In this article Fiona and David chat about their new build project, including:
- How their new build design evolved and how they decided on which eco features to include
- South facing design without overheating
- Details of photovoltaic (PV) installation including costs
- PV self sufficiency and payback times: electricity generated vs used, electricity exported, electricity stored in battery
- Full specification, floor plans, timeline and suppliers’ list
Overview
House size: 2,200 sqft
Plot size: 1 acre
Bedrooms: 5
Build method: blockwork cavity walls (thermal blocks)
Heating: oil boiler, two wood burning stoves
Ventilation: mechanical with heat recovery
EPC (SAP): A (106)
How did the eco new build project come about?
We acquired our own farmland in the early 1990s, but there was no dwelling on it. So we lived in the nearby town. We got thinking about building our own home, and started reading Selfbuild magazine, watched relevant TV programmes, took pictures of any new builds which interested us, and attended every Selfbuild Live event in Belfast.
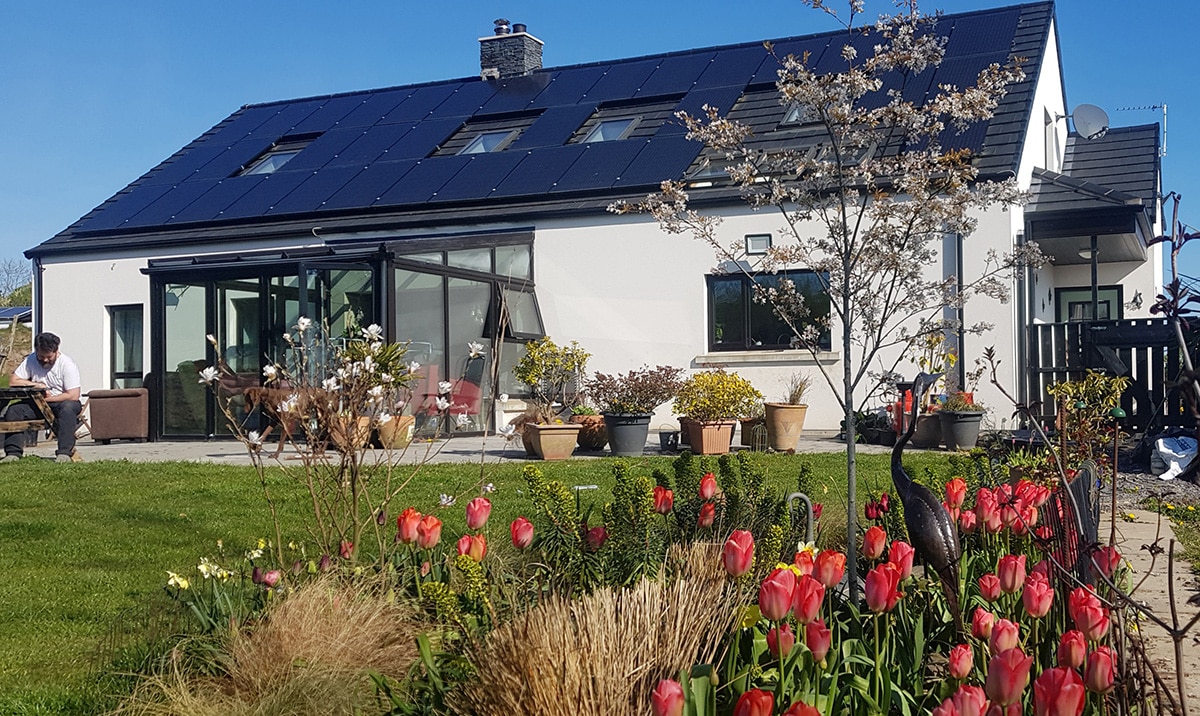
We became somewhat overwhelmed by the amount of information we had gathered, but went ahead and applied, and received approval, for full planning permission.
Then property values collapsed as a result of the recession, resulting in less money becoming available from the sale of our house in the town. We laid the foundations so as not to let the planning lapse even though we knew that the single storey design we’d gotten planning for did not meet our growing family’s needs.
