How this Scandi design new build in Co Meath was built by an architect and quantity surveyor couple.
In this article we cover:
- How this architect and quantity surveyor couple tackled the design process of their home
- How much they overspent by
- Modern farmhouse design tips
- Scandi (Scandinavian) design and finishes
- Achieving an A1 energy rating
- Choice of traditional build method
- Reasons for systems choices
- Planning process and going to tender
- Choosing a main contractor
- Troubleshooting on site
- Getting help from family and friends
- Timeline and specification
- Floor plans
- Professional photographs
After having lived in Texas for five years, Sinéad and Brian moved back home. “Our eldest was born in the USA and when we returned to Ireland in 2019, I was six months pregnant with our second child.”
“We were very fortunate that we had a site to build on,” says Sinéad. “My parents gifted it to us, it’s next door to my aunt and uncle. My brother who is a dairy farmer lives down the road with his family, beside my parents. We are surrounded by family.”
Site size: 0.6 acres
House size: 220 sqm
Bedrooms: 4
BER: A1 (5.53 kWh/sqm/yr)
Airtightness: 1.83m3/(hsqm) at 50 Pa
Heating and hot water: air to water heat pump
Ventilation: centralised mechanical with heat recovery
Build method: masonry (cavity wall)
They were also lucky to be able to draw on their own expertise. After all, the bill of quantities that Brian created at the tender stage was within €5,000 of the actual build cost. It’s no small feat considering the year was 2020, when Covid affected schedules and prices.
In this sense too, help from family helped a lot to keep things moving and on budget. “My dad and uncle were available during the build to help with deliveries, which was a huge help,” says Sinéad. “We also had family involvement in the form of our kitchen and utility fit out. Both were manufactured and installed by my husband’s cousin Niall, who is a carpenter.”
Scandi design
Sinéad was delighted to get to design her own house while on maternity leave. “As an architect, I always wanted to design and build my own home, and thankfully my husband and I were on the same page as to what we wanted from it. He’s also from a farming family, his is from Co Carlow, which means we both enjoy the unrestricted views over the fields. And occasional cow neighbours.”
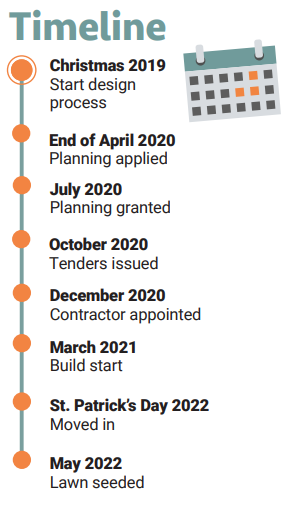
She refers to her home as a modern farmhouse, a traditional shape with modern finishes. “I love Scandinavian style interiors with clean lines, light wood functional furnishings, lots of plants and a neutral palette so my first design consideration was orientating the house to achieve maximum natural light to the living spaces.”
This meant plenty of windows, which is a design feature that comes with the risk of overheating. That’s something Sinéad considered from the start. “All windows on the north façade of the house are fixed panes. During hot weather the electric roof lights in the vaulted ceilings can be opened to act as chimneys for the hot air.”
