In this article we cover:
- Design process and what the homeowner’s must haves were
- How to build on a budget and which decisions saved the most
- Build costs and timeline
- Choices for systems, insulation and ventilation
- Planning restrictions
- Demolition work and site clearance
- Full supplier list and specification
- Floor plans
- Photographs of the exterior and interiors
When you’re self-building, getting the design right is more than half the battle. And for William Richmond, the obvious place to start was what he’d be looking at every day.
House size: 160sqm
Plot size: 0.82 acres
Bedrooms: 3
Construction: blockwork (cavity wall)
Heating: oil boiler
Ventilation: mechanical with heat recovery
EPC (SAP): B (87)
Cost (builder’s finish): £153k
Final cost (all inclusive): £200k
“My mum passed away in December 2015, and after that I settled back home,” says William. “I had lived and worked in England for a long while, and this move back to NI was the catalyst to building a home on land I had inherited from my uncle.”
“I started by looking for an architectural practice, and local estate agent David McKinney suggested a company specialised in eco builds that was energetic and progressive.”
“I wanted to build a low energy home because I knew it would save money in the long term. And now the house is so easy heated, I can say it does work.”
“When I met the eco build designer Ronan on site, the first thing I showed him was the view I wanted.”
“The original house on the property had been a 200 year old limewashed stone building which was originally home to three families. That was kept for sentimental value, as my granny had lived there, and for practical reasons. We kept it for storage now, and built the new part beside it so as to maximise the views.”
“The inspiration, first and foremost, was the surrounding landscape. I knew I didn’t want a big two storey house, and that suited the planners too as the skyline isn’t disturbed. My initial suggestion was a storey and a half to blend it into the landscape.”
Process of designing a low cost energy efficient home
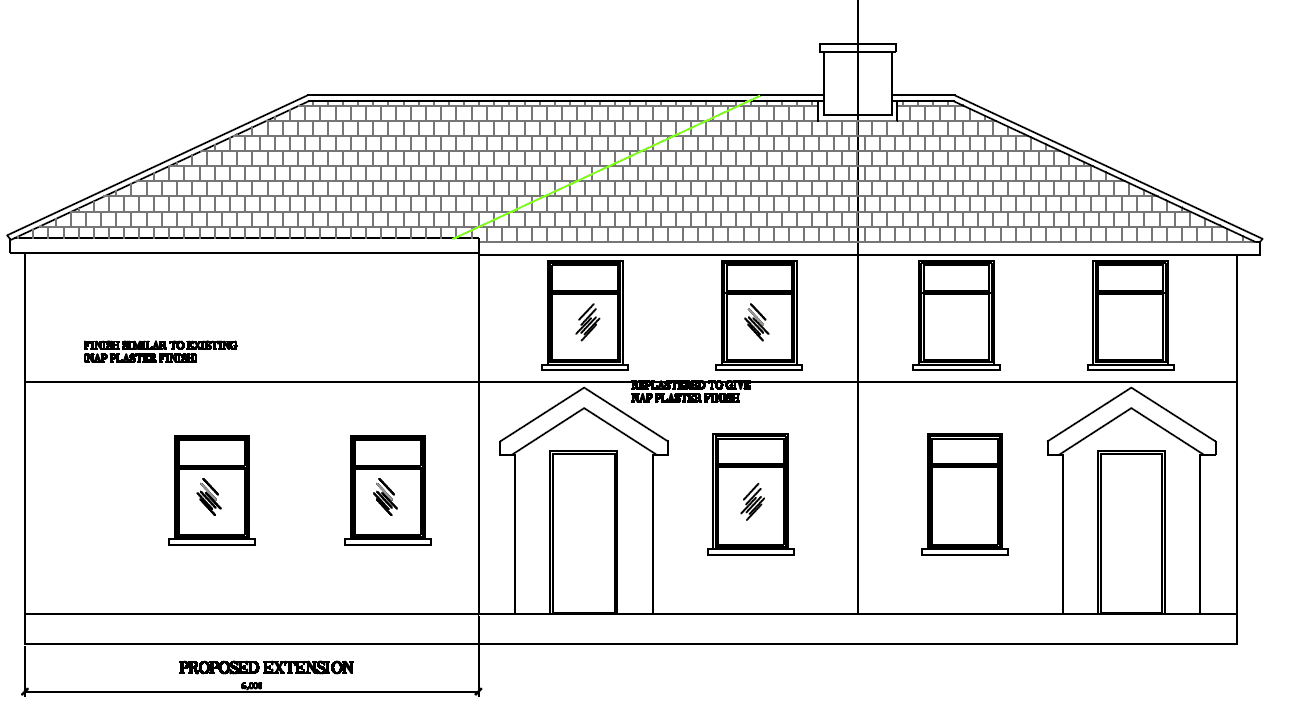
“To be honest, I first thought we would be building a square with a conservatory at the end,” says William. “I didn’t have to be persuaded to switch to the glazed opening instead – I loved the idea of a modern south facing wing.”
