In this article we cover:
- Finding the site
- Bidding for the site
- Searching for original planning permission
- Adapting the plans
- Appointing a main contractor
- Dealing with the builder going bankrupt
- Cash flow management
- Taking on the build as direct labour
- Tips for going direct labour
- Interior design choices
- Window choices
- Heating system
- Professional photographs
- Timeline
Anita and Mark weren’t actively looking for a building site, but when an auction alert popped up on Mark’s socials for a site with an unbelievably low guide price, they decided to go for it.
“The land is located in my husband’s hometown and not far from where I’m originally from,” explains Anita. “When we drove up and took a look at the site, we just thought, why not? The reserve price was great value with full planning approval, it seemed like a fantastic opportunity.”
When the auction day came around, back in 2013, Mark was working abroad, so a pregnant Anita took along her father-in-law for backup.
House size: 3,500sqft
Bedrooms: 4/5
Plot size: ¾ acre
Heating system: Oil boiler
Ventilation: Natural (trickle vent windows)
Build method: Blockwork
“My father-in-law and I agreed to cap our bid. However, it turned out that there were three repossessed sites up for auction on that lane. We stopped bidding for the first site when we reached our cap and it sold for not much more. My father-in-law suggested that if the first one had sold for that amount, then the next one might sell for about the same. So, we increased the cap, he stuck his hand up again and we bought it.”
The Joneses weren’t in a position to progress with their building plan initially. “I was pregnant and we were finishing up an extension to our existing home at the time. However, because the foundations for the garage had already been laid, we knew that the planning permission was protected.”
Best laid plans
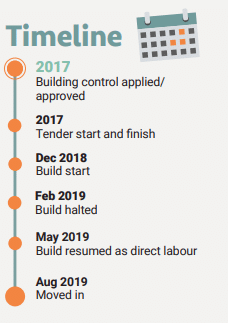
The couple picked up their self-build journey a little later, going on a search for the original plans.
“We phoned around a few local architects and happened to find the one who had signed the building plan in the planning commission. He gave us the contact details for the original architect and we went to him directly.”
“When we viewed the plans, the only thing we changed was the number of upstairs bathrooms – reducing from four to three – we didn’t see the need for the extra one. Everything else worked for us, so as the plans had already been submitted and approved, we just stuck to it.”
Externally, the house style is a timeless, storey and a half bungalow with dormer windows rendered and painted off white with a slate roof. There is a separate double garage with an upstairs office.
“Our friends had recently built their own home and recommended their builder to us, so we included him in the tender along with two other builders. We ended up choosing our friend’s recommended firm. His fixed price was really good for the house size and for all the things we wanted. It was almost a turnkey finish so we felt reassured that we wouldn’t need to stress or worry about it.”
“Yet, we were cautious. Though he estimated an 18-month construction period, we anticipated it could stretch to two years due to potential delays and rising costs so we aimed to solidify the plan to prevent unforeseen escalations.”
Anita and Mark had meetings with the builder throughout the construction process where he briefed them on the ongoing work. “At that time, I was on maternity leave, so I could be on site to make decisions,” says Anita.
