In this article we cover:
- Why the house is costing €250k instead of the €480k bank estimate
- Navigating a difficult mortgage process
- Background to the project and choosing to DIY build the house
- Project supervision choices
- Insurance and living arrangements
- Setting up the site to work on
- Water and electricity connections
- Where they made savings on materials and labour
- The DIY timber frame method they used
- Timeline up to September 2024
- Foundation design
- Floorplans and supplier list
- Progress build photos
Contents
Background
We were fortunate to receive the site as a wedding gift. Three years ago, we approached my father-in law who had some land, and asked if he had any spots where we could build. We went for a walk, found this location, and he generously said, ‘It’s yours if you want it.’
After that my wife and I designed the house on autoCAD, and we hired a local architectural designer, John. Pattinson, and told him exactly what we wanted.
House size: 220 sqm
Bedrooms: 2 and office/spare room
Site size: 1 acre
Provisional BER: A
Budget (all in): €250k
Heating system: Electric towel rails in the bathrooms
Ventilation: Heat recovery ventilation system
Build method: Stick build (timber frame)
The house is a decent size but the design is very simple. It’s a vernacular layout with a cottage side, and a ‘shed’ attached via a flat roof area, around a U-shaped courtyard. This traditional farmhouse
design likely helped us secure planning permission more easily. We were fortunate that the process took only four and half months.
It’s traditional in that it has a shed, which will be cladded with standing seam metal – on both the walls and roof. The cottage side features a natural slate roof, and the walls are finished with cement boards
rendered with lime plaster. No concrete blocks are used in this low energy build.
Project supervision
We worked with the architectural designer until we secured planning permission. As we are building everything ourselves, we decided to work with a structural engineer directly for the construction
phase.
I was lucky to have met and worked with Conor Keane on a church restoration project a few years ago. We have very similar ideas and views on timber framing construction.
Conor and I did the construction drawing details on CAD and Conor did the calculations to confirm the structural stability of the design.
Then Vanessa and I filed the commencement notice, we opted out of assigning an ‘Assigned Certifier’, assigning ourselves as both owners and builders. That meant taking total responsibility for the construction.
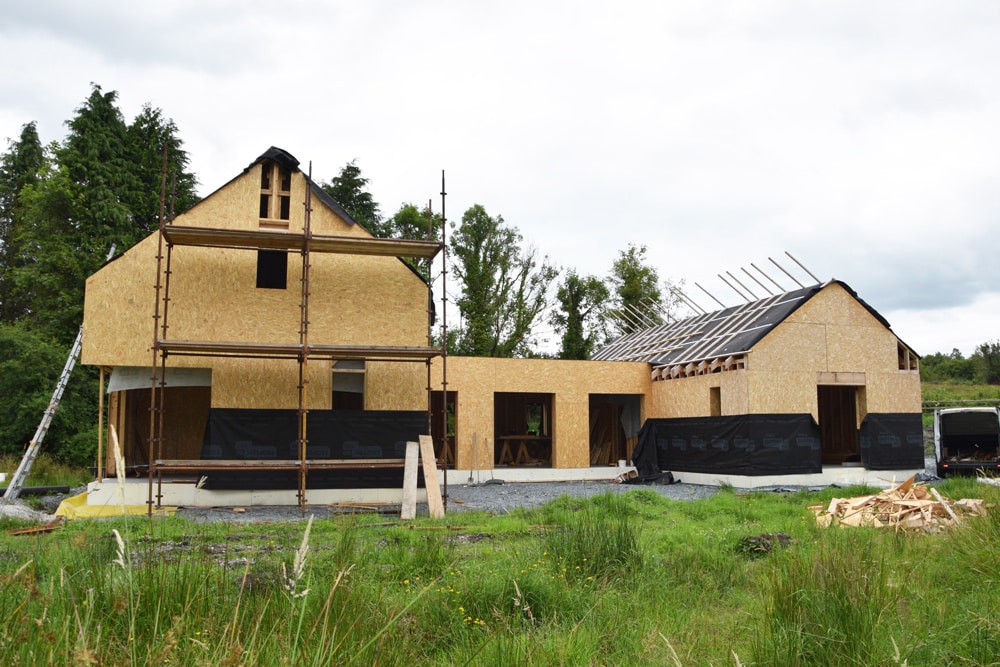
“Self-building is a great way to save on money, as labour usually accounts for 40 per cent of the total cost of a house build.”
