In this article we cover:
- How the house was designed
- Securing planning permission
- Financing the project
- Hiring tradesmen: top tips
- How they saved money
- Help from friends and family
- Details of how the house was built
- Which DIY element they took on
- Window choices
- Parquet flooring details
- Heating, ventilation and electrics
- Adapting a secondhand kitchen to their needs
- Landscaping details
- Professional photographs and supplier list
- Floor plans and specification
From designing their dream home to overseeing every detail of its construction, Michael and Edel were in charge of their self-build every step of the way.
It’s a project that began with the couple living in an old cottage, which they found themselves staying in far longer than anticipated. “We did a lot of work on the property, extending and renovating, but at this stage it had outgrown its potential,” says Michael.
House size: 4,500 sqft
Bedrooms: 7
Plot size: 0.4 acre
BER: A2
Heating system: air to water heat pump, standalone stoves
Ventilation: centralised mechanical heat recovery
Build method: cavity block
As a civil engineer with a wealth of experience in building and construction for major contractors, he led the charge to self-build their home.
“We were looking for potential plots and discovered a site on the edge of a lovely village in Laois,” says Michael. “It was close to family and adjacent to the golf course — an ideal scenic location— so Edel and I decided we’d try building again, this time from scratch.”
Crafting the blueprint
“Even though the plot wasn’t massive, we decided to go big with our house plans. We wanted to squeeze in as much as possible, so we went for a tall, two storey house with an attic conversion. This also helped us capitalise on the scenic views across the adjacent golf course.”
“The fact that Edel and I designed the house ourselves meant that we could make it fit and suit the site in the best way. I did all the planning permission application work, developed the construction drawings, and went on to manage the self-build without additional professional help.”
“However, I did have an independent supervising engineer for the purposes of quality control and drawing down the mortgage from the bank.”
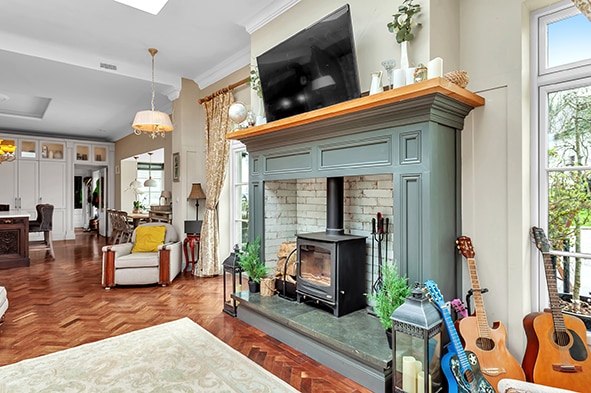
“When we purchased the site, there was already outline planning permission for a different, smaller house. We held the permission until we were ready to proceed with construction.”
Saving up for the build and ensuring they were financially prepared while still living in the old cottage posed a challenge.
“Securing a bridging loan was difficult due to the economic downturn, but we obtained approval in 2016. Fortunately, we were able to sell our previous home just as the new house was nearing completion, which worked out well for us.”
Michael and Edel relied on word of mouth and his previous connections within the construction industry. “I didn’t extensively shop around for quotes; I knew the specific individuals I wanted to hire. Through referrals and recommendations, one thing naturally led to another. The plumber we hired was local, as was the block layer, who happened to be related to the ground worker. We also received skilled help from Edel’s family, with her cousin and uncle serving as electricians. It was important to us to assemble a team of individuals we trusted to deliver quality work.”
Tackling challenges
Managing the project proved challenging, with Michael and Edel working full time while juggling raising four children aged three months to six years. “We also had to sell our original home, which was probably a bigger job than building the other house, to be honest. It was a lot of work and quite stressful.”
“But when you can do it yourself – design and manage the build – you can save so much money, so it was worth it. I don’t think we could have built this house without direct labour; it would have been far too expensive.”
One of their biggest challenges was navigating the aftermath of the recession. “Banks were hesitant to offer mortgages for years after the 2008 crash. New building regulations required self-build houses to be supervised by a chartered engineer and built by a registered builder. Although the regulations had changed a year before we started, banks were slow to adapt, which delayed our project.”
