he plant and tool hire business is a multi-billion-dollar industry that has grown in complexity and scope decade by decade. Many local companies are small (employing only a few people) but large corporations have increasingly come to dominate the market, bringing with them all the advantages that scale brings to any industry.
Not long ago, people could and would build a whole house using only a very limited range of hand tools and basic equipment. But as health and safety issues have become more important, as labour costs have risen and as builders want to maximise efficiency on their sites, we’ve all become accustomed to using more and more sophisticated equipment that can make tasks easier, safer, cheaper and quicker.
There are good reasons to hire equipment. When building your home, you won’t want to tie up money in owning expensive equipment and plant when you could pay for it only as you need it. By not owning it you’ll also be freed from the worry and expense involved in its maintenance and repair.
Today’s world of strict standards and regulations make the owning and operating of equipment an onerous responsibility. Hire companies take this very seriously and are responsible for the equipment they hire out, performing regular safety checks before you start to use their things. Because many hire companies are chains, they can often supply you from another branch with any item they don’t have to meet your exact needs.
Also, because hired equipment is so intensively used it reduces its carbon footprint – sometimes by as much as 30 per cent.
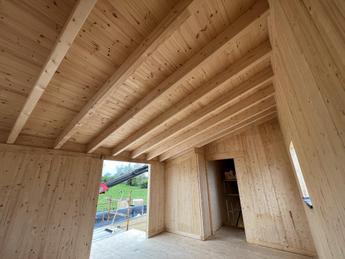
Scaffolding
However simple your build, there’ll come a time when you’ll need access to things that can’t be reached from the ground. Cherry-pickers, scissors-lifts, access towers and numerous other devices are now widely used on even modest self-builds.
But by far the most common system for working at height is scaffolding, which is a temporary structure created to allow access for the construction, maintenance and servicing of buildings. The average house build will use scaffolding on a relatively small scale and the cost will usually be between five and ten thousand.
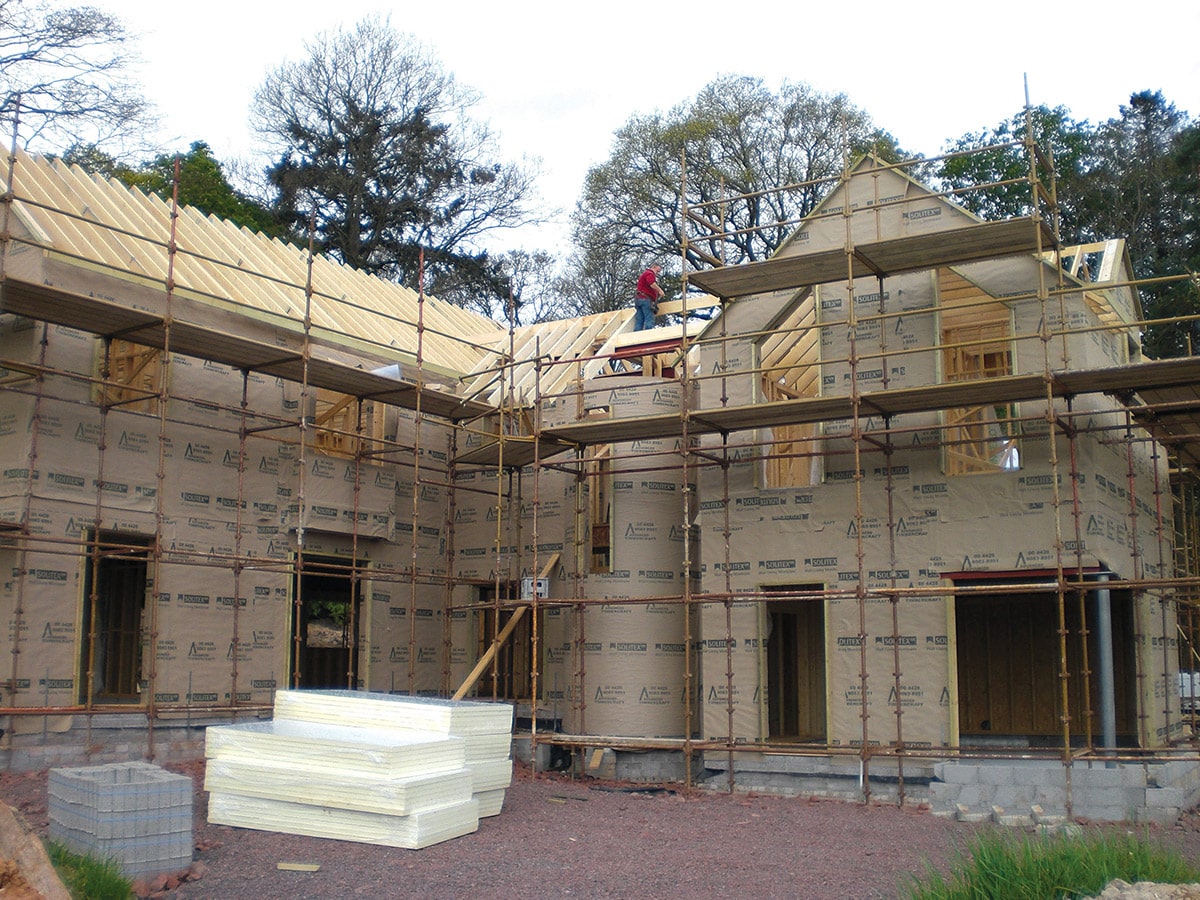
Most self-builders get their scaffolding from one of three sources. If you’re using a main contractor, he may have his own scaffolding and access towers which he keeps in a yard ready for when he needs them. Other main contractors or subcontractors choose to hire things in as required. If you are managing your own build it’s possible to buy scaffolding but this doesn’t usually make financial sense as you’ll probably get to use it only once. Unless you intend to use a tower many times over a long period it’s usually best to hire this too.