The engineer is signing off on the building stages for the bank; the first stage was prior to pouring the concrete slab for the foundations then the next stage was checking the structural timber frame integrity.
Then the next check will be before closing the walls with the vapour barrier to ensure all the bracing is in place. After that the final check for structural integrity will be when the building is weathertight.
For the foundations, we used a floating slab, meaning the house is sitting on insulation. The engineer did the calculations for the foundation’s reinforcement steel and placement of it, and I just followed his details.
Insurance and living arrangements
We opted for self-build insurance, primarily because it was required for our mortgage. But it’s reassuring to have coverage to rebuild the house at market value in case of an accident.
We recommend shopping around for insurance, as fees can vary significantly between brokers.
Also, ensure that all contractors have public liability insurance before starting work on site, as
this is necessary for your insurance to cover any accidents.
We are renting at the moment, about seven minutes away by car from the site, so in a way the
quicker we build the better.
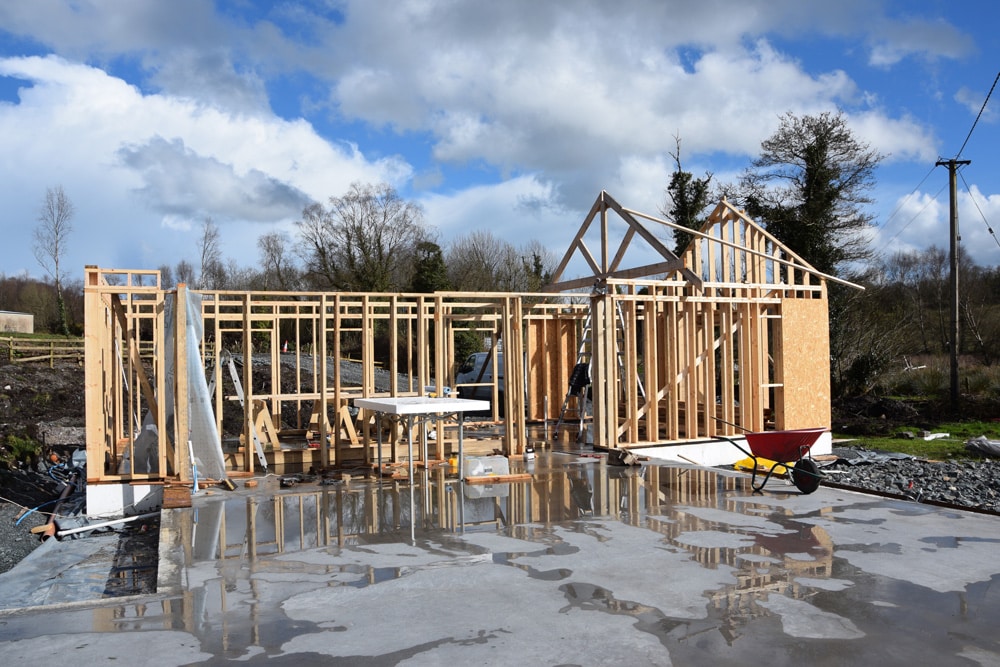
Setting up the site to work on
Luckily my workshop is 50 metres from the site so we stored all materials there. Vanessa’s studio
is next door to my workshop so that is the site office and canteen.
We own a digger and have it on site, so we just had to hire a little dumper truck and a roller for
the foundations stage. We also put down about 360 tonnes of stone, to create a driveway and also to level up the ground. We put up construction signs and the site already had wooden fences. We are
planning on installing the gate very soon.
To deal with waste, I take regular trips to the skip nearby with the van for plastic and polystyrene. And we give the offcuts of wood to family and friends to burn in their stoves.
