In this article we cover:
- What is second fix?
- Plastering watchpoints
- Visual checklist
- Staircases checklist
- Floor finishes checklist
- Architraves and skiting boards watchpoints
- Painting watchpoints
The first thing to know is that building materials and products which possess differing characteristics in terms of density, surface area and moisture content, etc., will, when fixed or set together, tend to move in relation to each other due to different rates of expansion and contraction.
The most frequent visible outcome is that of plaster cracks, especially at junctions between walls and ceilings and around window and door heads and sills. Plaster cracks up to 2mm are usually permitted. Cracks of up to 4mm may be found between timber stair strings and masonry walls.
The fact that this will almost certainly happen must be accepted and allowances made for remedial work later. Cracks exceeding 5mm in width or any which are believed to be moving
over time should be brought to the attention of the structural engineer.
If installing metal components, dissimilar metals should be isolated from each other where they are joined together. Also be aware that aluminium or its alloys should be kept separate from
cementitious material. Moisture will exacerbate these potential corrosion issues.
Plastering
Before starting, protect already-installed finished fixtures and fittings from spatter during
plastering and later skimming and painting.
External windows and doors and other products may have been supplied in plastic wrap, but if this is missing or damaged, you should fit or repair it yourself using appropriate adhesive tape and polythene sheet.
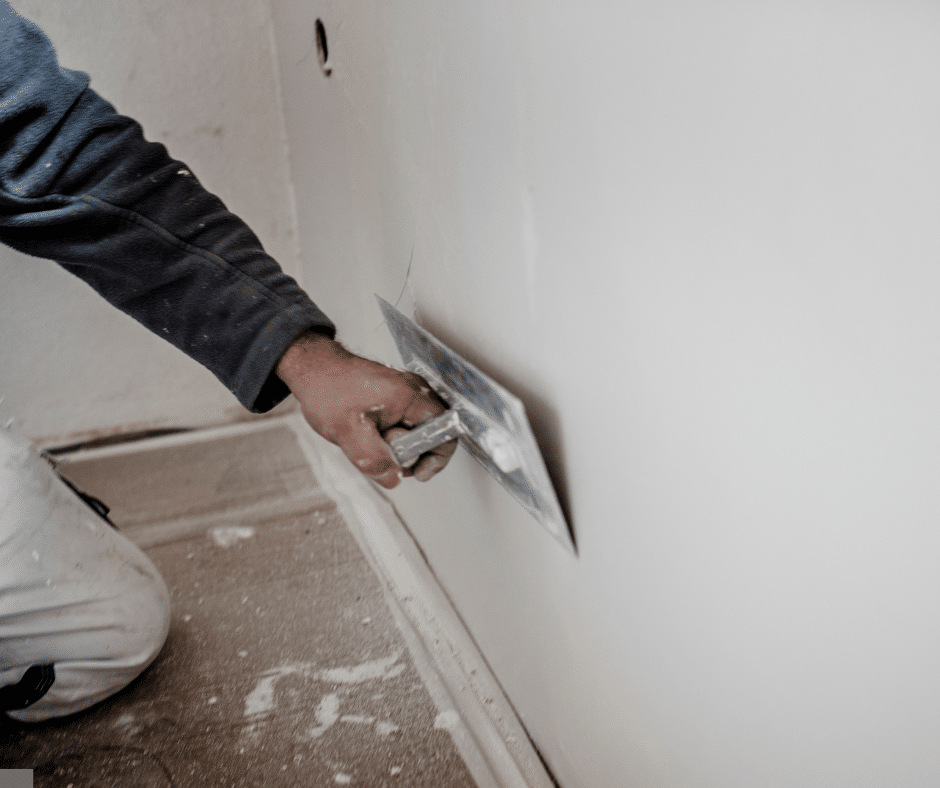
Check the blockwork manufacturer’s technical instructions before applying plaster to lightweight block walls. Normally, internal brickwork and blockwork walls require at least two coats of plaster.
The use of expanded metal lath in plaster at known problem areas may reduce crack problems and plaster beads should be used to provide edge protection at external corners.
Plaster mixes should never contain a combination of Portland cement and gypsum plaster.
Ensure that plaster which has been specified to contribute to the acoustic or fire resistance
performance of walls and ceilings is applied to at least the correct minimum thickness.