There are four main components:
The tubes: are usually made of steel, of a standard diameter but in several different lengths. Most companies brand their tubes somehow in an effort to reduce theft. Because the various components of scaffolding are so useful to people in the building and construction industry and are relatively small and portable, they are often stolen. For many scaffolding companies this is an important issue.
Boards: create the working surface at heights for builders and a place to store materials as the build progresses. They are made from seasoned wood in a standard (225mm) width and are a maximum 3.9 metres long. Their ends are protected by steel bands or plates. It’s also possible to use aluminium or steel decking instead of, or as well as, timber boards. But unless the scaffold is being installed on a solid surface, other timbers, called sole boards, will be needed. These are laid flat on the surface on to which the scaffold is placed, to create a firm base.
Couplers: are the fittings that hold the tubes together. These are the clever part of scaffolding because they have to hold the tubes in place (often under considerable loads) and yet be quick to fit and remove.
Ties: are essential to fix the tube structure to the building or other framework so the scaffold doesn’t fall over. Scaffolds are only rarely entirely self-supporting, free-standing structures. They need to be stabilised as they rise.
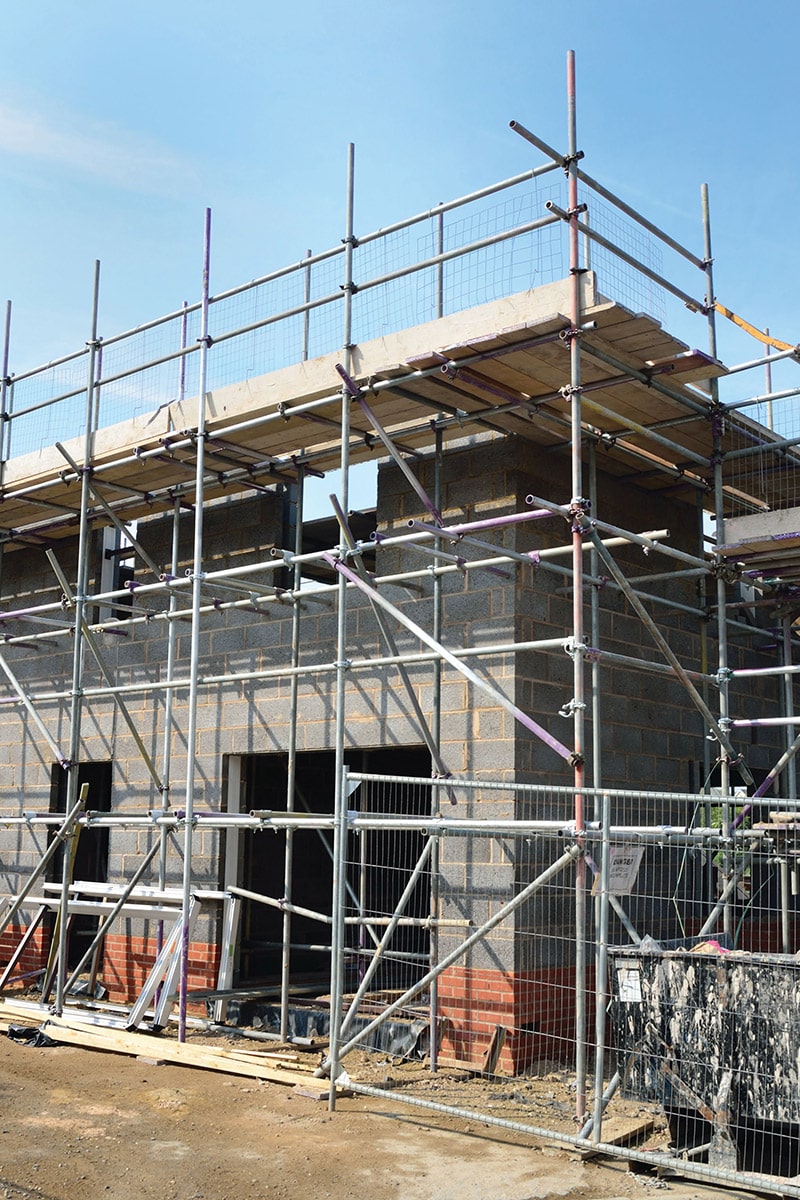
Types of Scaffold
Before you start your new build you’ll need advice from the scaffold company you intend to use. They’ll come to assess the job to decide:
• How practical the location is from an access point of view. Scaffolding, by its very nature, consists of many individual units, all heavy and needing to be taken by hand from a truck to the erection location. The closer the truck, the better and safer the exercise.