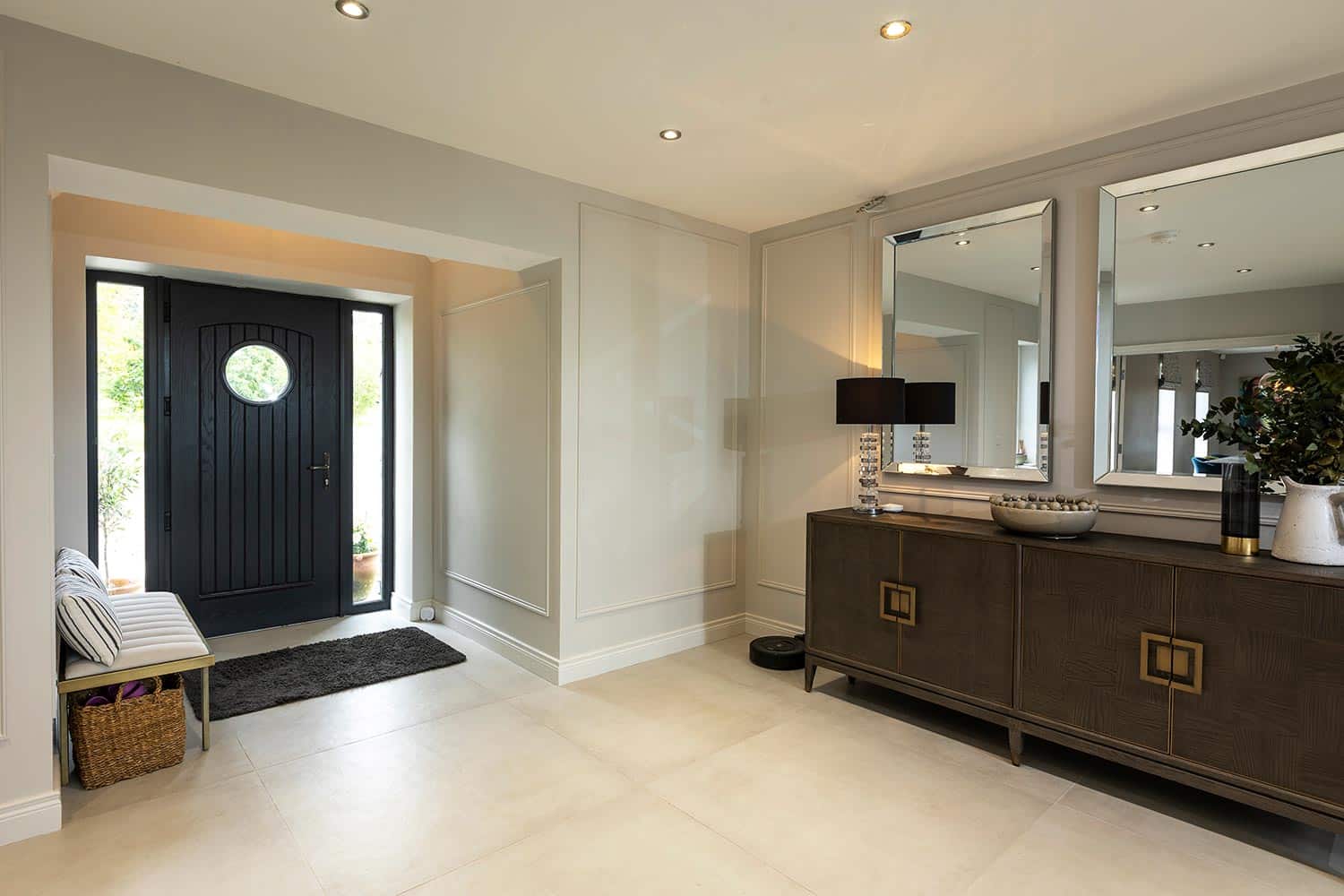
“We were presented with choices regarding heating systems, the building structure (timber frame or blockwork) and various other aspects. The builder assured us he would construct the house according to our preferences. We deliberated on whether to opt for a concrete first floor or timber joists, but we chose timber ultimately. Having small children, for me, it was more reassuring to be able to hear them moving around upstairs.”
Discussions also revolved around purchasing steelwork. “The spaces are quite large and open plan so we needed steels for structural support downstairs, so there were discussions about where to put them and how they would work.”
Bright ideas
The house boasts unique architectural elements, including stunning windows that allow natural light to permeate different areas. The hall window in the stairwell and the sunroom’s vast double height windows create a bright, airy space welcoming the sun throughout the day.
To maximise the efficiency of the downstairs underfloor heating, they chose a 100mm floor screed. “This allows for a faster heat up time compared to standard concrete,” explains Anita.
Drawing from Anita’s design background, envisioning their living space was a process. “We started with a large U shaped sofa in the lounge, eventually defining our interior style around it. Our kitchen, a blend of classic and modern, features a blue island, granite worktops, off white units, a brick front pantry and a striking smoky glass splashback.”
“When the girls were smaller I could see them reflected in the splashback, so I could keep my eyes on them. The whole open plan design means I can have a conversation with them while cooking – so neither the food nor the children get neglected.”
“Designing lighting for a larger space was challenging. We came from an average semi detached house with simple pendant ceiling lights, so we wanted to give this a lot of consideration; we wanted to get it right.”
“The kitchen hosts spots and lighting in glazed cupboards and above the island and dining table, offering flexibility to switch between all, one or no lights.”