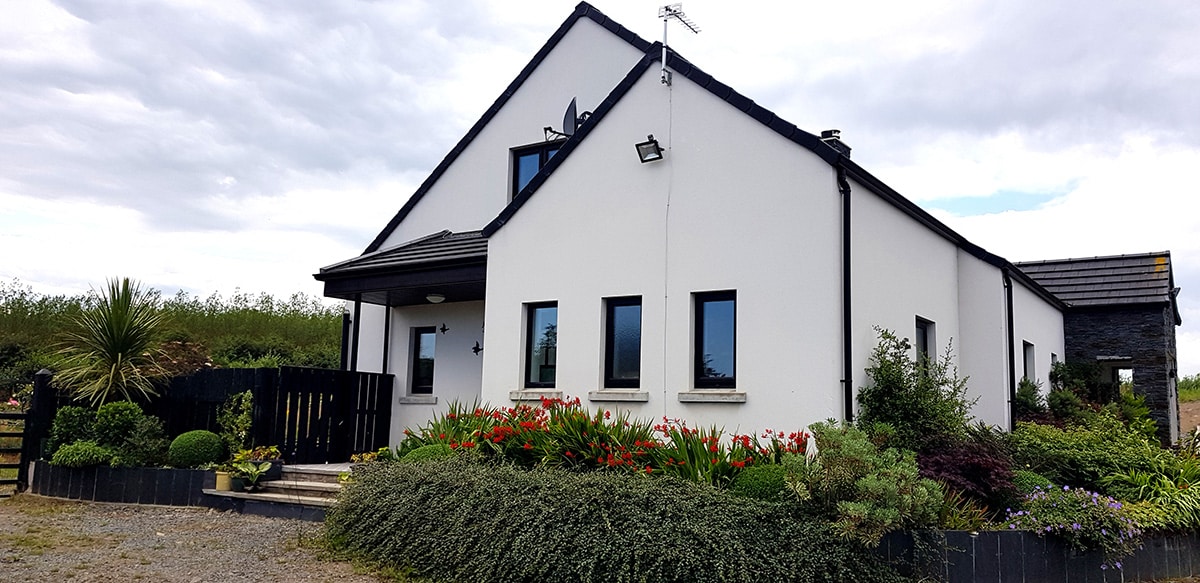
However, we were still determined that we should proceed with the building of our new home and in 2013 attended yet another Selfbuild show, where we had in-depth discussions with a number of architects but none seemed to be singing from our hymn sheet.
That was until we were handed a flyer as we passed a stand, and within a few minutes of reading its contents we went back and spoke to Ronan. Straight away we were impressed with his practical, no nonsense, realistic approach and the fact that he understood what we were looking for, coming from a farming background.
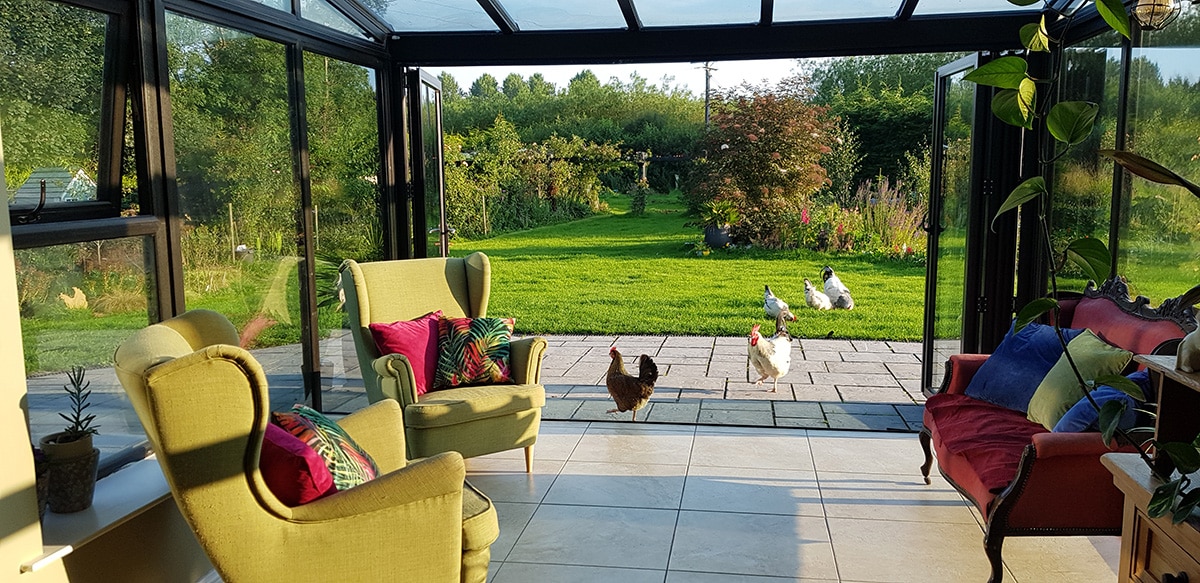
How did the eco new build design evolve?