“My main concern was how much more it was going to cost and whether we could stick to that budget, and we were able to.”
The house went through the planning process without a hitch, under PPS21 for a replacement dwelling. “Having had my finances in order, I then started clearing the site. There were some trees to clear in different parts, especially for the creation of a new entrance and for the visibility splays.”
“At the beginning, because we’re on so much of a slope, a lot of the building work was underground which added to the cost,” says William.
“Then there were some outbuildings that had to be removed. At the end of it all, I had a lorry load of scrap metal taken away. There were some bits of furniture and other waste I brought to the council amenity site on a trailer.”
“In the spring of 2017 I was happy to use Ronan’s experience to project manage the build. I considered this to be a cost effective decision.”
“I had a fair idea of costs but also priced it around, asked relations and friends as well as a few builders. But after considering all angles I felt it was worth paying for Ronan’s expertise. I didn’t want to hold the build back for my lack of experience.”
“Around Easter time we were discussing how much it would cost, and Ronan put out the drawings to tender to get prices back from builders. That’s when we knew what the actual costs would be. I then signed a contract with both Ronan and Gary the builder; Ronan took charge of overseeing the project and involved me in the decision making process throughout.”
“For instance with the windows, Ronan sourced alternatives and gave me a choice of style, finish, then colour. I decided based on my budget and the look I was after.”
“Over the course of the build, there were additional costs, beyond the tender price we had agreed on. The first had to do with the groundworks, there was £5k in extra digger work for example, plus an extra 1,200 blocks needed to get the levels right.”
“The kitchen and tiles were extra, as was the choice to go with precast insulated foundations and my decision to pave the path 1m50 instead of 1m for extra walking space. There was also an additional steel support that had to be added for the open plan area, for the big window.”
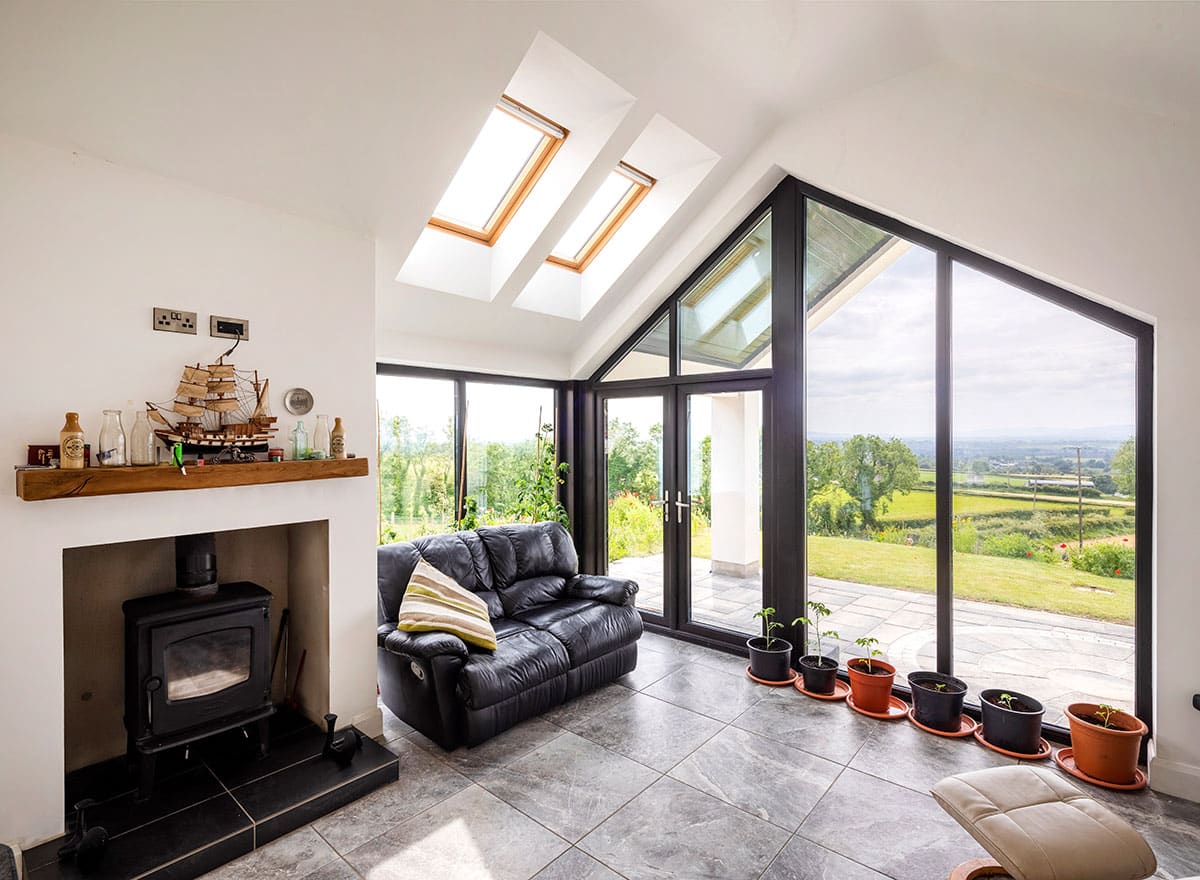
“Plus the tiling, which I was going to do myself, and spray painting. I hadn’t included those in the original contract so came to an agreement directly with the builder on these extras.”
