In this article we cover:
- What is ICF
- Difficulties being an early adopter of ICF
- How he secured planning permission
- Roof details
- Floor construction and window choices
- Heating system choice
- Costing the project and choosing to go direct labour
- Top tips for the direct labour route and how he went about it
- Top tips to keep the project on track
- How he kept on top of costs, budgeting tips
- Interior design and kitchen tips
- Floor plans and full specification
- Timeline and professional photographs
Michael grew up on a small farm in Co Longford which has been in his family for three generations. “The site I built on is roughly a mile and a half from my childhood home,” says Michael. “This land has a special connection to my family because it once belonged to my great uncle, Mike Fox, who was a well known figure in our local community.”
House size: 2,600 sqft
Bedrooms: 4
Plot size: 3 acres
BER: A2
Heating and hot water: air source heat pump
Ventilation: centralised mechanical with heat recovery
Build method: Insulating Concrete Formwork (ICF)
“Uncle Mike used to grow vegetables on this land and sell them at the local market. There was an old, extremely dilapidated house on the property; all that remains of it today is its foundation.”
Michael left the area for college in Galway, where he earned his engineering degree but work eventually brought him back. “I started working for a global energy company that established a local presence, and when I felt settled, I decided it was time to build my own house.”
“Having the opportunity to start anew and build a home on our land meant a lot to me. It’s like being a custodian of our family’s history. There’s a deep connection and a sense of responsibility associated with this site. I incorporated some of the old house’s stones into the facade of the new one, which adds even more meaning to it.”
“My design inspiration for the new house came from various sources. I had the chance to travel for work to places like Norway and Scotland, where I saw impressive modern and contemporary houses. I was particularly drawn to a design I saw on a TV programme, featuring a curved roof that blended seamlessly with its natural surroundings. I took elements from these designs, combining them with the local rural style, to create the vision for my house.”

Planning mastery
Given Michael’s engineering background, he felt confident to tackle the planning process himself. “I educated myself about the process and took the architect’s initial design to create the planning application. But, before that, I had a pre planning meeting with the local authorities, where I discussed the design, site specifics and what I aimed to achieve.”
“I was concerned about the unique barn style design of the house, as it featured a pitched roof, which was different from typical local architecture. However, I was pleasantly surprised that the planners were open to innovative designs that fit the rural setting. It turned out to be a smooth process, and the planning permission was granted without any issues.”
“People have asked me how I navigated this, and my advice is always to study the County Development Plan, meet with a planner for a pre planning meeting and be aware of what the local regulations allow for innovative designs. This approach worked well for me. I realised the importance of clear communication and understanding with the local authorities. It helped me tailor my plans to meet their expectations and address any concerns they might have had.”
Michael opted to build with insulating concrete formwork (ICF), which was pretty new on the self-build scene when he began his new build project.
“When I first encountered ICF, I had reservations about its cost, thinking it might be too expensive. However, at a Selfbuild Live event in Belfast I met a helpful ICF supplier who helped me explore my options.”
“As I delved deeper, I found that it offered comparable costs to conventional block construction but with significant advantages, including superior airtightness, speed of construction and insulation properties.”
“For the roof, I initially wanted zinc cladding but found a cost effective alternative, a uPVC style roofing material that resembles zinc – it also came with a 25 year warranty. The roof structure itself is constructed using engineered timber.”
