For many years, homes in Ireland and the UK have been ventilated via natural air infiltration. The result of this has been high energy consumption for space heating (which accounts for over 50 per cent of the energy used within a dwelling).
New energy efficient homes today are being built as airtight as possible with double or triple glazed windows, sealed doors, and high levels of insulation, with airtightness also contributing towards enhanced u-values. Existing property homeowners are being encouraged to make homes more energy efficient by insulating their roofspace, cavity walls, etc.
This increased airtightness in a dwelling requires a planned ventilation approach. The objective of a good ventilation strategy is to provide a balance between energy efficiency and indoor air quality. This strategy should have an integrated approach, taking into account other factors such as thermal insulation, heating systems, controls and the requirements of the household occupants.
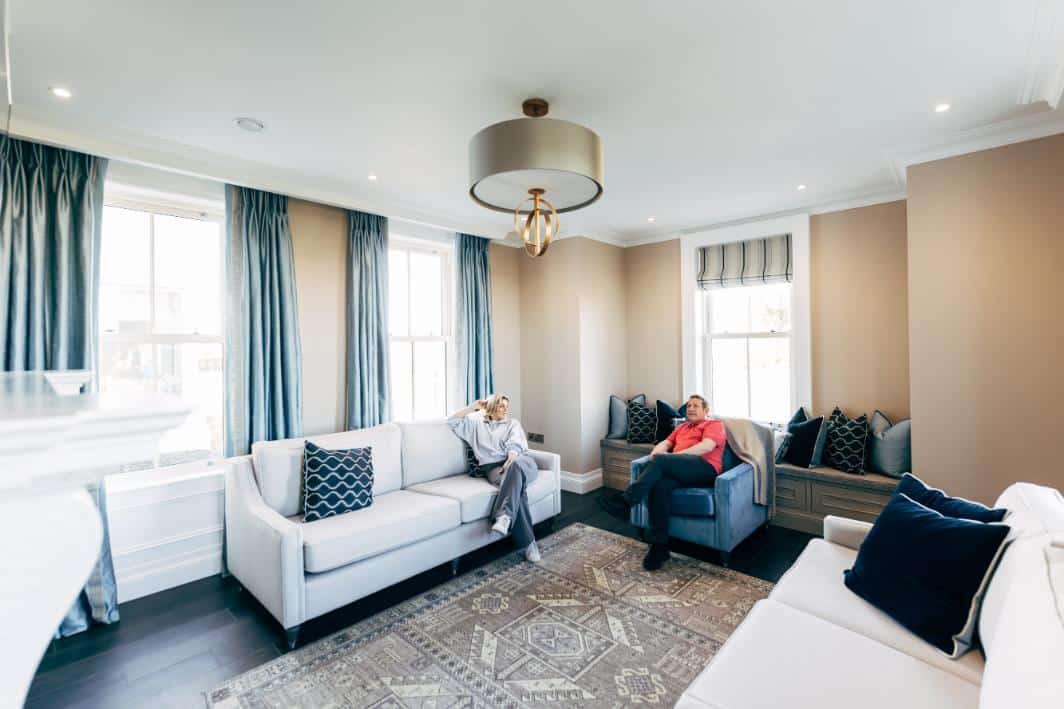
According to The Energy Saving Trust, “energy loss due to ventilation accounts for approximately a fifth of space-heating energy demand in an older poorly insulated dwelling. Natural air infiltration alone can result, at times, in too little ventilation. This leads to poor indoor air quality and other, more readily visible impacts such as condensation and mould on indoor surfaces”.
Add to this the fact that poor ventilation in a dwelling can also cause potentially serious health issues, excessive carbon dioxide, damage to the fabric of the building and it’s easy to see why the concept of “Build Tight – Ventilate Right” has never been stronger.
Energy Efficiency Savings
Achieving an energy efficient standard of ventilation requires consideration of both the building fabric and the efficiency of the ventilation system.
The 2 main ways in which ventilation “uses up” energy are:
- The requirement to heat up incoming air (particularly during colder weather when heating systems are running) and its subsequent loss as it leaves the property via purpose provided openings i.e. window vents or extractor fans, and through air leakage;
- The electrical power required to operate a mechanical ventilation system.
