Once you’ve secured planning permission and have all of your building control and health and safety approvals in place, what’s the sequence of works?
In this article we cover:
- A bird’s eye view of every stage of the construction process, from start to finish
- Which elements require an inspection and which do not
- What’s involved with the inspections on site and who does them
- What certificates you need as you go along
- Watchpoints and pitfalls to avoid during the construction phase
The construction timeline presented here is a suggested sequence of events for a typical house construction project.
The first item in the timeline can be regarded as pre-construction activities, but will usually require some input from the contractor. For instance, if an archaeological report is required, the survey may require soil removal under the archaeologist’s guidance; or sight splays may need to be excavated and fenced and the new entrance properly provided in accordance with the planning conditions.
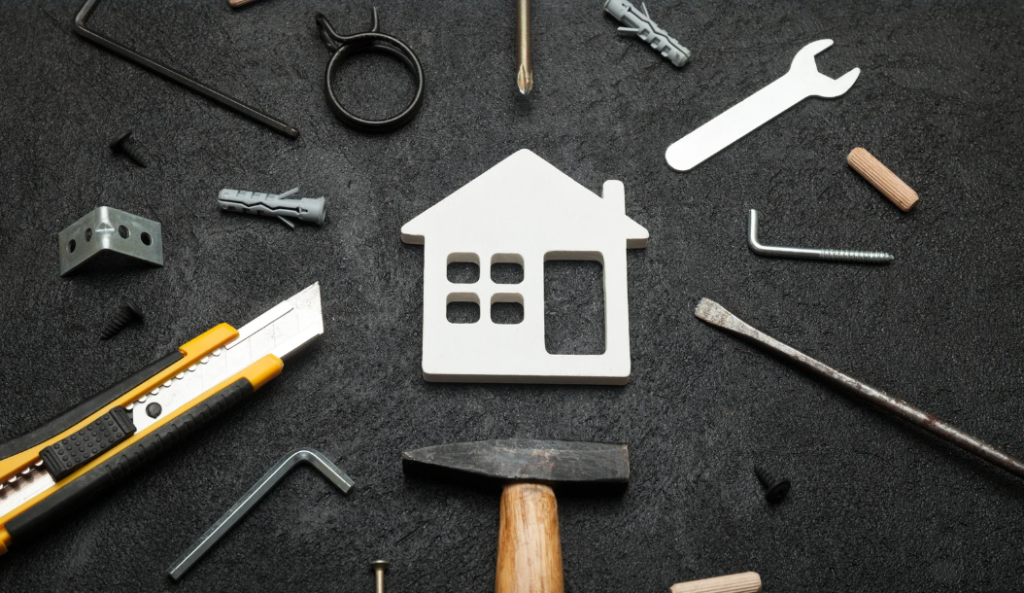
Environmental protection measures might include the removal or treatment of invasive species, the provision of hedgehog safe routes, the erection of bat boxes or the construction of earthen barriers to protect waterways, etc.
Certificates of compliance with standards may be requested by building control (BC) for certain structural components, e.g. roof trusses, precast concrete slabs before they are erected or installed on site.
The remainder should be kept on file for checking as part of the final inspection. Certificates should be obtained at the earliest opportunity from manufacturers, suppliers, installers, subcontractors or others as appropriate. Failure to keep on top of this will create a huge amount of extra time and frustration at the end of the build.
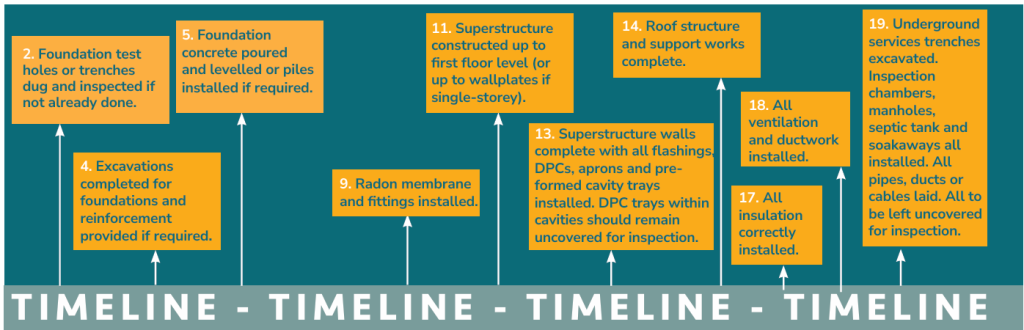
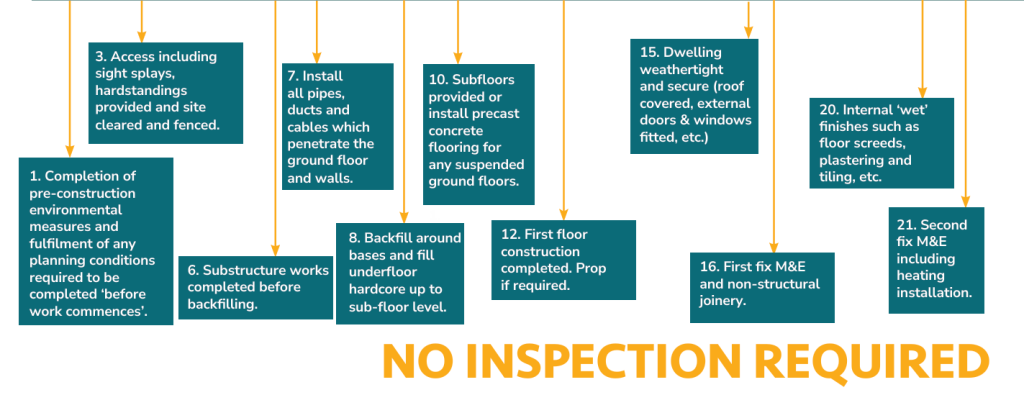
Inspections
During the course of the building works, site inspections will be carried out at various stages (top portion of the timeline below), not only by a surveyor from the local Building Control (BC) office, but also by a suitably qualified person who provides certificates for the satisfactory completion of each stage.