With Ronan’s help, advice and wealth of experience we reapplied for planning, for a change of design, using part of those previous foundations. This time round we got approval for a one and a half storey dwelling, which had a positive effect on build costs and also the design was one which better suited our needs.
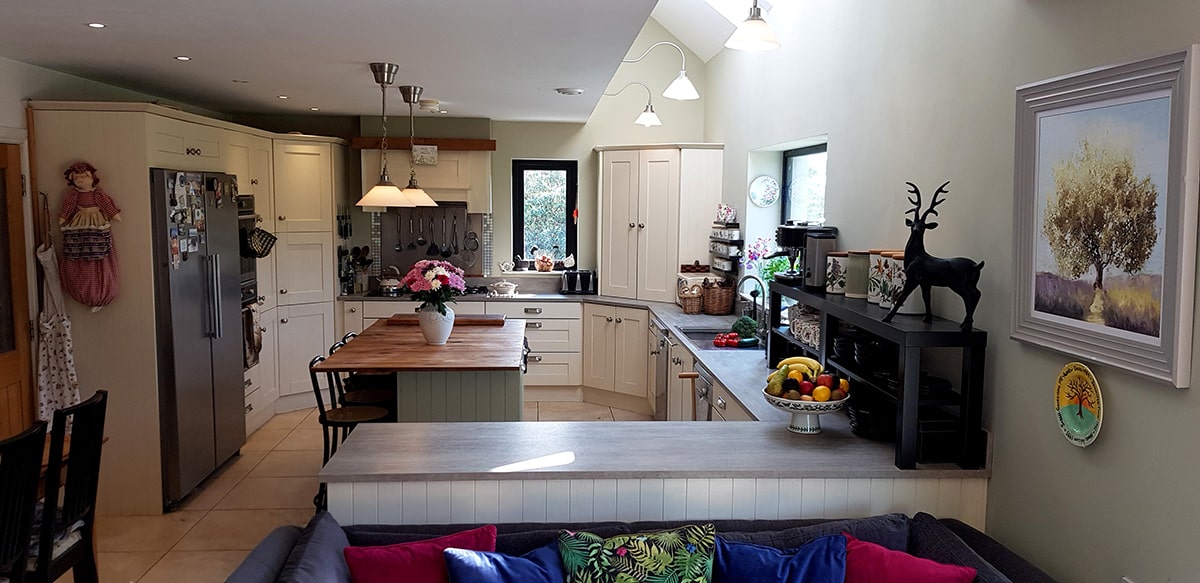
We learned from the negative aspects of our previous home. We wanted a bright east and south-facing combined kitchen and living room area big enough for all the family to spend the major part of the day together.
We wanted the luxury of a large second reception room where we could entertain visitors or watch television in a quiet, undisturbed, comfortable environment. A utility room to deal with laundry and more bathroom facilities were also essential. Finally, more than three bedrooms.
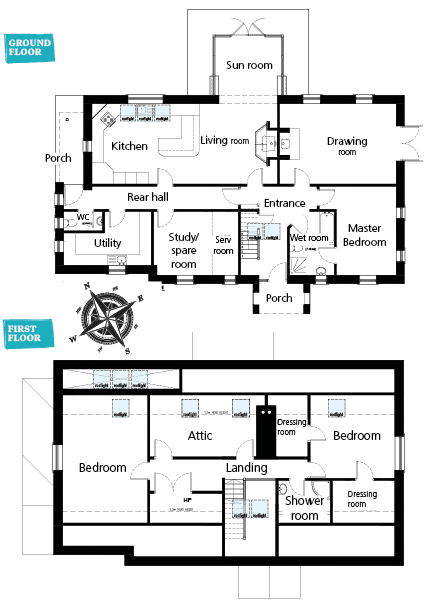
This was to be the only opportunity for us to build so it had to fulfil our needs from the outset. Many hours were spent perusing and tweaking layouts and trying to imagine how they would work in reality.
A hugely important benefit to us was that Ronan has a particular interest in low energy self-builds and this became paramount to our project.