As for the bathroom design, it was complex. “We sought advice and found varying designs across different shops, each unique. The baths are substantial, showers spacious, and we’ve chosen different taps in each bathroom—black, gold, and chrome.”
In line with standard regulations, they have incorporated insulation for energy efficiency – spray foam and fibreglass. “Upstairs is so cosy, we don’t need to put the heating on for most of the winter. Although we wanted more energy efficient solutions, we had to consider costs at the time.”
Bombshell
However, with the house almost complete, the Joneses were delivered a bombshell. “Everything was going according to plan, or so we thought,” says Anita. “We paid our contractor with the funds from our third mortgage drawdown, but then a few days later, we got a call from our plumber who told us
that the contractor’s firm had gone bust that day.”
“When the contractor confirmed bankruptcy, we faced a pivotal moment. Creditors began calling for payments we assumed had been already fulfilled.”
“We were left in a financial void, unable to secure more funds from the mortgage company, as they had just disbursed the payment. With no front door, back door or stairs installed there was no way our bank would release another drawdown. We were trapped between needing the final payment to finish the house and the mortgage company withholding it until the build was complete and signed off.”
Stuck in this quandary, Anita and Mark improvised. “A family friend, an electrician by trade, stepped in, and we transformed into self-builders. Using his industry contacts, we managed to start organising crucial on site tasks. However, we had to pay for the stairs a second time as they were withheld by the previous contractor.”
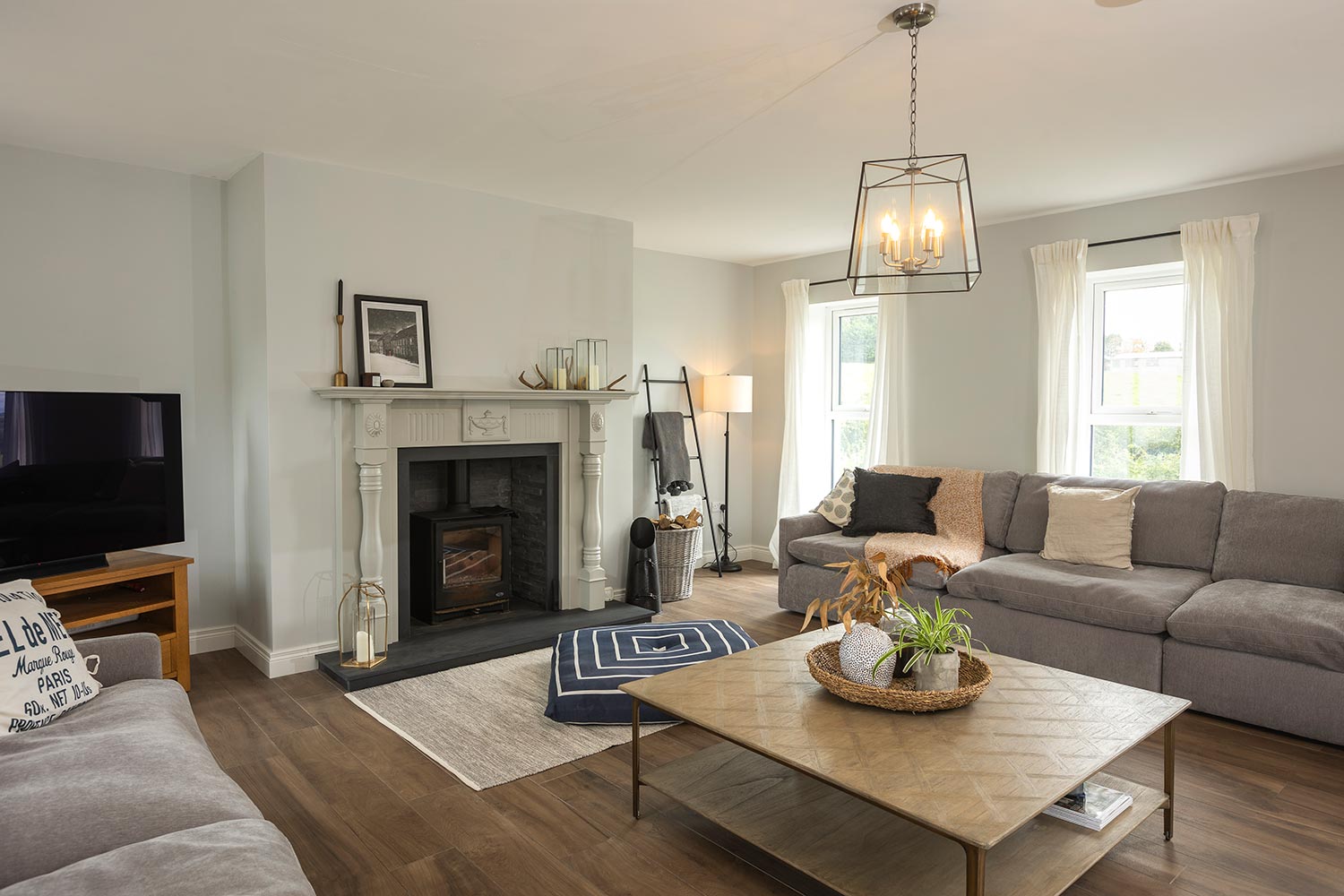
“We faced another delay in getting further building work done due to the fact we didn’t have the NHBC certificate – a warranty. We had applied for it at the very beginning. We handed over £3,500 to the original builder who said he would take care of the process, but he never applied for it.”