The construction is low in height for the cottage side, and we are building from the inside. We added scaffolding for roofing and cladding on the shed side.
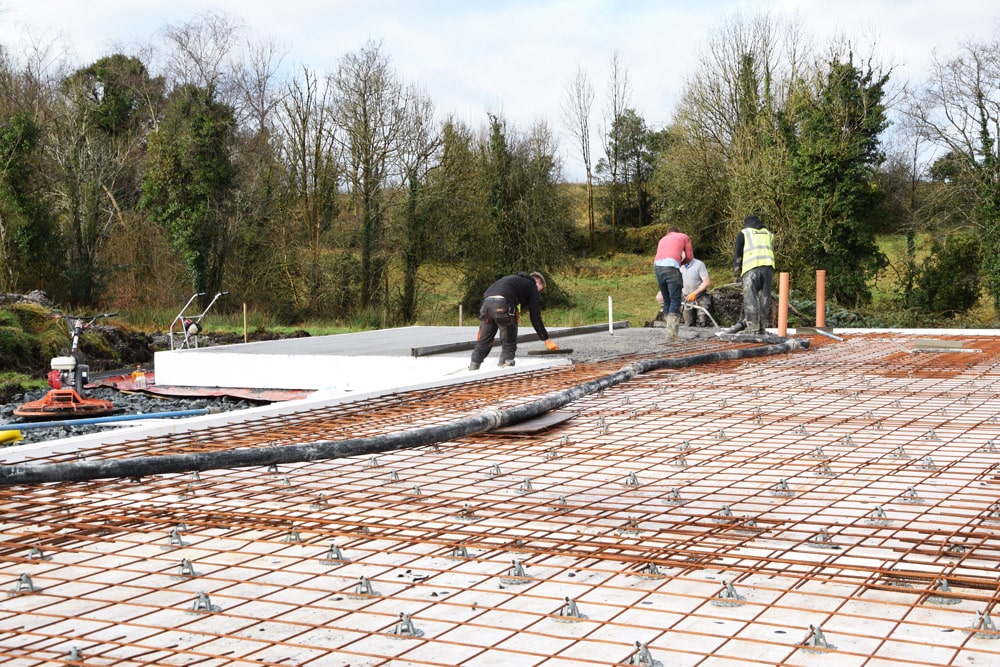
To build the two-storey portion of the house, the ‘shed’ side, we went at it in stages.
As we are working from the inside, we built the downstairs walls initially, followed by the first floor and finally we assembled and lifted the gable ends from the first floor.
We used a winch system attached to the floor, wherever we needed to lift any heavy wall sections, avoiding the need to hire a crane.
Tricky mortgage
We had some savings which meant we had enough money to buy materials and seal the building, enough to create the shell. However we didn’t have enough to finish the house to move in.
Since we were building the house ourselves and are both self-employed, and because the
project cost much less than the bank anticipated, it took us almost a year from when we first applied to when we drew down the first instalment.
By doing it ourselves our budget is €250k in total; which includes solar panels and quality products for a well insulated house. Again, we were lucky to not have to buy the site.
According to the bank the same house should have cost us €487k to build, based on a standardised cost per square metre from the Society of Chartered Surveyors Ireland.
We had to explain to the bank how we were saving so much. Our engineer was very good at
explaining and detailing the process, and the reasons why this build was different.
With my 30 years of experience in woodwork, we had to demonstrate exactly how the work would be done. It took a long time for them to process our application, and we had to resubmit multiple documents, but we got there in the end.