Plaster and plasterboard may be intended to provide local fire protection to steel beams and if so, should be carefully checked.
Different grades of plasterboard may have been specified in different areas, for example wet rooms or kitchens usually require moisture resistant products. Check against the drawings.
Plastic type ceiling boards and tiles are not seen so much nowadays, but if it’s something you really want, make sure that they comply with the fire regulations.
Moisture content
Before fitting finished products, the underlying structure must be at or below the maximum
permitted moisture content for each particular type of finish.
Traditional sand-cement floor screeds take a very long time to dry properly (allow up to 150 days for a 100mm thick screed). Fast-drying screeds will take less time, but always check the manufacturer’s technical information and be very aware that a self-levelling screed is not necessarily a fast-drying one.
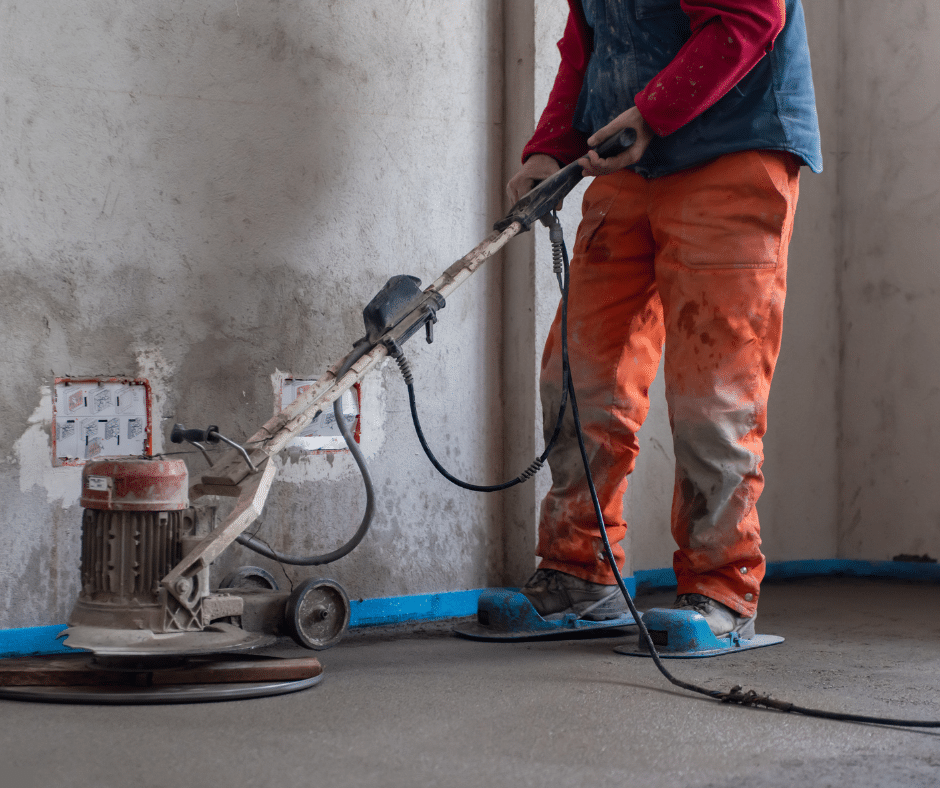
Carry out an accurate moisture content assessment towards the end of the drying period and check with each supplier to make sure the screed is fit for accepting their finished products and fixing methods.
Before fixing finished timber products, allow them sufficient time in the new building to
acclimatise to reach an average temperature and humidity level that will be experienced during
long-term use.
Timber floorboards and other wood-based flooring should be conditioned to the correct moisture content before fixing and it is advisable to keep underfloor heating running before and during the laying of the floor finishes.
Staircases
Stairs, whether they are of timber, glass, metal or concrete; are more often than not, fabricated off site. They were traditionally included in the first fix but nowadays, with the exception of concrete stairs, tend to be left until most of the wet trades have finished.
It is imperative that the stair manufacturer at least knows the exact measurements between finished floors, which means that you need to have accurately determined the structural floor levels and floor finish thicknesses in advance.
Last-minute changes to stair configurations can be very problematic and therefore costly. You might find difficulties with providing supports for glass balustrades where metal or timber was originally specified, or moving the stair position could create issues with headroom and distances to door openings.

Floor finishes
Floor finishes should be protected from damage until all works are complete. If grit gets under the protective layer, it will scratch floorboards and tiles.
