In this article we cover:
- Different floor types and how they tie in with ICF
- Wall plate details
- The concrete pours: how to prepare and what to expect from them
- Main watchpoints for this stage with images
The vast majority of self-build projects we come across choose hollow core slabs for their first floor construction. The beauty of ICF is that you can be ready for the hollow core at the first floor level very early into your build.
The slabs sit onto a bed of mortar laid on the concrete core, see Figure 1 for ICF walls at the first floor level waiting to receive slabs. As you can see from the photograph the vertical rebar is also left up to tie the first and second pour of concrete together.
Always refer to the precast floor manufacturer’s instructions regarding the minimum bearing required. It’s very important at this stage to ensure that the concrete core of the ICF is left level after the concrete pour.
Also, a note from the picture, the outside leaf of EPS is left to allow integration of the next lift of ICF formwork. This first block at the first floor level will need to be cut to allow for the depth of the hollow core. This is another good detail from an airtightness perspective.
You can also use timber joists at the first floor level. This once again is front loaded at the design stage, with input from your architect, structural engineer, ICF system supplier and webbed joist supplier.
Once spans are agreed and joist centres are agreed the ICF installer can cut out pockets at the required centres in the EPS to enable the concrete when poured to finish level with the outside of the internal leaf.
Figure 2 shows pieces of plywood screwed to the plastic supports of the inside leaf of ICF formwork. When this is struck (removed) the concrete will be level with the inside of the EPS which will allow you to fix a timber ledger to receive your timber or webbed joists. See Figure 3 for concrete pockets ready for timber ledger.
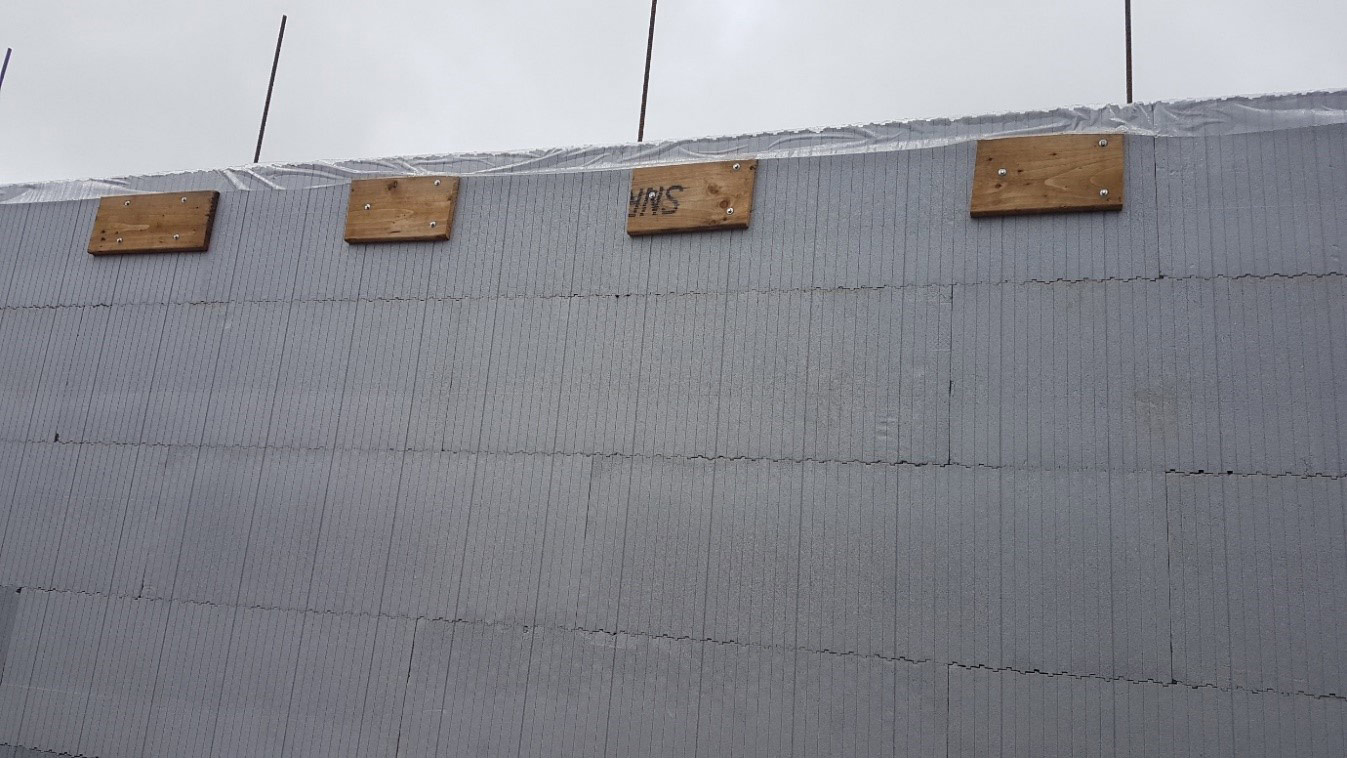
Wall plate detail
The wall plate can be bolted down or strapped to the concrete core much like the first floor. It is extremely important that the concrete is left level.
