In this article we cover:
- Basic overview of what to check for on site
- When to get the airtightness tests done
- Appointing an airtightness inspector
- Watchpoints specific to timber frame construction
- Watchpoints specific to cavity wall construction
- DIY installation
- How to simplify your airtightness strategy
There is no point specifying the best system on paper if it is not put together right on site. Here are the main touchpoints to be aware of so that the insulation and airtightness system works as intended.
Insulation and airtightness watchpoints
Insulation only works if it is continuous, i.e. there are no gaps in the insulation layer. Insulation that is not correctly installed, with gaps in-between, will never perform to its best. Boards for instance should be held in place by stainless steel wall ties, usually covered by a plastic disc, against the outer face inside of the inner leaf, when batts or boards are being used in a partial cavity wall.
The ties should be kept clean of mortar during construction as this could cause moisture to travel from the outside in. If the insulation is blown in post construction, it should be evenly dispersed throughout the wall cavity with no gaps.
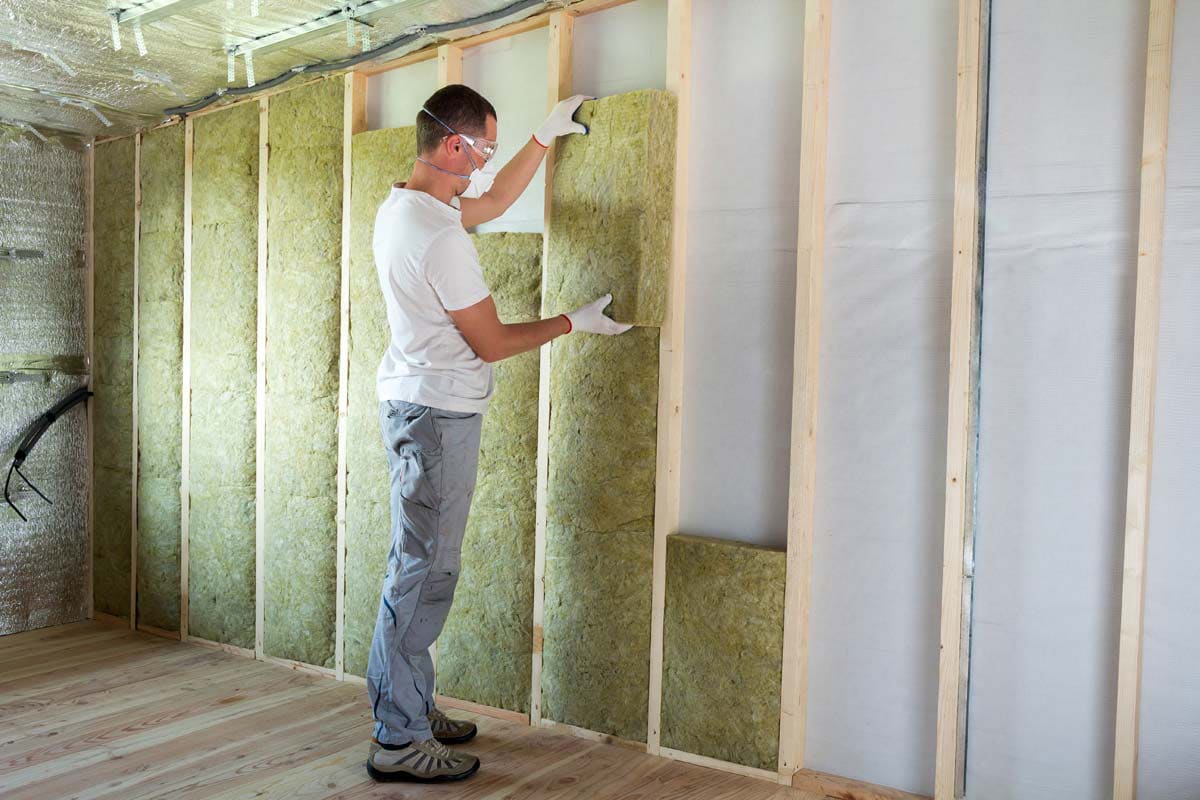
Once the insulation is in place and installed correctly, new builds will add an airtightness membrane. Airtightness is an air leakage and at times, a vapour control measure; weak points are usually found at openings, e.g. around windows. Where such a vapour barrier or vapour check is used, this should always be to the warm side of the insulation to prevent condensation.