“I was actually going to paint the walls and ceilings myself but it’s so much easier to have the painters do it professionally before second fix,” says William. “It’s more economical to do it then too. I just had to find the extra money for it.”
“Oftentimes, by spending more now you save in the long run. For example, when I had the joiner here from the kitchen company I asked him to also put in a built-in wardrobe to fill out the empty space in the dressing room. It beat the basic clothes rack I had there for a while. And the joiner on site put in shelves in the hot press; it made sense to get it done while he was still here.”

“Adding to the cost was the choice of the external silicone render as opposed to a traditional sand and cement finish. The only maintenance on the render is an algae treatment on the north side once a year to keep it looking fresh.”
“It’s a constant readjustment process,” says William of the self-build process. “I was reprioritising things all the time. When the tiler was here, for maintenance and for a uniform finish I figured I might as well go from the front door to the south facing wing including the utility room. The extra cost was the labour but better to do it then than have to ask them to come back.”
“When the electrician was here, I put extra lights in the south room and made sure the power plugs would have a chrome facing as opposed to white uPVC.”
“To balance the budget, I didn’t go for a slate roof covering as originally intended. I also meant to have the garage built, but I figured it would only be used as storage anyway. And I had the original cottage for that.”
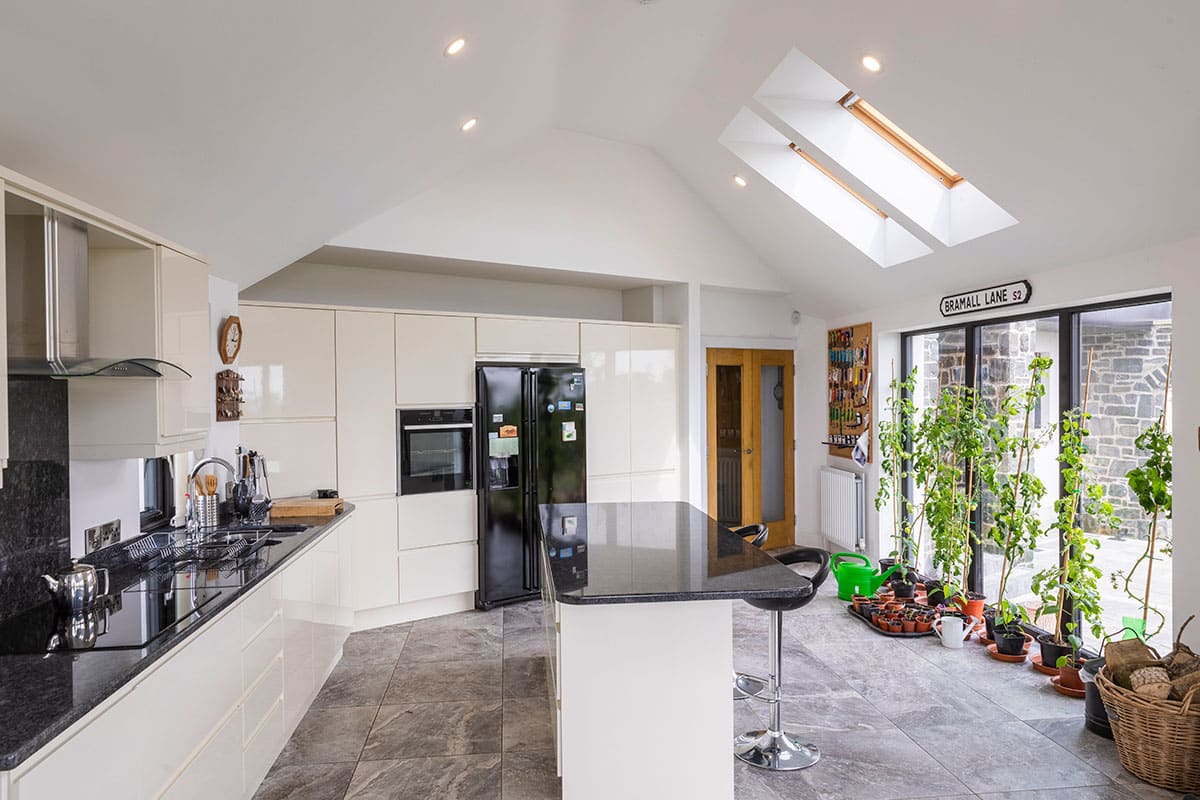
“Day to day, I had all of the stage payments organised with Ronan. If I had a question I didn’t hesitate to raise it,” says William. “The entire build was done through Ronan but I had my ear to the ground as to what was going on. I was there most of the time anyway. If there were questions or the build had problems, Ronan contacted me. As and when required.”
Living the life
“The house is built in such a way that the ensuite is upstairs with the master bedroom,” says William. “I had a dressing room on top of the wish list, and I got that too.”
“I also wanted to futureproof the house, in case I get in a situation where I am not able to go upstairs. That meant including a walk in shower downstairs with adjoining bedroom. I’m currently using that room as a gym.”
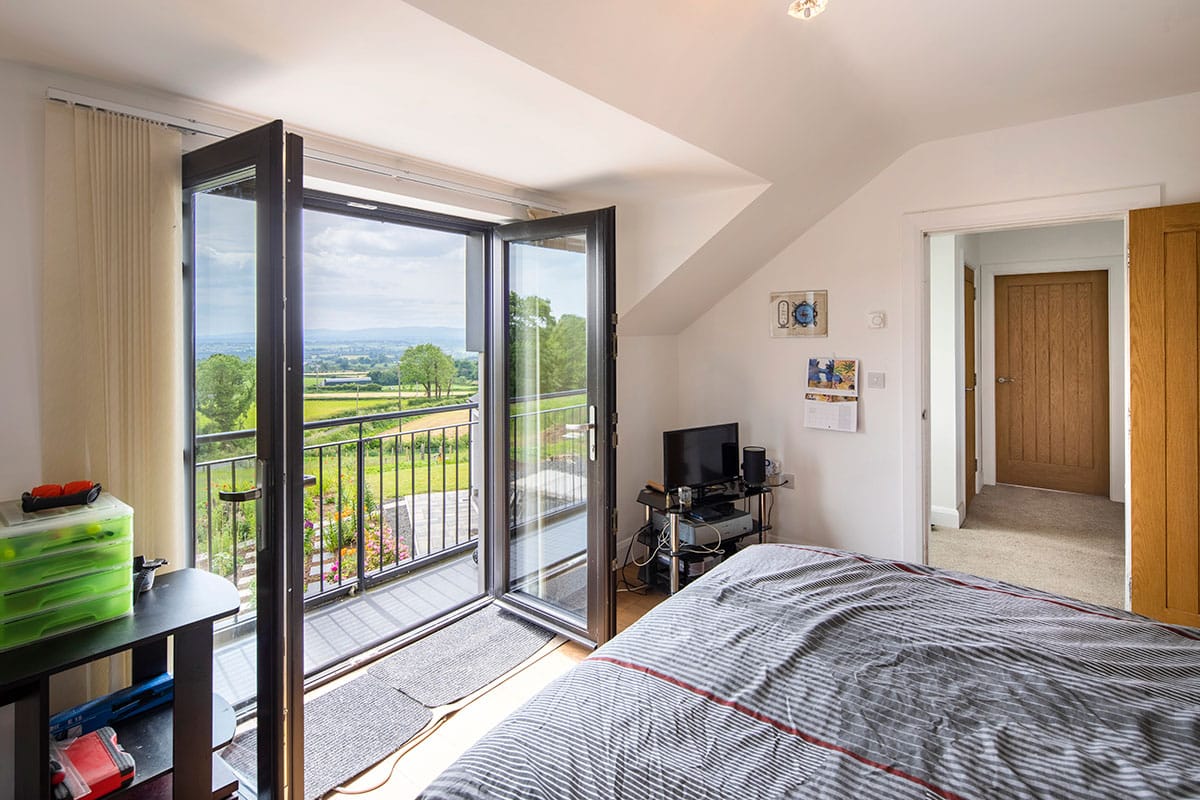
“The back of the house is my living area and it’s what I now refer to as the front of the house. The amount of glazing we put in is fantastic. The house is so easy to heat in winter. And it’s just such a nice feature.”