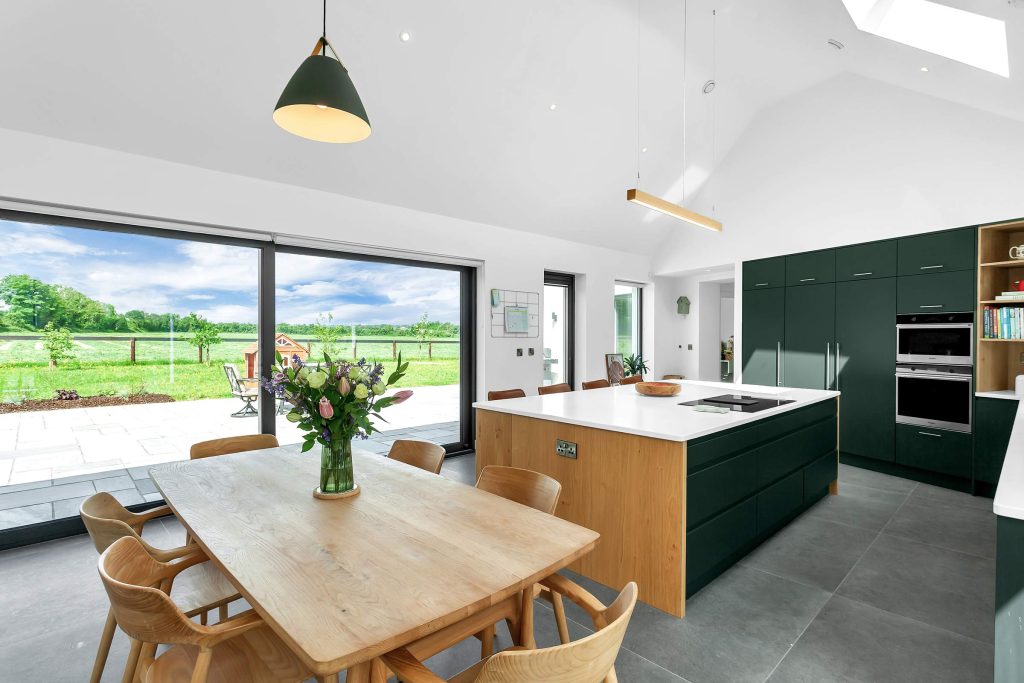
“Externally, I prefer the look of flush eaves so we don’t have fascia and soffits, and have metal gutters and downpipes. Our main roof is a fibre cement slate and the rear extension is finished in an aluminium standing seam roof. The entrance canopy at the front door is clad with matching aluminium and composite timber cladding.”
“With the Scandinavian theme, we decided early on that we would spray paint the entire house white and gradually introduce colour to rooms using furniture, textiles and artwork. At this stage we also knew we’d use laminate throughout the ground and first floors and up the stairs in a light oak colour. We tiled the floors in the kitchen, utility and bathrooms.”
The couple achieved an A1 building energy rating (BER) thanks to high levels of insulation, triple glazed windows and doors, as well as renewable energy via heat pump and solar panels.
“For the build method, we went with a traditional masonry cavity wall construction, with bonded EPS beads pumped to fill the cavity with insulation, as we were both familiar with traditional construction,” says Sinéad. “We did research non traditional methods such as metal and timber frame during the design process but in the end we went with what we were comfortable building.”
“For the first floor slabs and stairs, we chose precast concrete for two reasons – sound and time. We had previously rented a house with timber floor joists and the sound would travel from room to room, floor to floor, we don’t have that problem in the new house. Also our hollowcore floors and precast stairs were craned in and finished in one day – it would take a lot longer to build timber floors and stairs.”
“We visited the Selfbuild Extend & Renovate Live show in Citywest in September 2019 which gave us a good idea of suppliers for certain elements we wanted to include.” For space heating and hot water they chose an air to water heat pump (with underfloor heating as the heat emitter), and for ventilation they opted for a mechanical ventilation and heat recovery (MVHR) system.

“We chose a heat pump as it provides a constant temperature in our home,” says Sinéad. “All our thermostats are set to 18 degrees and we have never felt cold since we moved in due to the high levels of insulation and airtightness.”
“We chose MVHR to ensure the air quality throughout the house was maintained as the system works by continuously extracting the stale air and replacing it with fresh filtered air. We have a downdraft recirculating hob in our open plan kitchen as we didn’t want to penetrate the external envelope with
an extract vent, so the MVHR also helps eliminate cooking smells.”
“We have a stove but had to find a sealed low kilowatt output stove in order to maintain our A1 BER rating (we had it shipped from The Netherlands) and had to add 4.6kW of solar panels to the roof to balance out the carbon emissions,” adds Sinéad. “We now have an electric car and during the summer, we charge it directly from the solar panels.”
Their wastewater system is a concrete sewage treatment plant with a raised bed percolation area which was included in the contract with the main contractor to install. “We are on mains water, which runs past the gate to our house so connection was quite easy for that, and we were lucky to have a connection in place for most of the build,” adds Sinéad.
“As for planning, it was really straightforward with Meath County Council as we qualified for a local housing need as returning emigrants.” Once planning was secured, it was time for Sinéad to draw up the construction drawings and put together the tender package.
At this stage Brian drew up a bill of quantities, which is a costed breakdown of the elements that go into building a house. “That meant we had a really good idea of actual costs involved,” says Sinéad.
