Roofing is a specialist trade but there are watchpoints you need to know about.
In this article we cover:
- What’s in a roof: roofing layers
- Watchpoints for underlays
- Watchpoints for ventilation and vapour control
- Watchpoints for insulation
- Guarding checks
- Fire safety checks
- Roof drainage watchpoints
- Watchpoints for flat timber roof structures
- Watchpoints for pitched timber roof structures
- Watchpoints for wallplates
- Watchpoints for fixings
- Watchpoints for flashings
- Watchpoints for flat concrete roofs
- Watchpoints for metal deck roofs
- Watchpoints for waterproof roofing membranes
- Watchpoints for access to roof spaces
- Watchpoints for openings in roofs
Watchpoints for underlays
Underlays below slates and tiles will be delivered in rolls. In roofs of buildings in areas of
severe exposure, boards or rigid sheets may support the flexible underlay. Check that:
- The underlay and any support boards are all of the correct specification.
- It is undamaged and the manufacturer’s instructions are being followed.
- Laps are of the correct size and the underlay continues over hips.
- It is cut neatly and not torn, around service penetrations in the roof covering.
- It is fixed over rafters at vertical laps and secured by battens over horizontal laps.
- Support is provided at the eaves. e.g. by using support trays, to prevent sagging.
- The underlay is UV resistant at the eaves and over gutters or a proprietary eaves guard is used.
- It is dressed correctly under ventilated ridge systems.
- It is turned up at abutments, usually a minimum of 100mm.
- It will allow any water to pass behind the slating or tiling battens.
Watchpoints for ventilation and vapour control
Cold roofs require ventilation between the timber members and over the insulation, with an unbroken airflow between the lowest and highest external points of the roof on each slope. VCLs are usually polythene or polyethylene of a minimum thickness of 125 µm (500 gauge).
- Common ventilation problems are encountered at lean-to roofs at wall abutments, roof slopes meeting at valleys, above and below roof windows or other obstructions and where a flat roof meets a pitched roof. Ventilation failure is very likely to lead to condensation within the structure and decay of the roof timbers.
- Attention needs to be paid to the junctions of wall and roof insulation to provide continuity of the thermal envelope. Ventilation routes can be maintained by inserting rigid insulation boards snugly between rafters to prevent the ceiling insulation quilt from blocking the airflow. Preformed plastic trays can also be used.
- To prevent birds, small animals and larger insects from entering the building through ventilation gaps, they should be covered with fine mesh of maximum 4mm apertures.
- Minimum permitted vent sizes at eaves and ridges will differ according to the roof shape, pitch, span, air permeability of the roof covering and type of underlay used.
- VCLs should be fitted only after the building is weathertight and the moisture content of the structural or framing timber is 20% or below.
- VCLs should be fixed at maximum 250mm centres, sealed at all penetrations and jointed with minimum 100mm laps which should be fixed to timber members.
- Lap and seal VCLs in around openings in roofs and walls.
- Check that all recesses in ceilings, such as downlights, are correctly sealed.
- Repair any tears in VCLs before they are covered over.
- Ensure that a VCL is always fitted on the warm side of any insulated element.
Watchpoints for insulation
Insulation for warm roofs should be bonded or mechanically fixed to resist wind uplift in accordance with the manufacturer’s recommendations. Insulation of warm flat roofs can be laid ‘loose’ and ballasted to resist wind uplift.
- All insulation on warm flat roofs should be kept dry to avoid trapping moisture.
- If using ballast, the roof structure must have been designed to support it and it must prevent wind uplift of the layers below.
- Insulation on warm roofs should wrap the structural timbers within the thermal envelope.
- Counterbattens running in the direction of the slope are required on warm pitched roofs to avoid any moisture from building up behind the horizontal battens.
- Care should be taken to prevent condensation build-up in ducts or pipes passing through insulation layers. Such ducts or pipes should be rigid with the correct CE or BS markings and laid to fall to the exterior of the building. Some commonly available types of flexible ducts are of very inferior quality, so avoid.
- Attic decking for walkways or light storage, or platforms for water tanks or MVHR units, etc. must be supported on legs to be at least 50mm above the height of the uncompressed ceiling insulation.
- Ceiling insulation in attics should go around and over, but not under, water storage tanks.
- All water pipes and overflows on the cold side of the ceiling insulation must be insulated.