“When I tried to find someone who would take over the build following the bankruptcy the first thing they asked for was the certificate, because that will stand over the work that previously had been carried out. It also meant our mortgage wouldn’t be signed off, so we paid a fee for a retrospective house guarantee.”
“There were a couple of months when we had a house that nobody could live in, and which we couldn’t finish because we didn’t have the money.”
With a house incomplete and finances tight, Anita took on the challenges of project managing. “I took on tasks myself, such as finishing laying the loft insulation, tiling and painting the hallway. With the help of our friends and family, we finally were able to finish the work, move in and the final mortgage funds were released.”
“When we started the whole self-build journey, we thought it was going to be fairly straightforward. We employed a recommended builder, we were happy with his work, and then, out of the blue, it all went wrong. But I want people to know that it’s still doable.”
“My husband has absolutely zero experience of any of this. I have an interest in it, but it doesn’t mean I know what I’m doing. But you just plod along and ask the right questions. Call the experts and ask, ‘Can we do this?’ ‘Can you come and help us?’ ‘How much for?’ and you figure it out as you go along. If we can do it, anyone can.”
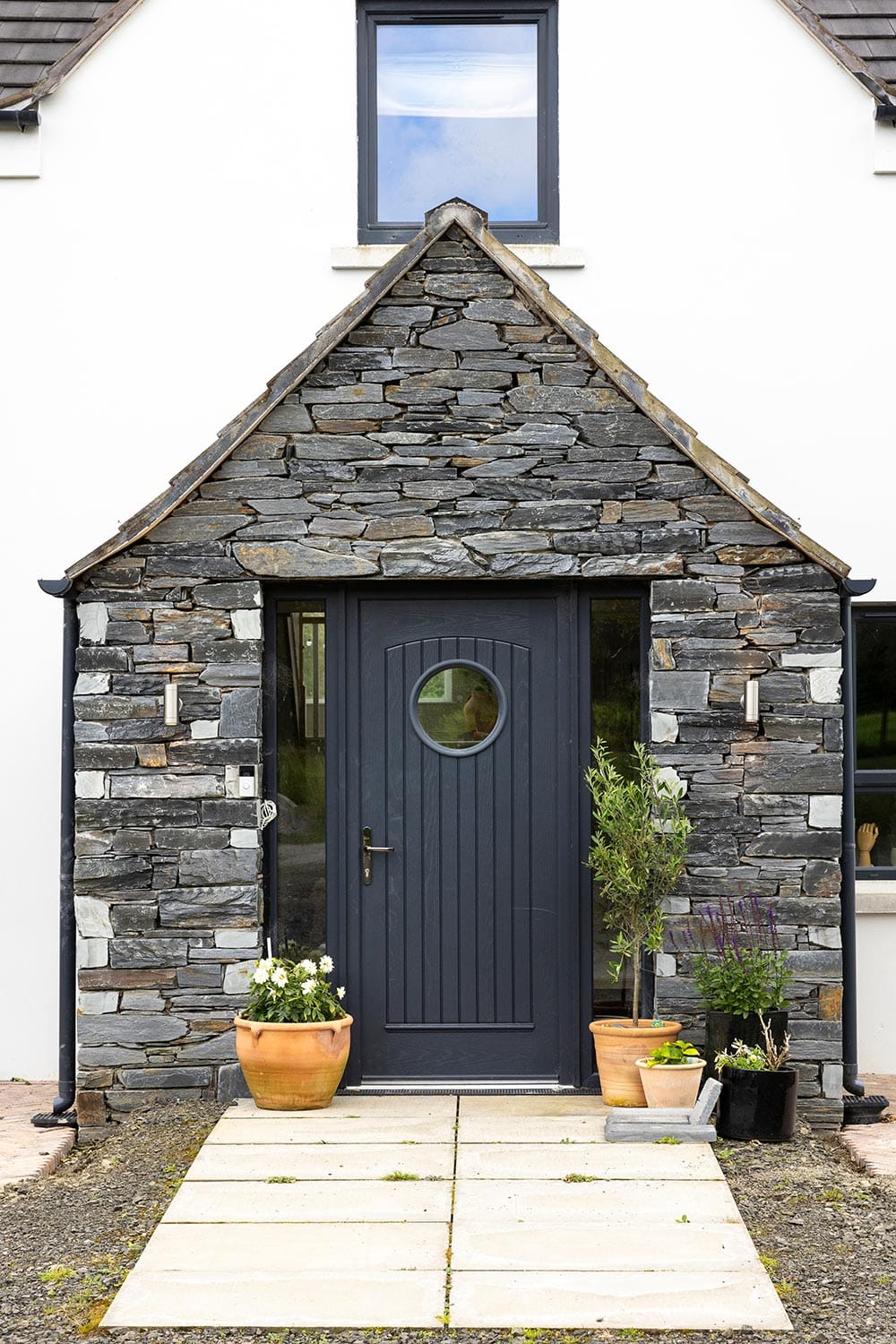
So how is the house working for them? “We’re into the swing of things now, and the house works really well for us. We’re still figuring out certain decorative choices, but the bulk of it is done. I still have some bare plaster in the hall upstairs landing and a ceiling somewhere, but I’m doing it myself, and that’s fine. I will paint it when I have time to paint it.”
“I visited a house recently; the kitchen had just been painted by a decorator. I was, maybe wrongly, looking a bit too close at the finish and I could see that there was paint down the side of the kitchen cupboard. I thought I could make that mistake, for free. I don’t need to pay someone else to do that.”
“What’s the worst thing that can happen? There’s not much you can’t take on yourself when you have to.”
Follow Anita & Marks Journey on Instagram: Insidenumber.77
Tips
Do your research and don’t be afraid to ask for advice.
Read magazines and speak to the right people to get advice. Suppliers and tradesmen will each have a take on things, so speak to everyone and anyone who has expertise in what you need at that point in time.
Go with your gut.
Friends and family like to get involved and they’ll say ‘You should have this’ or ‘You should have that’. But you’ve got to go with your gut feeling on it, don’t just follow the trend if you’re not feeling it. You’ve got to just stay true to your vision, design and what you like. There were many ways we could have changed the design to modernise it, but it wouldn’t have been the right home for us.
