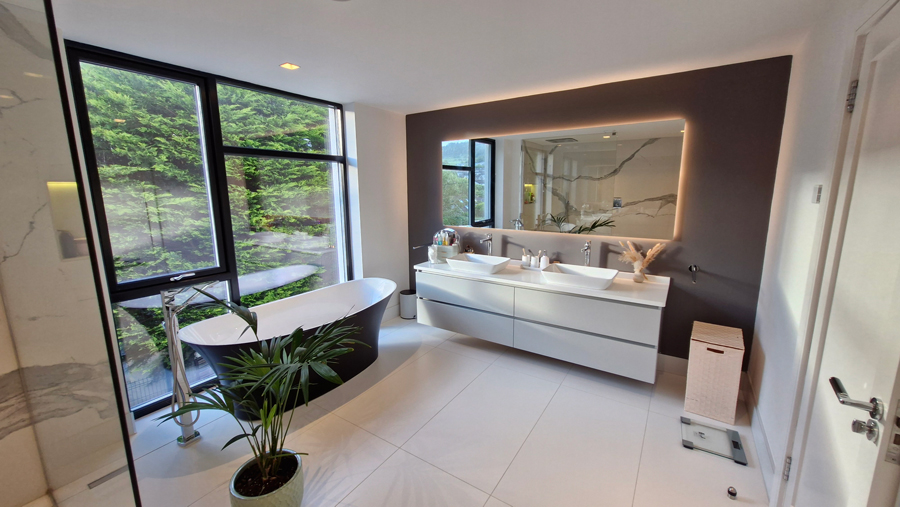
What were the next steps?
Planning went very well. The problem we came across was more to do with the foundations. Because the plot is sandy, we had to engage with a ground investigation company to determine what to do. They drilled holes three metres deep, did impact tests, all so we could get the foundations poured.
The first two metres were too sandy but further down the ground could take the weight for the extension so we filled the whole perimeter with concrete (trench fill) with a lean mix to a certain point then standard concrete foundations to take the walls of house. This swallowed up our contingency, it cost €15k more than what it should have been.
The old house is just sitting on stone on the sand and we left that as is.
Who project managed the build?
I took on the role of the project manager. Because I knew who I wanted to build our house, using the same builder who’d built the mews, I waited a year for them to be free to work on this project.
The main contractor would normally take on the entire build but I took a lot from them. I organised the windows and subcontracted the plumbing, electrician and so forth. They had to tie in with them but I was here every day to keep things running smoothly.
Contractors wouldn’t usually allow this, and I did use most of their subbies, but as I had a working relationship with them, they were happy for me to organise the first fix trades – I just had to make sure it met with their programme of works.
The only issue I came across was with the plasterer, as I hired my own even though the builder had his own. I should have used theirs as mine wasn’t meeting deadlines, and held up the schedule when it came to roofing and putting in the downpipes.
I learned a lot from our previous house, about the nitty gritty, the sequence of works like when the steel has to go in, and how much everything cost. It’s one thing to draw it on the plans but quite another for it to happen on site; the ceiling goes in before the floor, that kind of thing, thinking more like a builder than an architectural designer.
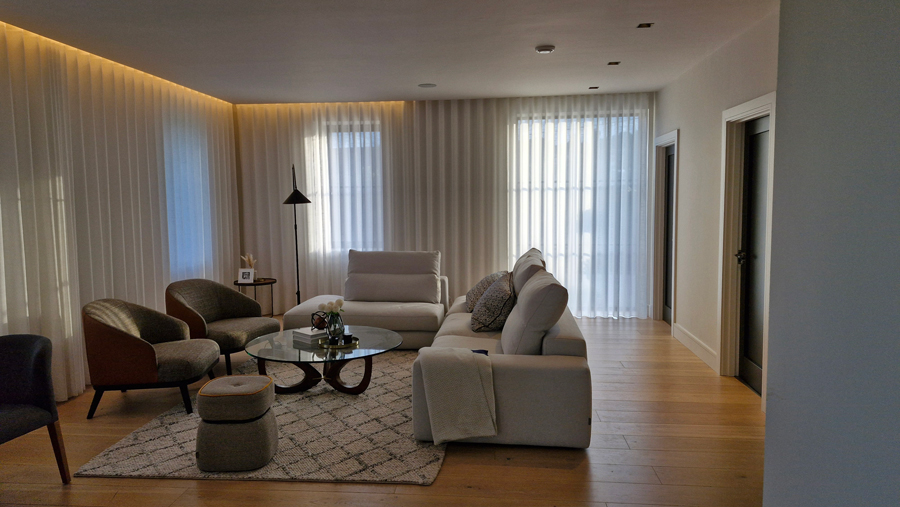
Tell us about the statutory requirements.
I organised everything from a building control point of view, filing the commencement notice. If I were building today I would have opted out of appointing an assigned certifier as that’s the way to go when self-building.
In terms of health and safety we had the inspectors come here, who issued instructions before we could continue on site. We had the scaffolding ticketed, but their concerns had more to do with producing the reports relating to Project Supervisor Design Stage (PSDS) and Construction Stage (PSCS).
Even Revenue showed up to make sure everyone was on the books; I think it’s because our site was so exposed, near the local supermarket, that we got so much attention.
Tell us about the deep retrofit scheme.