- Loft hatches must be insulated and fitted with air seals and holding-down catches.
Check the guarding
A flat roof which is intended to also act as a terrace, deck or roof garden should have design details for access and perimeter guarding. The roof design should account for any permanent service equipment to be installed on it and temporary construction loads.
Timber is not a suitable material for any element of the guarding around a roof, terrace or balcony and also should not be used as a structural support for a terrace or balcony.
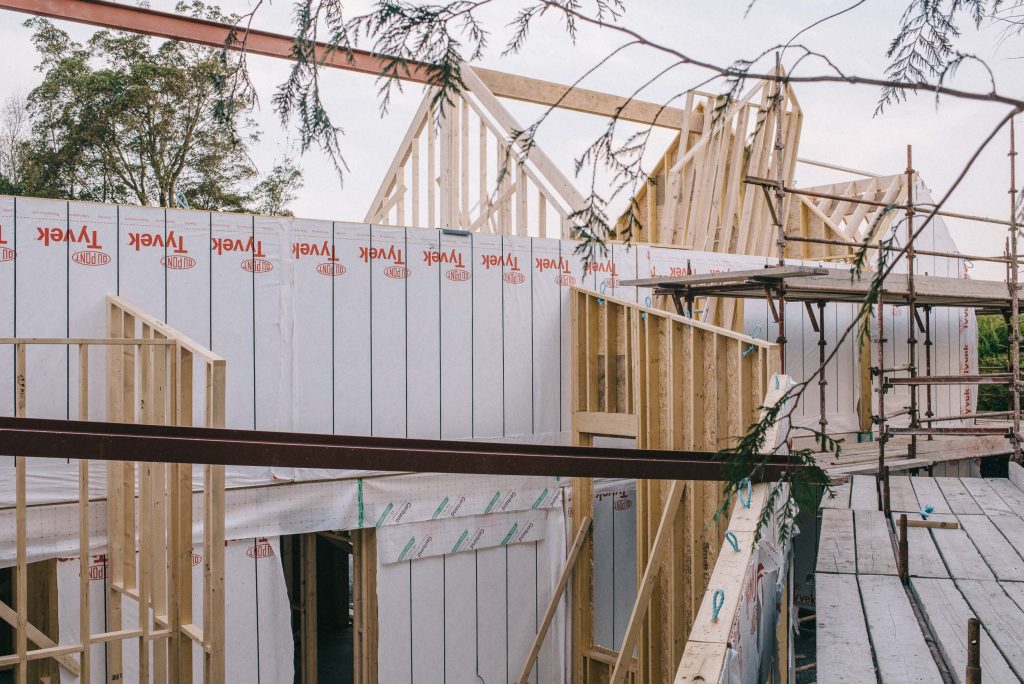
Fire safety checks
- For green roofs, make sure that the guidance in the GRO fire risk guidance document and Building Regulations is being followed.
- Any surface protection provided to the waterproofing layer must satisfy the fire protection requirements in the Building Regulations.
- Pay attention to the waterproofing details at abutments, joints between the roof waterproofing and the wall cavity trays or DPCs and the heights of waterproofing to be dressed up walls. Non-combustible trays may be required in external walls.
- Flat roofs may be used for emergency egress, with a protected route leading to a safe place on the ground. Guarding will almost certainly be required.
- Emergency egress can be provided from dormers and roof-light windows.
Roof drainage watchpoints
Gutters are not water storage vessels, but are intended to get rainwater off your roof structure. Some gutter installers lay them flat but they should have a slight fall towards the outlet, as should built-in gutters in flat roofs and in level valleys between two adjoining roof slopes.
- Rainwater outlets in flat roofs must be recessed into the waterproofing layer.
- Check that the installer is using the correct sizes of gutters and downpipes, as specified.
- Check the fall towards gutters and rainwater outlets in flat roofs.
- A blue roof should have a slow run-off to attenuate the rate of water flow into stormwater drainage systems. Blue roofs should be constructed as warm roofs, with flow restrictor outlets and with overflows which are visible when in use.
- Drainage outlets in built-up roofs (green, brown, biodiverse, etc.) should have inspection hatches fitted at surface level.
- Green or biodiverse roofs may require automatic irrigation systems.
- Check gutter and downpipe joints and supports for strength, spacing and fixing.
- Internal downpipes must be insulated.