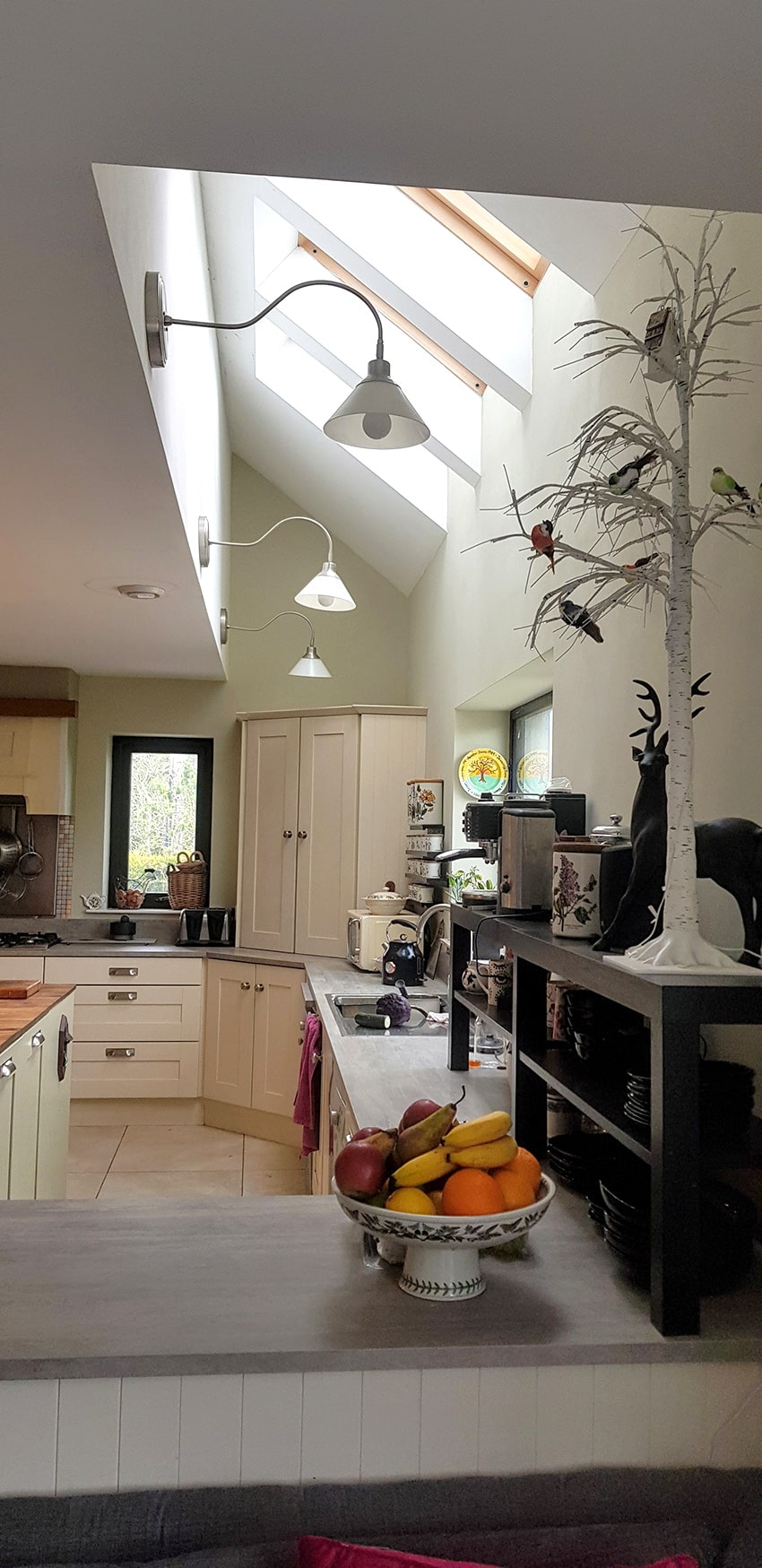
We knew we would be building a house more than twice the size of the one we had in town. This meant we had to focus on reducing our energy costs, but also on environmental issues and for us that meant investigating our options for rainwater harvesting and sewage early on.
The orientation of the house and its position within the site were paramount to making the most of solar gains, or free heating. This coupled with a highly insulated and airtight building would reduce our heating requirements, but we still had the issue of power so we looked into photovoltaics (PV).
On reflection it all worked out ideally in the end. Technology and materials and knowledge of environmental issues had advanced so much in the interim period that we have ended up with a home which is better than we could ever have dreamed of in the past.