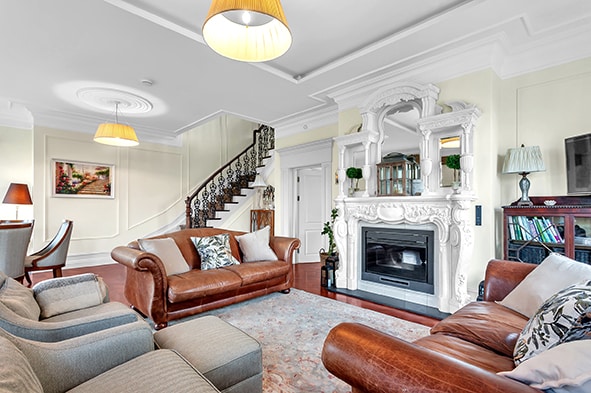
An opt-out clause was subsequently introduced to allow self-builders to build their home without having to hire an assigned certifier.
Taking charge of the project themselves meant countless late evenings and weekend commitments. “Many times, we found ourselves arriving on site after dark, with the day’s work already completed, trying to catch up on progress. During weekends, we juggled various tasks around the house.”
“There was less opportunity to supervise than I would have liked, so that was a challenge. I probably would have done a lot of work myself, but I just didn’t have the time.”
“We were very fortunate to have Edel’s aunt and uncle help us out, they own a builder’s merchant in Monaghan. They and their staff were a huge help in giving us advice on products and sourcing products for us.”
“When we moved in for Christmas, conditions were far from ideal, but we needed to get in. We had sold our house at this stage and had been living with Edel’s parents for a couple of months, so it was time to move. Despite having electricity for only two weeks and minimal heating for a few days, we made do with bare concrete floors, an unfinished bathroom and a rudimentary kitchen to get by.”
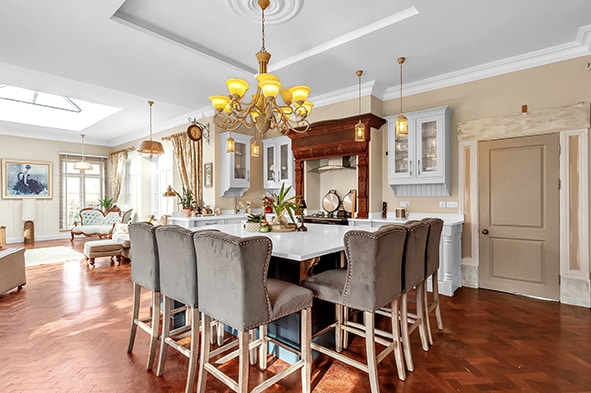
Hands-on design and build
The house’s structure is made up of traditional strip footings, concrete cavity block construction with blockwork and timber partition walls, a concrete ground floor, hollowcore precast first floor slabs and a timber floor on the upper storey. A non-structural screed was poured on the ground floor to facilitate the underfloor heating.
The roof is a traditional timber roof with two-tone fibre cement slates. “There is a flat roof component at the top of the house with a roof lantern positioned over the stairwell, which is centrally positioned within the house,” says Michael. “We also have a flat roof on our sunroom with another roof lantern.”
Michael took on much timberwork throughout the house, such as laying the reclaimed parquet flooring on the ground floor. “It was a lot of work — there were thousands of parquet pieces that had to be individually cleaned, planed, and laid— but we saved thousands of euros on installation costs, so it was worth it.”
Glazing and artifical lighting also played a critical role in the design. “We opted for a French-style window design that is in keeping with the house’s overall style, bringing in lots of natural light and making the most of the beautiful views around us. Placing larger windows and doors on the ground floor helped create an easy flow between inside and outside, making the space feel more open and connected.”
Michael and Edel opted for standard lighting and wiring plans throughout the house. “With the constant evolution of wifi enabled products, we’re relieved we didn’t invest in any specific lighting technologies,” says Michael.