- Where gutters are positioned behind parapet walls, overflows must be provided.
- Smaller surfaces should be drained, such as balconies, terraces and small roofs.
- Where roofs have upstands on all sides, there should be a minimum of two rainwater outlets provided to two separate downpipes.
What’s in a roof?
As with all other structural elements, a new or renovated roof will have resulted from a design process that conforms with the building regulations, planning guidance, client preferences, the physical shapes required, external finishes and the structure needed to support it.
Most roofs with a timber support structure will consist of a weather resistant roof covering on battens or decking, supported by rafters or joists. In terms of insulation configuration, there are two principal types, warm roofs and cold roofs. Essentially, a warm roof has its insulation between and over the rafters or joists and a cold roof has the insulation between and under the rafters or joists.
Flat, or sloping roofs of up to a 10 degree pitch, may also be constructed as green, biodiverse or brown roofs. Blue roofs need to be flat. These non traditional roof types tend to be heavier so generally require a stronger supporting framework; and they should be constructed by members of the appropriate trade bodies, such as the National Federation of Roofing Contractors (NFRC) or the Green Roof Organisation (GRO), etc.
As alternatives to the ubiquitous slates or tiles, roof coverings can be lead sheet, zinc and zinc alloys, copper, stainless steel, aluminium, shingles, composite products and thatch. Advice is available for the correct use and fitting of each of these alternatives, for instance the Thatching Advisory Services (TAS), the Federation of Traditional Metal Roofing Contractors (FTMRC) and the Lead Contractors Association (LCA) are just some of the bodies which supply extensive guidance.
For slates and tiles, there is a huge range of natural and man-made products available, so know what you are buying and study the manufacturer’s written technical guidance carefully.
Fascias, soffits and barge boards may be timber, composite, PVCu or a metal product maybe matching the roof covering. If timber, they should all be preservative treated or be naturally
durable and the first coat of stain or primer should be applied to all surfaces before fixing.
Prefabricated roof cassette systems may be supplied, similar to timber frame construction, in which case the requirements are: certification for the structure and its installation, durability,
moisture protection, structural, thermal and acoustic performance, fire resistance, ventilation and condensation control.
Installers of solar roof panels must liaise with the roof covering manufacturer before work commences, in order to ensure compatibility, stability, weather-tightness and any special
requirement for flashings and fixings. At coastal locations, grade 316 stainless steel fixings and brackets are usually recommended.
Watchpoints for flat timber roof structures
- Firring pieces should not taper to zero, but should be a minimum of 38mm high at their lowest ends. It is vital that these are accurately cut.
- Any structural timber which may be exposed to the weather or which may be subject to wetting and all timber used in flat roofs, should be kiln dried and vacuum treated with preservatives. Any cut edges of structural timber should be re-treated.
- Check all structural timber to confirm that it is as specified on the drawings.
- All timber, including solid and engineered joists, should be checked on delivery and any which are excessively wet, distorted or damaged should be rejected. All timber products should be stored under cover to prevent wetting or sweating until they are going to be used.
- Check that metal web ‘space’ joists or ‘I’ joists are being installed in accordance with the manufacturer’s design layout and technical instructions.
- Cross-laminated timber (CLT) is generally not acceptable for use in flat roofs.
- Structural insulated panels (SIPs) are not acceptable for use in warm flat roof construction.
- Check that the decking material has been supplied according to the specifications.
- For metal roof coverings, there are certain species of timber which should not be used with certain metals.
- Plywood or OSB decking boards should have movement gaps at rigid upstands. Square edge boards require an additional movement gap between boards.
- Roof decking boards are usually tongued and grooved (t&g). Square edge boards should be used for metal roof coverings.
- OSB decking should have arrows denoting the direction of fixing in relation to the joists or firrings.
- Timber nogging pieces are needed under any edges of decking which do not have direct support from joists or firrings.
- Decking should be fixed at 100mm centres using the correct sizes of ring shank nails.
- Timber decking should never be allowed to get wet.
- All metal fixing components and fastenings should be of the correct size, corrosion resistance and strength.
- Metal components must be fixed strictly in accordance with the manufacturer’s details.
Watchpoints for pitched timber roof structures
Prefabricated roof trusses are designed and manufactured specifically for each roof and should never be adapted. Check for:
- Condition of all timber and the joint plates upon delivery to the site.