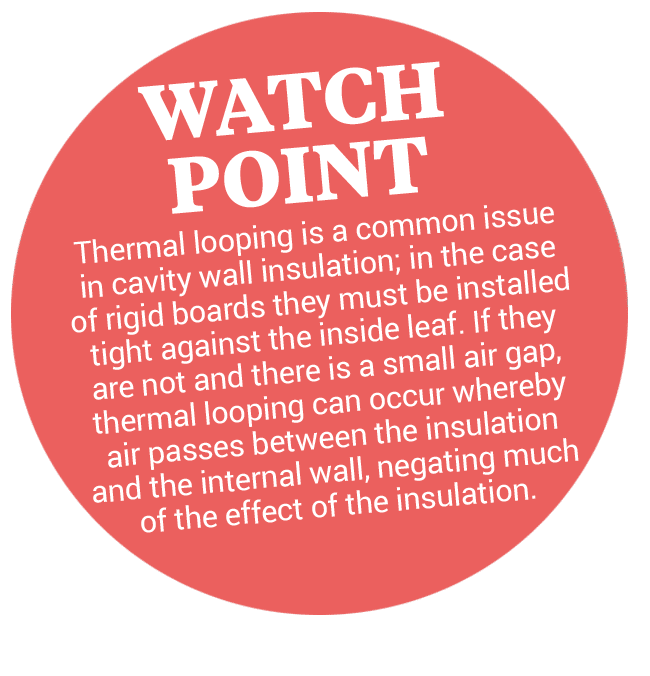
Examination of areas that may give rise to air leakage should be carried out continuously during the build and thus avoid any gaps or holes being covered up, or service penetrations being added without careful sealing. Pre-test devices (smaller fans which can be inserted in windows) are available to builders – these are less accurate but provide a very good indication of leakage points.
When the dwelling is completed, a further and final air tightness test must be carried out for the building regulations requirement (ROI) and in NI unless the default value was used in the design SAP assessment. In ROI you must follow Part L’s Acceptable Construction Details.
Airtightness inspector
Your ‘airtightness strategy’ will need to be conducted very early on in the process and take into consideration moisture management. It is essential that all members of the construction team understand the process involved in maintaining airtightness; it’s very easy for an electrician, for example, to cut an opening in the airtightness membrane for a cable without then resealing it. It is therefore highly recommended that your builder ensures that every subcontractor on site understands the process. And, if you are a self-builder, it is up to you to ensure that your subcontractors seal any penetrations as they go, otherwise the end result is likely to be poor and require remedial works to pass the regulatory standards currently applicable.
The challenge during the construction phase is to ensure all operatives on site adhere to almost military style discipline needed to locate, install and protect the airtight barrier through all phases of construction. Sequencing the works through the various stages from foundations, floors, walls, roof, windows, doors, fixtures and finishes must prioritise sealing and protecting this airtight barrier.