“I can’t believe how warm it gets,” he adds. “For the past couple of years I have grown tomatoes at the window, which keep me supplied from May to December. And I can use the space as a nursey type greenhouse, to get a head start on planting the vegetable garden.”
“Then it does get very hot in summer but I just open the patio doors for a draught and that’s enough to cool the house. The patio provides shelter from the high summer sun.”
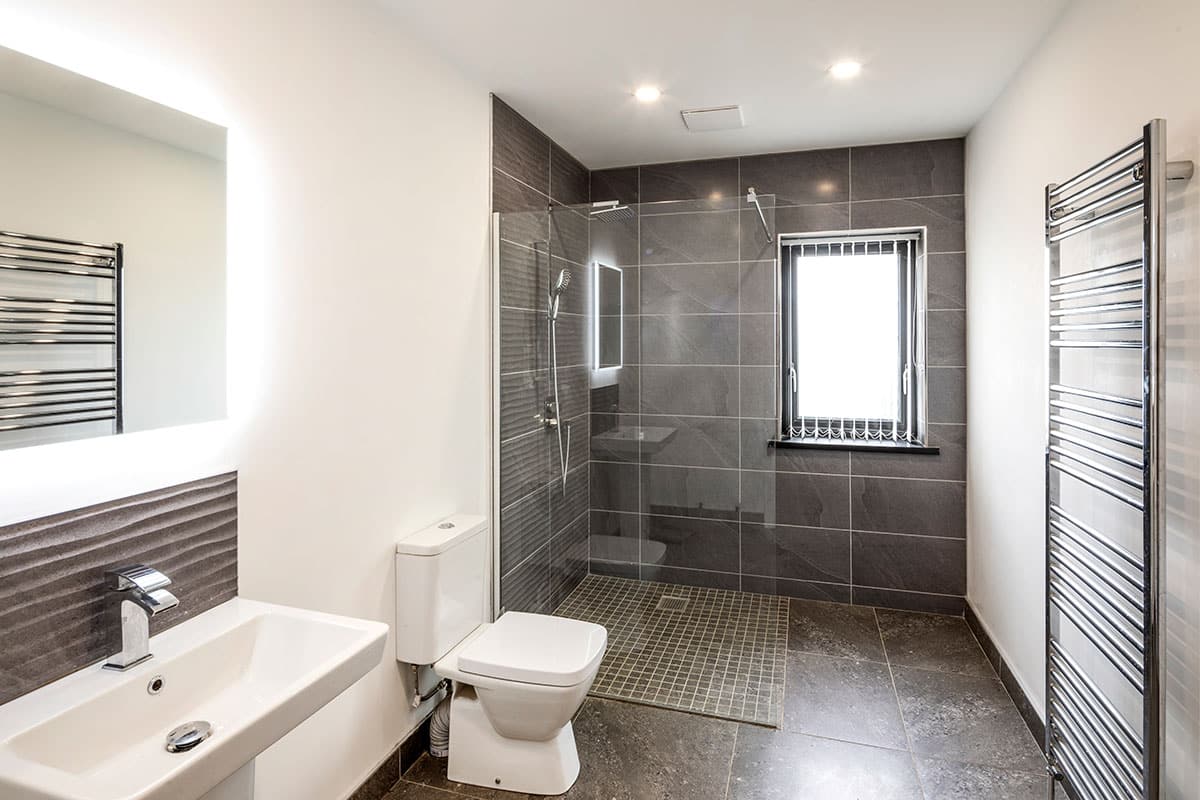
“Inside, the kitchen layout originally had a breakfast bar,” says Willian. “Ronan had left space for the kitchen with ideas of how to lay it out, but I approached a kitchen designer to help finalise those drawings.”
“We put the island in the middle and that simplified the design and provided more drawers for storage. I preferred it being in the middle as opposed to having a peninsula. There’s an internal door, which is glazed but split into two half doors, to transition from the hall to the south facing open plan.”