We had to achieve a minimum building energy rating (BER) of A3 to get the grant; we got to A2. And with the solar panels we recently installed we’re now A1.
Like the One Stop Shop grant system that’s in place now, the deep retrofit grant paid for half the costs, so €60k in grants, but only on the original house. This included windows, heating system (heat pump with underfloor heating), insulation, ventilation.
It was the pilot scheme and this entailed using a registered energy company to compile the report and the application, and to monitor the build. We had to do external wall insulation on the existing house and could have done it on the extension but the cost was prohibitive so we went with cavity wall insulation there. Overall it was a stressful process, mostly because we were one of the last ones to get in on the pilot scheme. This was the time they cancelled it, and we’d started the works on the basis we’d get the grants. Fortunately, they brought the scheme back in for applications that were in.
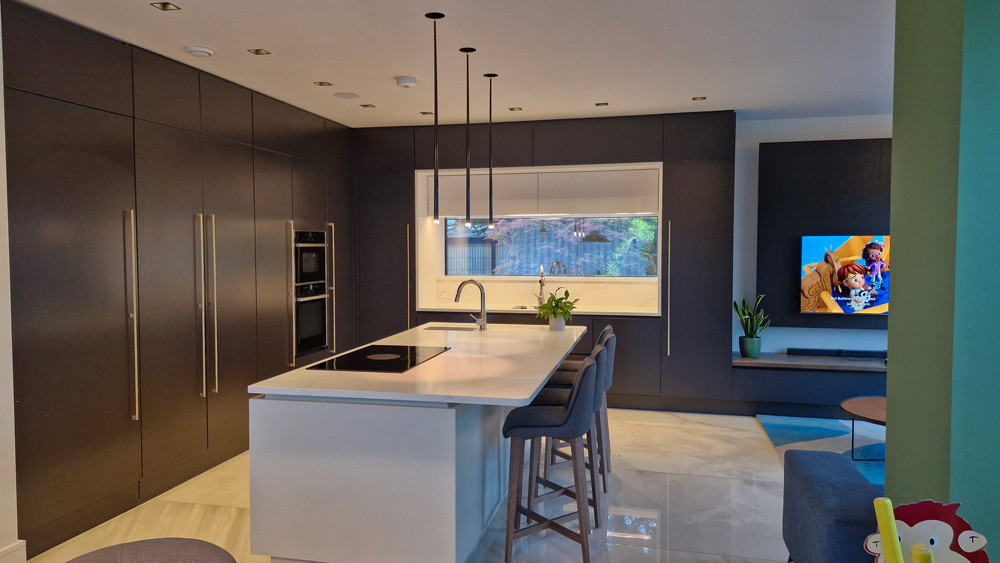
We’d put all the requirements in to obtain the grants, which was costly and wouldn’t have been within budget without the grants. Because they only paid money out at the end, it was stressful enough from a cashflow point of view.
We should have done the solar panels then, as we would have gotten a subsidy, but our budget didn’t stretch at the time. We put in 24 panels with 20kW battery storage since then, and our electricity bills have come down dramatically.
Tell us about the fit out.
Elis had a big input into finishes; I also had my ideas, so instead of us fighting I asked Garry to act as a mediator. Since we moved in, we added a TV unit, floating stairs, renovated the attic with ensuite bedroom, got all the garden landscaped including mature planting, we also put in a walk in wardrobe for the master bedroom, got a headboard, repainted rooms, added furniture.
We also invested in decorative lighting and house furniture, which we got shipped over from two stores in Madrid. We found a shipping company that collects from the store and brings it over by boat – we saved 40 per cent as compared to a high-end store we were looking at in Dublin, taking into account the shipping.
What would you do differently?
The fibreglass flat roof makes noise – when it heats up, it cracks so you get banging from it that’s quite loud. It settles down after a few years. But honestly, I can’t fault it; the design is delivering everything I wanted from the house and I really appreciate it all, especially after the effort that’s been put into it.
Top Tips
Don’t rush. Once you get on site, it all happens very quickly so spend the time to think of how you want everything to be finished. Our interior architect Garry helped a lot with the interiors which has knock on effects on the way you build and configure the house. Getting spaces right for furniture placement is important.
Let the builder take on the superstructure. I’m involved in the trade but it was still a big learning curve taking on subbies; my advice is to let the builder do the whole superstructure, leave it within his remit to hire the subbies. Especially considering you need to get the insulation and airtightness right, and it’s not that straightforward to do. You can take on finishing items like the kitchen, floor finishes, bathrooms. It’s not going to save that much to go direct labour for the main structure of the building; you might even be paying more if you don’t know the sequence of works
Extension Spec
Walls: 150mm full fill cavity (PIR board), outer block 100mm, inner block 215mm
Floor: ground floor 150mm insulation on top of structural slab with 50mm liquid screed containing underfloor heating pipes, concrete precast first floor with underfloor heating pipes with 50mm liquid screed
Roof: timber warm flat roof with 150mm insulation board and fibreglass roof finish
Suppliers
Design
Arc Design, arcdesign.ie
Interior designer
Garry Cohn, cohndesign.com
Structural engineer
Terry Sweeney, gnce.ie
Bathrooms
Villeroy and Boch sanitaryware, idealbathrooms.ie
Air to water heat pump
Veissmann
Ventilation (MVHR)
Brink, greenoakenergy.ie
PV panels
Solar Solutions Ltd