Note the EPS on the inner leaf is left up level with the top of the wall plate. As you can see galvanised wall plate straps were set in the concrete during the second pour.
Alternatively, a threaded bar to your structural engineer’s specifications can be used. This may be a better option as the wall plate can be shimmed if required to be levelled.
I always detail a warm pitched or flat roof for ICF houses. This carries on the blanket of insulation that wraps the structure on the outside of the building. It starts with the insulated foundation, ICF walls, and then carries over the roof structure.
This ensures that the structural elements are kept at or near internal environmental conditions, therefore, reducing the chances of thermal stress and risk of condensation.
The concrete pours
Concrete pours are usually completed by the ICF installer, the contractor who built the walls. This happens after the architect and engineer have checked and signed off on both the ICF formwork and that the window and doors are in the correct locations, straight and plumb.
The structural engineer will check all rebar is as specified and will get an adequate concrete cover. It’s time for the concrete pour. This is ordered from your local concrete batching plant. Key point here is to ensure the correct compressive concrete strength class is ordered as specified by your structural engineer.
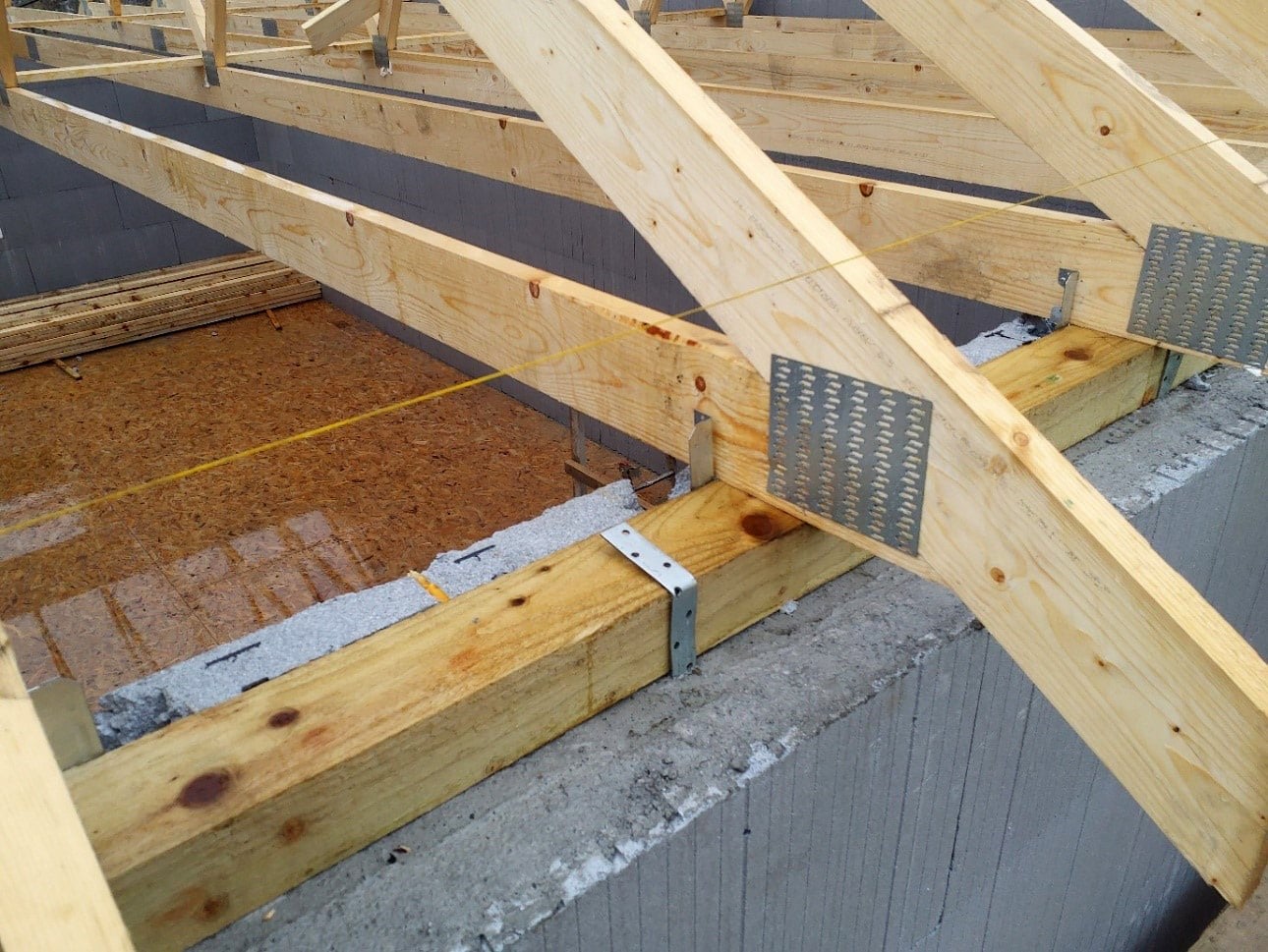
The pour is not very labour intensive as the concrete is pumped using either a line pump or overhead boom from a concrete pump lorry, which moves around the formwork in a circular fashion and pumps the concrete into the cavity of the ICF formwork.
