In this article we cover:
- What is standard concrete?
- What is self compacting concrete?
- What is reconstitute stone?
- What is low carbon concrete and how eco friendly is it?
- What is carbon neutral cement?
- What is limecrete and how to use it?
- What is hempcrete or hemp-lime and how to use it?
- Other concrete types, from aerated to autoclaved
- Bonus: Take our flooring quiz
Specifying the concrete you’re going to be using can be a complex task, with five main methods for compiling the specifications. These are known as designated, designed, prescribed, standardised and proprietary. Every project has different requirements, so the decision on which method to use and how to use it is best left to your designer or structural engineer.
Standard concrete
Standard or regular concrete is what’s commonly used for modern domestic floors. It’s made of cement, aggregates (sand and stone) and water. Admixtures can be added to enhance the concrete. When mixed together, the aggregates and water interact with the cement in a reaction called hydration.
The combined materials gradually harden and grow stronger over time. It usually takes 28 days to reach its target strength. Typical simple unreinforced concrete mix ratios of cement-sand-aggregate by volume are 1:3:6 or 1:2:4, Gen 1 and Gen 3 mix respectively. Gen 1 could be used for foundations on a good load bearing subsoil stratum or for kerb-laying and Gen 3 could be used both for foundations and subfloors.
A higher ratio of cement content results in stronger concrete, so of these two mix ratios, the second one is strongest. Mixing concrete on site is not often seen nowadays, but in those cases where it is preferable, the quality depends on being consistent with the mix ratios, water content and admixture dosage for each batch. For speed and batch volumes, most building contractors use ready mixed concrete.
Water and admixture content affects workability and a factor known as the slump class, which is simply a measure of the distance a sample of fresh concrete slumps over a given period of time. Be aware that too much water results in weaker concrete so there will be a trade off between slump (workability) and performance.
Chemical admixtures are commonly used to extend the duration of the workability, reduce water content, enhance durability, provide a measure of protection against freeze-thaw cycles and to protect against corrosion of reinforcement.
They can also be used to retard or accelerate the setting time, improve flowability, enhance the strength and help to control crack propagation by reducing shrinkage. Note that the mix examples given above are just two out of many possible mix specifications which can be used.
Gen 1 concrete is roughly equal to C10 and will have a strength of 10N/sqmm and Gen 3 is similar to C20 with a strength of 20N/sqmm. As a general rule, reinforced concrete should have at least a minimum strength of 30N/sqmm. Concrete strengths are generally expressed as their compressive strength.
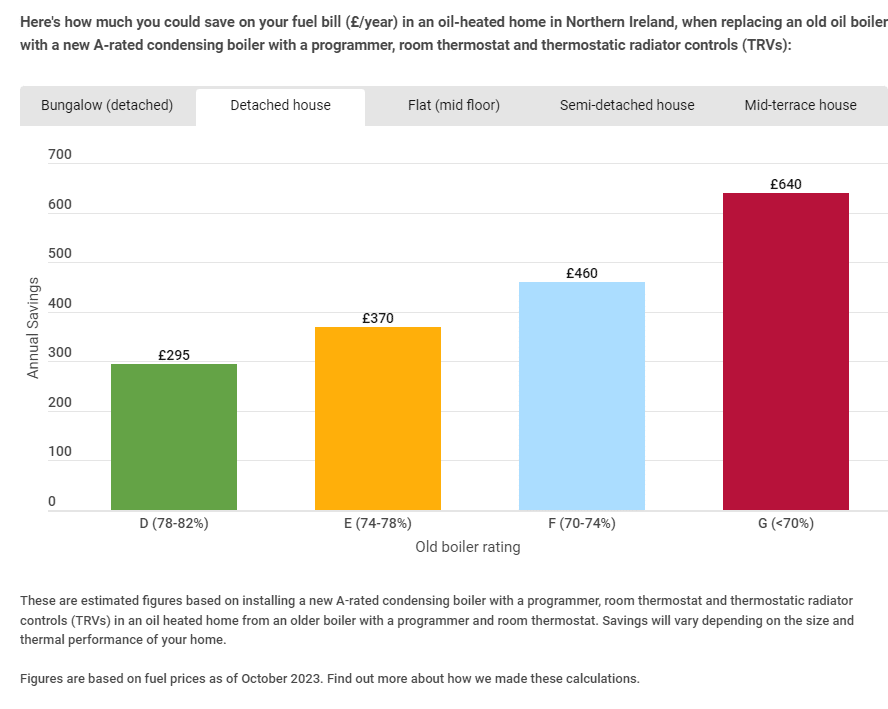
Self compacting concrete
Self compacting or self consolidating concrete (SCC) was developed in Japan in the 1980s as a solution to the need for a fast flowing concrete. It can be pumped and flowed into formwork without the need for mechanical compaction. It uses superplasticisers and stabilisers to enhance its flow characteristics and should not be vibrated or otherwise compacted.