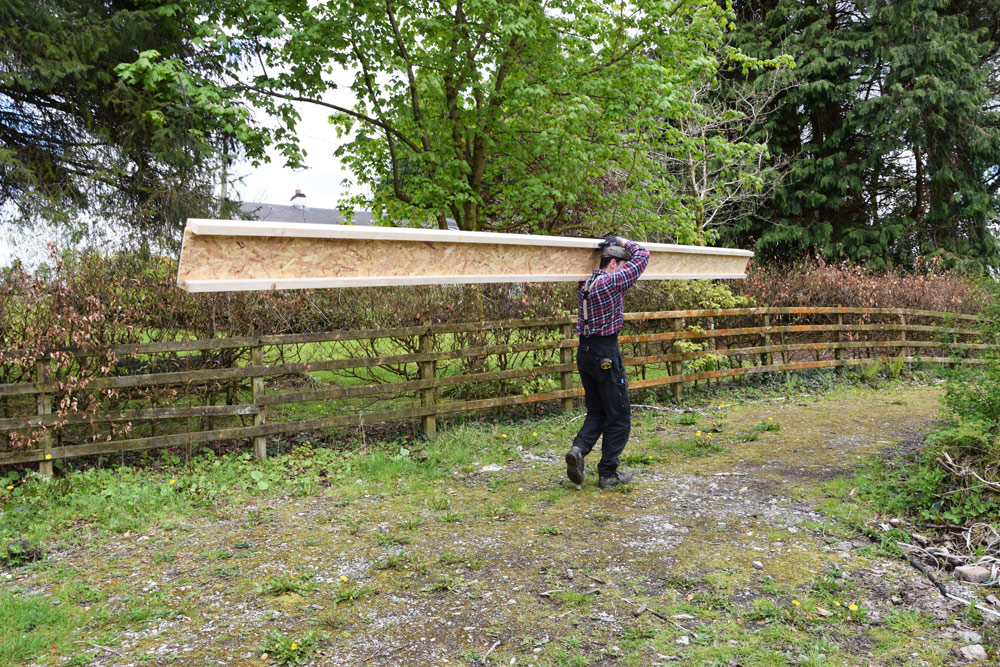
Water and electricity
The water connection process was straightforward enough. We had to bring up a water mains pipe to the side of the road to where we wanted the water meter installed. We also had to send them a photo
of the pipe in the ground to confirm the position of the pipe.
We then applied to get the water connection fee waived and were successful. There were several documents we had to supply for this but we had it all from the mortgage application, so it was easy.
Documents to supply included things like planning permission, commencement notice, etc.
The electricity was on site already, and we applied to get the line moved, as it was obstructing the shed side of the house. So we met an ESB Networks engineer on site and discussed the various options for
moving the line. The engineer recommended installing five new posts further down the site. We applied online for our electricity connection on the ESB Networks website. We had to supply the folio number and exact site coordinates of the site as we did not have an Eircode yet. We paid upfront for the
connection.
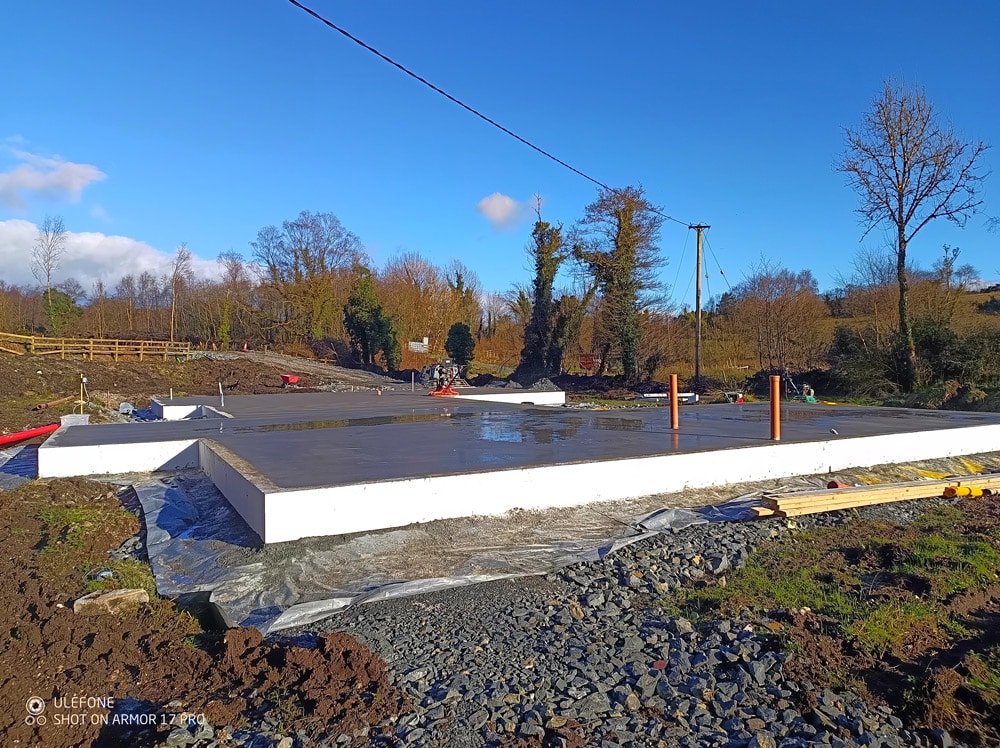
Savings on labour and materials
By doing it all myself in timber frame, there is a big saving on the construction cost. It made sense financially for me to take on the project and stop taking on client work.