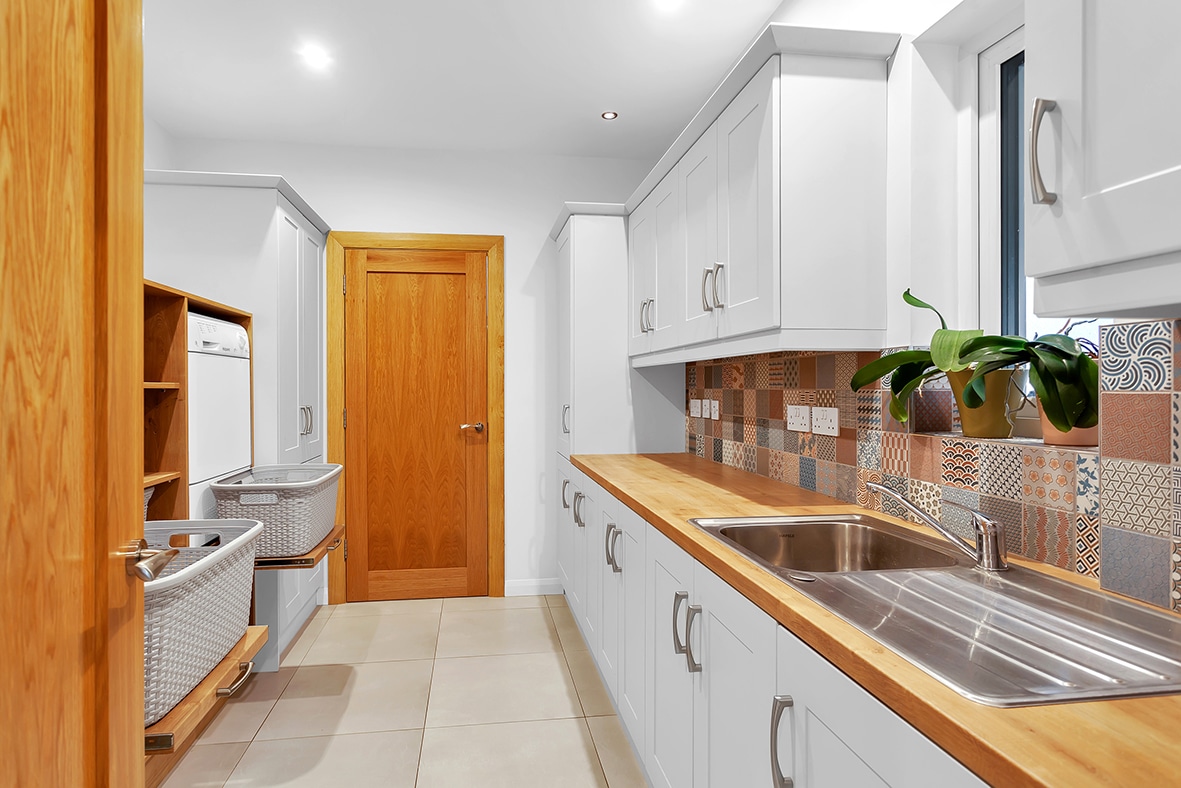
“I chose a precast concrete floor for the upper level to reduce noise transmission between floors and improve fire safety. In my previous experiences, timber framed houses with timber floors upstairs tended to be quite noisy. As for floor covering, I installed timber floors throughout the house, both upstairs and downstairs, for a consistent finish.”
“I selected triple glazed windows with grey frames to complement the overall design and opted for underfloor heating as it provides a more consistent and comfortable temperature compared to conventional radiators. Additionally, I incorporated a mechanical heat recovery system, which I installed myself, to maintain air quality without the need for frequent window opening.”
“Given the house’s excellent insulation and energy efficiency, a 7kW air to water heat pump was sufficient for heating needs, eliminating the need for an additional heat source. But I am currently exploring the possibility of adding solar panels this year, to further enhance the home’s energy efficiency.”
Direct approach
“I initially approached a local builder with my plans, but the quote I received was substantially higher than expected. This was primarily due to the unique design and associated risks. The builder factored in a large contingency for any potential issues, making the cost prohibitive. So, I contacted several ICF contractors within a 60 mile radius, thoroughly evaluating their work and pricing to select the most suitable one for the project. I decided to take on the project management role myself and opted for direct labour.”
Given the design’s unconventional nature, finding skilled tradespeople was a critical aspect. “I researched the market extensively, dedicating three years to gathering knowledge,” explains Michael. “I sought multiple quotes from different trades, ensuring they aligned with my project’s standards. I didn’t solely rely on references provided by the trades; I conducted my research and observed their work. Building relationships with trades is essential, but it’s equally important to maintain a firm stance on quality standards to achieve the desired results.”