Check the alignment of joints in floor and wall tiles unless they are intended to be irregular. Also check the manufacturer’s details for the correct joint sizes for the tiles being used.
There may be small variations in surface level between adjacent tiles, but these should generally be 1mm or less where the joint is up to 6mm wide, or 2mm or less where the joint is over 6mm
wide. There should be no more than ± 3mm of deviation in the level of a tiled surface across a
distance of 2m.
Tiles on solid floors should be bedded on a continuous bed of mortar (i.e. not dabs) or a proprietary adhesive, either of which should be laid to the correct thickness for the material used.
Tiles on timber floors should be laid on an approved flexible adhesive.
In wet rooms, decide whether tiled skirtings are to be fitted. Also decide on whether tiles should be from floor to ceiling and whether you want tiles or PVC wall panels within showers. When choosing shower trays, ensure that the proper depth of waste traps can be fitted (check your drawings).
Why do tilers charge so much these days?
The tiling rate in Dublin at the moment is €65/sqm; it was €18/sqm four years ago.
Anything off standard you will pay extra, so large format tiles or if you need them cut and laid in a pattern, the latter adding €15/sqm extra. The high cost may be attributed to the fact that tilers are hard to find and tend to be the most difficult trade to get on site to do a job.
Where the width of a tiled floor exceeds 2m, movement should be provided at floor perimeters and around rigid upstands. Note that floor perimeters would include those which meet under internal doors.
All tiles must be suitably grouted according to their location and in accordance with the manufacturer’s instructions.
Floating floors are those in which the floor finishes are separated from the substrate by a layer of insulation boards and/or a vapour control layer. The layers should allow the floor finish to be physically isolated from the walls and the supporting floor structure. Extra support, using battens for example, may be required under heavy items such as storage heaters.
Timber floor finishes such as woodblocks or parquet flooring which are directly applied to the solid substrate should be fixed using the correct adhesives, to the pattern shown on the drawings and with the correct perimeter movement gaps.
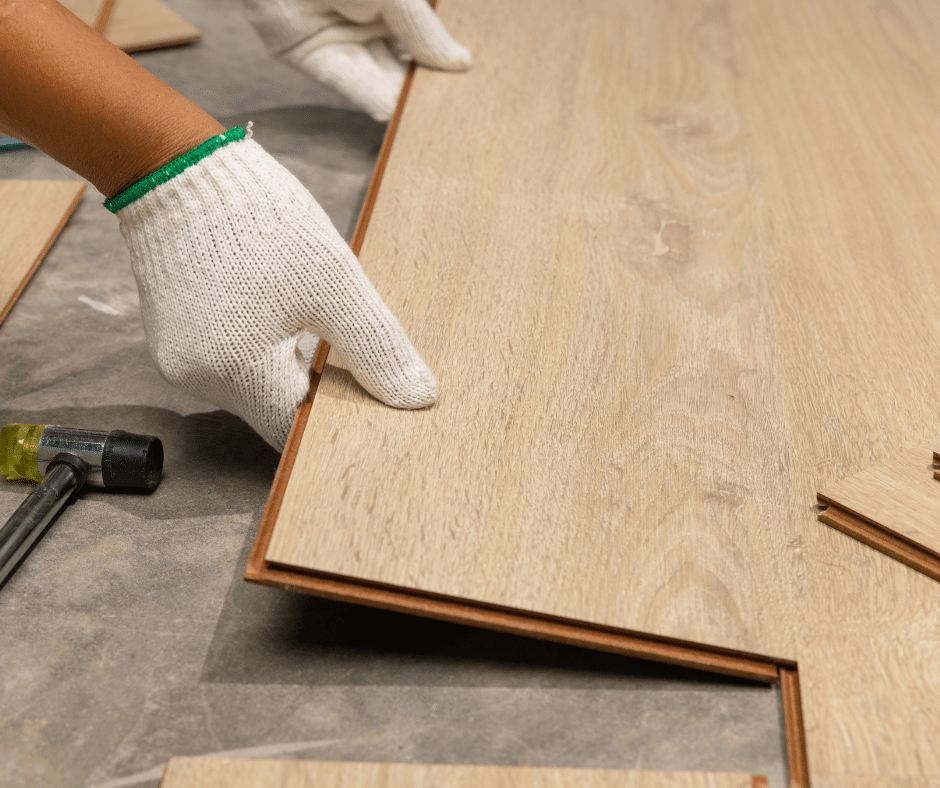
Panel type flooring products such as plywood, chipboard or oriented strand board (OSB) have particular requirements for nails or screws, fixing patterns and intermediate supports.