Building a passive house is demanding, and if you’re not in a position to do it yourself, there are ways to reduce labour costs by handling some tasks on your own. For instance, taping the vapour barrier is a task that requires more time than skill and can be done independently.
Another way we saved money was by importing materials from mainland Europe, which allowed us to get the same products for half the price.
For example, we sourced our windows from a company in Poland that also has fitters in Ireland. To avoid delays, I ordered the windows immediately based on my measurements. I knew that if the
windows ended up being the wrong size, I could adjust the timber frame easily. Fortunately,
everything fit perfectly and there were no unexpected issues.
I ordered the roof slates from France with just a phone call and arranged for a courier. I know a truck driver who regularly travels between France and Ireland, so he picked up the three pallets on his way. The delivery cost me €600, but even with the transport fee, it was still cheaper than buying them in Ireland.
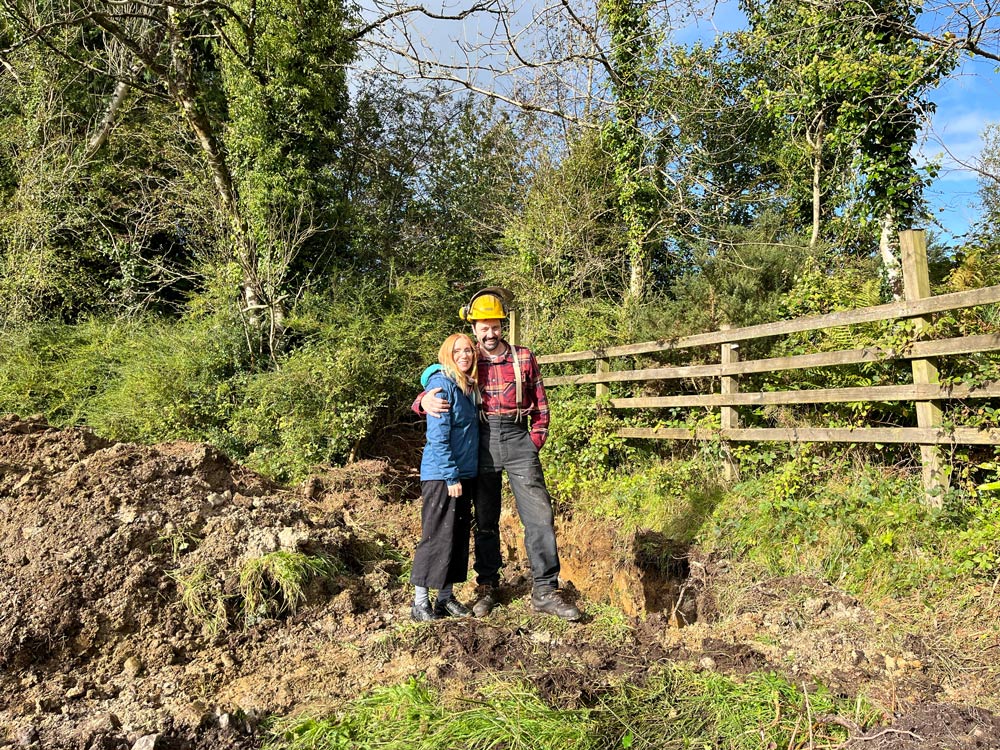
For the timber, I shopped around a lot. And it turned out our local builder’s merchant in Drumshanbo, Leitrim, was very competitive. I usually deal with a much larger timber supplier but they turned out to be the most expensive. Timber is still way more expensive than it was a few years ago but it has come
down in price a bit. Plywood is still quite high.