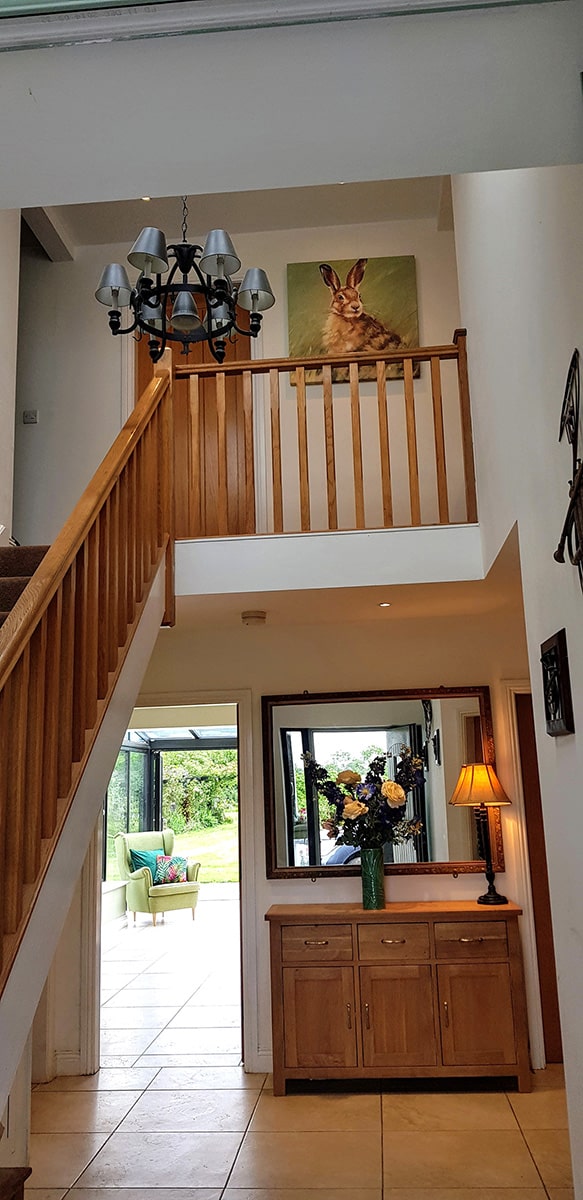
What did you do for heating and hot water?
This is the part of the build which resulted in the most deliberation. From our initial enquiries about burning wood instead of oil, to “save the planet”, and using the then Government backed Renewable Heat Incentive (RHI) scheme, we followed a dead end path, finally abandoning the whole idea. To name a few issues, waste wood (of which we had a plentiful supply) did not qualify, neither did a multifuel stove.
It appeared to us that the scheme did not reward a heat retaining, low energy consuming house but instead subsidised a poorly insulated, high energy consuming one.
The cost of the only approved wood burning stove at £2,500 with an additional £300 required for a heat monitor, and seven year subsidy of £10 a year didn’t make sense. We also calculated that for the equivalent amount of energy per litre from oil, it would cost much more to buy in wood, never mind the extra work and storage involved with anything other than oil.
So we installed an oil fired system that feeds underfloor heating downstairs and radiators upstairs – after five years living in the house the radiators have barely been used and with hindsight, we didn’t actually need to install them. We also have a multifuel stove in each of the two reception rooms.
We have used the stoves mostly to create a feature focal point but last winter in particular (2020/2021) we made a point of lighting the slightly larger living room one more often in the dead of winter. We burned our waste wood which significantly reduced our consumption of oil from an average of 900 litres per year to 500. We have not had a delivery of oil since December 2019.
If we were building today, we probably would research an air source heat pump and this could be something we consider in the future as a replacement to our oil boiler once it nears end of life.
In reality, even on a sunny day mid-winter, the temperature in our glass room and living / kitchen area increases so much (23 to 26 degC) that we keep internal doors open to let heat out to the rest of the house, and this heat is then circulated around by means of the mechanical ventilation system with heat recovery.