Attic access
Don’t forget about fitting insulated and sealed loft access doors and abide to the various regulations that apply to them.
Check the specifications for the correct methods, because fixings are often missed, resulting in noisy floors. The minimum acceptable thickness of the flooring will be directly related to the support spacings and the design strength of the material.
Flexible resilient sheet or tile flooring products have specific requirements for underlay materials, adhesives, jointing, moisture control, laying temperatures and methods for adjustment after initial expansion or contraction. Follow the manufacturer’s instructions for whichever type is being used.
Problems arising with these flooring materials are often attributable to incorrect moisture content of the floor structure and to poor preparation of the substrate.
Architraves and skirting boards
Internal door frames will have been fitted during the first fix. Most of a door frame will be covered during the second fix by door stops and architraves, but the part where the door sits will be exposed so will need protection, especially if it is to be left with a natural timber finish.
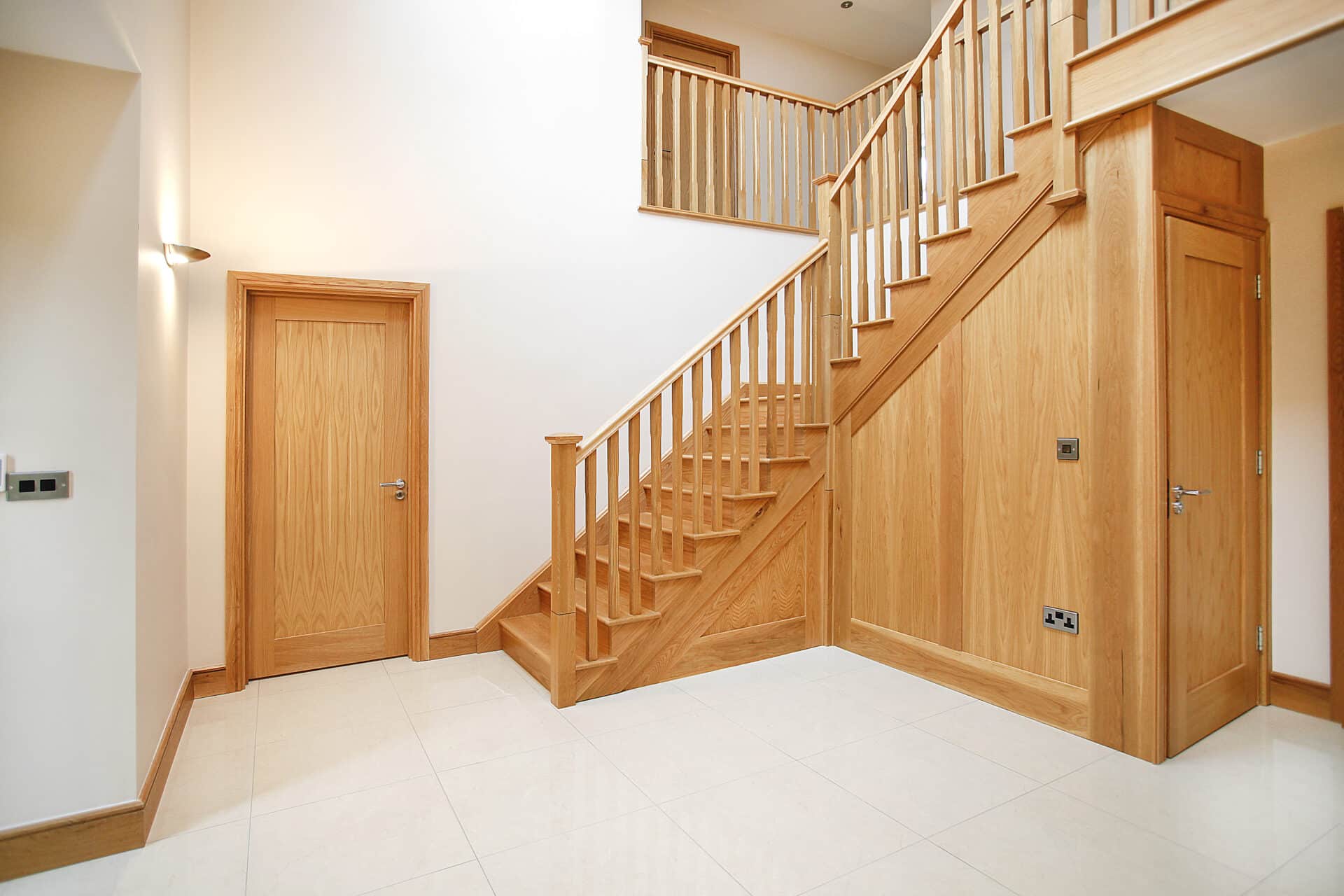
Pre-finished internal doors and doorsets should be robust and good quality. You will also need reassurance that pocket doors and their sliding or rolling gear will remain trouble free. Examine them closely in door showrooms before buying.