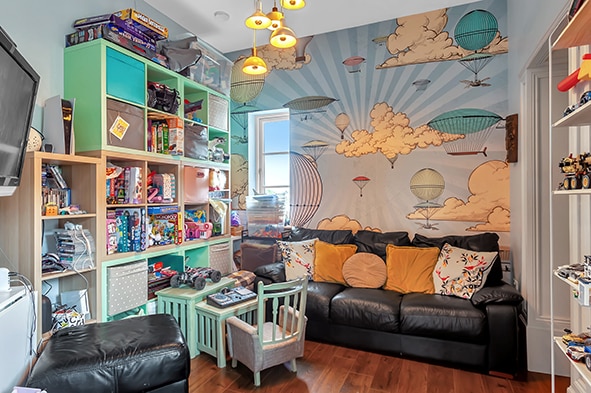
An air to water heat pump and heat recovery ventilation complete the set up. Underfloor heating serves the ground and first floors, with radiators heating the second storey.
“We installed a wood stove in the sunroom, not because we needed the extra heat, but because it gives the room a cosy feel. The solar gain from the glazing in the sunroom — even in winter — is huge. Opening into the kitchen, this is the heart of the home all year around.”
A pellet stove installed in the dining hall, which is open to the central stairwell, helps distribute additional heat throughout the first and second floors of the house.
Next steps
“We’re thinking about adding solar panels to reduce our running costs,” says Michael. “While we initially wanted to include them, we prioritised other aspects at the time. However, it’s something we can still consider at a later stage.”
As for the kitchen, it came from the manufacturer that supplied the units for their original cottage. “I managed to buy this kitchen secondhand before we even started building the house. We liked the design so much that we wanted to incorporate it into our new home. I arranged the layout of the kitchen around the units. But, since moving in, we’ve made significant changes.”
“We added another wall of storage units from a different supplier, and I also built the kitchen island myself. It features an old dresser backing onto modern units, all hand done in a shaker style.”
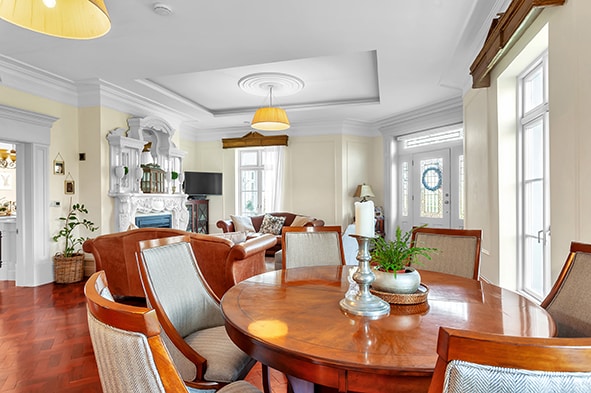
Michael and Edel felt it was important to create a safe environment for their children and visitors to enjoy outside. “We built the outdoor patio areas pretty soon after moving in, even though there was a lot to do inside. But we have no regrets about investing in the outdoors early on.”
Overall, they were happy with how smoothly the construction progressed, especially considering the availability of labourers at the time. “Things moved along seamlessly with the labourers, block layers and roofers until we reached the stage of making the house airtight. However, as we neared the end of our project, we noticed a shift. Securing contractors and labourers became increasingly challenging as demand for their services started to rise again.”
Fruits of their labour
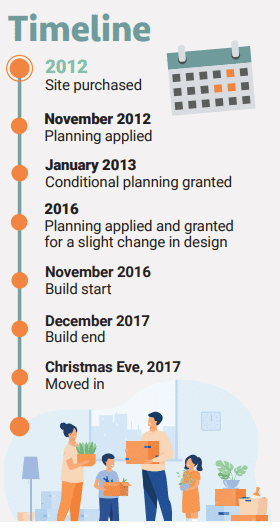
How well does the house serve as a family home now? “It’s absolutely wonderful. We’ve designed spacious, open plan rooms that connect throughout the house,” says Michael.