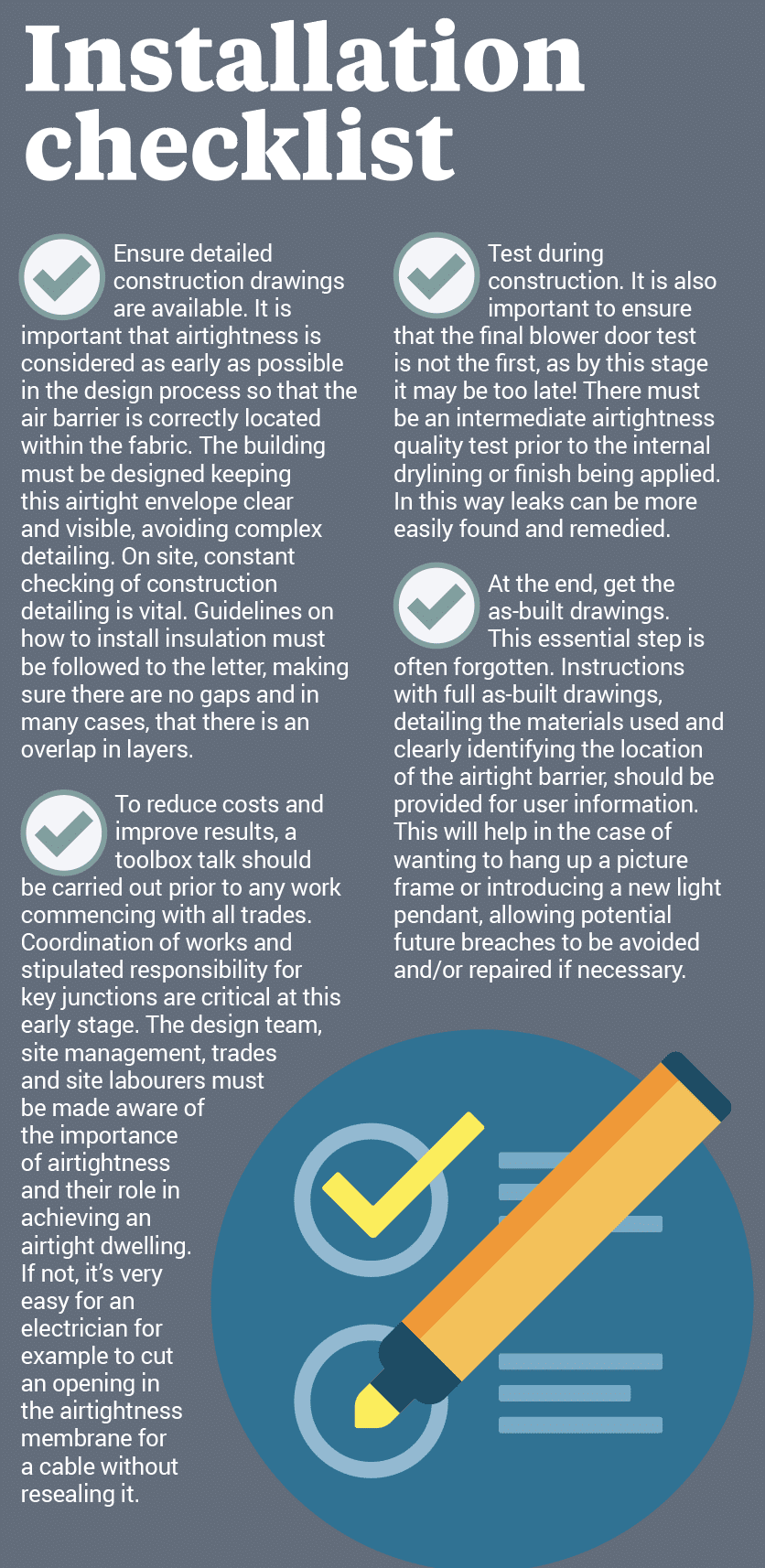
Timber frame construction
In the case of timber frame construction, you will have to fix an airtight membrane internally on the entire envelope. Alternatively, a certified airtight structural board may be applied internally.
It is important to ensure a dew point assessment (condensation risk analysis) is conducted to ensure the correct materials are used within the timber frame wall. As a rule of thumb, the external layer of a timber frame wall should be at least six times less vapour resistant compared to the internal airtightness and vapour control layer, but a dew point assessment as a rule should be conducted for reassurance.
Cavity wall construction
In standard plastered blockwork, cavity walls are typically considered to be airtight as long as they are plastered externally and internally with a minimum of two coats (scratch and finish). Potential air leakages occur where the walls are penetrated (with doors and windows for example) and adequate airtight sealing has not been considered at these junctions.
Also, it is now common practice to insulate walls internally (dryline) with insulated plasterboard (normally a 50mm board with 38mm insulation and 12.5mm plasterboard) but this may not necessarily be airtight as the junctions between the boards may not be sealed adequately: a skim coat does not provide an airtight barrier, nor does plasterboard tape!
The solution therefore is to scratch coat the blockwork walls first and then fix the insulated plasterboard. You will still need to pay particular care at window and door reveals to ensure the airtight barrier is maintained by applying an airtight seal or using proprietary tapes. The main thing to remember is that your structure is not airtight at junctions where you are only relying on the thickness of the finishing coat of plaster.