For some reason, a common omission is forgetting to fix internal door hinges with the correct number of screws, so check every hinge.
Window dressing
Decide whether curtains or blinds will be fitted within window reveals or outside them. Ceiling tracks may be required, especially at corner and bay windows. Ensure that recessed ceiling tracks do not compromise the fire or acoustic performance of the ceiling.
All openings in walls should be squared, level and plumb, subject to permitted tolerances. Similar rules apply to the windows or doorframes fitted within those openings.
There are also permitted tolerances for internal doors and their frames, but do check the rules with the manufacturer if fire doors are fitted.
The fixing of skirting boards is best left until after all floor tiling or boarding is complete. A
maximum gap of 5mm between the bottom of the skirting and the floor finish is considered
acceptable, but note that joist shrinkage in timber floors may increase this gap over time.
Ventilation solutions may require gaps to be left under internal doors, so check that this is done in accordance with the approved drawings. These are gaps need to additionally allow for floor finishes if they have not yet been laid.
Note that factor-finished item such as a door may have a slightly different appearance to site-finished components such as the architraves and doorstops adjacent to it.
Some joiners will fix skirting boards, architraves, dado rails, picture rails, coving or cornices,
etc. using a strong adhesive. This is very effective and avoids having to fill nail holes, but can
be notoriously difficult to remove without damaging plaster if you need to change any of it in the future.
The fixing of skirting boards is best left until after all floor tiling or boarding is complete.
Spray paint
Most new houses are now painted internally for the first time using spraying techniques.
The first thing to do is make sure that the painters take particular care to protect all
other finished surfaces.
Spraying will tend to highlight imperfections in the underlying surface so scrupulous preparation is essential.
A professional service will do so, or tell you what needs to be done, and also let you know at what moisture content they can start the job.
Some spray paints may create unhealthy fumes or contain volatile organic compounds (VOCs), so access to others may need to be restricted during this work.
Checklist: Visual checks
Internal finishes should usually be checked in daylight from within a room and if a room does not have daylight, only fixed (i.e. not portable) lighting should be used.
Fitted kitchens should present straight lines along worktops, drawers and doors. Gaps
between doors and drawers, etc. should be regular, whilst some allowance needs to
be made for adjusting the likes of door hinges and drawer runners.
All kitchen parts must be resistant to delamination, warping and other damage from heat, steam and moisture. Surfaces with significant scratches or marks should be repaired or replaced by the installer.
Radiators and other factory-manufactured components such as electrical connection boxes, socket outlets and hatch panels, etc., should be checked for obvious defects.
Make sure that your fuse box has been clearly labelled (i.e. not with illegible pencil scribbles) so that you know which fuse does what and you can identify them easily by torchlight.
Check sanitary items such as baths, wash basins and shower trays for chips and scratches. Any items with defects which are conspicuous at a distance of not less than 5m should be repaired or replaced.
Glass should be generally free from undue defects, although occasional bubbles, small particles and small scratches may be visible. Glass should be checked in daylight from within the room at a minimum distance of 2m, or 3m for toughened, laminated or coated glass.
Look for the correct stamps on safety glass and fire rated glass, you will usually find these in a corner of the pane.
In almost all finishes and particularly true of reclaimed materials, colours and textures may not be consistent. It is very much a matter of opinion as to how much inconsistency is acceptable, however there are common sense limitations as to what is an aesthetic feature and what is not.