- Handling, stacking, ventilation, and weather protection when stored on site.
- Dimensions, including overhangs, angle of pitch, and spacings when erected.
- Stamps and markings of compliance with standards.
- Bearing lengths on truss shoes.
- All bracing is provided at the correct locations.
- Straps at wallplates and lateral restraint points.
- Multiple or ‘girder’ trusses should be factory-fixed together.
- Trimming and supports around openings such as chimneys, hatches, and roof windows.
- Support platforms or decking on the ceiling joists.
- Intersections between truss roofs and cut roofs.
- Strutting where the bottom chord of a truss acts as a floor joist.
Cut roofs will be specified on the drawings; check for:
- If different strength grades of timber are being used in different parts of the roof, make sure that the right grade of member is in its proper place.
- The structural frame must be fully completed before any roof coverings are fitted.
- Purlins and binders should be built into supporting walls.
- Valley boards and hip rafters must be wide enough to accept the full cut of the rafters.
- Valley rafters will be larger than the main rafters.
- Purlins should be mitred at hips and jointed to take the bottoms of the hip rafters.
- Check that any joints, holes, and notches in the timber members comply with the building regulations and the working drawings.
Timber is not a suitable material for any element of the guarding around a roof, terrace or balcony and also should not be used as a structural support for a terrace or balcony.
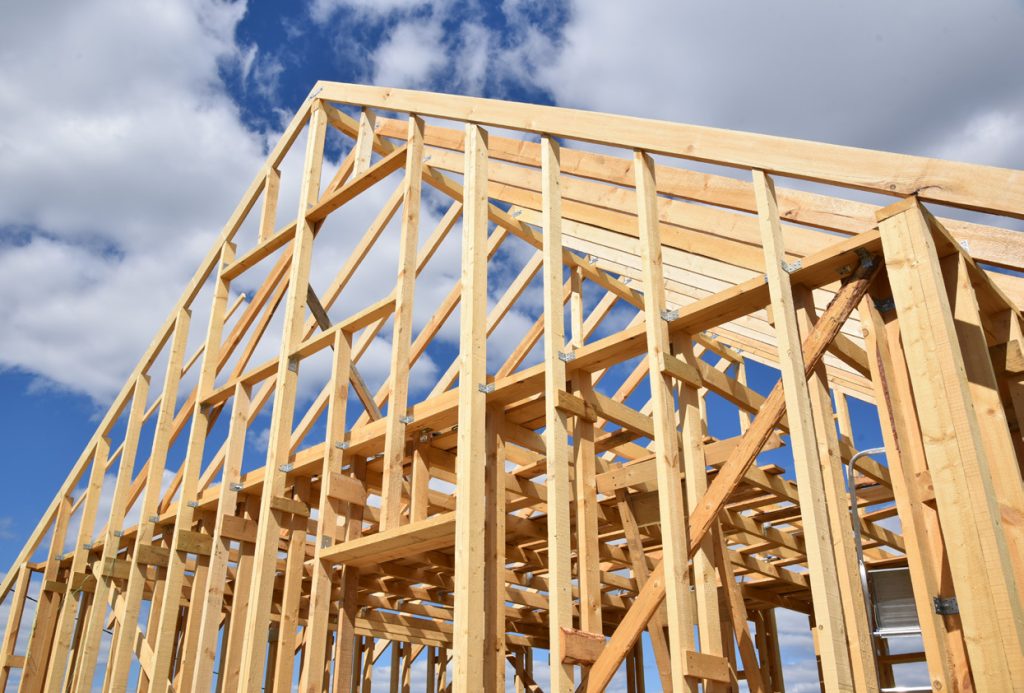
Watchpoints for wallplates
Wallplates are common to both trussed and cut types of roof. They should be:
- Jointed using half-lap joints, including at corners.
- Bedded straight and level and strapped down to the walls.
- Tied across at corners using angle ties and tied to hip rafters using dragon ties.
- At least 3 metres long or should extend over at least 3 joists, rafters, or trusses
Watchpoints for fixings
Timber slating or tiling battens should be sized to suit the roof covering and the rafter spacing, be at least 3m long and be fitted to avoid joints occurring over the same rafter. Zinc-coated annular ring-shank nails of the correct dimensions should be used to fix battens, but use hot-dip galvanised steel nails or aluminium nails on roofs in coastal areas.