It usually is supplied with a strength of around 40-50 N/ sqmm and should be specified in terms of its flow rate. SCC offers a fast method of laying floors, especially around potential obstructions such as reinforcement, pipework and service ducts.
It is possible to use it as a single floor layer with the floor finishes directly on top instead of the usual combination of subfloor and screed. For this floor solution, the cost and time savings could be significant, but you need to be absolutely sure that the design and preliminary site works procedures have accounted for the positions of all of the service penetrations beforehand.
Reconstituted or composite stone
A spin-off concrete product which is made to look like stone, but being around in one form or another for centuries, has no standardised formula for its manufacture. This method of manufacturing artificial’ stone is nowadays used for a wide range of attractive construction components, for example in both interior and exterior walls and floors.
Low carbon concrete
Whilst there is no question that we need concrete in some form or another, the big question now is how to make it a greener product. Portland cement is responsible for the continued success of regular concrete, but it also accounts for most of its carbon emissions.
Cutting the emissions in its production is feasible through the use of green energy sources, whilst lower carbon content can be achieved by the increased use of supplementary cementitious materials (SCMs) and other recently developed products.
Geopolymer concrete describes a group of alternative solutions to ordinary Portland cement-based concrete and is made by adding regular aggregates to a geopolymer cement slurry.
This type of cement is made from inorganic aluminosilicate polymer compounds that makes use of recycled industrial waste such as fly ash or ground granulated blast furnace slag (GGBS), resulting in lower carbon dioxide emissions.
The concrete also has the added advantages of possessing greater thermal and chemical resistance and better mechanical properties. It is claimed that specifying pulverised fly ash (PFA) also known as fly ash or ground granulated blast furnace slag (GGBS) can reduce the embodied CO2 of a reinforced concrete flat slab by 35 per cent.
It is also generally understood that the use of GGBS (as a partial cement replacement) results in a denser cement which increases the conductivity of the concrete. This may be bad for its thermal insulation properties but is good for its thermal mass properties of absorbing, storing and releasing heat. Both PFA and GGBS need to be used in conjunction with a certain amount of Portland cement.
Silica Fume (SF) is a byproduct of the manufacture of silicon and can be used as a dense powder or slurry in concrete production. Due to cost, it is generally only used in concrete where resistance to harsh environmental conditions are expected, or where high strength is required. The silica fume content of such concrete is usually about 10 per cent by mass of the total cement content.
Limestone fines are created simply by grinding limestone, which is a much less energy intensive process than producing Portland cement. The fines can be added to ordinary Portland cement to create Portland limestone cement and in the UK its content by mass is currently 6 to 10 per cent of the total cement content.
It is expected that updates to the British Standards for concrete in 2023 will cover some 112 general purpose cements, including those with greater ratios of more sustainable components. The update is set to include ternary cement blends of up to 20 per cent limestone fines in addition to GGBS or PFA. These ternary blends should become the default over time, which is already the case in Ireland where they have been allowed for some years and ‘limestone cement’ has become the norm.
Carbon neutral cement
As coal power stations are phased out in the future, PFA will gradually become unavailable and GGBS is already fully utilised, so supply of that is now limited. This means that current research projects are trying to find alternatives to the alternatives already used in geopolymer concrete.

A company called Seratech in the UK has won the prestigious 2022 Obel Award for its work on producing a prototype carbon neutral concrete which replaces part of the cement content with a type of silica created from the capture of carbon dioxide from factory flues. As industrial emissions reduce over time, the long term plan is to draw the carbon directly from the atmosphere.
Elsewhere, other experimental work includes an innovative concrete produced at the University of Colorado Boulder, which uses limestone grown by microalgae to entirely replace the cement content.