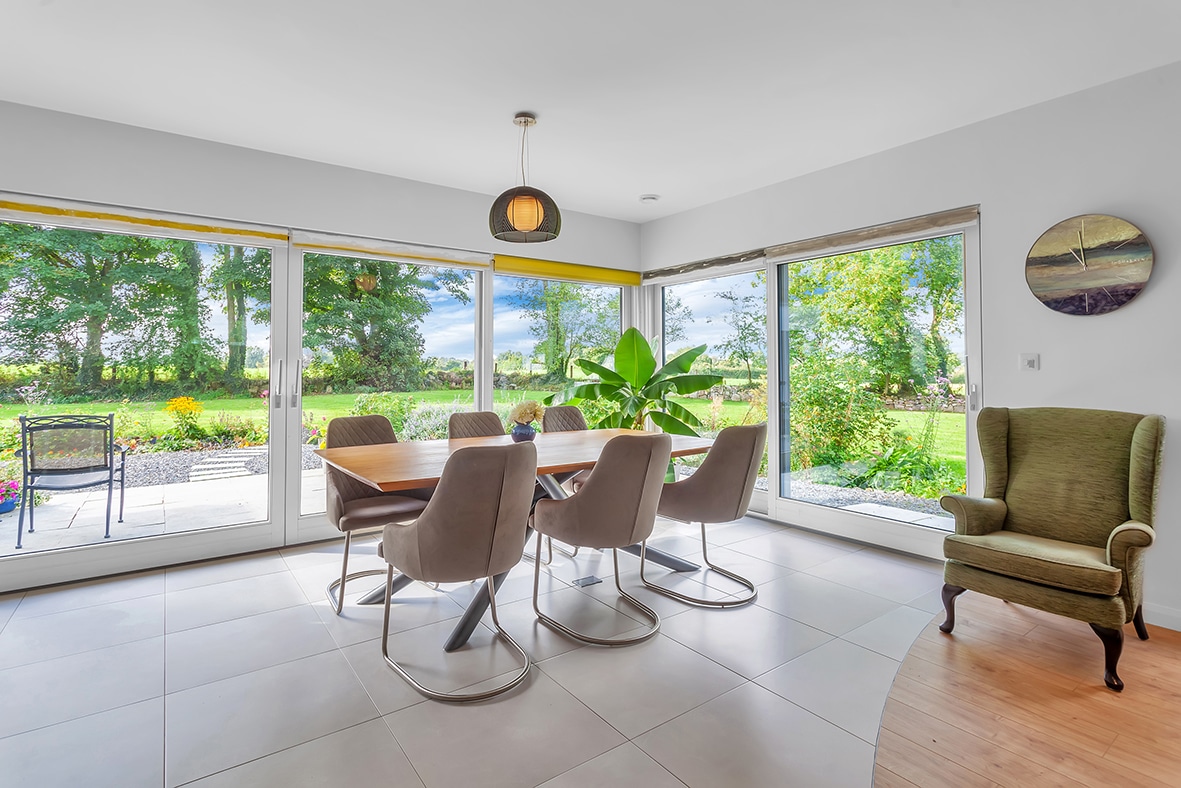
Michael took on various tasks during the build, such as groundwork, sewer pipe installation, wall chasing, installing a mechanical heat recovery ventilation system, setting up a CCTV system and painting. “However, I learned that it’s crucial to strike a balance between DIY and hiring professionals. You need to assess what tasks you can realistically handle yourself. Don’t take on tasks that are beyond your skill set. For instance, unless you’re a professional plasterer, don’t attempt plastering. Instead, consider more manageable tasks like wall chasing or other projects that fit into your daily life. Trying to do too much can lead to mistakes that will ultimately cost more in the long run, both in terms of money and time.”
Michael’s engineering background provided a foundation for managing schedules and budgets. “I maintained detailed records using a spreadsheet
to track costs, invoices and schedules. While my experience helped, I also dedicated time to understanding the specific needs of this project. The lack of time pressure allowed me to plan meticulously, ensuring everything progressed smoothly, but there were still some things that took me by surprise.”