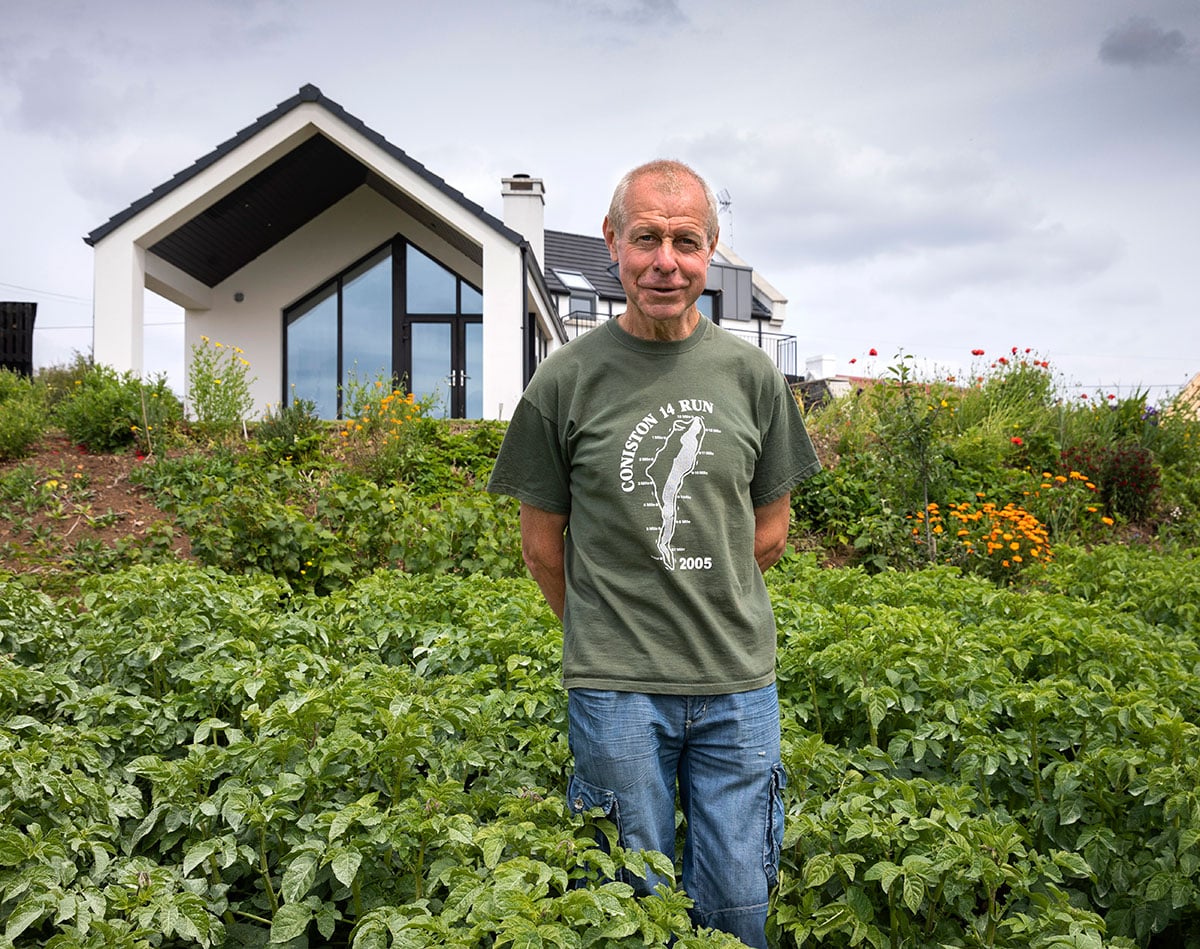
“After the house was built, I did have some work to finish,” says William. “The overflow drainage from the original cottage wasn’t connected to anything, coming out from a slope through the ground. I dug the drainage channel myself, and filled it in.”
“And I still have to do more landscaping, but it’s all enjoyable. I’m now almost self-sufficient for vegetables. I brought in topsoil for the vegetable garden and for the area at the front of the house – between it and the meadow I’m now growing potatoes. I’m living the life.”