The standard of airtightness achieved within a dwelling will have a significant impact on the ventilation rates achieved. In a non-airtight house, the most common air leakage paths include:
- Underfloor ventilator grilles
- Gaps in and around suspended timber floors
- Leaky windows or doors
- Pathways through floor / ceiling voids into cavity walls and then to the outside
- Gaps around window frames
- Gaps at the ceiling-to-wall joint at the eaves
- Open chimneys
- Gaps around loft hatches
- Service penetrations through ceilings
- Vents penetrating the ceiling / roof
- Bathroom wall vents or extract fans
- Gaps around bathroom & kitchen waste pipes
- Kitchen wall vents or extractor fans
- Gaps around floor-to-wall joints (particularly with timber frame)
- Gaps in and around electrical fittings in hollow walls
- Air infiltration through unplastered walls,
It is considered good practice to have a maximum air permeability (m3/h/m2) level of 5 for a dwelling, with this reduced to a level of 3 to reach Best Practice guideline. To achieve this level, many of the above common air leakage paths are eradicated, resulting in a greater need to ventilate effectively and gain more energy efficiency.
There are many energy saving features in mechanical ventilation systems. The type of ventilation used is often determined by airtightness level, budget, overall house construction type, the lifestyle of the occupants, and the knowledge of specifiers advising on the ventilation strategy. The energy efficiency of a mechanical ventilation system can be improved, where applicable, by using heat recovery elements, low energy fans, and/or energy saving control devices.
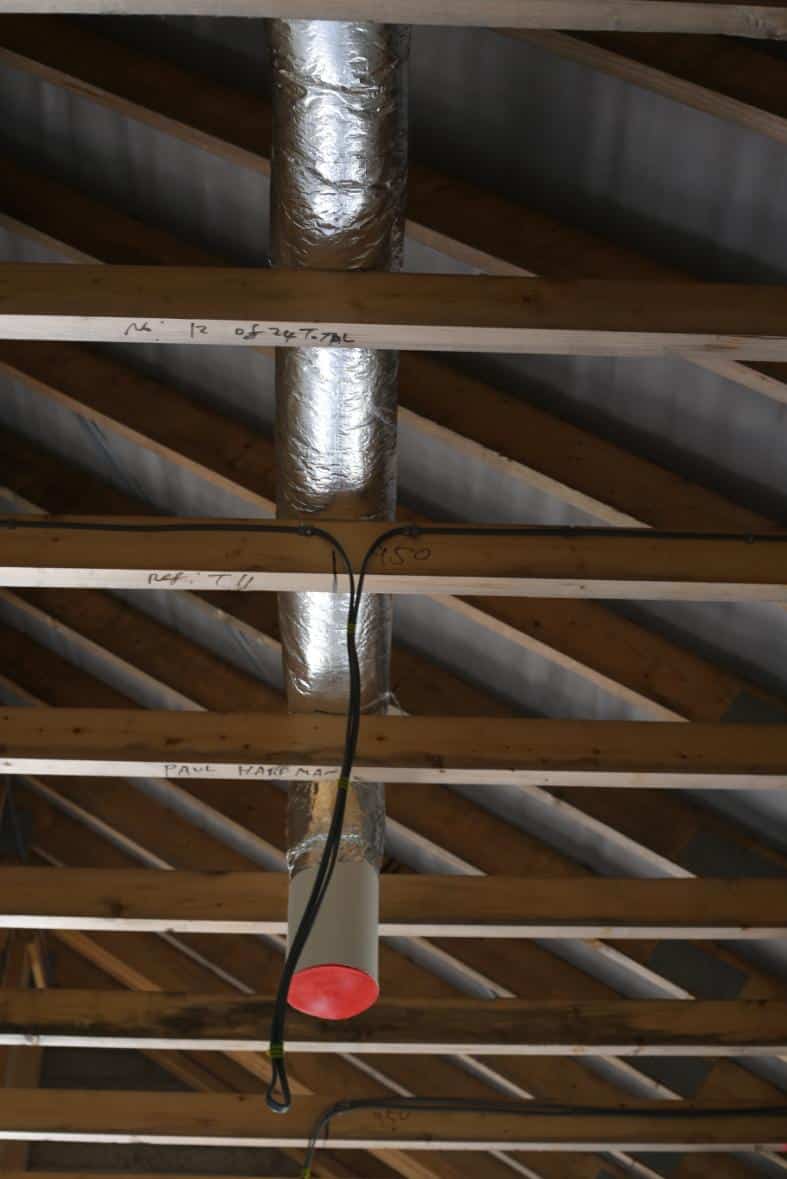
The term Specific Fan Power, or SFP, is used to measure the electrical power to operate a mechanical system, including power to the fans, transformers, controls and safety devices. Thus, the lower the SFP, the more energy efficient the ventilation system. It is also important to minimise unwanted pressure losses in the ventilation system during installation. This can be done by avoiding the use of flexible ducting, and minimising the number of bends as possible.