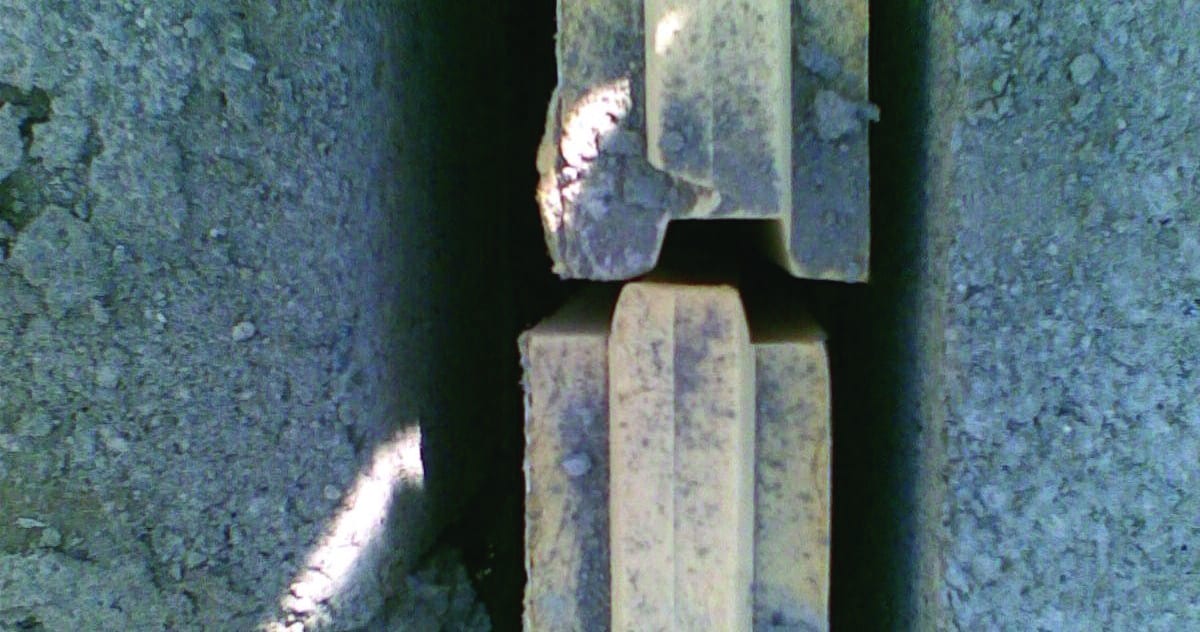
An alternative to wet plastering the inside of cavity walls which is gaining prominence is the use of certified airtight paints. Provided they are fitted correctly, these can be more efficient and cleaner to install.
An alternative method for applying an airtight barrier to a cavity blockwork construction is to apply a similar technique to a timber frame wall, that is, to batten the un-plastered internal blockwork wall and then to apply the airtight membrane to the battens. As well as creating an airtight envelope you are also creating a cavity for any services such as electrics or plumbing, thereby eliminating any chasing, though pay close attention to the points where the services penetrate the membrane and use the proprietary tape to seal up the gaps. The final stage then is to plasterboard and skim.