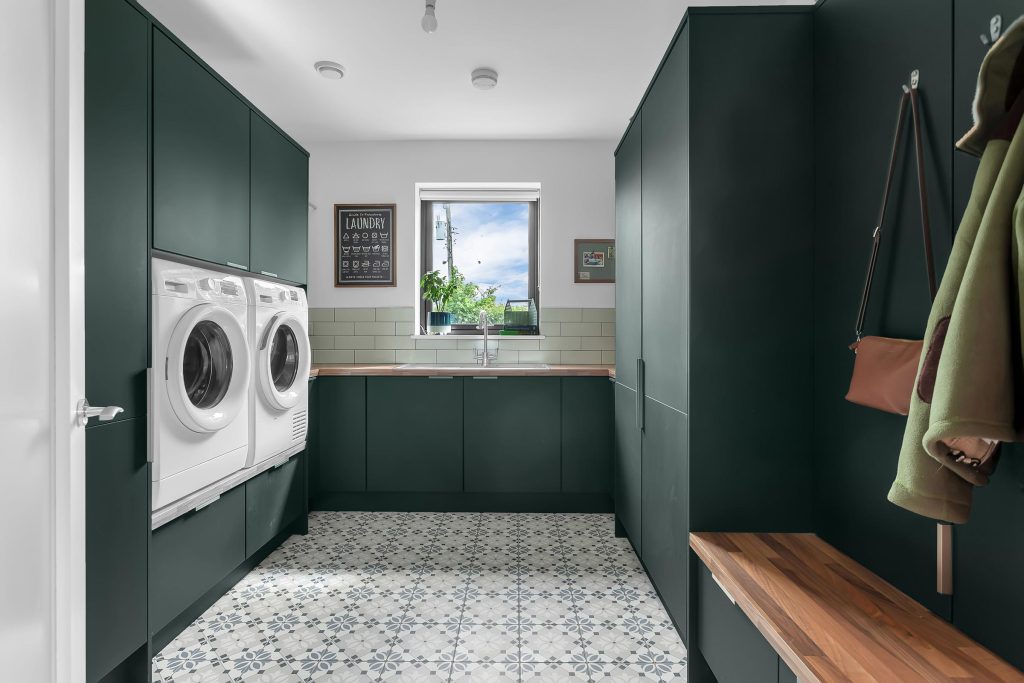
Turnkey build
“We sent out tender drawings to five or six local contractors in Co Meath and interviewed the two contractors who returned the lowest tender prices, before visiting projects that they had both recently finished,” says Sinéad.
“Both contractors’ work was of a very high standard so it came down to the contractor with the lowest price. The reason we went with a main contractor, for a turnkey construction service, is that we both were working full time.”
The contractor’s site manager David was on site most of the time. “He was very enthusiastic and had a positive attitude which we liked,” recalls Sinéad.
But that doesn’t mean they weren’t hands on. “Even though it was a full turnkey construction service, I took on the role of procuring the items which were included as provisional sums in the contract.” This included window suppliers, sanitaryware, tiles, kitchen and utility cabinets, appliances, light fixtures and flooring.
They were also on hand to answer any questions or troubleshoot. “We were renting a house less than a kilometre from site for the duration of the build, so if the site manager needed questions answered or decisions made it was easy enough to drop down to site before or after work, or on our lunchbreak as both my husband and I were working from home at the time.”
That’s not to say there weren’t any setbacks. “I wanted a feature lighting piece over the stairs and vaulted hallway and we also went for a vaulted ceiling in our kitchen so sourcing light fittings when you have a four metre plus drop was a challenge,” she says. “We got drop cords made specifically for the ceiling height over our stairs. They took five months to arrive but were worth it.”