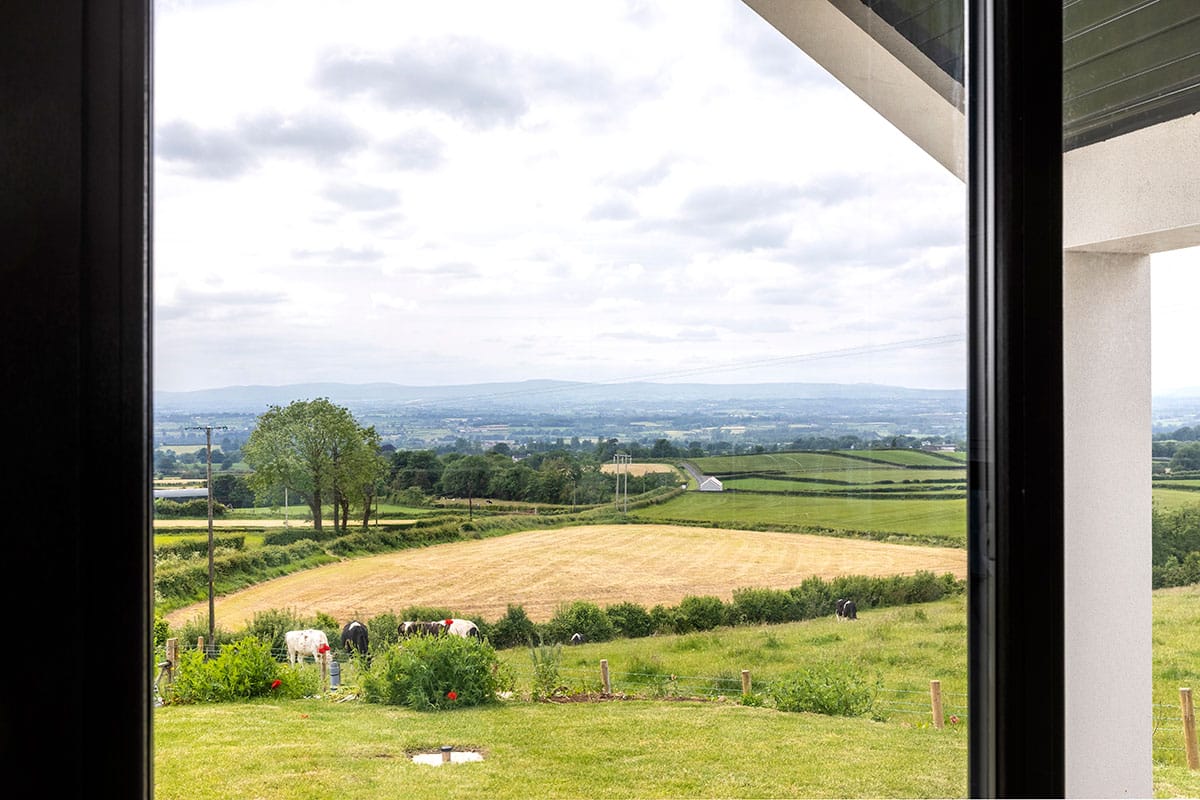
William’s tips
Spend time on your electrical plan.
My only regret is the way I have the power points organised in my bedroom. The L space is actually perfect for a desk but there are no sockets so I have an extension cord. And if I had known better, I would have put in dimmer lights too, for the open plan area. There’s also a socket above the fireplace that’s not being used, the original point for the television. I had another power point in the corner for it too, next to the view, which is what I now use because I like sitting near the fire and be able to either watch the telly or admire the view.
Design the house as if you were living in it, with all of the different furniture combinations you can think of.
I ended up having to buy new furniture for the space, as and when I needed them. Starting with the bed.
Q&A with William
What’s your favourite design feature?
The south facing room overlooking the Bann valley and Sperrin mountains, a view from Lough Beg to the Limavady Mountains. Even at night it’s nice looking out at all of the lights. I still have my granny’s oil lamp that still works; it’s nice and cosy with the fireplace. I went for a larger multifuel burner than I originally intended. It took up a few extra inches which impacted on building control and health and safety aspects but it didn’t cost more.
Would you do it again?
Seeing how expensive everything has gone, I’m not sure I could afford it now! Seriously though, now that I am all moved in, I don’t intend to move.
What would you change?
Apart from a couple socket positions, not a thing. Being so hands on when the house was built was a really enjoyable experience. Whenever plans were put to me, I had a clear vision of what I wanted and that’s how I ended up there. I’m delighted with the end result.
What’s your main piece of advice for self-builders?
Don’t be overambitious and live within your budget. Otherwise you won’t finish the house. Know what means you have, then allow for extra costs. Think about how you will manage the cash flow. Otherwise any extras could stall the project.