By purchasing most of the materials at once, i.e. timber, mesh for the foundations, waste pipes, and more, we spent around €24k.
Even with years of experience, I still underestimated the quantity of some materials, like the number
of nails needed. I would advise using a quantity surveyor to avoid any surprises.
A day in the life…
A typical day for me is to drop my daughter to school and be on site for about 9am. I stay until 6pm; I’m too tired to stay any later than that. My van broke down, I’ve had no van for a month, so I’ve had to carry all the wood from the workshop 50 metres uphill. Timber, sheets, all by hand. It’s an extra challenge. I wouldn’t recommend it
DIY timber frame method
We are physically building the house ourselves; it’s all timber frame. We will have double stud walls pumped with cellulose insulation.
We are using C16 standard grade timber, and Canadian Standard Lumber (CLS) which is ideal for timber framing because the wood is planed with rounded edges. It’s also a better grade in terms of fireproofing.
There was hardly any waste or offcuts; this is because we designed the building in multiples of the standard timber length of 2.4m. So all the interior walls are 2.4m high, and the dimensions of the rooms also follow standard sheeting dimensions.
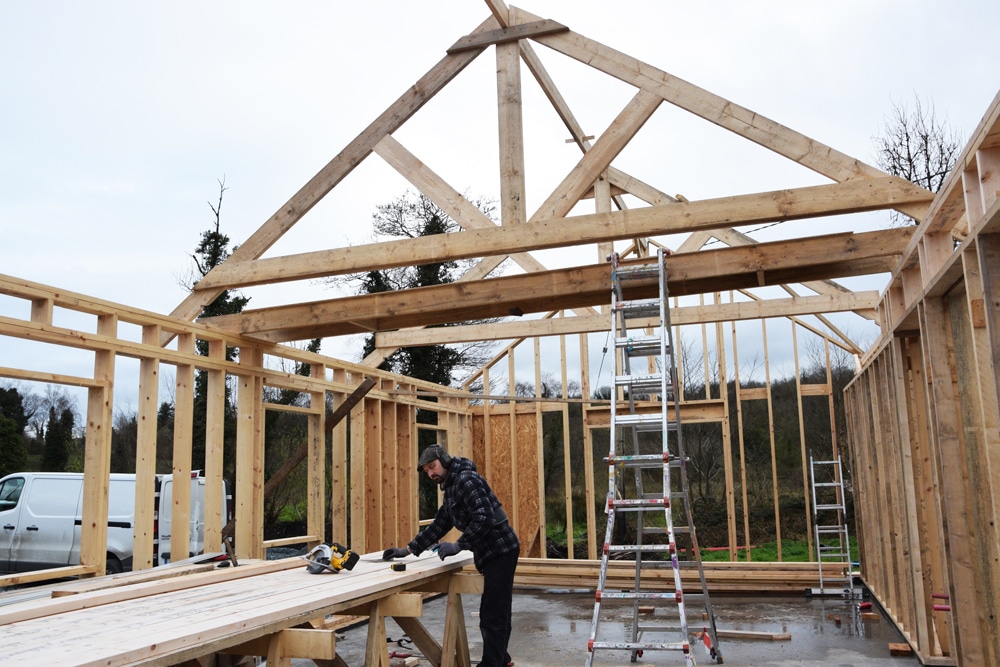
“By doing it ourselves our budget is €250k in total… according to the bank the same house should have cost us €487k to build.”