“I underestimated both the cost and safety requirements associated with scaffolding. I had initially thought about setting up some of it myself, but a safety review revealed that a certified scaffolding company was necessary. This additional expense wasn’t originally factored in, and it added some pressure to the project timeline.”
“Delays, such as waiting for windows to arrive while the scaffolding was in place, were among the challenges we faced. Time management really is key in self-building. It’s not uncommon to find yourself juggling multiple responsibilities and schedules to keep the project on track.”
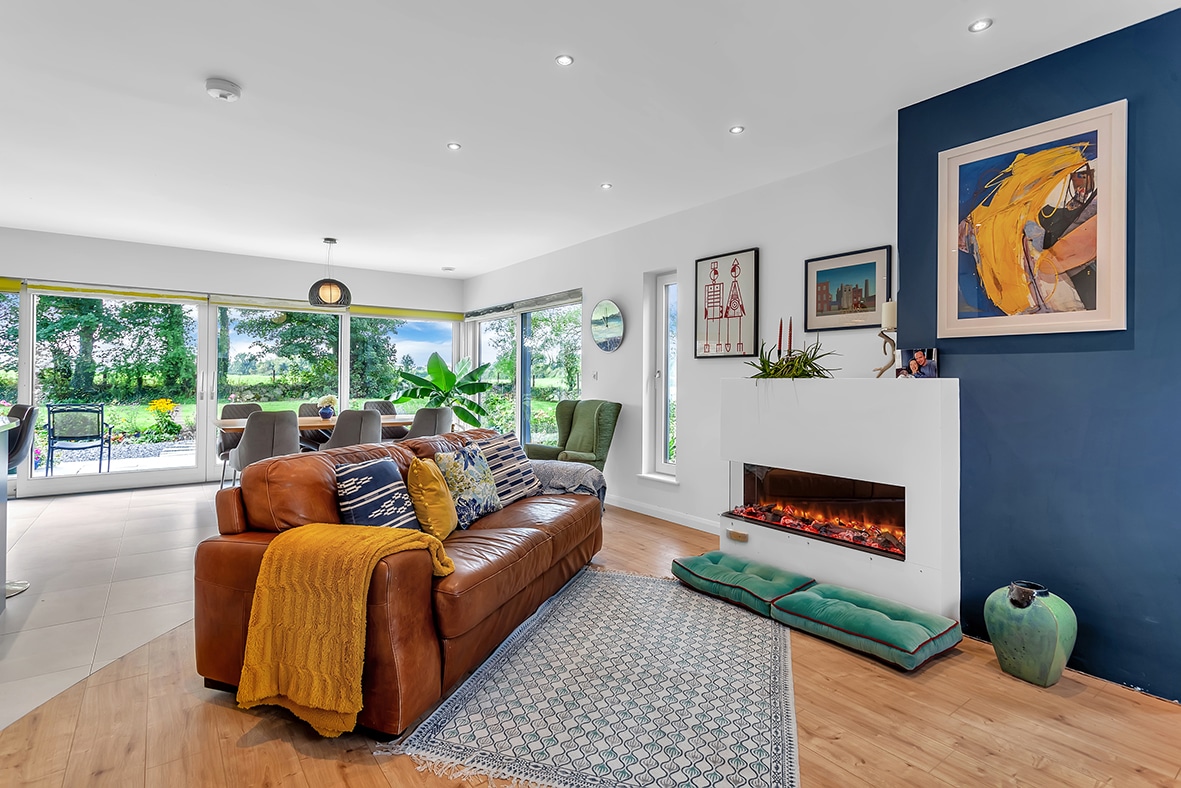
Free flow
“The interior design blends an open plan style with mid century furniture influences. We aimed for a minimalist, free flowing layout with carefully selected individual pieces of furniture, sourced from various places, including online marketplaces.”