Tell us about your PV system
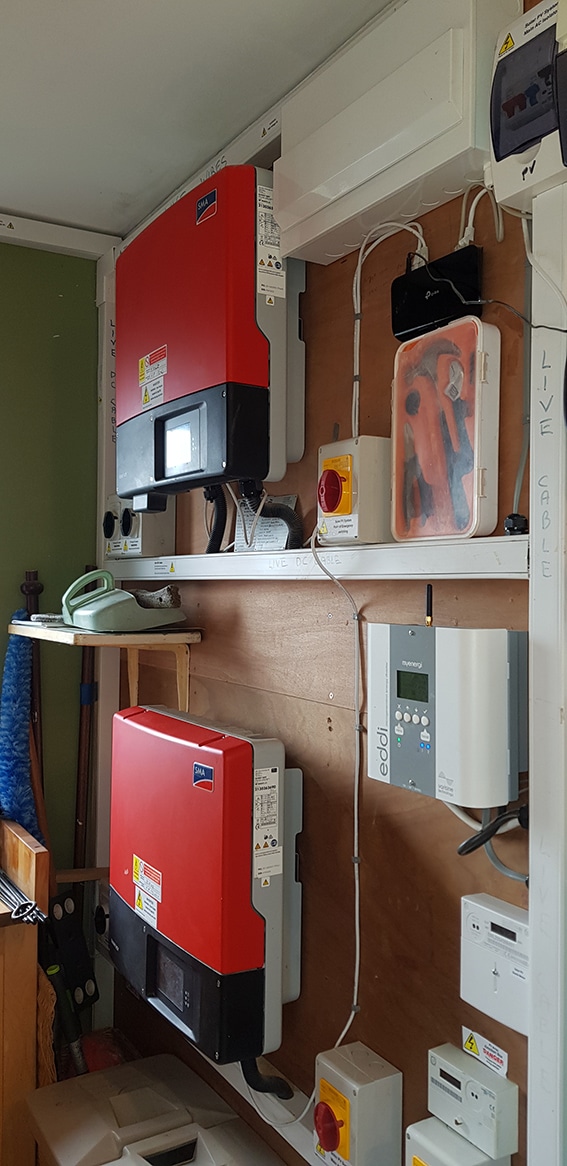
Application process: The network operator NIE would not progress an application for greater than 4kW (16 panels) without planning approval already in place. Following a hastily arranged on-site meeting with the planners, they granted permission for the maximum number of panels which would physically fit on our roof (36), enabling the NIE process to restart.
System size: 9kW in the form of 36 panels on the roof.
Orientation: South facing, 42 degree angle, free from any shadowing obstructions, all of which help maximise PV production.
Cost of system: Installation cost of £10,000 for the 9kW system, a payback period of five years based on ROCs and feed in tariff.
ROCS: When installed in 2015, the panels qualified for the Renewable Obligation Certificate (ROC) scheme (no longer available), earning £1,500 in ROC payments each year.
Feed in tariff: On average we sell back £500/yr to the grid. The current cost of electricity in NI is approximately 17p/kWh purchased from the grid, and we receive 5.1p/kWh for the export tariff so to maximise the benefit from the solar panels it pays to use the power you generate.
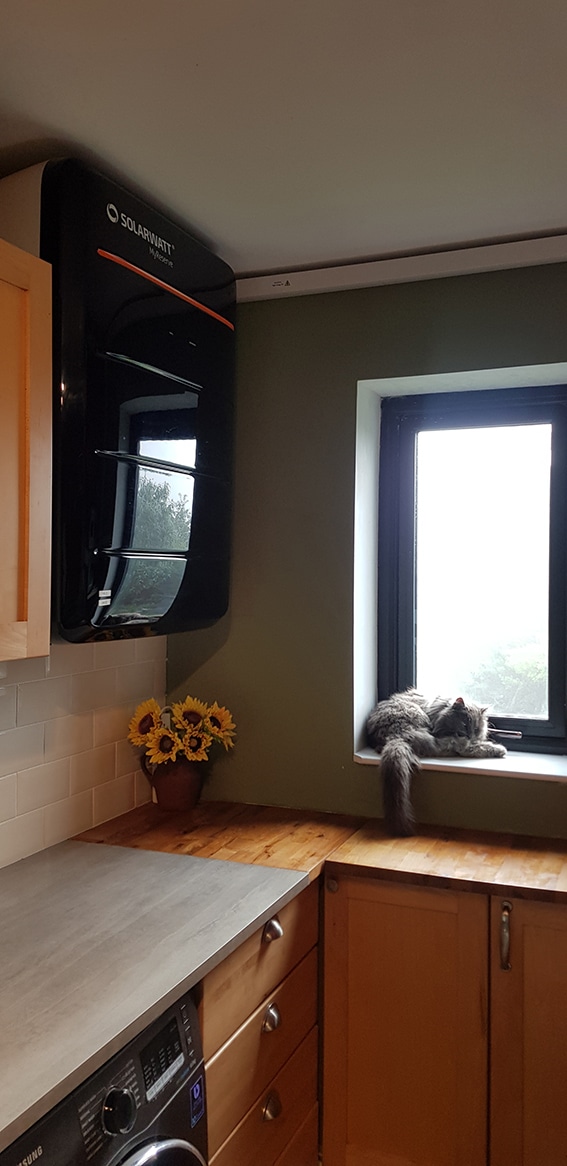
Battery: The 4.6kW battery cost £3,700 to install in 2020; naturally this reduced the amount of electricity being sold back to the grid. The battery has priority over the water heating but if there is sufficient electricity being produced the battery sensor will allow water to be heated simultaneously to it being charged. Any surplus to that feeds into the grid.