The walls consist of 6x2s outside and 4x2s inside, braced with half inch OSB sheets. Given the unfavourable weather this year, we wrapped the timber frame as we progressed using a proprietary rain barrier, supplied and designed by a specialist company. We sealed the sections with proprietary tape, ensuring the water and airtightness necessary for a passive house.
We started with the cottage side to quickly create a sheltered space for storing materials and continuing the construction. We built the external leaf of the timber frame first, then braced the whole building with OSB on top of the 6 inch stud walls.
Then the A frames and rafters on the cottage side went up, making the building secure and sturdy and then we covered it with a rain barrier membrane and battens.
Once all the outside timber frame was built up, we tackled the inside 4 inch stud walls. To guarantee continuity in the airtightness layer, we made sure that wherever we were bracing the internal walls and joining them to the external walls, we put a strip of vapour barrier first.
The interior leaf is also load bearing but the building can stand on its own without it. Once all the vapour barrier is in place, and the engineer is happy with the structure, we will pump cellulose insulation through the vapour barrier – cutting a little hole to pump through the insulation and sealing it afterwards with tape.
Once all of the walls are pumped in with cellulose, we will put 2 inch battens on top of the vapour barrier. The battens will create a cavity between the plasterboard and the vapour barrier. Within this gap all of the wiring and plumbing will go. This means the vapour barrier won’t need to be pierced at any stage, as there are no services running behind it.
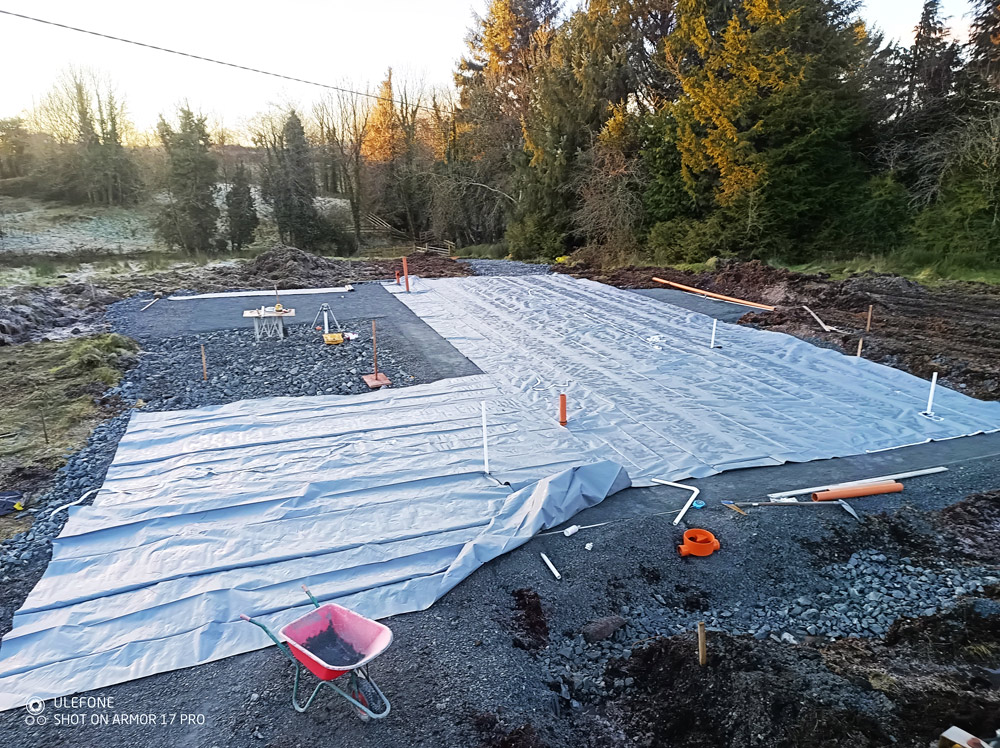
Foundations
We began the groundwork in October 2023. The first task was to drain the land, given the
typical conditions in Leitrim. The soil consists of a thin layer of topsoil over hard blue clay.