An energy saving can be made by the use of SAP Appendix Q listed ventilation units, as opposed to non-compliant units. This Appendix Q listing only applies where the installation has followed the correct guideline procedures as recommended by the Building Research Establishment (BRE), i.e. solid, rigid ductwork is used.
Energy savings can also be made if a Mechanical Ventilation with Heat Recovery system (MVHR) is installed in a dwelling. An MVHR system reduces the amount of energy needed to heat up the incoming air to room temperature. When considering the heat recovery efficiency, often expressed as a percentage, other variables should be taken into account, e.g. the SFP of the ventilation unit, the airtightness level of the dwelling, the heating system, the type of ducting installed etc.
Some ventilation systems offer energy saving controls as optional features, including humidity sensors, moisture/pollutant detection etc. This means the level of ventilation in a room can be automatically reduced if the pollution level in a room is low, again saving energy.
Presently, ventilation (required by Building Regulation) in houses is provided by 4 different methods:
- Balanced Mechanical Ventilation with Heat Recovery (MVHR)
- Mechanical Extract Ventilation (MEV)
- Demand Controlled Ventilation (DCV)
- Positive Input Ventilation (PIV)
- Background Ventilation
Mechanical Ventilation with Heat Recovery (MVHR)
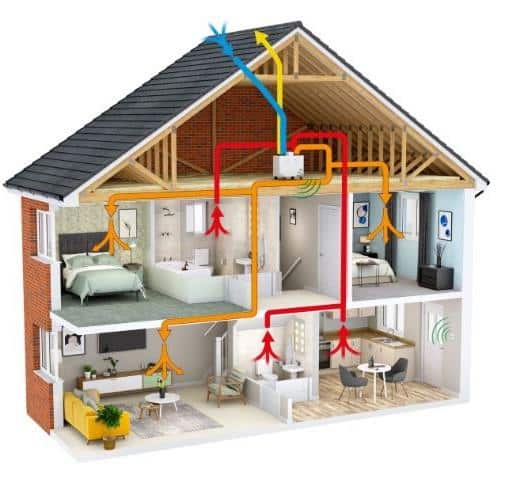
MVHR systems are considered to be the most energy efficient method of ventilating an airtight dwelling. Fresh air is continuously drawn into the home via a low energy heat recovery ventilation unit, located in the roofspace/utility area of the home. The ventilation unit filters the incoming air to remove pollutants and insects. Once passed through the heat exchanger within the ventilation power unit, the warm, clean, fresh filtered air is distributed around the home through a series of ducts which are run to each habitable room i.e. living rooms, bedrooms etc.
The air from wet rooms i.e bathrooms, kitchens, wc’s, utility areas etc is continuously extracted and filtered back through the ventilation unit. Most of the heat from the extracted air is transferred to the fresh incoming air. The heat recovered can off-set the heating costs and reduce fuel bills. The system provides low energy balanced continuous ventilation without the need for extract fans or window vents, ensuring a draught-free living environment.
This controlled, pre-heated fresh air is provided throughout the house whilst at the same time delivering constant clean, fresh filtered air, and improving indoor air quality. Once again, it is vital that an MVHR system is installed and commissioned properly according to the guidelines set. Filters within the MVHR units should also be changed / cleaned annually to help maintain system efficiency.
MVHR systems are designed to recover up to 95% of the heat normally lost through open windows, trickle vents and other break-out points i.e. extractor fans in a building structure. To help with energy savings, MVHR units should contain low energy EC motors, and have an SFP less than 1.0wls−1. Commonly used heat recovery technologies include counterflow and rotary thermal wheel, both of which should have low energy EC fans fitted resulting in very low running costs.
PassivHaus
If a dwelling is being built to Passive standard, In the interest of maximum energy savings, the rate of ventilation with fresh air should not be higher than needed to achieve a comfortable indoor humidity.