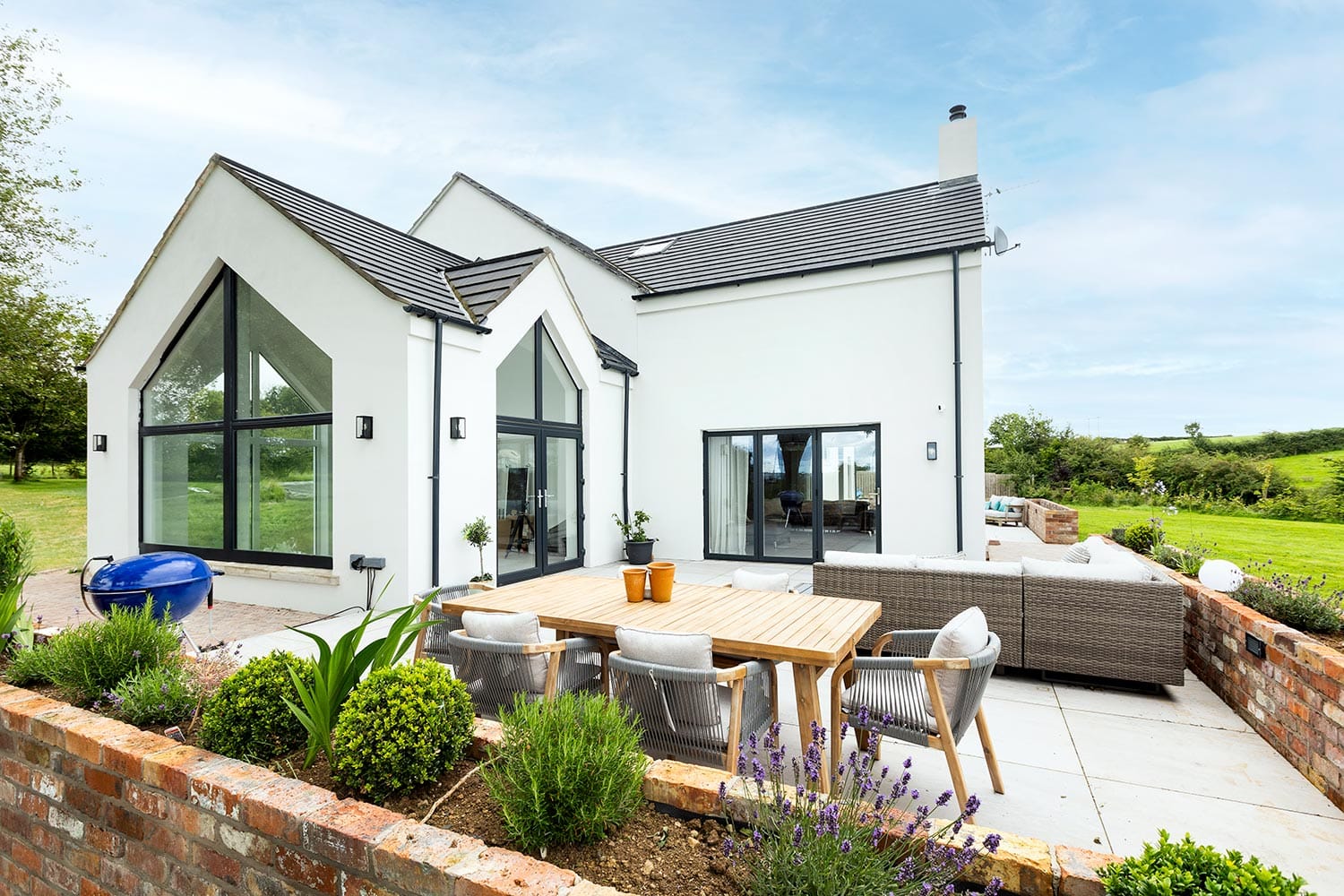
Q&A with Anita
What is your favourite design feature?
I love our entrance hall, it’s spacious and bright and has an interesting curved wall. It’s a lovely feeling when you come in the front door. There are still days when I walk around and go: “We’ve done this and we get to live here. It’s great.”
What would you change or do differently?
We were happy with the original plans, but now living in it there are some things I would change. For instance, our upstairs landing extends as a long corridor with a lightwell. In retrospect, extending the ceiling to create a double height landing might have been more aesthetically pleasing than having the current lightwell. The layout of our daughters’ bedrooms and playroom, specifically, has some logistical challenges. To address fire safety, the playroom needed an additional door leading to one of the bedrooms. Looking back, I’d probably reposition a bathroom to form a more practical Jack and Jill
arrangement.
What surprised you?
I suppose project managing was easier than I expected. When we put the build out to tender, we were told if we led this ourselves, we’d save maybe 40 per cent. We said, no, we wouldn’t trust ourselves, and we wouldn’t know how. But once you have to take it on, you figure it out.
Would you do it again?
I would love to, but I don’t think my husband or children would.
Suppliers
Doors: McIlhattons – Ballymoney
Plumbing: Jameson Plumbing – Derek Jameson 07740980476
Windows: NH Trade Frames Mallusk
Electrician: EMC electrical Ballymena
Bathrooms: Abbey kitchens and bathrooms
Kitchen: Interior 360
Tiling: J&R Keys, Ballymena & Tuscant tiles, Ballymena
Underfloor heating: Jonathan Duff 07595023516
Fireplace: Wilson’s Ballymena
Photographer: Paul Lindsay