Our engineer advised against digging too deeply into the clay to preserve its structure. Instead, we built up the site with compacted layers of small quarry stones (804) to create a level base for the foundations.
At this stage, we also laid all the waste pipes, radon sump, and water mains before installing the radon barrier.
For the foundations, we opted for an insulated system, designed in collaboration with the manufacturer and our structural engineer. The system consists of polystyrene blocks laid directly on the levelled site
to form a mould for the concrete slab.
The blocks were connected using large staples and pegs. The concrete slab, reinforced with two layers of steel mesh (8mm and 10mm), was poured using C35 concrete, as we intend to use the slab as our finished floor. The C35 mix allows the concrete to be floated and polished to a high standard.
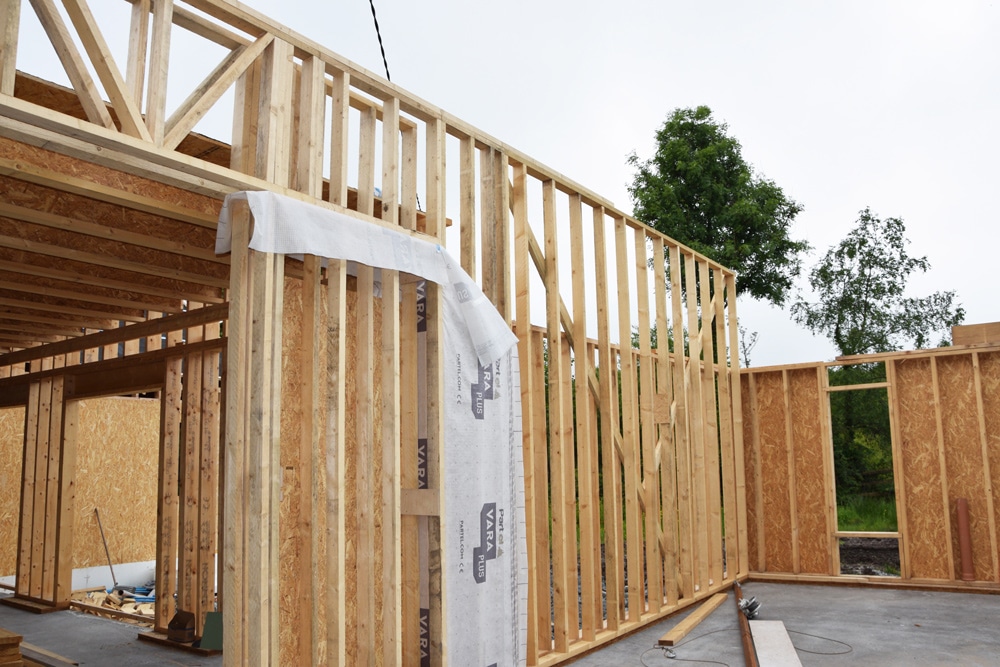
DIY timber build on a budget suppliers
Architect
John Pattinson, ArchEngTech Consulting Ltd, Roscommon
Structural Engineer
Conor Keane, SDS – Civil, Building & Structural Engineers, Mayo
Stone
McWeeney Sand & Gravel, Leitrim
Materials
Including wood, steel mesh, staples, nails, sewage pipes, roof windows, all from Mulveys
Hardware, Drumshanbo, Leitrim
Airtightness products
Rain barrier, vapour barrier and multiseal tape (Exoperm150 rain barrier, Conexo60 tape)
from Partel, Tuam, Galway
Foundations insulation
Kingspan Aeroground
Concrete
B McCaffrey & Sons, Enniskillen
Pouring and polishing concrete
Fineform Concrete, Tyrone
Windows and French doors
Fenbro, Poland
Cellulose insulation
Ecocell, Cork
Small dumper and roller hire
Northwest Tool Hire, Leitrim
Big dumper hire
Reilly Tool Hire, Ballyconnel, Cavan
Mortgage provider
Bank of Ireland