According the PassivHaus Institut: “In the past, air change rates as high as 0.5 or even 0.8 were considered necessary to keep interior humidity in winter low enough to discourage the development of condensation, which can cause mildew and damage to building components. But this risk does not exist in a passive house. Outside building elements are so well insulated that interior surfaces are too warm for condensation to occur even at 60% relative humidity; and moisture barriers and air seals prevent moist inside air from reaching building elements that could cool it to below the dew point. Therefore, fresh air volume can be lower, particularly when occupants perceive the humidity as being too low. “Appropriate” air change rates for residences are between 0.3 and 0.4. For passive houses, we generally recommend leaning toward the lower rate. This keeps the indoor air quality good, while maintaining a comfortable humidity and maximizing energy savings”.
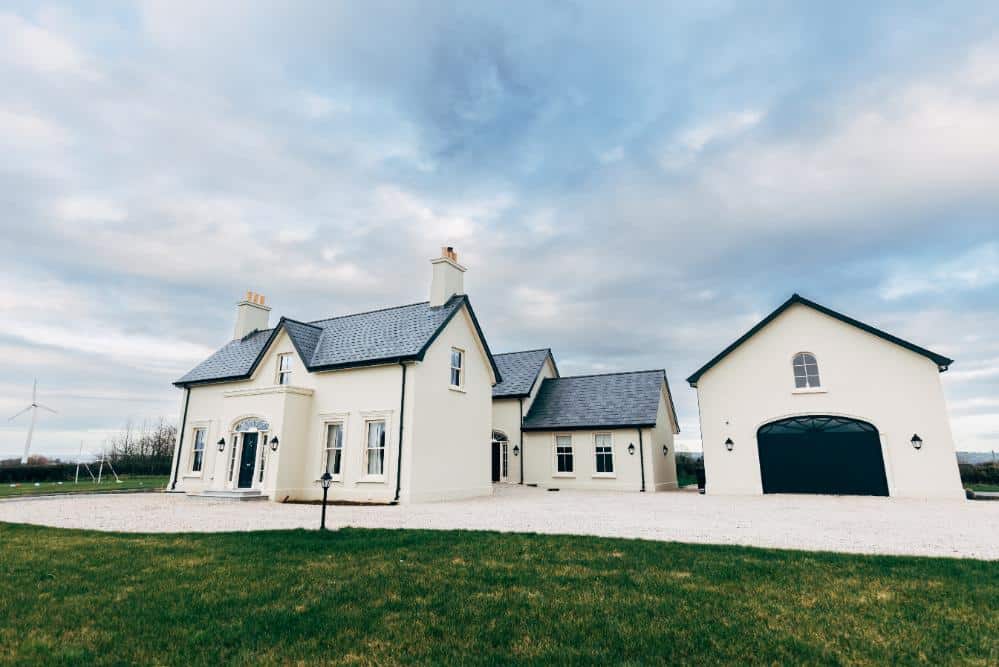
Mechanical Extract Ventilation (MEV)
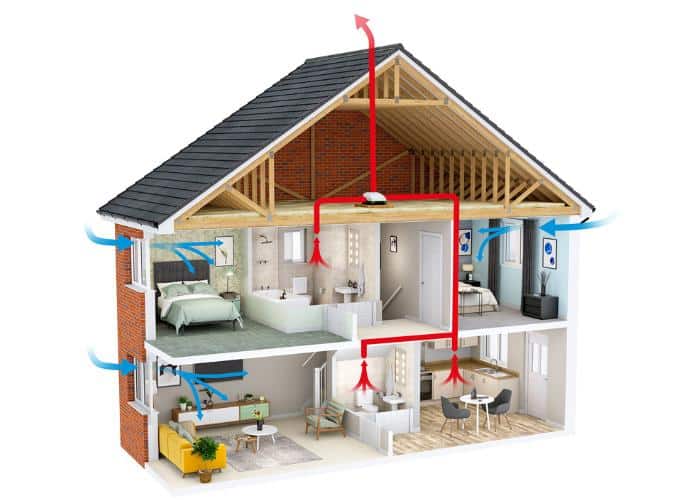
An MEV system is a low energy, continuous mechanical extract ventilation system designed with multiple extract points to simultaneously draw moisture-laden air out of the wet rooms, Primarily for use in dwellings with 6 wet rooms or less (or dwellings up to 300m2/3200sq.ft), a mechanical extraction ventilation system is usually installed in a roof space or cupboard and runs continuously at a normal low ventilation rate, extracting stale polluted air from rooms where the most moisture is generated, e.g. kitchens and bathrooms whilst minimising the migration of humidity to other rooms. A flow of fresh air from outside is supplied by a Positive Input Ventilation unit or window vents.