Follow the manufacturer’s written technical instructions if using metal batten and clip systems for slating and tiling.
Nails for fixing slates or tiles can be silicon bronze, phosphor bronze, aluminium, stainless steel or copper; but not galvanised steel. They should be at least 38mm long and penetrate at least 15mm into battens. Additionally, hooks and clips may be used. Check the slate or tile manufacturer’s fixing schedule.
Slates or tiles on mansard roofs, dormers and dormer cheeks will require additional fixings, so check this. Cut tiles or slates on dormer cheeks close to the main roof surface. Follow the verge construction details on your drawings
Watchpoints for flashings
Flashings can be formed using lead, aluminium, aluminium alloys, zinc alloy and copper. Other proprietary lead alternatives and GRP products are also available. Follow the details on the drawings and guidance literature such as the Lead Training Academy’s manual.
The job of forming, welding and fitting lead flashings is skilled and quite complex. Ensure that lead is the correct code for the exposure rating and watch out for things like protection of lead against reaction with mortar, the heights of upstands, lap lengths, strip lengths, methods of support and fixing. Saddle flashing should be fitted at the tops of valleys.
Watchpoints for flat concrete roofs
Although less common, reinforced concrete decking can be used, either cast en-situ or precast. Concrete which is cast en-situ should be propped and protected until fully dried and cured. All precast concrete decking must have minimum bearing distances, so check this with the designer or structural engineer.
- Check the moisture content of concrete decks before bringing the waterproofing layer installer on site. Confirm that adhesives are compatible with any additives in the concrete.
- The installer of any bonded waterproofing layer to be laid on concrete or screeds should carry out adhesive bond tests before commencing.
- Some precast decks require a screed to achieve their intended strength and these can be sloped to create falls.
Watchpoints for metal deck roofs
Warm flat roofs can be built up on profiled metal deck sheeting. There are a number of methods used for the make-up of these roofs, so check yours.
Any insulation board used to span across the troughs of profiled metal deck sheeting should have adequate compressive strength or be laid on support boards across the profiles.
Insulated metal roof cladding can be used on a steel framed construction to create roofs which can range in pitch upwards from as low as 1.50 (after deflection).
Watchpoints for waterproof roofing membranes
Waterproof roofing membranes are most often used for flat roof applications but can also be used on pitched roofs. Most flat roofs are covered with a proprietary single-ply membrane, but they can still be waterproofed using modified bitumen, mastic asphalt or liquid-applied products.
- Check that the installer is a member of a suitable quality control certifier.
- The erector of the flat roof deck should survey it when complete in order to correct any depressions and to verify the falls to outlets, before handing it over to the waterproof covering installer.
- Provide walkways to protect the membrane until all works are complete.
- After the covering is laid, it should be checked by an independent testing company using electronic leak detection equipment to prove the integrity of the waterproofing layer.
- Re-test any defects which have been repaired.
- Get the test report and a written warranty for the materials and installation on completion.

Watchpoints for access to roof spaces
Proper access to roof voids will allow for inspection, maintenance and possibly removal of equipment including ventilation units, water tanks, roof-mounted services (e.g. solar panels), TV and telecoms cables and connection boxes and other plumbing and electrical components.
Access to roof voids should:
• Have a minimum opening width and length of 520mm.
• Not be located in hazardous locations, such as over stairs.
• Be served by decking, walkways or platforms (of at least 1.0 m²) to allow maintenance of the equipment.
If the roof has only a small void which doesn’t contain permanent equipment or services, access may not be required.
Watchpoints for openings in roofs
Openings need to be made for dormer windows, rooflights, and chimneys. The details for doing this should be shown on the drawings. Wider openings such as stairwells require design input by a structural engineer. Multiple trusses will be installed to each side of an opening. Check that:
- All openings are trimmed and supported correctly.
- There’s a minimum gap (usually 38mm) between roof timbers and the face of any chimney.
- Openings in roofs must not impede the ventilation airways.
- Correctly sized ventilation is provided around any dormer at the sill, head and both sides.
- Breather membranes are fitted correctly around dormers.
- Dormer walls have air and vapour control layers (AVCLs).
- Dormer side walls or ‘cheeks’ should be supported by double rafters or joists.
- Prefabricated or proprietary dormers are fitted correctly.
- Integrated solar roof panels may require spaces under them for ventilation.