The concrete made from this biogenic limestone is net carbon neutral. It can even be made carbon negative if the additional ground limestone which is typically added to the cement mix as a filler material, is also replaced by the algae grown product.
To produce enough raw material to make all of the cement needed by the USA, the total area of algae ponds required is estimated to be roughly equivalent to just 1 per cent of the area that the country currently uses to grow corn. To keep concrete prices low, researchers suggest using the same algae to make other products such as biofuels, food and cosmetics.
Limecrete
Limecrete is a combination of natural hydraulic lime and lightweight aggregate such as sharp sand or glass fibres. The result is a vapour permeable material that can be used as an alternative to regular Concrete, in particular for floor slabs in the conversion of old buildings, where it helps to deal with naturally occurring moisture.
It can be laid on a base of foamed glass beads rather than hardcore and without a damp proof embrane (DPM). This enhances the vapour permeability of the slab. Limecrete is relatively slow to set and absorbs CO2 during the drying process. And although more flexible than concrete, it is strong enough under compression to serve as a floor slab material. It can be strengthened by adding fibres and increasing the lime content, although this requires expert knowledge and experience.
Hempcrete (or hemp-lime)
Hempcrete is a mix of chopped hemp shives and a binder composed of natural hydraulic lime and a small amount of cement. Typically used as insulating timber frame infill, it can also be used for floor slabs when combined with aggregates. Hempcrete is carbon negative and vapour permeable and contributes to regulating the temperature and humidity of a building. It can also help to reduce or eliminate the need for heating and cooling systems. Being vapour permeable, hempcrete is ideal for use both in historic buildings and in modern buildings using natural materials.
Other types
No-fines or pervious concrete contains less or zero fine particles (e.g. sand), so is a mix of cement, aggregate and water. Containing between 15-25 per cent voids, it is usually used as a solution for dispersing surface water.
Lightweight, aerated, cellular or foam concrete is a concrete produced by the addition of an air-entraining component to the mix. This can be in the form of a foam which introduces air bubbles. Alternatively a product such as lightweight expanded clay aggregate, waste cork granules, vermiculite or perlite can be used.
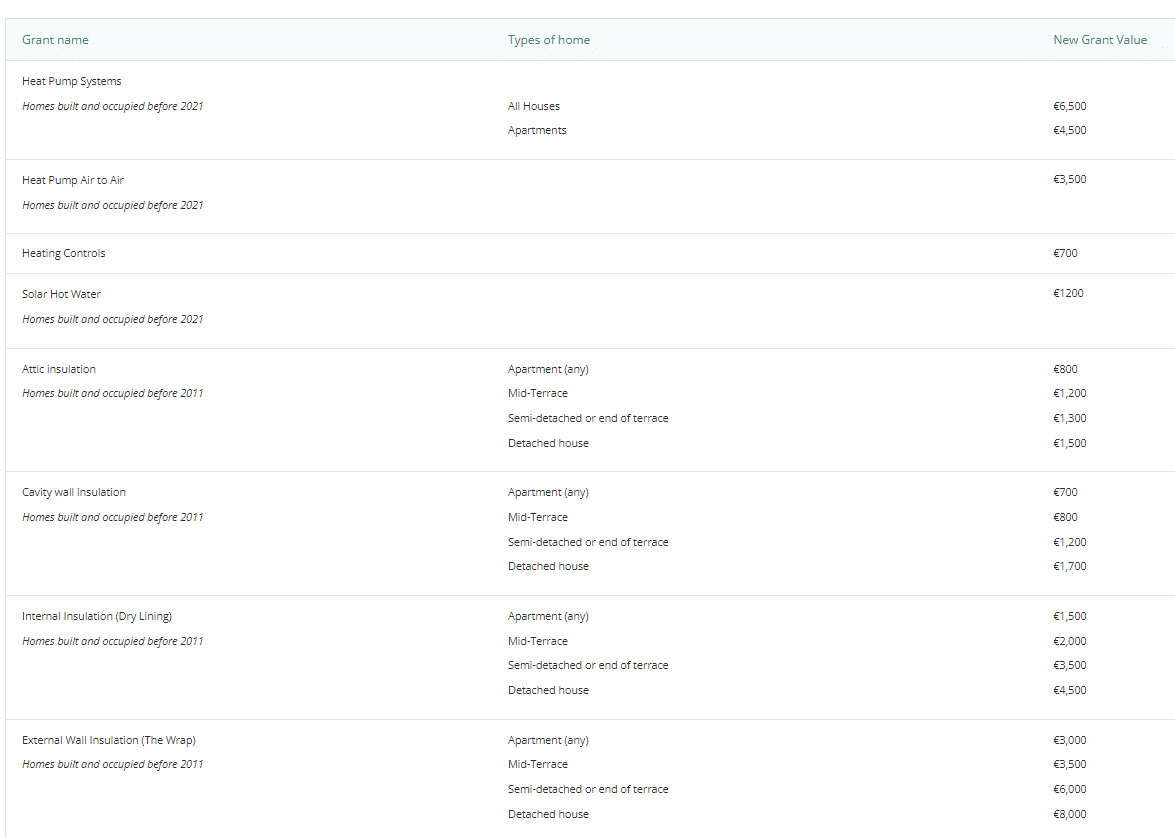
The main idea is to replace concrete mass with small air pockets to enhance its thermal and/or acoustic insulation performance, albeit at the expense of strength. The weight by volume of lightweight concrete can be as little as an eighth of that of regular concrete, so at such low density it would no longer be suitable for use in a structural element but would act more as a filler or insulation layer.