Electricity costs: In 2020, a year when we had five residents, three of whom were adults working full time from home, our bill including standing charge was £308 for the year and the income from the power exported was £276 so effectively our net electricity bill for the year was £32. We did shop around to get the best tariff.
We also run the washing machine and dishwasher only when there is surplus electricity being generated and even cook on our electric hob during that time. It was a conscious decision to have both gas and electric hobs, to be able to cook during any power cut.
Self-sufficiency: On long sunny days we can live totally independently from the grid thanks to the battery. Without the battery, 45 per cent of our annual consumption of 5,300KWh electricity would have been from the PV panels.
Even though our panels produced 1.7 times more than what we consumed over the past year, we still had to purchase 1,890 kWh from the grid. This was owing to the fact you still use electricity when the sun doesn’t shine or when the draw for electricity is higher than the production at any given time.
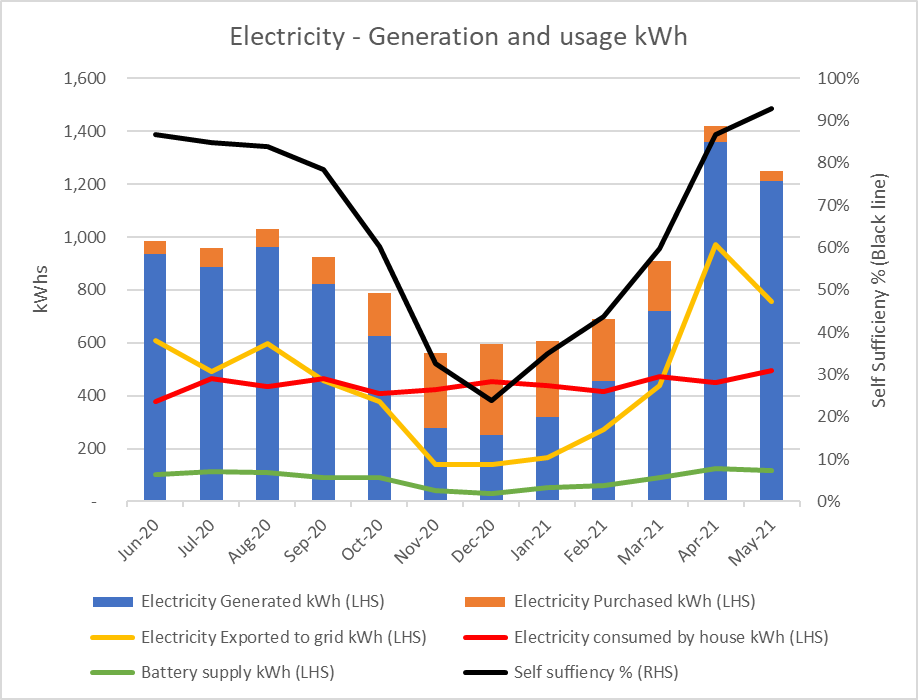
What did you do for water and sewage?
For wastewater, we selected an air-vented sewage treatment system which is environmentally friendly, has no moving parts to wear out or go wrong and is not powered by electricity. This complied with our aim to keep maintenance and costs to a minimum. We were in the fortunate position to be able to install it ourselves to the given specification, and we have found that it works well.
It made no sense to us to be using treated water needlessly for flushing toilets, watering gardens etc., so we harvest and store all rainwater from our roof. In times of drought, we top it up from an old farm well.
This water is used to flush all three toilets, to water the garden, and to power wash paving and vehicles. David designed and installed the rainwater storage system himself whereby all roof water is harvested via a network of underground pipes to the underground storage tank near the house.
There is a second storage tank at a higher level, uphill from the house, to which water is pumped from the lower tank from time to time, as necessary. This means that the harvested water to the house is gravity-fed. On average we use 1,000 litres per week from this system for up to six adults.
We found that the geology of our land is suitable for a borehole, which should cost £3k to drill and install. This will allow us to get below or within rock, to access a plentiful supply of drinking water. In light of climate change, and with increasing frequency of restrictions to public water supply recently publicised, this is likely to be our next project to augment the off grid benefits of our home.