The Certifier is usually, but not necessarily always, the designer; and could be an architect, a chartered architectural technologist or the structural engineer. The contractor might be registered with a warranty body such as NHBC or Homebond and their representatives will also carry out routine inspections.
The different inspectors will not necessarily visit the site at the same time, nor will they always be checking exactly the same things. Sometimes a number of stages might be covered by one inspection. Experience indicates that the Certifier will usually appear more often than the BC surveyor. The warranty surveyor will have their own inspection schedule as instructed by their employers.
All inspections will include checks that the building is being carried out in compliance with the building regulations and the effluent discharge consent (if it was required); however the BC inspections are only one part of the story.
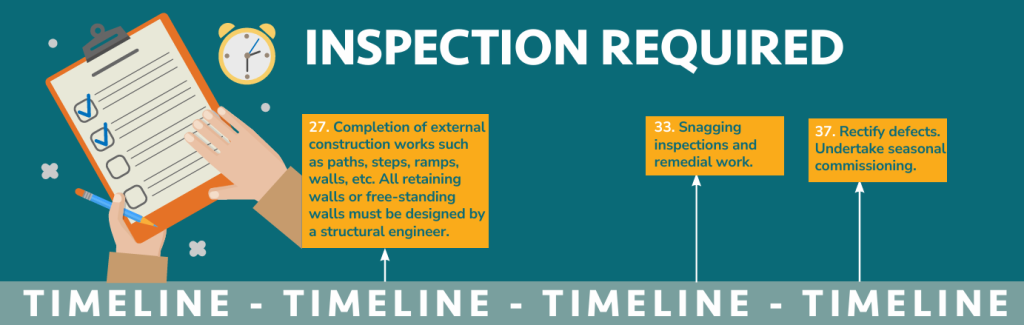
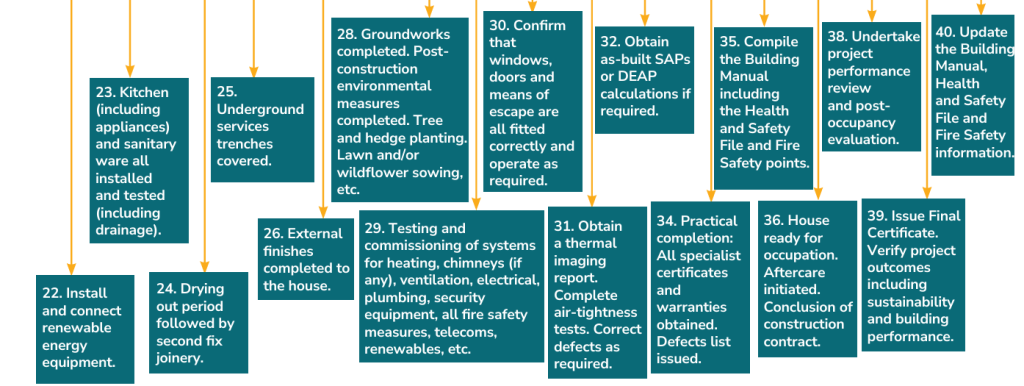
The Certifier will additionally be checking that planning conditions are being met, including any environmental measures which might have been stipulated, together with any requirements by other
public bodies such as the roads authority, water service, rivers agency or the historic buildings department, etc.
Some other aspects of the works might not need to be formally certified but neither should they be ignored, such as temporary works and health and safety measures. It is the responsibility of any competent professional visiting the site to make a note of any safety related matter which may be noticed and to immediately bring it to the attention of the contractor and the employer (the employer being yourself as the property owner).
Contractors and employers are legally obligated to notify the health and safety authority (HSENI, hseni.gov.uk, or HSA, hsa.ie, depending on where you are) of any reportable injuries, diseases and dangerous (‘near miss’) occurrences.
By doing so, you will assist the enforcing authority in identifying where and how risks arise and whether they need to be investigated or when they need to provide advice about how to avoid work-related deaths, injuries, ill-health and accidental loss.
It is essential that any items which may later be covered up, remain uncovered (but kept safe) until they are inspected. The construction contract will usually stipulate that if the contractors close or cover work before it is inspected, then it may be requested to be uncovered for inspection at the contractor’s expense. Works should not proceed to another stage before an inspection of the current stage is carried out.
Certificates
The project certificates file should include certification of products such as insulation, radon
barriers and associated fittings and sealants, fire retardant paints, cladding, glazing, sheeting materials,
wall ties, bolts and other structural components. Evidence of compliance is also necessary for fabricated structural components including timber frame and ICF structures, roof trusses, space joists, lintel systems, precast concrete (including bricks, blocks, beams, flooring planks, etc.), metal assemblies, welding and connections, etc. Product certificates should match the markings on the products or their packaging and stamps, labels or similar markings must be clearly visible, legible and indelible.#