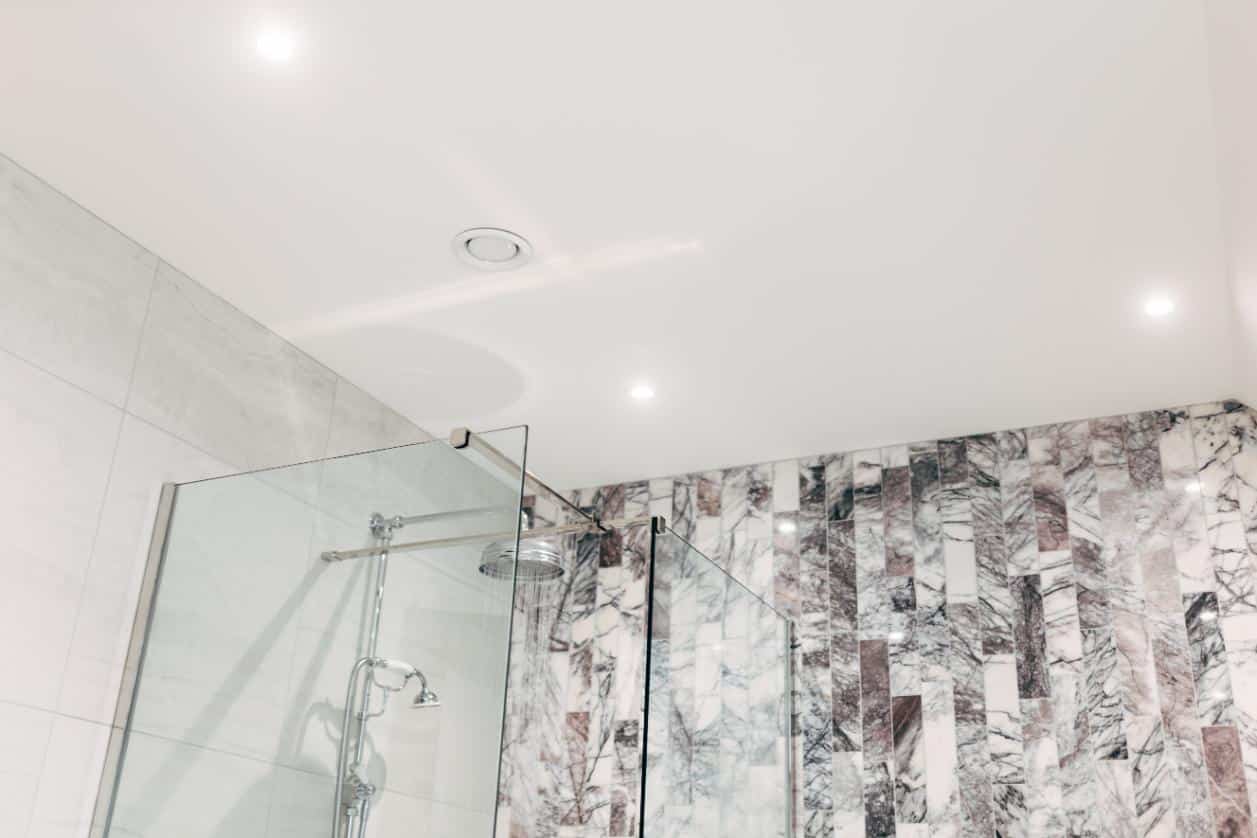
Homeowners can make significant energy savings as there is no need for noisy extractor fans in each wet room which create multiple breakout points in the building, creating draughts, air leakage and heat loss. It is also much more economical to run one fan instead of multiple fans and can have an SFP down to 0.18wls.
However, MEV systems need to be balanced and commissioned, can have long runs from certain wet rooms and can be slightly more expensive than extract fans.
Demand Controlled Ventilation (DCV)
Demand-Controlled Ventilation (DCV) is a ventilation system designed to supply fresh, filtered air and extract stale, moist air. The system automatically boosts ventilation rates as required based on humidity levels.