“The kitchen is the hub, flowing into the sunroom and living area. Instead of compartmentalising the space with walls, we opted to limit the number of hallways. We have a ‘dining hall’ on the ground floor – a warm and inviting entrance to the house that opens up into a generously sized living space. It’s perfect for gatherings, with a dining area, cosy seating and a sleek pellet stove adding to the atmosphere.”
“Our home exudes comfort, with easy access to the garden via the patio. During the planning stages, we aimed to incorporate chimneys for their visual appeal, resulting in more than we initially planned. This allowed us to include an outdoor fireplace on the patio and even one in the bathroom.”
“Our primary objectives in designing our home were to create ample space, ensure comfort and make it operate as efficiently as possible. Looking back, I have to say there’s nothing we would change or do differently.”
“We wanted a secure and inviting environment where our children could thrive, and that’s exactly what we got.”
Q&A with Michael
What is your favourite design feature?
The sunroom is a lovely space, and I love the stairs. From the hallway, you can look up to the top of the house, and the roof lantern brings natural light right down through the core of the house, which is excellent.
What surprised you?
How exhausted I was at the end of the whole process.
What single piece of advice would you give a friend who’s looking to embark on a project similar to yours?
It isn’t easy to offer advice because I wouldn’t advise anyone else to do it the way we did, as you would need in-depth knowledge of every aspect of the build. So make sure you have the right advice and professionals advising you and always go with recommendations.
Would you do it again?
While I’m proud of the result, I’m not sure I’ll be doing it again
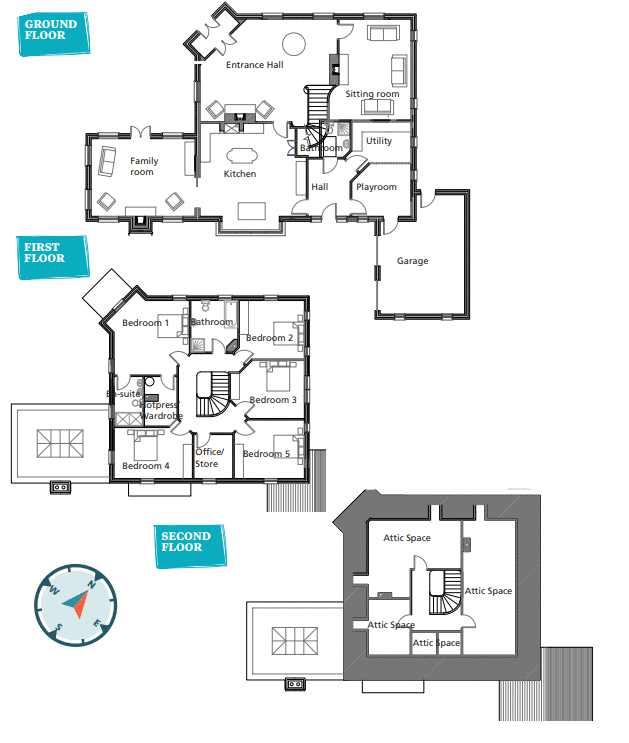
Spec
Walls: cavity wall construction 100mm blocks, 50mm cavity filled with PUR boards with wall ties at 750mm centres horizontally and 450mm vertically, internal walls 50mm PUR laminate plasterboard, skim finish
Floor: 100mm powerfloated concrete slab on 100mm expanded PUR board on continuous radon barrier on well compacted sand blinding and hardcore filling
Roof: spray foam insulation
Windows: triple glazed timber aluclad
Suppliers used for this hands-on selfbuild in Co Laois
Heat pump
Joule
Ventilation
ProAir Heat Recovery Ventilation, Co Galway, proair.ie
Builder’s merchants
Fletcher’s Topline Hardware Portarlington, Co Laois, and Grahams of Monaghan, grahamsofmonaghan.ie
Attic insulation
Pro Spray Foam, Birr, Co Offaly
Windows
Rationel Windows, Edenderry, Co Offaly
Electrics
Johnny Fitzpatrick Electrical, Mountrath, Co Laois
Photography
Damien Kelly, damienkellyphotography.com