When pumping the concrete, ensure it’s pumped into the central cavity away from the corners and not directly against the polystyrene. The pour should happen in layers not exceeding 1200mm/hr and the total daily height should not exceed 3m. This ensures adequate compaction is achievable and to avoid possible movement and excessive pressure being placed on the ICF formwork.
A single storey dwelling with a wall plate higher than 3m will require two pours. This is where a good installer is required who knows their trade.
If the next lift is only 1350mm high, or approximately three ICF blocks, my experience has taught me that it is very difficult to keep this section of wall plumb and level during the pour. Extra attention is required during the propping and pouring of this section of the wall to ensure it is plumb straight and level.
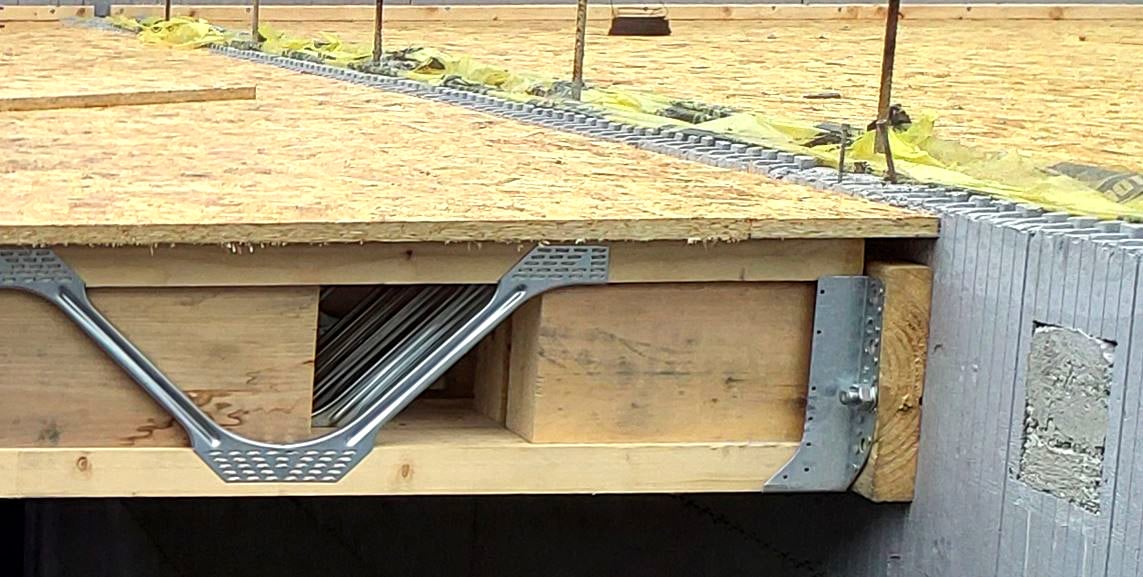
This I where I would recommend bracing on both sides. Generally bracing only occurs on one side, usually the inside.
To avoid air pockets /voids in the concrete, particular attention should be paid to areas where the flow of concrete may be impeded such as corners or lintels where extra rebar is placed. The use of a vibrating poker is recommended but the poker diameter should not exceed 25mm and when using the poker keep back approximately 1m from the corners and do not touch the ICF formwork.
Once pouring is complete, immediately check the walls are straight, adjusting props vertically as required. Any damaged forms should be repaired immediately and concrete leakages can be hosed off the external face of the forms before it sets.
The concrete should be left to cure until it has achieved the minimum strength class, usually after two to three days to allow construction to continue. Props should be left in place as long as possible.
In freezing or very hot weather, ensure the top of the ICF formwork is covered to protect the concrete from adverse weather curing.