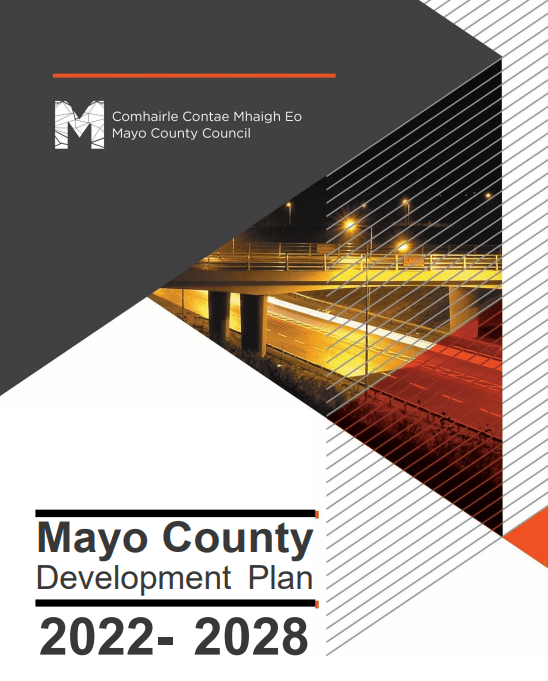
“My wife played a significant role in designing the interior, focusing on colour palettes and repurposing old pieces. I even built some of our
furniture, like the kitchen table, using Irish oak.”
“The kitchen was custom designed by a local kitchen manufacturer. It features a two tone design with a combination of dark grey and soft white, complemented by a quartz countertop.”
“Overall, we’re delighted with how everything has turned out. But, as the house was originally designed before I met my wife and had a family, there were a few things that would be included now, if we were starting again.”
“For example, we would have preferred a larger walk-in wardrobe in the master bedroom. And, while functionally designed, the utility room could be bigger, particularly considering the need for space for boots, etc.”
Externally, Michael handled most of the landscaping himself. “When we moved into the house in 2018, the driveway was just loose gravel, and there were no fences or paving. I landscaped the property with a focus on low maintenance features. I used decorative gravel for the driveway, which is easy to maintain and doesn’t require frequent power washing. I also opted for a metal fence, galvanised for durability and minimal maintenance.”
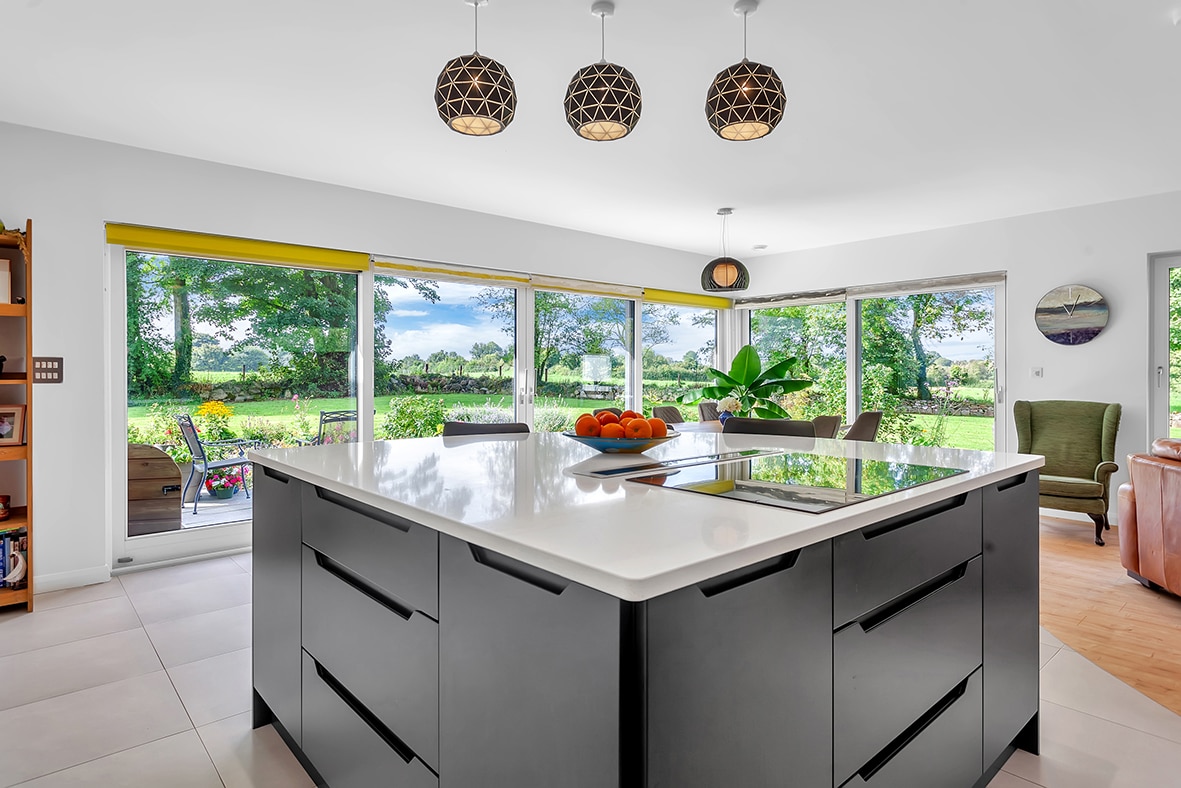
Wearing his engineer’s hat, Michael had some thoughts on the construction process, and how it could improve. “From an engineering standpoint, implementing well structured contracts and governing documents for construction projects could greatly benefit both contractors and homeowners. It reduces misunderstandings and grey areas, ensuring that everyone is on the same page throughout the process.”
“I did face some initial resistance when trying to implement this approach with traditional trades, but I believe it would greatly benefit the industry as a whole.”
“It’s been quite a journey, from planning and designing a self-build to creating a warm and cosy family home. I met my wife to be during the build, we later got married and now have two daughters and a dog.”
“Our home has transformed from a bachelor pad to a family friendly space, and it’s been a wonderful transition.”
Click here for Michael’s self-build diary.
Q&A with Michael
What is your favourite design feature?