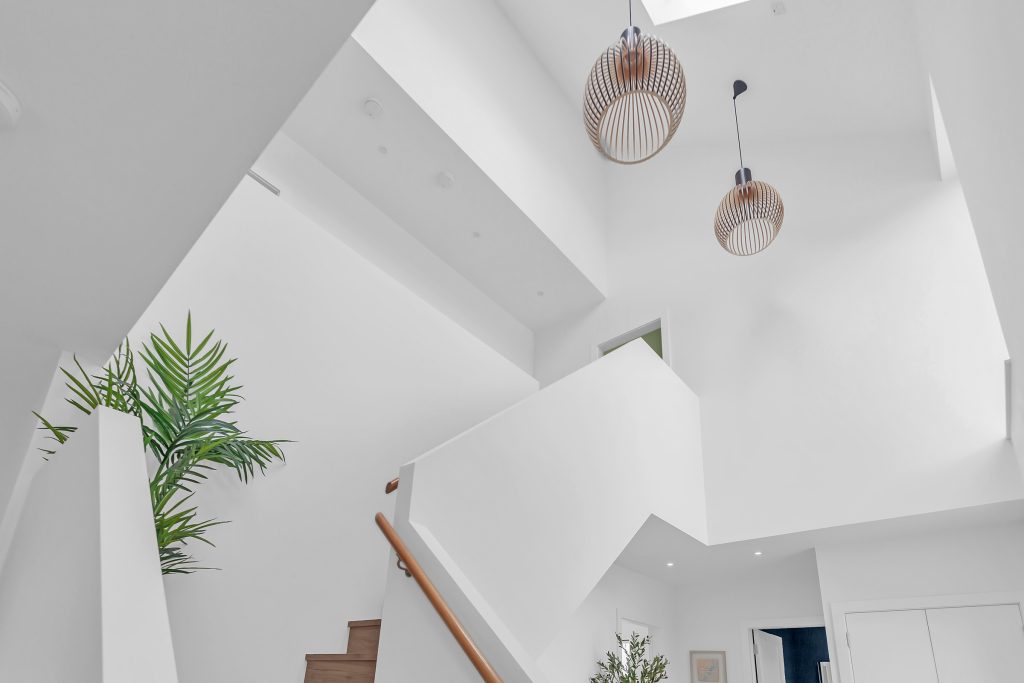
Then of course, Covid hit. “We were initially due to start construction in January 2021 but sites were shut down across the country. We were delayed starting by about three months and then encountered further delays due to Brexit, shortage of materials and the Suez Canal.”
Thankfully, the contractor still managed to complete the entire build within his 12 month timeframe. “I think we might have saved time on the build because a lot of the big decisions were made before we got to site and we made very little changes during the construction,” she says.
What about the garden? “We had our patio laid as part of the site works as the back door is our level access entrance to the house. We levelled and seeded the lawns and planted fruit and ornamental trees, which were presents from family and friends. We would like to do more work on the gardens in the coming years.”
As for the house, it’s working like a dream. “The house is great, we love it. We have a layout that is designed to work for us as a family.”
Q&A with Sinéad
Favourite features?
I love the open airy feeling of the high ceilings, large windows and the connection to outside provided by the views of the surrounding countryside.
What would you change?
One thing we would probably change is that because of hybrid working from home, we both now need an office in the house. As the house was designed before Covid this wasn’t a consideration at the time.
Biggest splurge?
Our double sided stove was probably our biggest splurge as it is only used for about three months of the year. I wanted a real wood burning stove, and although the house is generally warm throughout the winter, the stove has come in handy when we’ve had power cuts due to storms.
Top tip
Spend time on the design.
Try to make as many decisions as you can at planning stage – take your kitchen plans to a designer and that will then help with placement of sink, cooker, fridge, sockets, etc. in the kitchen when you are doing first fix. Mark out the floorplans on the site and this will let you move windows to frame any special views you want.
Spec
Floor: 75mm screed with underfloor heating pipes on polythene separating layer on 130mm rigid PIR board with 30mm edge of slab insulation board on 150mm concrete slab on damp proof membrane, on standard build up, U-value 0.12 W/sqmK
Walls: 370mm cavity wall construction with 20mm render, 100mm external concrete block, 170mm full fill cavity bonded bead insulation 0.035W/mK, 100mm internal concrete block inner leaf, 20mm parge coat (airtightness level of 3 maximum) plaster finish, U-value 0.16 W/sqmK Slated roof: slate on treated battens, breathable membrane, 50 mm ventilated cavity, 150mm phenolic insulation between rafters with 62.5mm insulated (phenolic board) plasterboard and airtight self-adhesive sealing tape at junctions with blockwork, U-value 0.16 W/sqmK
Metal roof: standing seam metal roof on 18mm WBP marine plywood decking with rafters fitted with 38mmx38mm treated sw battens on membrane on 44mm x 175mm rafters with 50mm ventilated cavity. 150mm phenolic insulation between rafters with 62.5mm insulated (phenolic board) plasterboard beneath and airtight self-adhesive sealing tape at junctions with blockwork, U-value of 0.16 W/sqmK Attic insulation: 100mm fibre insulation laid between trusses with two layers of 150mm laid over. Pitched roof insulated on rafter, U-value 0.16 W/sqmK
Windows: triple glazed, argon filled, U-value 0.8 W/sqmK