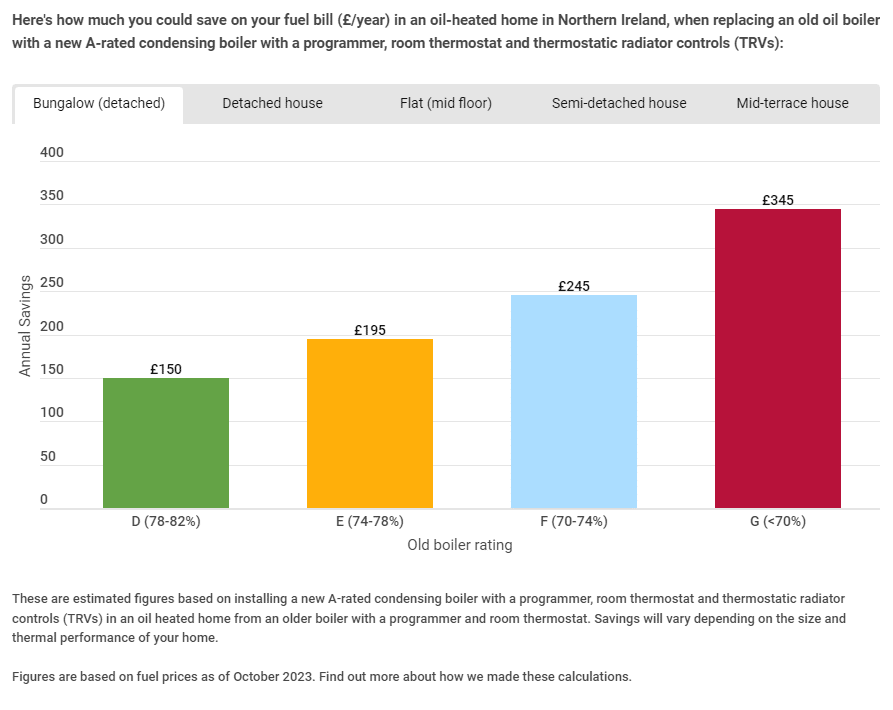
Low energy efficient home suppliers
Estate agent
David McKinney, Ballymena, mckinneys.uk.com
Design and project management
Ronan McKee of FMK Architecture Ltd, fmkni.com
Airtightness and MVHR
Supplied through Eco Homes Store, ecohomesstore.co.uk. Mechanical Ventilation with Heat Recovery: Vent Axia Kinetic Plus B, 90 per cent efficiency. Full airtightness system includes Blowerproof / Varafluid airtight paint on membrane and Compacfoam and Almatherm for thermal door thresholds.
Preinsulated foundations
Spantherm, creaghconcrete.co.uk
Builder
Gary Scullin – GP Scullin Construction
Windows
Baskil Passive Certified windows, baskilwindowsystems.co.uk
External plaster
K-Rend, k-rend.co.uk
Kitchen and wardrobes
James McCloy Joinery, Ballymoney, tel. 2588 1499
Patio
Tobermore, tobermore.co.uk
Bathrooms
Bassetts, bassettsonline.com
Multifuel stove
Lamont fireplaces, Coleraine, lamontfireplaces.com
Tiles
Moss Tiles & Bathroom Centre, Magherafelt, tel. 7941 8478
Electrical appliances
Basil Knipe Electrics, Ballymoney, basilknipeelectrics.co.uk
External lights
Yesss Electrical, Ballymena, tel. 2563 6758
Timber supplies (outdoors)
Clady Timber, tel. 582512
Furniture
Homestyle Ballymoney, homestyle-furniture.com
Fencing and posting
Killyless Stores, tel. 5880233
Photography
Paul Lindsay, paullindsayphoto.co.uk
ROI calling NI prefix with 048
Spec
Floor: EPS preinsulated foundations, U-value 0.14W/sqmK
Walls: cavity walls with 175mm cavity pumped with graphite coated EPS beads, U-value 0.18 W/sqmK, airtightness paint on airtightness membranes and thermal door thresholds
Roof: pitched roof 150 mm mineral wool between rafters with 50mm PIR boards under rafters, flat ceilings 550mm mineral wool insulation, U-value 0.08W/sqmK, U-value 0.16W/sqmK. Both installations include airtightness membrane with a 50mm service void below
Windows: triple glazed, overall U-value 0.74W/sqmK
Timeline
2008 – Inherited site
Apr 2016 – Planning applied
Jun 2016 – Planning approved
Jul 2016-May 2017 – Site clearance, tree removal
Jul 2017 – Signed contract
Aug 2017 – Demolition, new lane, build start
Sep 2018 – Build end
Oct 2018 – Moved in
Nov 2018 – Completion cert from building control