The term aerated concrete should not be confused with aerated autoclaved concrete (AAC) or Eeinforced aerated autoclaved concrete (RAAC), which is an entirely different product. Some precast RAAC panels used in the UK for roof, wall and floor construction from the mid 1950s until the mid 1980s have been subject to sudden failures. Their potential for failure risk is now categorised depending on when and how they were manufactured.
Other concretes not usually found in use for domestic construction projects include High Strength Concrete (HSC) with a minimum strength class of C50/60 and High Performance Concrete (HPC) which conforms to standards above those required for the usual purposes.
Not all high-performance concrete is high-strength but high-strength concrete is a high performance concrete. There is also Ultra High Performance Concrete (UHPC) and Micro Reinforced UHPC, neither of which are ever likely to be needed in normal house building. Likewise, Shotcrete and Vacuum Concrete are also available but are more suited to industrial or infrastructure projects.
Quiz
Which region invented concrete over 9,000 years ago?
1. Middle east region of Syria and Jordan
2. Italy
3. Sub-Saharan Africa
4. Ireland
1. Concrete is a very old material, the true origin of which is still debated today, but it is believed to have been developed somewhere around the Middle East region of Syria and Jordan.
Of course, much depends on what you think is meant by the term concrete. Contrary to popular belief, it was not invented by the ancient Romans, although they were first to use it in much the same way that we see it being made today.
Their most successful versions used a mix of harena fossicia (a naturally reactive volcanic sand) or pozzolana (volcanic ash), mixed with lime, water and various aggregates. Portland cement which forms the basic binding component of all modern concrete, did not come along until 1824.
In Britain, Ireland and other parts of northern Europe, an early version of concrete which can still be found in some old rubble stone walls was made from sand and lime, or lime and clay, or sometimes all three. This might be better described as mortar, but in any case was inferior to the old Roman concrete.
What material was used as an early damp proof membrane?
1. Pig’s bladders
2. Wood
3. Horse hair
4. Ashes
4. Most houses at the end of the Victorian period were built with suspended timber
ground floors. Before this, houses had ground floors built with stone or clay flags laid on a bed of ashes or directly onto compacted earth. Slate was also used as a natural damp proof membrane.
Which geographical location would you be able to cover (to a depth of 450mm) with all the concrete that’s produced in the world today?
1, Australia and New Zealand
2. Northern Ireland
3. Republic of Ireland
4. Greenland
Globally, we are now producing around 14 billion tonnes of concrete annually. That is
equivalent to laying around an 18” deep layer of concrete over the entire surface area of Northern Ireland every year.
Which rating scale would you use to compare the hardness of different wood species used for timber flooring?
1. The Chromatic Scale
2. The Mohs Scale
3. The Janka Scale
4. The Butcher’s Scale
3. The Janka hardness rating scale is created by using the Janka Hardness Test to measure any type of wood’s ability to resist dents and scratches. The test is named after Gabriel Janka, an Austrian wood researcher who developed a system for testing wood hardness by measuring the amount of force required to press a small steel ball into the wood to a certain depth. The scale number can typically be expressed in either N (Newtons) or lbf (pound force), so it is important to know which units the timber supplier means if they just give a number.