• How long you’ll need the scaffold for. Your architect or main contractor will know this.
• The height and other dimensions of the proposed structure. These details can be obtained from the drawings.
• The numbers of lifts that’ll be needed. This will usually be one per storey but will vary with complex or unusual designs.
• What sort of loads will have to be supported by their scaffold. Whether pulleys or other ways of getting materials to heights will be needed.
• How the structure will be accessed (for example, ladders, staircase, ladder bay etc). These access methods will have to take not only safety into account but also security. To avoid vandalism and theft it’s not uncommon for scaffolding to be fitted with alarms.
• Whether you’ll need netting, sheeting or brickguards. If your scaffold is very close to a neighbour’s boundary, netting or sheeting can be vital in ensuring stray dust or materials don’t fly off into their property. Barrier sheeting like this can also provide a wind-guard and protection against rain, allowing construction to progress in bad weather. More ties are required if sheeting or netting is used, as winds can exert considerable forces.
• How good the surface is for their scaffold’s foundations.
• From your drawings, how they can plan what ties will be needed.
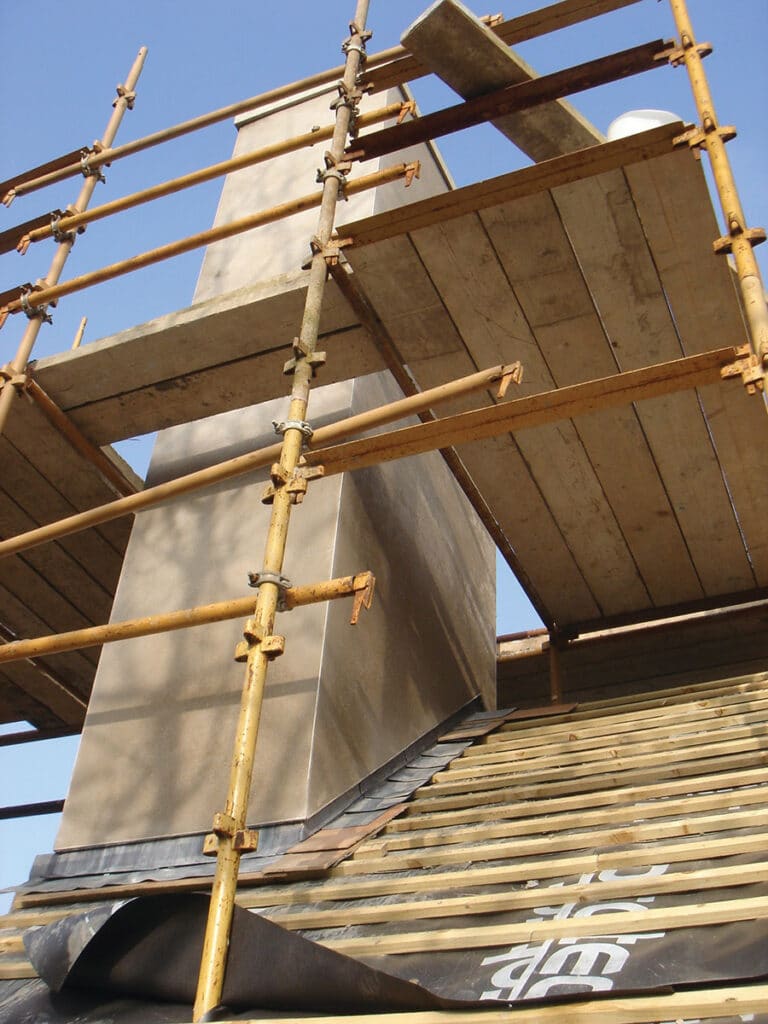
If your build is non-standard (seriously ambitious) they’ll take all this information back to their office where engineers will design and draw up the exact, bespoke, system of scaffold required. Only once this is all done can they assess what type of scaffold you’ll need and how much it’ll cost.
A putlog (bricklayer’s) scaffold is the simplest type, consisting of an outer row of standards held together with ledgers and with the transoms (putlogs) built into the block or brickwork at intervals as it rises, to provide stability. It is open at the construction surface for the builders to work.
An independent tied scaffold has two rows of standards, with each row joined by ledgers to support transoms. This type stands on its own, independent of the building but then has to be tied in at intervals. The inner row of standards is set as close as possible to the building.
A working platform is created using scaffold tubes and boards with guard rails and boards to give a strong, stable platform that may be only ever be one lift high. Taller versions are often built in one go at the start of the project and accessed by ladders throughout their use.
A birdcage scaffold is usually only one level high, in a very tall building or high hallway, for example. It is built in one go and then accessed by ladders. A variation of this is a sling scaffold, which is supported high in the air, leaving the ground area underneath it free for other workers to use while construction proceeds above them.
Other, more specialised, scaffolds can be designed for every conceivable type of access.