I would have to say the main sitting room with its curved ceiling is my favourite space in the house. It offers a unique perspective of the site, immediately capturing the view of the mature trees and creating a relaxing ambiance. We invested in a large, bespoke couch for that room, which is where we spend a lot of our time.
What would you change or do differently?
There are very little things we would change, but maybe we’d make the master walk in wardrobe larger and also increase the size of the utility room.
What surprised you?
One of the significant challenges I faced as a project manager was being responsible for all stages of the construction. For instance, the concrete stairs were installed at the wrong height. We were able to rectify that but it left very little distance between the bottom of the front door and the floor, leaving no room for a door mat. We ended up incorporating recessed mats under the doors. As a self-builder you have to oversee every detail because ultimately, you’re accountable for the project’s success or any issues that arise.
What advice would you give a budding self-builder?
I would strongly advise them to invest time in thorough research and gaining knowledge. I spent three years researching and learning about various aspects of construction, and it paid off significantly during the project. Being well informed and inquisitive is essential when taking on such a venture.
Would you do it again?
I wouldn’t hesitate to do it all over again. I relished the challenge and enjoyed the experience of seeing a brand-new space come to life. Being the first occupant of a newly constructed home and witnessing it evolve was truly rewarding.
Michael’s Tips
Meet the planners. Even if you intend to hire a professional to complete the planning process, I would strongly encourage you to go through the pre planning process first to gain insights from it.
Be prepared to give up all your time. Self-building requires a significant time commitment. During
those two to three years of our build, there were no Sundays; it was all Saturdays. It’s essential to be prepared for the time and effort it demands. I thoroughly enjoyed the process because I had the time then, but I realise it might not be feasible now, with a young family.
Have a good support network. I was extremely lucky to have a support network consisting of family, friends and good neighbours who were always on hand to offer support and guidance, and also to open the site for tradesmen on the rare occasions that I opted to have a lie in!