Eco new build on a budget in Co Down Suppliers
Architectural design and supervision
Ronan at FMK Architecture, fmkni.com
Builder
Moyle Construction from Ballymoney
Co Antrim
PV panels
Next Gen Power, Bangor;
power diverter: Eddi
Windows, external doors and glass room
Swish Windows, Cookstown
Render
K-rend, k-rend.co.uk
Thermal blocks
Mannok, mannokbuild.com
Wastewater treatment system
Biorock, biorock.ie
Electricity supplier
Budget Energy, budgetenergy.co.uk
Insulation
Roof: Rockwool, Floor: Kingspan
Kitchen
Supplied and fitted by Trevor Parker at Extended Living
Airtightness system
Including tapes for windows, doors, openings & ceiling membrane, with 50mm service void; (Ampack) supplied by ecohomesstore.co.uk
Ventilation
The Mechnical Ventilation with Heat Recovery unit is a Vent Axia Kinetic Plus B, 90 per cent efficiency
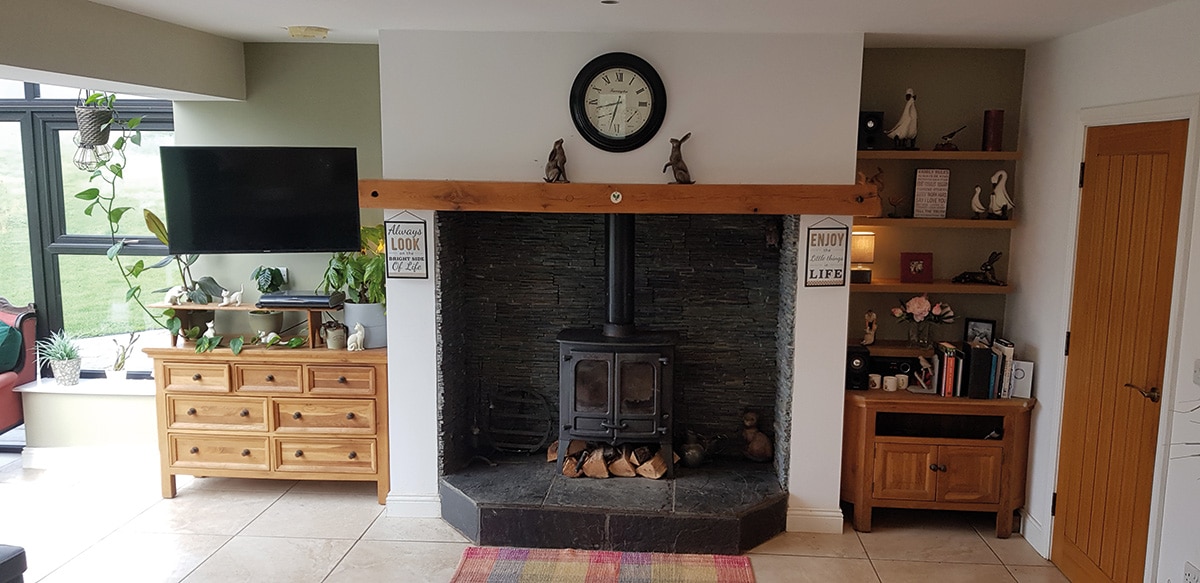
SPEC
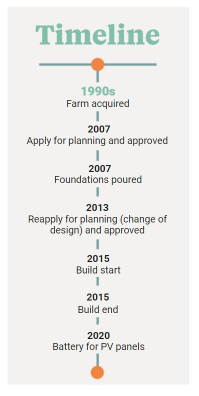
Walls: 8 inch cavity wall constructed of 100mm thermal concrete blocks externally and 100mm thermal blocks internally, 200mm cavity filled with graphite EPS beads. Wall ties of insulated plastic to prevent cold bridging. U-value 0.15W/sqmK
Roof: trusses are not built into the concrete walls but rest on a wooden plinth to reduce heat loss. Flat ceiling section (area above the ceiling of the first floor) filled with up to 550mm of rock wool insulation, U-value 0.08W/sqmK. Sloped areas of the ceiling to either side of the first floor rooms has 150mm glass wool insulation between rafters plus 50mm PIR board to underside, U-value 0.16W/sqmK. Black concrete tile covering.
Floor: concrete precast hollowcore units for the ground floor on which 150mm of phenolic board insulation supported the layout of the network of underfloor heating pipes, over which the liquid floor screed was poured. U-value 0.11W/sqmK
Glazing: all windows including rooflights and glass room are triple glazed.