A DCV unit is usually located centrally in the roof space or in a cupboard space. Wall ventilator grills are located in every room. The system is equipped with a sensor which detects humidity levels and automatically adjusts the airflow rate based on the indoor air quality. If a room is heavily occupied, the humidity levels will be high – a DCV system will sense this and increase airflow into the room. If a room is unoccupied or humidity levels are low, the ventilation rate is reduced. Similarly, in wet rooms such as bathrooms, when there is an elevated level of humidity and moisture detected, the rate of extraction is boosted to adequately remove the moist, stale air.
As a DCV system optimises airflow rates based on the indoor air quality, the ventilation rate varies. Therefore, the system only boosts ventilation rates when needed, increasing energy efficiency.
Alternative Ventilation – Positive Input Ventilation (PIV)
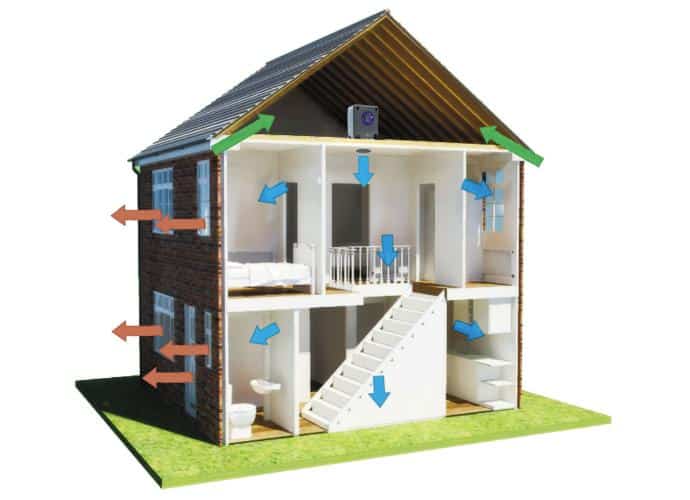
An alternative option to background ventilation is Positive Input Ventilation (PIV). These are mechanical ventilation systems which supply a continuous flow of air to the dwelling from a central location. Designed to run continuously, a PIV unit dilutes, displaces and replaces moisture laden air with fresh filtered air, forcing contaminants out of the property through natural cracks and leakages. Indoor air is improved, eliminating condensation and mould growth, generating fresh filtered air throughout.
PIV systems are easy to install, easy for the end user to operate, and are ideal for social housing and existing house market. Also, as a PIV system replaces trickle vents in the window, more of the heat generated within a dwelling, stays in the dwelling and is thus a more energy efficient option. However, PIV units are not widely recognised in the industry as a form of ventilation in new dwellings and can be perceived as causing draughts in the dwelling.
Background Ventilation
Sometimes referred to as natural ventilation, background ventilation occurs when fresh air enters the building i.e. via trickle vents in the head of window frames (which sometimes can be permanently closed) or through open chimneys. Natural leakage also occurs through gaps around windows and doors throughout the fabric of the building, due to poor construction.
If window trickle vents are the source of background ventilation, the volume of air needs to be 65,000mm2 per 100m2 of floor area for a typical 5 bedroom house, adding 7000mm2 per 10m2. This gives an air permeability level (Q50)< 5.
Extraction fans are still required in kitchens, bathrooms, utility rooms, WC’s and ensuites to provide rapid extraction.
This form of ventilation is popular because of low price, the ease of which installed, and the simple operation. The disadvantages are that the ventilation is not energy efficient as it cannot be controlled, can cause draughts, the homeowner also has to listen to noisy extraction fans, and both window vents and extractor fans can be easily tampered with by a homeowner.
This system is not recommended as a best practice standard.
In summary, whilst there are different types of ventilation options, energy efficient homes of today should have high levels of insulation, be built as close as possible to airtight standards and contain a Mechanical Ventilation with Heat Recovery system to provide fresh indoor air and energy savings. In addition, all mechanical ventilation systems should:
- Be independently tested at the BRE
- Be SAP Appendix Q listed
- Comply with all building regulations
- Ideally be Energy Savings Trust compliant
- Be installed and commissioned following recommended procedures
References
Passive House Institute, Germany
Northern Ireland Building Regulations
Republic of Ireland Building Regulations Part F – Ventilation