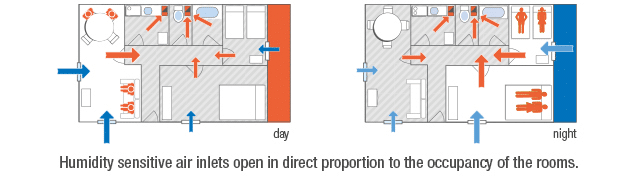
Spec
Walls: 63mm ICF each side 6-inch concrete inside, five-part acrylic render system, U-value 0.22W/sqmK
Windows: triple glazed aluclad
Roof: truss roof, cold roof construction, 400mm mineral wool, U-value 0.11W/sqmK
Floor: standard build up with 150mm henolic board insulation (2x75mm cross lapped), U-value 0.13W/sqmK
Suppliers
Architect
Enda McKiernan Architects
Builder’s merchant
B Fallon Hardware Longford
Roof trusses
Murdocks
ICF
AMVIC Ireland
uPVC covering
Alkorplan
Roof
Pat McKnight Roofing
Photography
Damien Kelly, damienkellyphotography.com
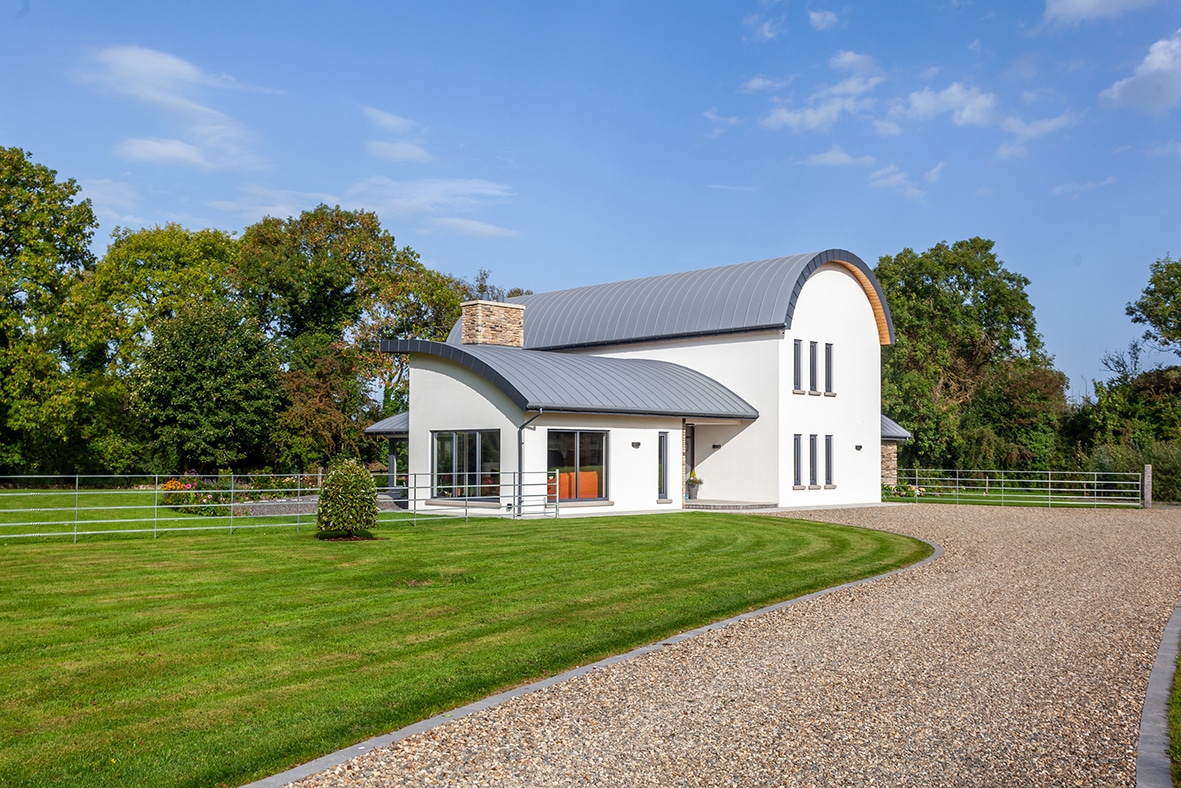