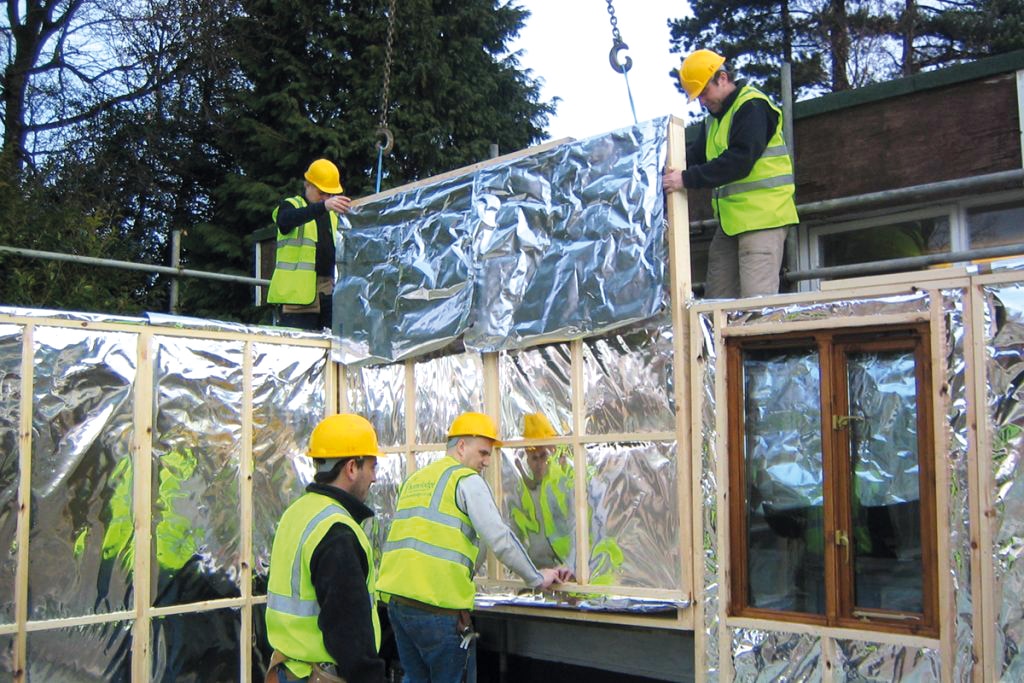
DIY installation
You can attend a specialist airtightness course provided by the suppliers of the airtight membranes; if you are a self-builder that intends to get their hands dirty then consider attending one of the ‘contractor’ courses which will teach you every detail of applying the membranes, tapes and seals.
The same goes for insulation products; technical academies tend to be open to self-builders and will often include a review of the benefits and precepts of nearly zero energy buildings. There are also training courses open to self-builders from Education Training boards in ROI such as the WWETB.
EXPERT TIPS by Niall Crosson, Ecological Building Systems
How can I simplify my airtightness strategy?
Firstly, I would recommend moving as many services off the external walls as possible and bring them up through foundations or internal walls and use appropriate sealing solutions.
Where services do penetrate external walls, employ suitable grommets as opposed to tapes. Airtight grommets are available in a range of dimensions. Compared to a taped solution, grommets offer greater flexibility in that cables and pipes can be easily adjusted after the installation whereas this is not the case with tapes.
The biggest expense with airtightness is time, and any solution which may appear to cost more materially, but saves time, should be strongly considered.
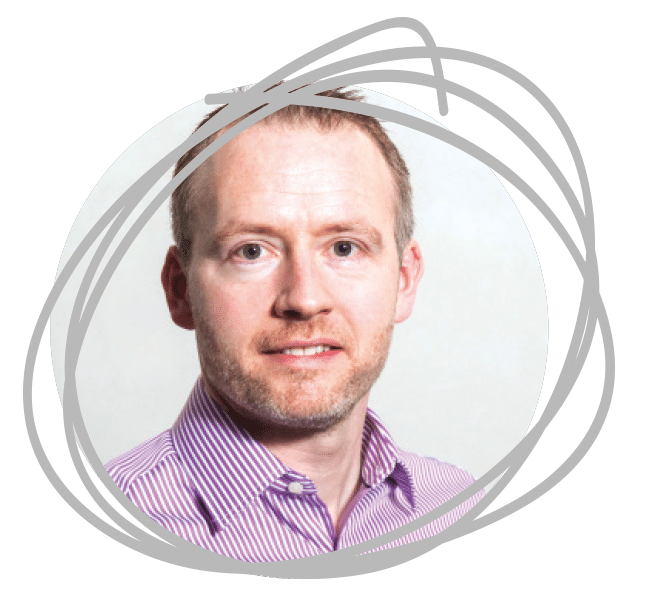
What are the common pitfalls when relying on plaster for airtightness?
When applied correctly, wet plaster directly on block is a reliable airtight layer, but on occasion some areas that are not exposed, can inadvertently be left unplastered.
A case in point is the area between a precast concrete slab and suspended ceiling. This area around the perimeter of a building can be substantial and if left unplastered, can lead to significant air leakage. Another classic example is an unplastered drylined chimney breast. Airtightness will always find the weakest link, so it is critical to address all seen, and unseen areas.